Oil filling process sequence: shell oil filler → oil filling sleeve groove → oil filling sleeve groove → shell oil filling hole → diaphragm → stator. Oil drainage process sequence: rotating stator → diaphragm Cycloid hydraulic motor Manufacturer → Shell oil distribution hole → oil distribution jacket longitudinal groove → oil distribution jacket groove → shell oil return port. The rotating motion of the rotor includes rotation (rotation in the direction of expanding the high-pressure cavity around the center of the rotor) and revolution (rotation in the direction of deviation from the radius around the center of the stator). The rotation of the rotor is opposite to the revolution direction, and the rotation is transmitted to the output shaft through the linkage shaft. Rotor rotates for 1 cycle special-purpose Cycloid hydraulic motor The rotor is driven by 42 pressure oil with the maximum volume for 6 revolutions, so the motor has a large emissions.
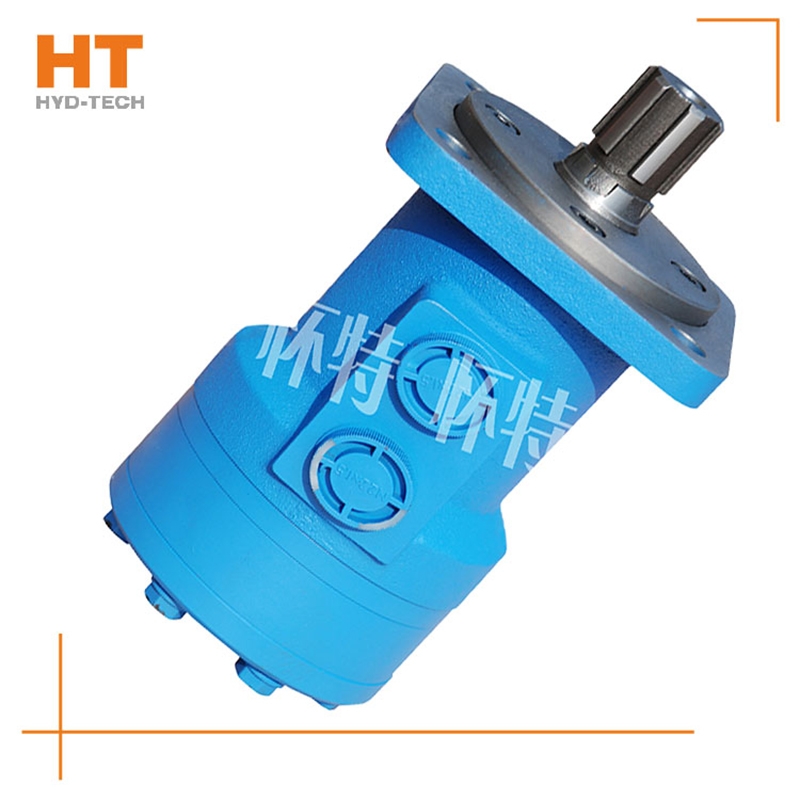
What is the oil supply mode of the hydraulic pump? The straight shaft swashplate plunger pump can be divided into two types: self suction type and pressurized type. Most high-pressure oil supply hydraulic pumps use pneumatic oil tank, and some hydraulic pumps are also equipped with oil make-up slave pump to deliver pressure oil to the oil inlet of the hydraulic pump. The self-priming pump has the characteristics of strong self-priming ability and no need for external oil supply special-purpose Cycloid hydraulic motor 。 Bearings for hydraulic pumps. The most important part of the plunger pump is the bearing. If the bearing has clearance, the normal clearance of the three pairs of friction pairs inside the hydraulic pump cannot be guaranteed. At the same time, the hydrostatic support oil film thickness of each friction pair will be damaged, thus reducing the service life of the plunger pump bearing. According to the data provided by the manufacturer of the hydraulic pump, the average service life of the bearing is 10000 hours. If the service life exceeds this value, a new port shall be replaced. 3、 Conclusion. The service life of the piston pump is related to the maintenance at ordinary times, the quantity and quality of the hydraulic oil, and the cleanliness of the oil. At the same time, avoid Cycloid hydraulic motor Manufacturer The particles in the oil will wear the friction pair of the plunger pump, which is also an effective method to extend its service life.
