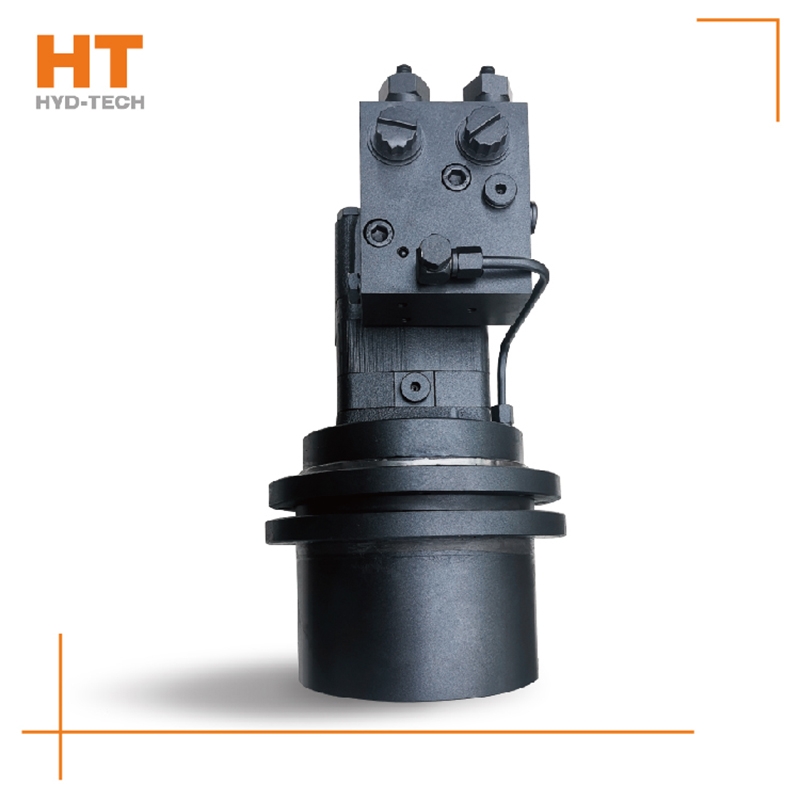
What is the oil supply mode of the hydraulic pump? The straight shaft swashplate plunger pump can be divided into two types: self suction type and pressurized type. Most high-pressure oil supply hydraulic pumps use pneumatic oil tank, and some hydraulic pumps are also equipped with oil make-up slave pump to deliver pressure oil to the oil inlet of the hydraulic pump. The self-priming pump has the characteristics of strong self-priming ability and no need for external oil supply special-purpose M+S cycloidal motor 。 Bearings for hydraulic pumps. The most important part of the plunger pump is the bearing. If the bearing has clearance, the normal clearance of the three pairs of friction pairs inside the hydraulic pump cannot be guaranteed. At the same time, the hydrostatic support oil film thickness of each friction pair will be damaged, thus reducing the service life of the plunger pump bearing. According to the data provided by the manufacturer of the hydraulic pump, the average service life of the bearing is 10000 hours. If the service life exceeds this value, a new port shall be replaced. 3、 Conclusion. The service life of the piston pump is related to the maintenance at ordinary times, the quantity and quality of the hydraulic oil, and the cleanliness of the oil. At the same time, avoid M+S cycloidal motor Manufacturer The particles in the oil will wear the friction pair of the plunger pump, which is also an effective method to extend its service life.
