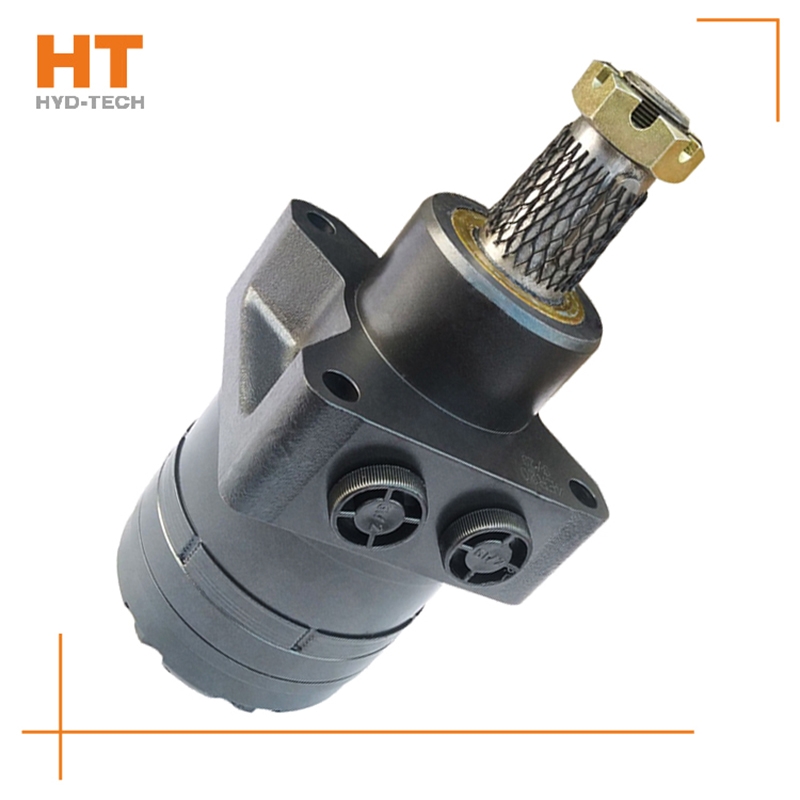
The valve control system controls the flow by changing the opening of the valve throttle, thus controlling the speed of the actuator. Usually, the reason for low efficiency is the existence of throttling and overflow losses. Almost all mechanical equipment adopts valve control system. The pump control system can realize the stepless control of speed by changing the displacement of variable displacement pump, or control the flow through the combination of multiple constant displacement pumps to achieve the stepwise control of speed. The reason for high efficiency is that there is no throttling or overflow loss. It is widely used in high power hydraulic devices such as pressure processing machinery and plastic machinery. The actuator control system controls the flow by changing the variable hydraulic motor flow of the actuator, or through the joint work of multiple quantitative hydraulic motors, or by changing the action area of the composite hydraulic cylinder. Similar to the pump control system, this system has high efficiency because it has no throttling and overflow losses. It is suitable for traveling machinery, press and other hydraulic equipment.
