In the late 1850s, the original low-speed high torque hydraulic motor was developed from the fixed rotor part of the oil pump, which consists of an internal gear ring and matching teeth city in Guangxi manufactor Wheel or rotor. The inner gear ring is fixedly connected with the housing, and the oil entering from the oil port pushes the rotor to rotate around the center point. This slowly rotating rotor is driven and output by a spline shaft to become a cycloidal hydraulic motor. After the first cycloid motor came out, after decades of evolution, Jinjia hydraulic hydraulic motor delivers high efficiency energy for you. Another concept of motor also began to form. The motor installs the drum in the built-in ring gear. Motors with rollers can provide high starting M+S cycloidal motor manufactor With the running torque, the drum reduces friction and improves efficiency. The low speed output shaft can also produce stable output.
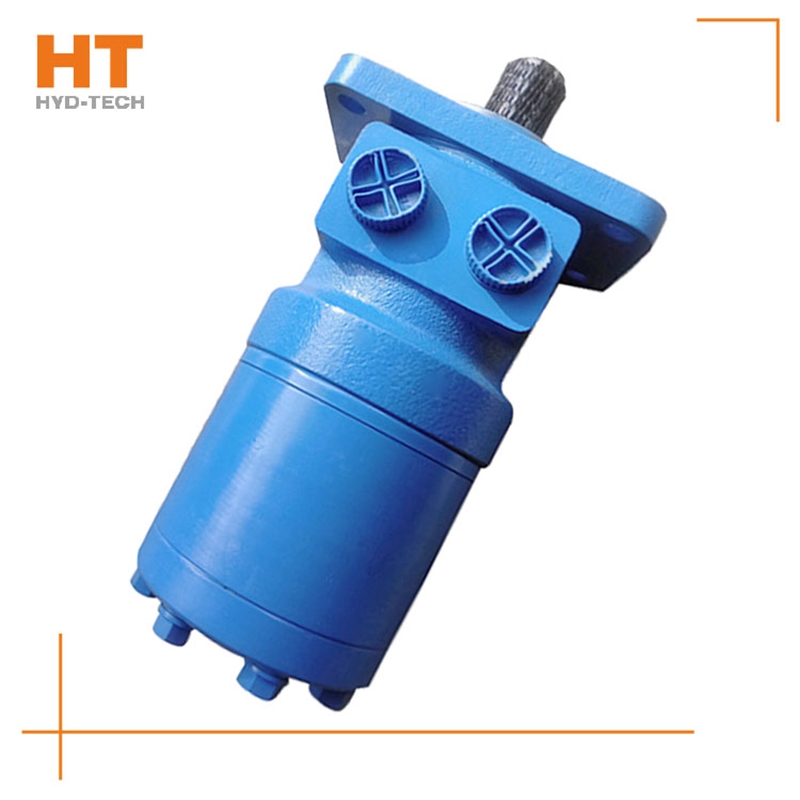
The hydraulic motor manufacturer explains to you the reasons for the poor performance of the hydraulic motor: 1. First of all, according to the analysis of the causes of the wear of the port plate, the main reasons for the weakness of the hydraulic motor are: because the port plate is worn, the oil inlet channel and the oil return channel are connected at the port plate, part of the high-pressure oil leaks, the oil pressure flowing through the stator and rotor pair decreases, and the flow decreases, Eventually, the output speed and torque of the motor will decrease. 2. Due to the wear of the valve plate, its relative position in the valve body has changed M+S cycloidal motor manufactor The preload and adhesion of the spring on the valve body between the valve plates will be reduced, which will intensify the leakage of hydraulic oil and lead to the decline of the performance of the hydraulic motor. 3. With the increase of hydraulic oil temperature, its comprehensive performance declines, driving the cycloidal rotor to rotate city in Guangxi manufactor The ability to move is further reduced. Upon inspection, there is no obvious wear on the joint surface of the stator and rotor pair and the bearing seat and valve disc matched with both sides of the stator and rotor pair. The movement is normal without jamming, which will not cause performance degradation.