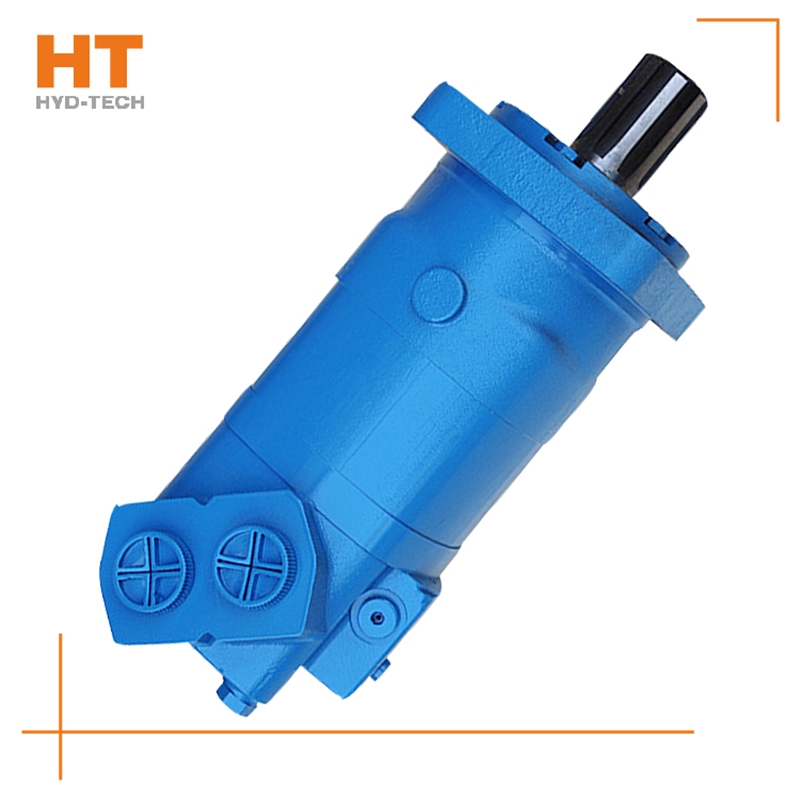
The output pressure of the hydraulic motor also depends on the load. Rated pressure Pn: the rated pressure refers to the working pressure that the hydraulic motor can withstand during continuous operation. It can special-purpose M+S cycloidal motor To ensure the volumetric efficiency and service life of the hydraulic motor. Working pressure P: the working pressure is the actual pressure of oil input when the hydraulic motor is working M+S cycloidal motor Manufacturer power. Its value depends on the size of the load. However, the maximum working pressure is determined by the safety valve in the hydraulic system. The throttle adjustment value must not exceed the maximum pressure value of the hydraulic motor. The third is the maximum pressure: the limit pressure that the motor is allowed to overload in a short time. Pn ≤ Pmax value.
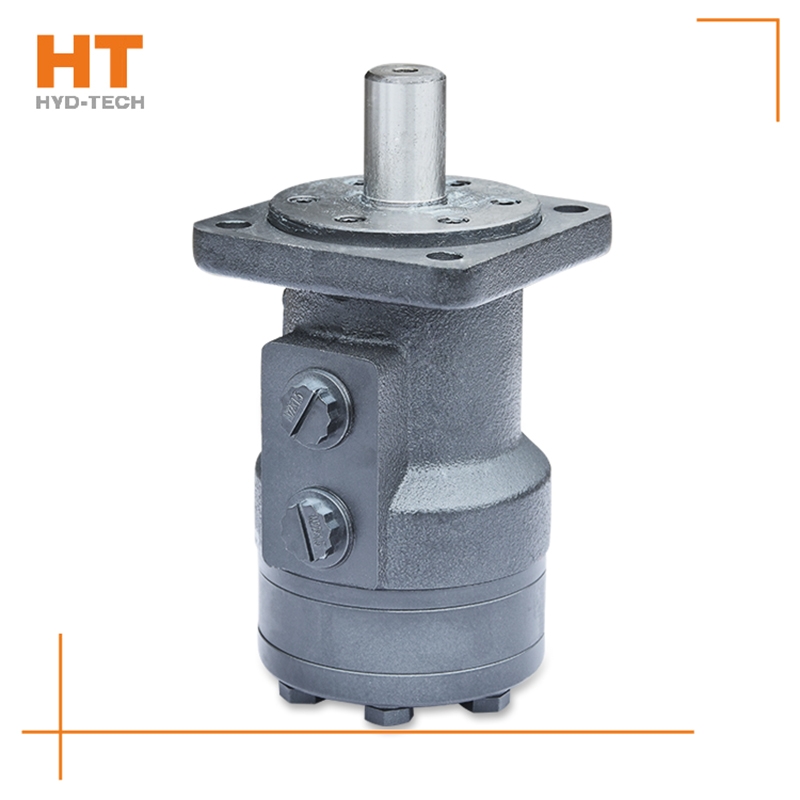
In the late 1850s, the original low-speed high torque hydraulic motor was developed from the fixed rotor part of the oil pump, which consists of an internal gear ring and matching teeth Nantong Manufacturer Wheel or rotor. The inner gear ring is fixedly connected with the housing, and the oil entering from the oil port pushes the rotor to rotate around the center point. This slowly rotating rotor is driven and output by a spline shaft to become a cycloidal hydraulic motor. After the first cycloid motor came out, after decades of evolution, Jinjia hydraulic hydraulic motor delivers high efficiency energy for you. Another concept of motor also began to form. The motor installs the drum in the built-in ring gear. Motors with rollers can provide high starting M+S cycloidal motor Manufacturer With the running torque, the drum reduces friction and improves efficiency. The low speed output shaft can also produce stable output.
