Most of its hydraulic system uses working medium, such as hydraulic oil with continuous fluidity, which converts the mechanical energy of the prime mover driving the pump into the pressure energy of the liquid through the hydraulic pump, and sends it to the actuator (hydraulic cylinder, hydraulic motor or swing hydraulic motor) through various control valves, such as pressure, flow, direction, etc., to convert it into mechanical energy to drive the load. This hydraulic system is generally composed of the following parts: power source, actuator, control valve, hydraulic auxiliary device and hydraulic working medium, which play their respective roles: power source: prime mover (motor or internal combustion engine) and hydraulic pump, whose role is to convert the mechanical energy generated by the prime mover into the pressure energy of liquid, and output oil with a certain pressure;
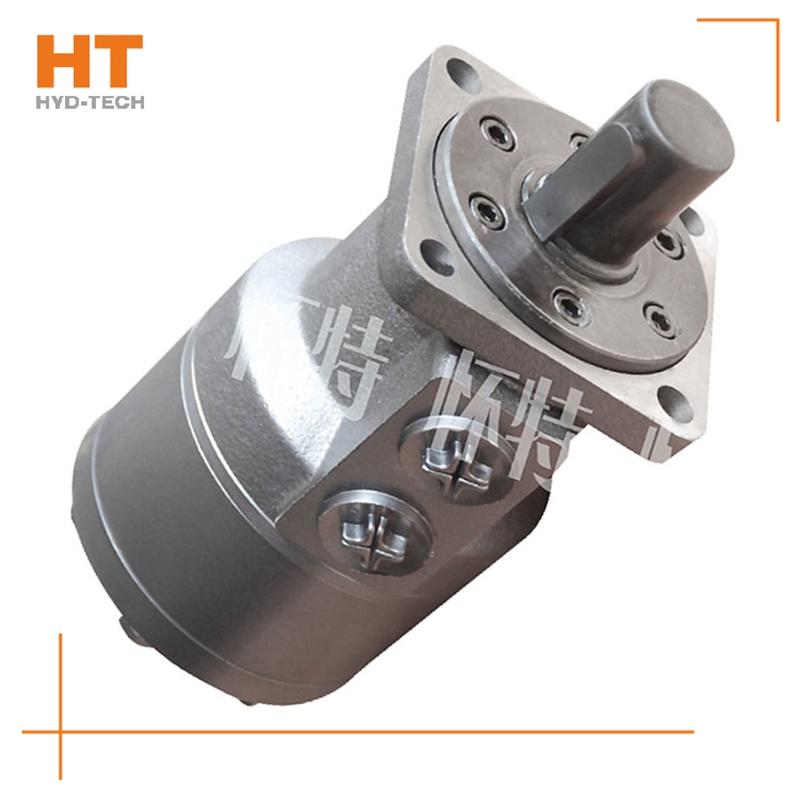
The hydraulic motor has two circuits: the hydraulic motor series circuit and the hydraulic motor braking circuit. These two circuits can be classified into the next category. One of the series circuits of hydraulic motors: three hydraulic motors are connected in series with each other, and a reversing valve is used to control the start stop and steering. The flow through the three motors is basically the same. When the displacement is the same, the speed of each motor is basically the same. The oil supply pressure of the hydraulic pump Shaoxing Manufacturer High, small pump flow, generally used for light load and high speed. Serial circuit II of hydraulic motor: each reversing valve in this circuit controls one motor, each motor can work independently or simultaneously, and the rotation direction of each motor is also special-purpose orbit motor optional. The oil supply pressure of the hydraulic pump is the sum of the working pressure difference of each motor, which is applicable to the condition of high speed and small torque.