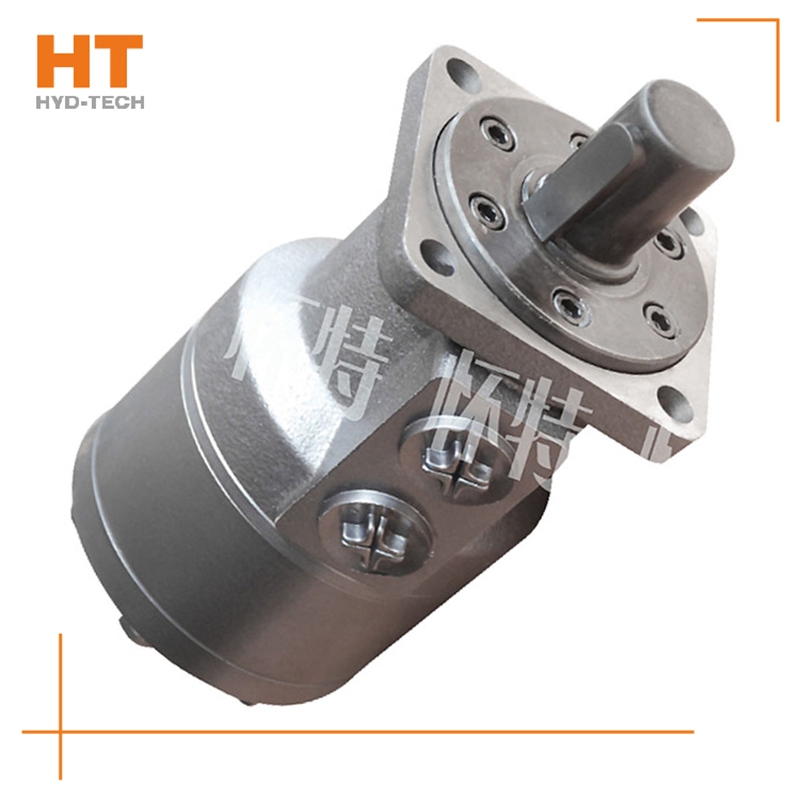
What is the oil supply mode of the hydraulic pump? The straight shaft swashplate plunger pump can be divided into two types: self suction type and pressurized type. Most high-pressure oil supply hydraulic pumps use pneumatic oil tank, and some hydraulic pumps are also equipped with oil make-up slave pump to deliver pressure oil to the oil inlet of the hydraulic pump. The self-priming pump has the characteristics of strong self-priming ability and no need for external oil supply special-purpose M+S cycloidal motor 。 Bearings for hydraulic pumps. The most important part of the plunger pump is the bearing. If the bearing has clearance, the normal clearance of the three pairs of friction pairs inside the hydraulic pump cannot be guaranteed. At the same time, the hydrostatic support oil film thickness of each friction pair will be damaged, thus reducing the service life of the plunger pump bearing. According to the data provided by the manufacturer of the hydraulic pump, the average service life of the bearing is 10000 hours. If this value is exceeded, a new port shall be replaced. 3、 Conclusion. The service life of the piston pump is related to the maintenance at ordinary times, the quantity and quality of the hydraulic oil, and the cleanliness of the oil. At the same time, avoid M+S cycloidal motor manufactor The particles in the oil will wear the friction pair of the plunger pump, which is also an effective method to extend its service life.
