Mobile crushing stations are more and more used in today's social and economic development. They are smart, convenient, and mobile. This feature makes mobile crushing stations very popular. After all, mobile crushing stations are industrial equipment. If they are misoperated, problems will arise. Today, Zhuoya Mining Machine will talk about how to deal with the blockage in the mobile crushing station.
Double output shaft cycloidal motor Because the operating current of the super heavy conveyor under the crushing equipment has a very good correlation with the raw materials of the lower chamber body, and each time the lower chamber body causes more machine equipment in the mobile crushing station to trip, a solution has been developed based on the current characteristics of the plate conveyor equipment, Namely, an electric bell and alarm flashing light shall be installed at the feeding port of the mobile crusher equipment, which shall be immediately connected with the automobile relay in the electrical control cabinet. When the plate conveyor equipment reaches a set current, the automobile relay will pull in, the alarm light will gradually flash, and the electric bell will ring. If the middle and downstream machinery equipment trips, and the plate conveyor equipment current is zero, the audible and visual alarm will also remind. The driver of the mobile crushing truck will stop feeding after receiving the alarm, so as to avoid material blockage.
OM series cycloidal hydraulic motor The alarm current of plate belt conveyor shall be moderate, neither too low nor too high. If the crushing opportunity is too low, the material is often cut, and the stone will hit the plate belt conveyor. If the setting is too high, the volume of the lower chamber is too much, and the space in the buffer chamber is insufficient, it is also very easy to cause the material blockage of the grinder if the common faults of the middle and downstream machinery and equipment occur. Practical experience has proved that the preset value of 33A not only ensures the continuous and stable feeding of the crusher, but also leaves enough buffer room space for the lower chamber of the crusher, which can reasonably avoid material blockage. This method is simple, reliable and low-cost. At the same time, it also alleviates the work pressure of employees and improves the productivity of the grinder.
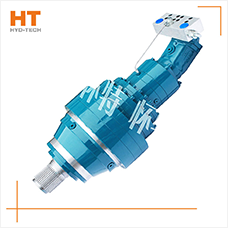