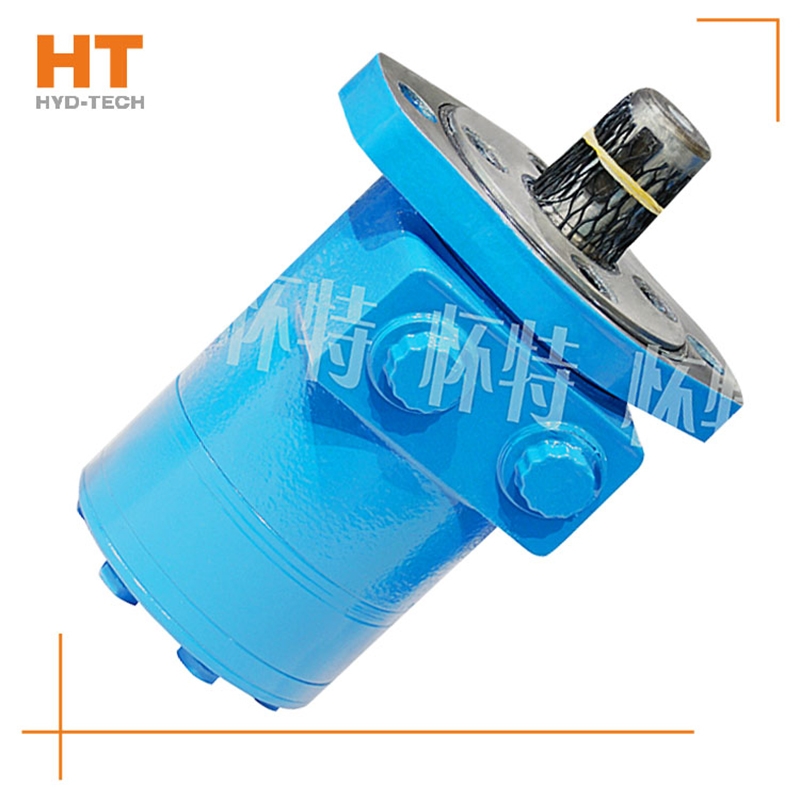
1. Air intrusion. When the air intrudes into the hydraulic system, it has a large volume in the low-pressure area. When it enters the high-pressure area, it is compressed, and the volume suddenly decreases. When it enters the low-pressure area, the volume suddenly increases, resulting in a sudden change in the bubble volume, that is, "explosion" phenomenon, resulting in noise. Solution: Generally, the hydraulic cylinder is equipped with an exhaust device want to buy OM cycloidal motor Exhaust. In addition, a common method is to exhaust the actuator several times during the fast full stroke after startup. 2. The quality of the hydraulic pump or motor is poor. The quality of the hydraulic pump is poor, the accuracy does not fully meet the technical requirements, the pressure and flow fluctuations are large, the oil trapping phenomenon has not been eliminated well, and poor sealing and poor bearing quality are the main reasons for the noise. In use, due to wear of hydraulic pump parts, excessive clearance, insufficient flow Yuyao Manufacturer The force is easy to fluctuate and will also produce noise.
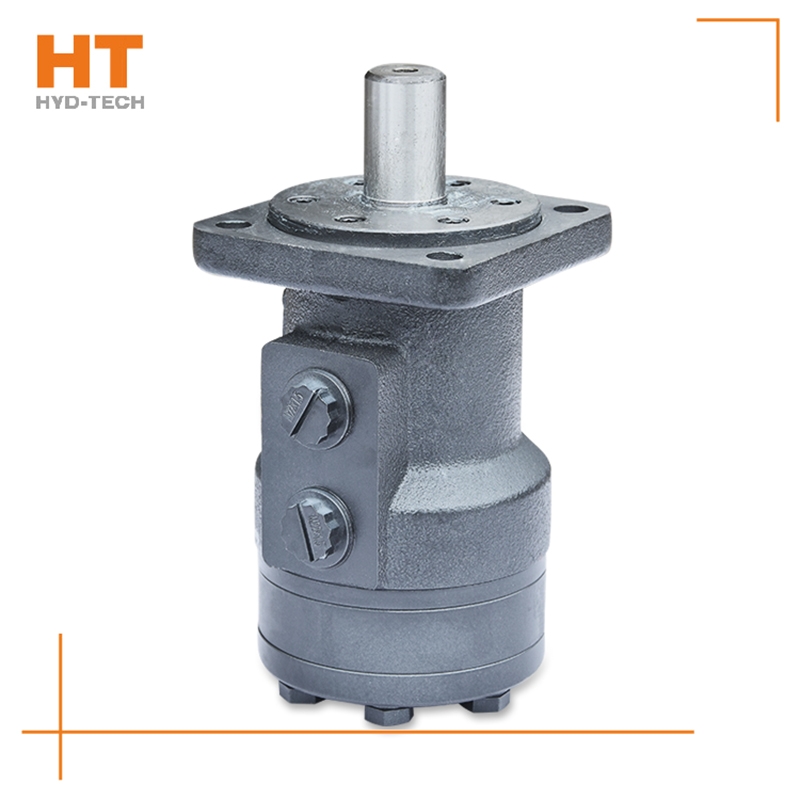
Hydraulic motors are divided into high-speed hydraulic motors and low-speed hydraulic motors. They are widely used in many aspects. The manufacturer told us that they are convenient to use and suitable for high-speed hydraulic motors. First, its adjustment sensitivity is very high: due to special structural design and composition, high-speed hydraulic motors generally have high adjustment sensitivity, especially in speed adjustment OM cycloidal motor Manufacturer This is especially true during the integration and commutation. In this way, the user can make the motor itself respond sensitively and enter the corresponding working state through simple operation when using the motor. Second, get up Yuyao Manufacturer It is very convenient to move and brake: because the high-speed hydraulic motor has the characteristics of high speed and small moment of inertia, it can easily enter the corresponding state when starting and braking in application. This convenience is an important part of its convenient application. High speed hydraulic motor has many advantages, which brings us great convenience.