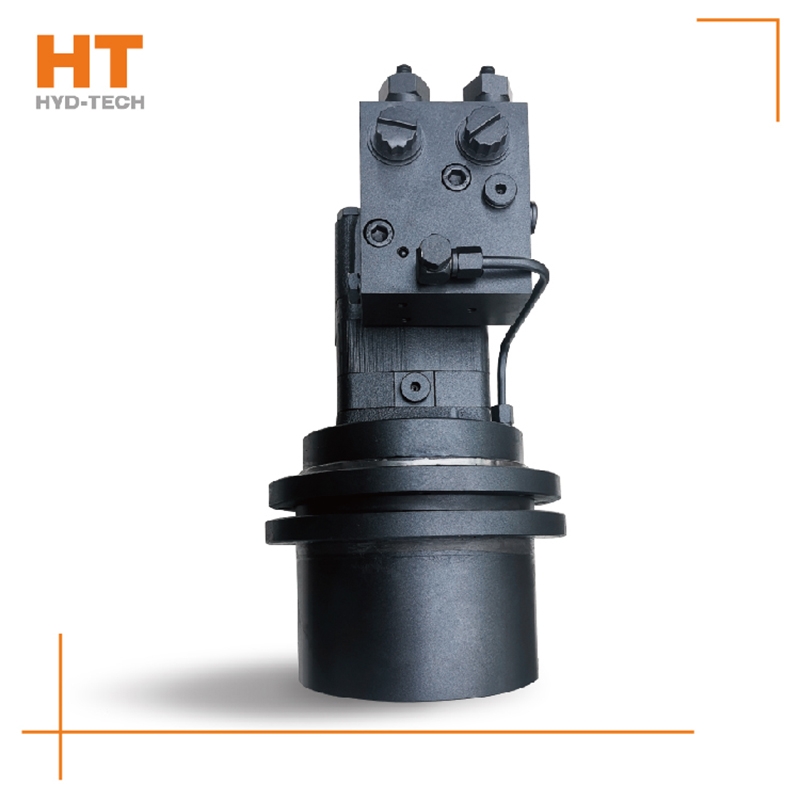
When the working load changes from low speed to high speed in a wide range, the hydraulic motor is also required to be able to drive and regulate speed in the corresponding wide range, which requires the motor to have good low-speed stability and high speed performance. The speed regulation range K of the hydraulic motor is usually expressed by the ratio of the allowable maximum speed to the minimum speed. special-purpose orbit motor It is the highest operating speed of hydraulic motor, but it is limited by many factors, mainly including: 1. Service life. After the speed increases, each pair is worn Shaoxing Manufacturer The service life is shortened. 2、 Mechanical efficiency limits. At high speed, the hydraulic motor needs to input large flow, accordingly, the hydraulic loss of each circulating component increases, reducing the mechanical efficiency.
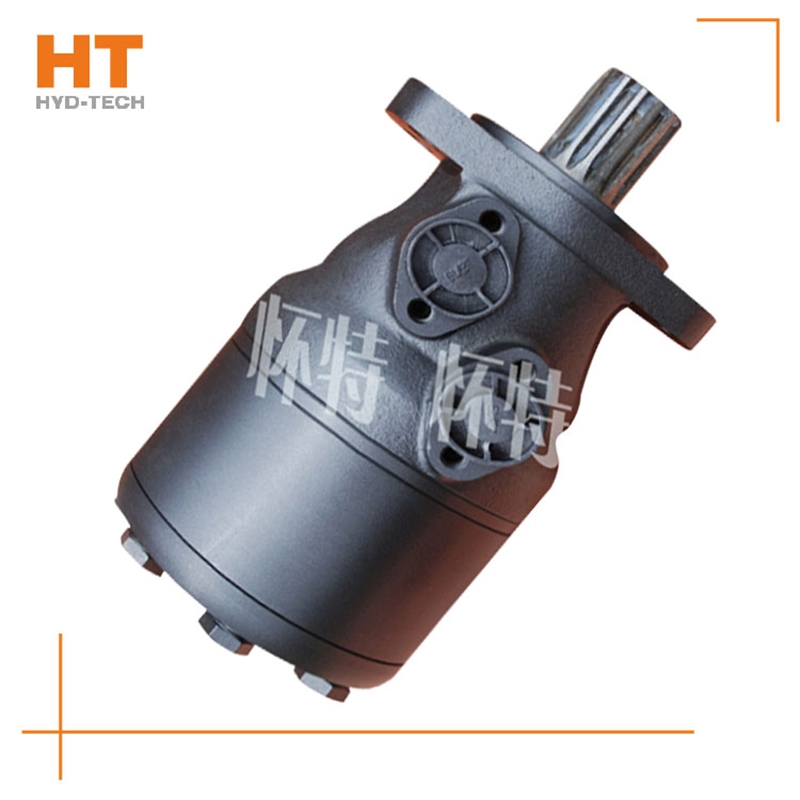
As the power source and actuator of the hydraulic system, the performance of the hydraulic motor has a great impact on the performance of the entire hydraulic system. Therefore, the importance of studying the hydraulic motor performance test system is special-purpose orbit motor It is very important that the rise and application of hydraulic testing technology based on virtual instrument has opened up a broad prospect for the performance testing of hydraulic motors. Hydraulic motors are widely used