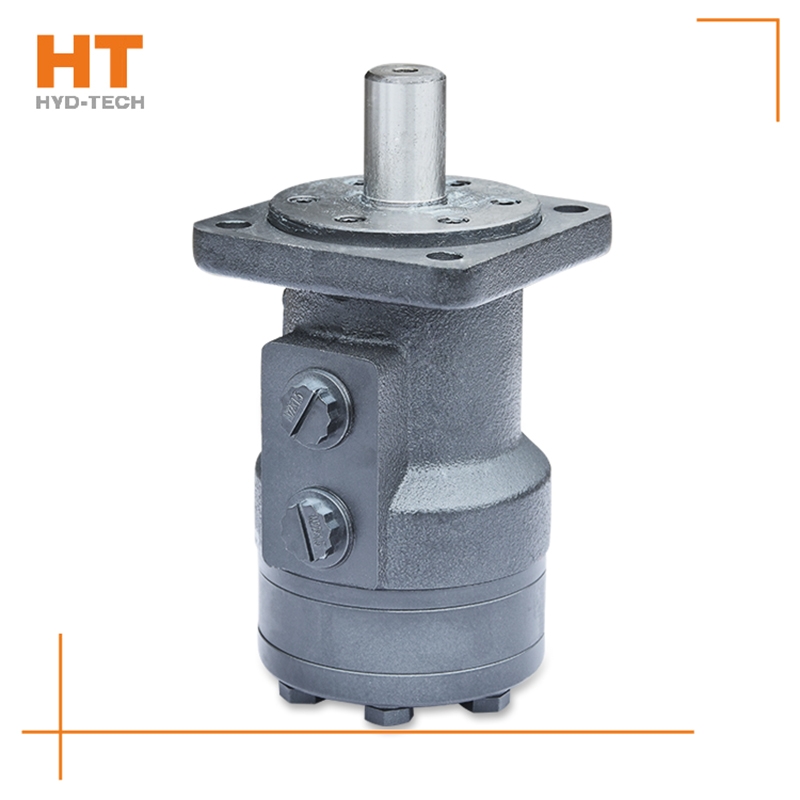
After disassembling and inspecting the hydraulic motor installed on the drill, it was found that the friction surface of the valve disc and the port plate of the hydraulic motor was severely worn, and the deepest worn part was 0. 15mm; The output shaft oil seal is leaking. Cause analysis of oil leakage of output shaft oil seal. After disassembly inspection and test, the axial and radial clearances of the output shaft meet the standard requirements special-purpose Crane cycloid motor There is no obvious wear on the oil seal mating surface. However, it is found that the oil seal rubber has hardened and its elasticity has deteriorated. With the increase of sealing lip wear, the pre tightening capacity and sealing performance decrease, and the excessive oil temperature accelerates the wear of sealing lip; In addition, due to the liquid Nanning Crane cycloid motor The leakage of the pressure motor causes the back pressure in the housing to be too high, which further aggravates the wear and leakage of the sealing lip. The smaller the friction of the rotor in the stator sleeve, the higher the mechanical efficiency of the motor.