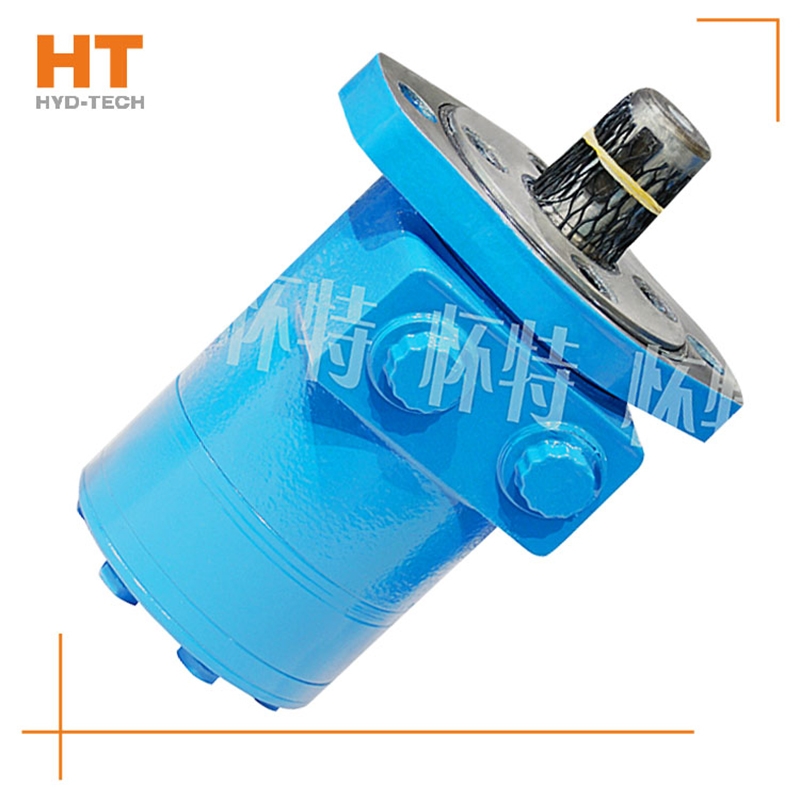
When the main reversing valve of the central closing system and the central closing system is in the neutral position, all oil ports of the reversing valve are closed. If a fixed pump is used for oil supply, the liquid of the hydraulic pump will return to the tank at high pressure through the overflow valve. When the reversing valve is in neutral position, energy transmission starts from the high value, that is, the maximum pressure regulating value of the system. Just reverse M+S cycloidal motor Manufacturer , its energy can be used by the actuator. When the reversing valve is in the middle position, it sometimes bears all the pressure of the system, so the internal leakage is greater than that of the open system. Generally, when the Nantong M+S cycloidal motor In this case, the energy consumption of the closed loop is high, but if the intermediate unloading measures are added or the pressure compensated variable pump is used for oil supply, the energy consumption of the closed loop can be greatly reduced. Closed hydraulic systems are used for a variety of equipment.
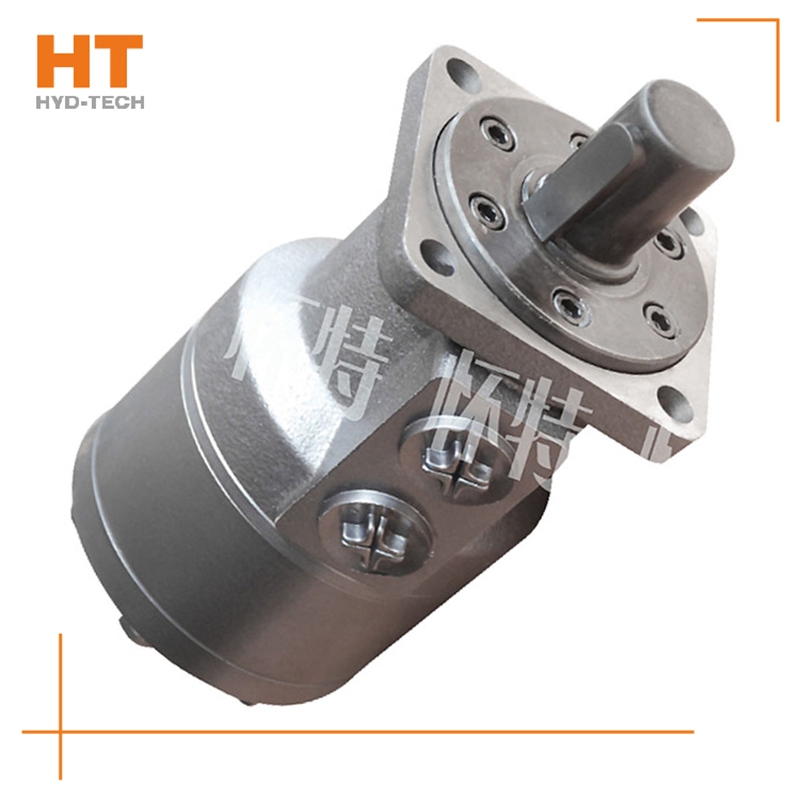
Its basic types are gear type, screw type, vane type and axial plunger type. Its main characteristics are high speed, small moment of inertia, convenient starting and braking, adjustment (speed adjustment and special-purpose M+S cycloidal motor Reversing) High sensitivity. As the output torque of high-speed hydraulic motor is generally small, it is also called high-speed small torque hydraulic