in machine tools, metallurgy, engineering machinery, plastic machinery, agricultural machinery, mining machinery, marine machinery and many other important fields. The performance of the hydraulic motor has a decisive impact on the whole system, and will directly affect the stability of the system. At the same time, the performance of the hydraulic motor will have an impact on the life of the system components and the production efficiency of the system. Shaoxing Manufacturer Unexpected failure of hydraulic motor will greatly reduce production efficiency.
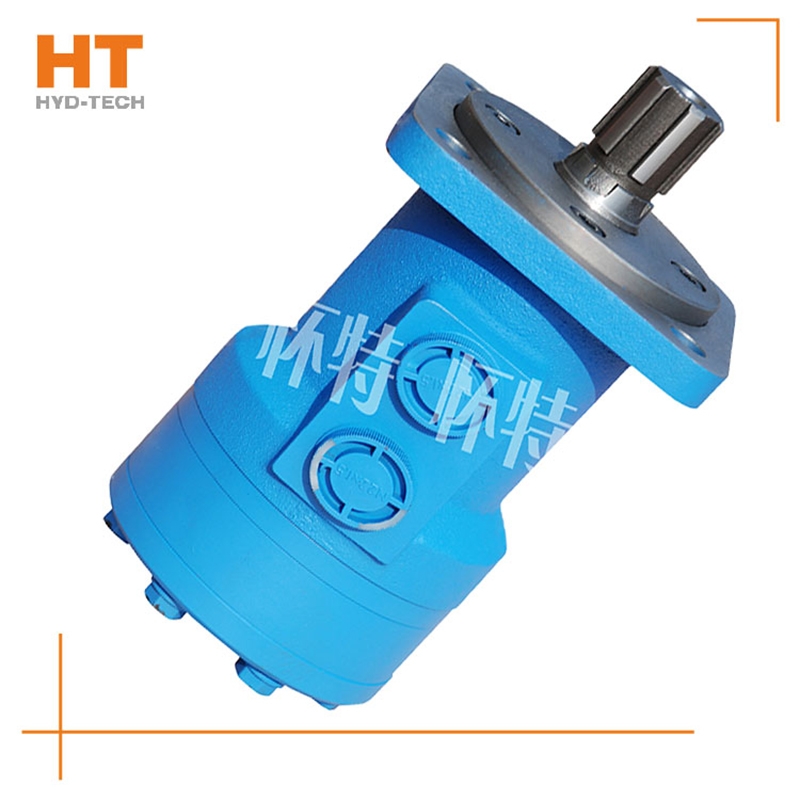
The oil distribution sleeve is synchronized with the rotor, so that the rotor rotates once, and the seven oil distribution holes on the housing are closed 840 times by the twelve diaphragms of the oil distribution sleeve, while the rotor and stator form the largest and smallest closed cavities respectively 1420 times, collectively referred to as the seal cavity. In the circle of the oil distribution hole of the closed housing, the oil inlet and outlet of the rotor have three chambers respectively, one Shaoxing orbit motor The cavity is closed. When the rotor is transferred from the smallest enclosed cavity to the next largest enclosed cavity, before the rotor is transferred from the largest enclosed cavity to the next smallest enclosed cavity, oil is supplied to four cavities and three cavities special-purpose orbit motor Drain the oil.