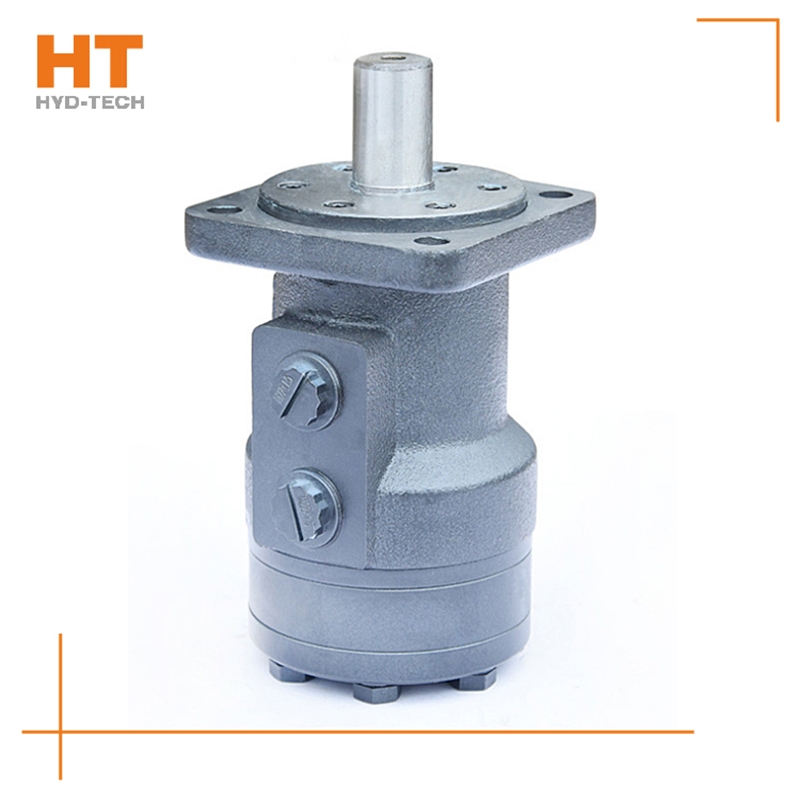
Along the revolution direction of the rotor, the volume of the tooth cavity at the front side of the connection between the rotor and the stator becomes smaller, which is an oil discharge cavity, and the volume at the rear side becomes larger. When the connecting line passes through the two tooth roots of the rotor, the oil inlet ends and the largest tooth cavity appears. When the connecting line passes through the two tooth tops of the rotor, the oil drainage ends and the smallest tooth cavity appears. In order to ensure the continuous rotation of the rotor, it is necessary to have the same regular oil distribution mechanism to cooperate with it, so that the tooth cavity at the front side of the connecting pipeline is always connected with the oil drain port, and the rear side is connected with the oil inlet port. As mentioned above, the oil distribution mechanism consists of a housing and an oil distribution sleeve. The 12 longitudinal grooves (x) on the oil distribution sleeve and the 12 intervals formed by the oil distribution groove face the root and top of the rotor through the positioning device, which proves that when the largest and smallest cavities occur, the oil distribution hole of the housing can be closed, thus separating the oil inlet groove and oil outlet groove of the oil distribution sleeve.