motor. Its basic type is radial plunger type, in addition, there are axial plunger, vane type, gear type and other structural types. Low speed hydraulic motors are mainly characterized by large displacement, large volume and low speed (sometimes M+S cycloidal motor Manufacturer It can rotate a few revolutions per minute or even a few revolutions per minute), so it can be directly connected to the working mechanism; It does not need a speed reducer, greatly simplifying the transmission mechanism. Usually, the output torque of low-speed hydraulic motor is large, so it is also called low-speed high torque hydraulic motor.
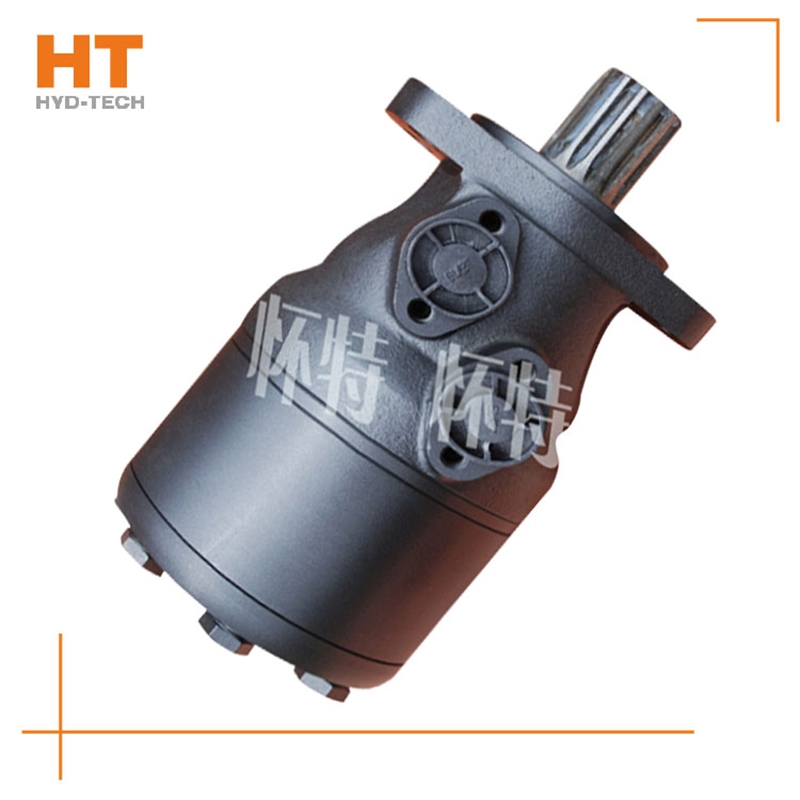
Most of its hydraulic system uses working medium, such as hydraulic oil with continuous fluidity, which converts the mechanical energy of the prime mover driving the pump into the pressure energy of the liquid through the hydraulic pump, and sends it to the actuator (hydraulic cylinder, hydraulic motor or swing hydraulic motor) through various control valves, such as pressure, flow, direction, etc., to convert it into mechanical energy to drive the load. This hydraulic system is generally composed of the following parts: power source, actuator, control valve, hydraulic auxiliary device and hydraulic working medium, which play their respective roles: power source: prime mover (motor or internal combustion engine) and hydraulic pump, whose role is to convert the mechanical energy generated by the prime mover into the pressure energy of liquid, and output oil with a certain pressure;