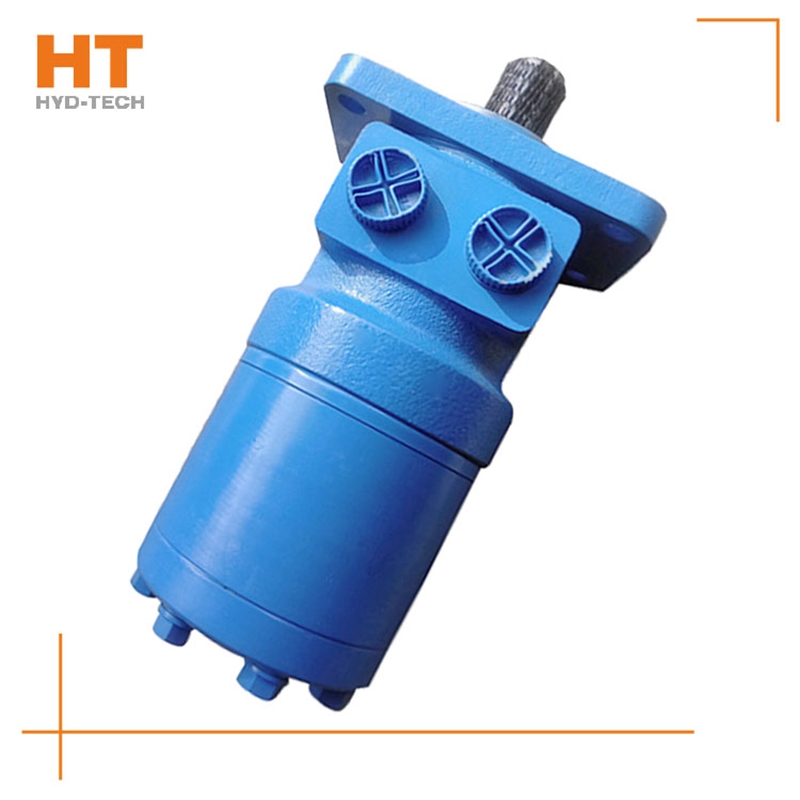
When the high-pressure oil enters the oil distribution shaft and enters each plunger cylinder hole of the working section through the oil distribution window, the corresponding plunger set is pushed against the curved surface of the cam ring L (housing), Nanning Crane cycloid motor The cam ring surface gives a reaction force to the plunger at the contact position. This reaction force N acts on the common plane where the cam ring surface contacts the roller. This normal reaction force N can be decomposed into radial force PH and circumferential force T, which are balanced with the hydraulic pressure at the bottom of the plunger, while the circumferential force T overcomes the load torque, special-purpose Crane cycloid motor Drive cylinder 2 to rotate. Under this working condition, the cam ring and oil distribution shaft do not rotate. At this time, the plunger corresponding to the oil return section of the cam gear moves in the opposite direction, and the oil is discharged through the oil distribution shaft.
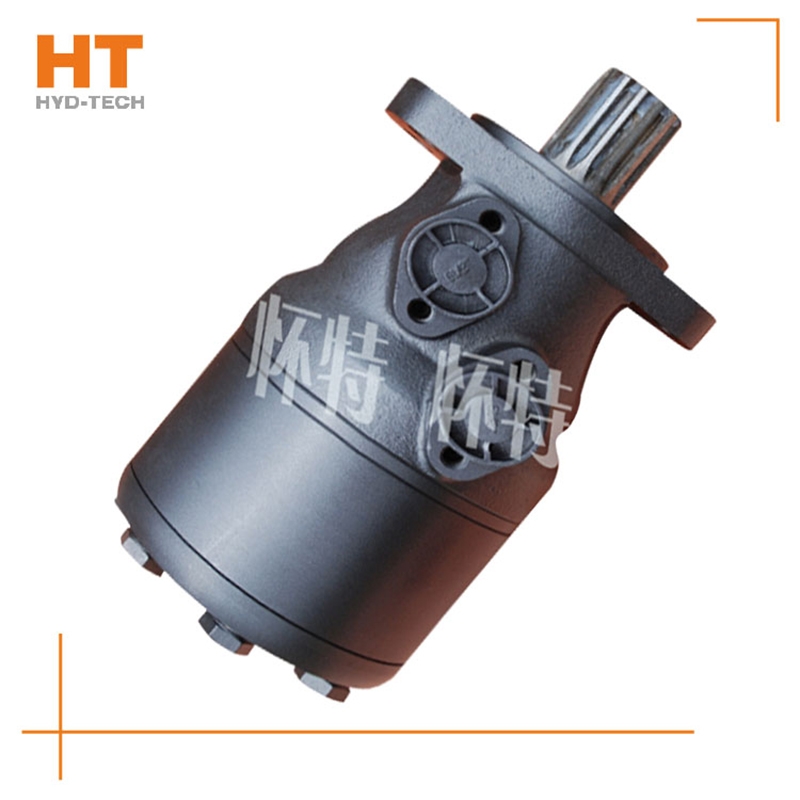
Actuator: hydraulic cylinder, hydraulic motor and swing hydraulic motor. Function: convert the pressure energy of liquid into mechanical energy, which is used to drive the working mechanism to do work and realize reciprocating straight special-purpose Crane cycloid motor Linear motion, continuous rotation or swing; Governor: pressure, flow, direction control valve and other control elements. Function: control the oil pressure, flow and direction from the pump to the actuator in the hydraulic system, so as to control the force (torque) and speed output by the actuator Nanning Crane cycloid motor Degree (speed) and direction, to ensure that the main engine working mechanism driven by the actuator can complete the predetermined motion law; Hydraulic auxiliary device: oil tank, pipe fittings, filter, heat exchanger, accumulator, indicating instrument, etc.