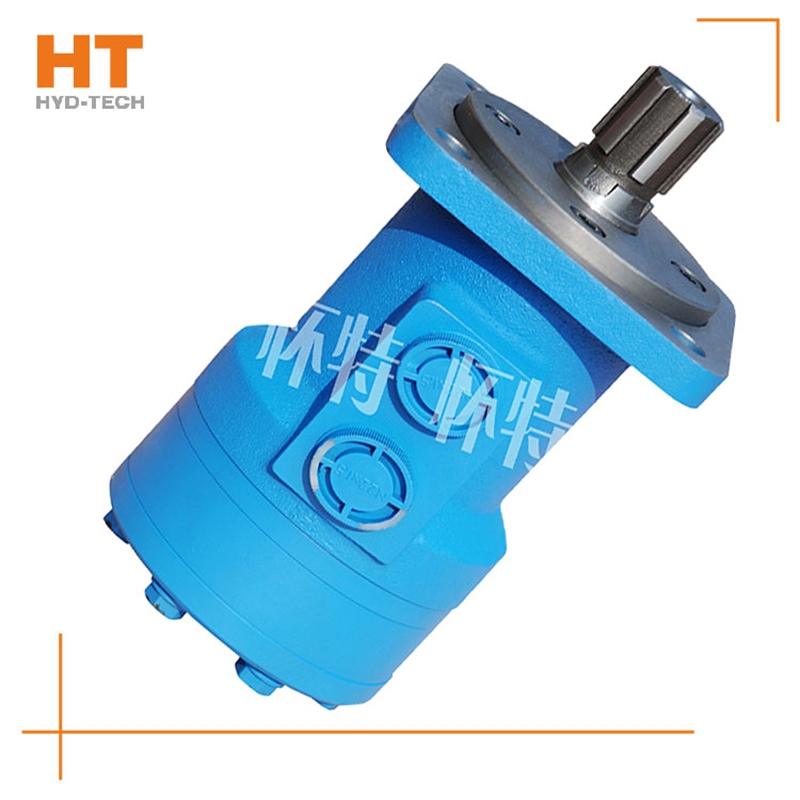
The valve control system controls the flow by changing the opening of the valve throttle, thus controlling the speed of the actuator. Usually, the reason for low efficiency is the existence of throttling and overflow losses. Almost all mechanical equipment adopts valve control system. The pump control system can realize the stepless control of speed by changing the displacement of variable displacement pump, or control the flow through the combination of multiple constant displacement pumps to achieve the stepwise control of speed. The reason for high efficiency is that there is no throttling or overflow loss. It is widely used in high power hydraulic devices such as pressure processing machinery and plastic machinery. The actuator control system controls the flow by changing the variable hydraulic motor flow of the actuator, or through the joint work of multiple quantitative hydraulic motors, or by changing the action area of the composite hydraulic cylinder. Similar to the pump control system, this system has high efficiency because it has no throttling and overflow losses. It is suitable for traveling machinery, press and other hydraulic equipment.