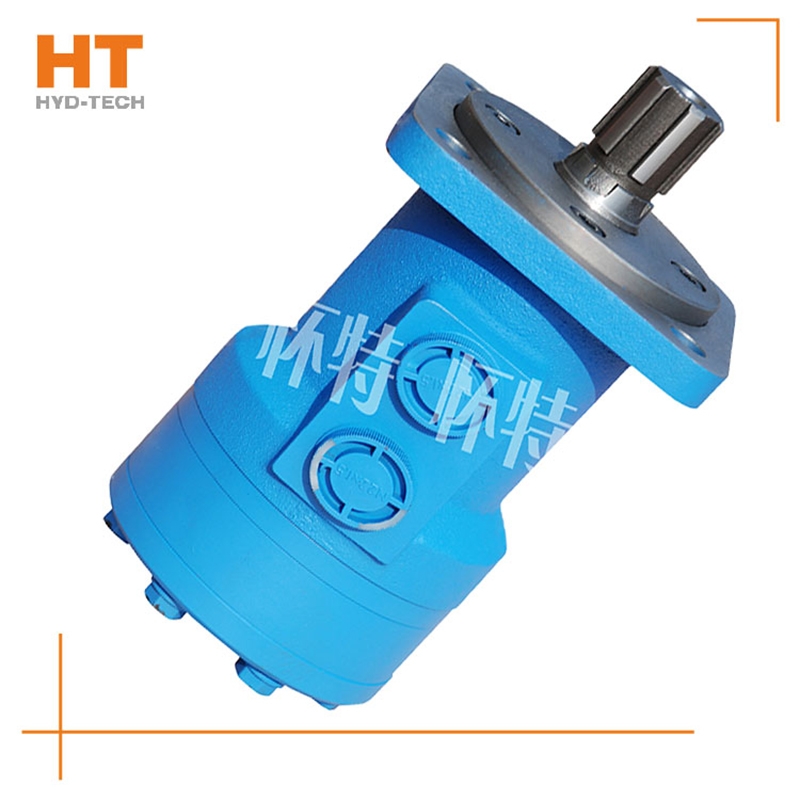
The manufacturer of the hydraulic motor has explained to us the relevant knowledge about the speed and low-speed stability of the hydraulic motor. The speed of the hydraulic motor depends on the flow of the supply fluid q and the discharge of the hydraulic motor itself v. The hydraulic motor has internal leakage. Not all the liquid entering the motor drives the hydraulic motor to work. Some of the liquid is lost due to leakage, and the actual speed of the motor is lower than the ideal situation. When the working speed of the hydraulic motor is too low, it cannot maintain a uniform speed, and it stops when entering city in Guangxi M+S cycloidal motor The unstable state is a creeping phenomenon. The high-speed hydraulic motor is required to work at a speed below 10r/min and the low-speed high torque hydraulic motor is required to work at a speed below 3r/min. All hydraulic motors can meet the requirements. Generally speaking, the low-speed stability of low-speed large torque hydraulic motors is better than that of high-speed motors. Due to the large emissions and size of the low-speed high torque motor, the sliding speed of the friction pair will not be too low even if the rotation speed is low special-purpose M+S cycloidal motor Large emissions, relatively small impact of leakage, large rotation inertia of the motor itself, easy to obtain good low-speed stability.
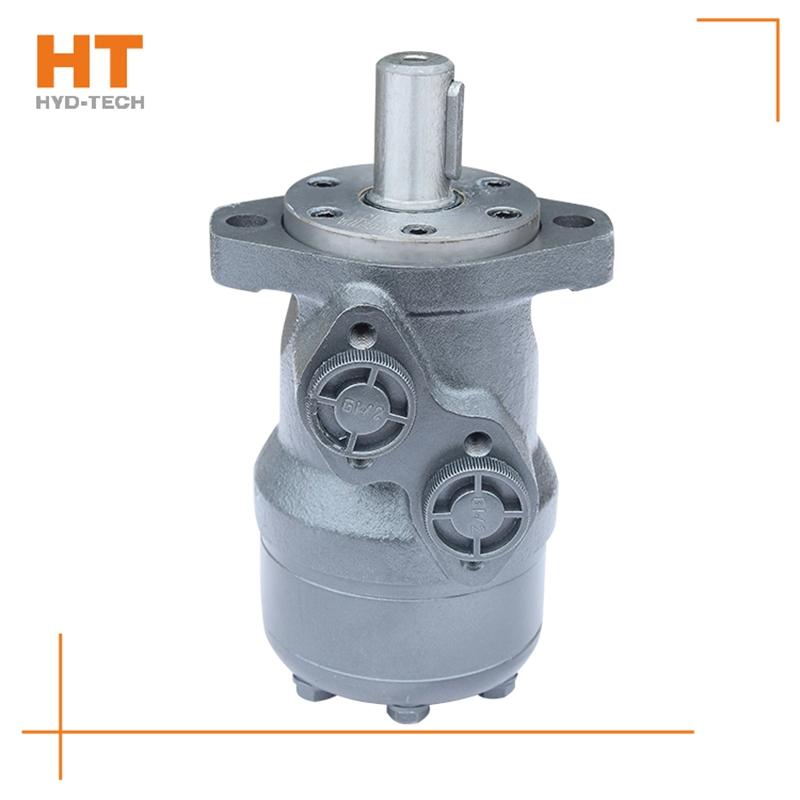
Cycloidal hydraulic motor, as a kind of construction machinery equipment with small price increase and light weight, is also widely used in daily life. Cycloidal hydraulic motor is a kind of motor, which is essential for some equipment. In fact, the operation of all hydraulic systems is almost the same. This cycloidal hydraulic motor is widely used city in Guangxi special-purpose It is used in construction, manufacturing, mining and other industries, so pay attention to daily maintenance when using the motor to ensure the service life of the cycloidal hydraulic motor. In order to keep the whole system in a stable state, it is necessary to ensure that the motor function has a constant pressure, ensure that the hydraulic system is normal, and ensure that the pressure in the system is not M+S cycloidal motor manufactor leak.