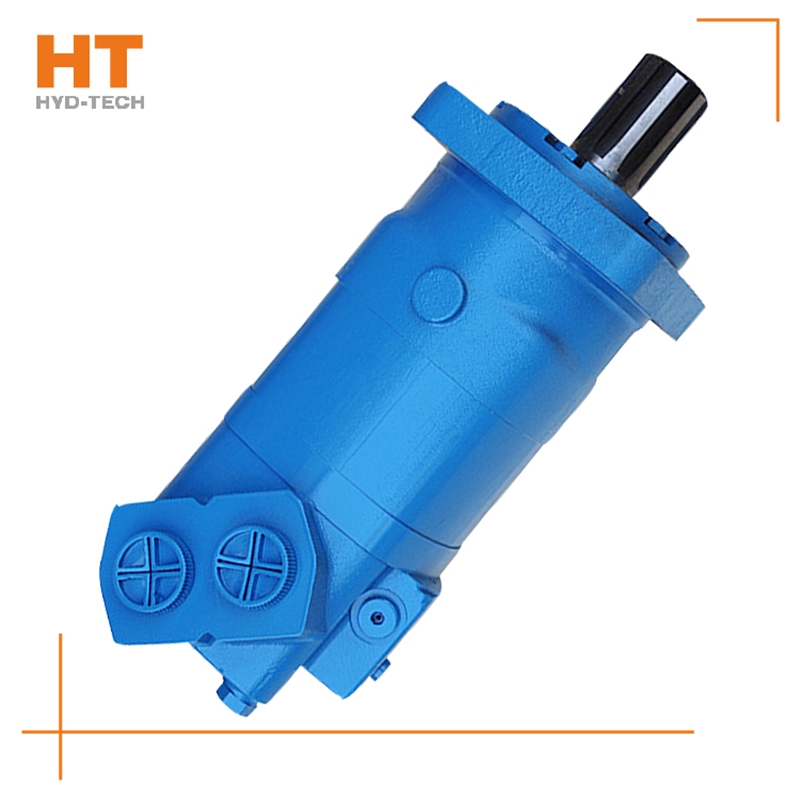
As a kind of hydraulic transmission device, hydraulic motor has been widely used in many places. In fact, I have seen it on many occasions. The main application fields are. 1. The hydraulic motor has convenient speed regulation, which can be adjusted infinitely from 0 to the maximum speed according to the adjustment of the hydraulic valve. The motor itself does not need special design and has low cost. This is much cheaper than motor+reducer, or variable frequency motor and servo motor. 2. The hydraulic system has strong anti overload capacity and relies on the overflow valve for protection, allowing a long time special-purpose Crane cycloid motor (Relatively) Frequent overload, easy to recover under overload, no damage to equipment, no restart of equipment. 3. The hydraulic system is characterized by high energy density. For motors of the same power, hydraulic motors are much smaller than motors Crane cycloid motor Manufacturer , much lighter. And it is easy to apply to mobile devices. 4. The hydraulic motor is totally enclosed and can be safely used in dusty, wet (even underwater) and flammable environments, which is much more reliable than explosion-proof (flameproof) motors.