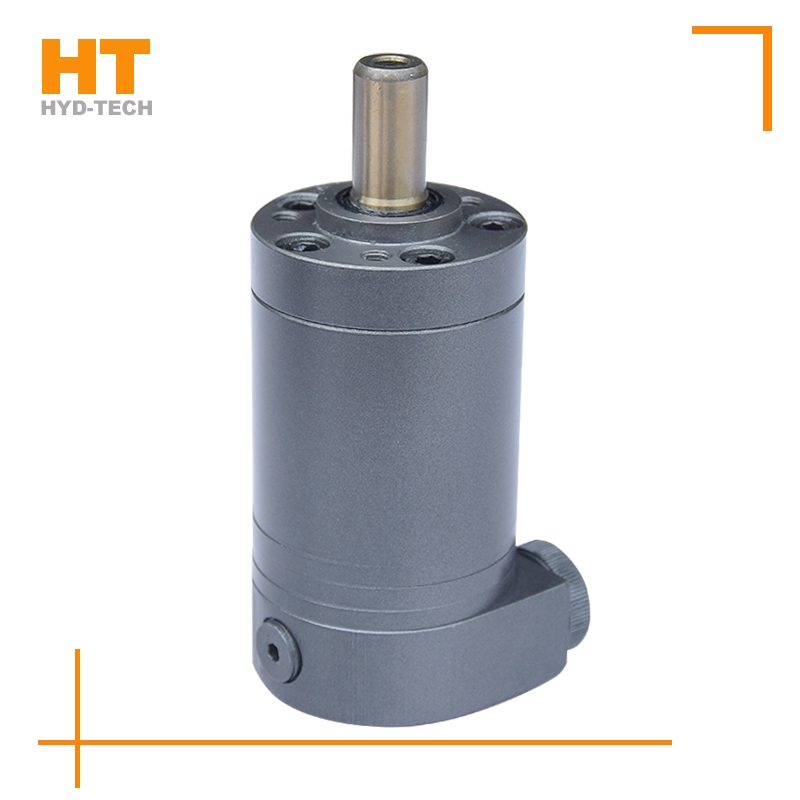
The oil distribution sleeve is synchronized with the rotor, so that the rotor rotates once, and the seven oil distribution holes on the housing are closed 840 times by the twelve diaphragms of the oil distribution sleeve, while the rotor and stator form the largest and smallest closed cavities respectively 1420 times, collectively referred to as the seal cavity. In the circle of the oil distribution hole of the closed housing, the oil inlet and outlet of the rotor have three chambers respectively, one Fushun Cycloid hydraulic motor The cavity is closed. When the rotor is transferred from the smallest enclosed cavity to the next largest enclosed cavity, before the rotor is transferred from the largest enclosed cavity to the next smallest enclosed cavity, oil is supplied to four cavities and three cavities special-purpose Cycloid hydraulic motor Drain the oil.
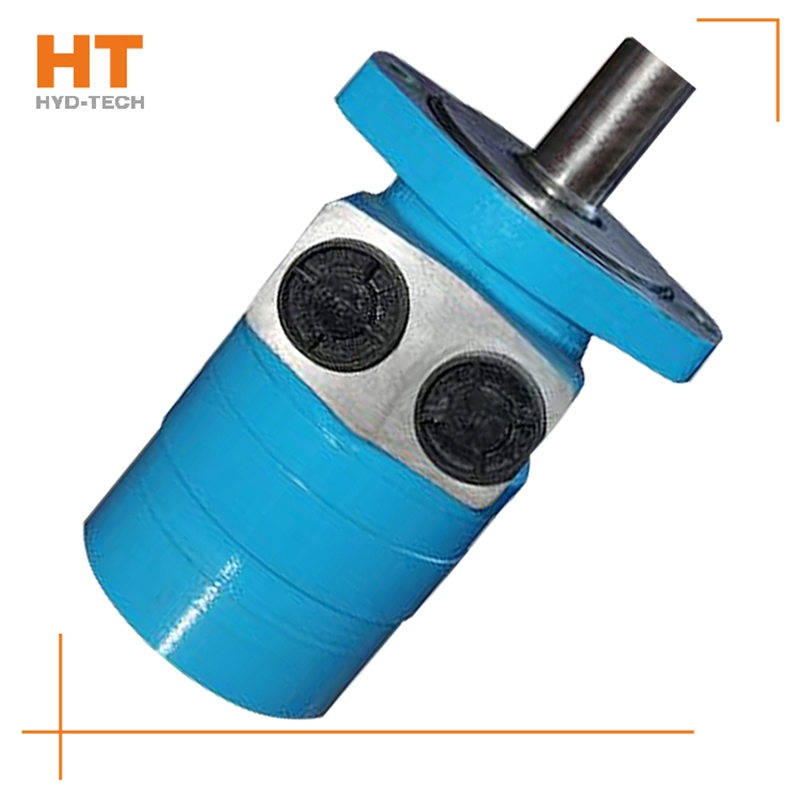
Generally, rolling bearing or hydrostatic sliding bearing, hydraulic special-purpose Cycloid hydraulic motor Since the pressure motor works under the condition of input pressure oil, it does not need to have self-priming capacity, but it needs to have a certain initial air tightness to provide the necessary starting torque. The existence of these differences makes the structure of the hydraulic motor and the hydraulic pump relatively close, but they cannot work reversibly. The classification of hydraulic motors can be divided into gear type, impeller type, plunger type and other types according to the structure type. According to the rated speed of the hydraulic motor, it can be divided into high speed and low speed. The rated speed exceeds 500r/min Fushun Cycloid hydraulic motor High speed hydraulic motor, while the rated speed is lower than 500r/min, it belongs to low speed hydraulic motor.