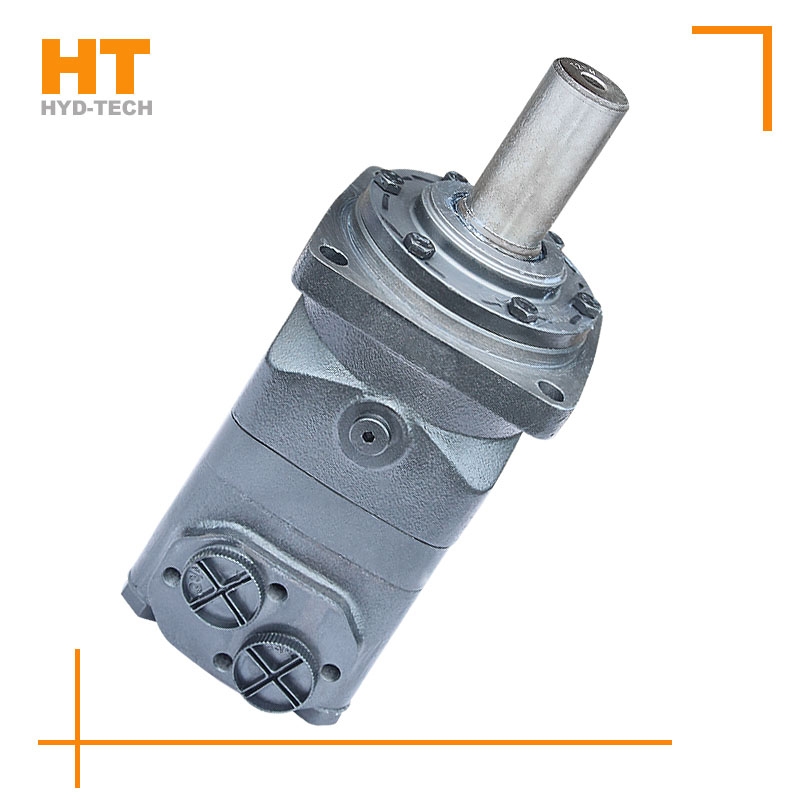
Oil filling process sequence: shell oil filler → oil filling sleeve groove → oil filling sleeve groove → shell oil filling hole → diaphragm → stator. Oil drainage process sequence: rotating stator → diaphragm M+S cycloidal motor manufactor → Shell oil distribution hole → oil distribution jacket longitudinal groove → oil distribution jacket groove → shell oil return port. The rotating motion of the rotor includes rotation (rotation in the direction of expanding the high-pressure cavity around the center of the rotor) and revolution (rotation in the direction of deviation from the radius around the center of the stator). The rotation of the rotor is opposite to the revolution direction, and the rotation is transmitted to the output shaft through the linkage shaft. Rotor rotates for 1 cycle special-purpose M+S cycloidal motor The rotor is driven by 42 pressure oil with the maximum volume for 6 revolutions, so the motor has a large emissions.