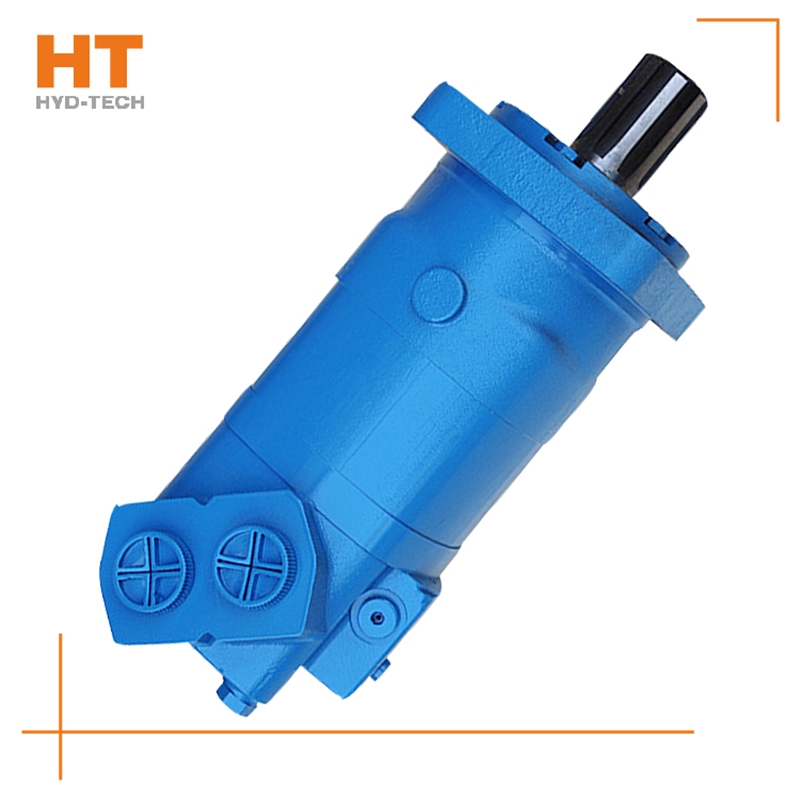
As far as energy conversion is concerned, the hydraulic pump and hydraulic motor are connected as reversible hydraulic components, and the working fluid can be input into any kind of hydraulic pump to make it become a hydraulic motor; On the contrary, when the main shaft of the hydraulic motor rotates under the action of external force Cycloid hydraulic motor Manufacturer It can also become a hydraulic pump. Because they all have the same basic structural elements, namely sealed and recyclable volume and corresponding distribution mechanism. However, the working environment of hydraulic motor and hydraulic pump is different special-purpose Cycloid hydraulic motor The performance requirements are also different. Therefore, there are many differences between the hydraulic motor and the hydraulic pump of the same model. The first hydraulic motor should be positive and negative, so its internal structure should be symmetrical; The speed range of the motor must be large enough, especially its minimum stable speed must have certain requirements.