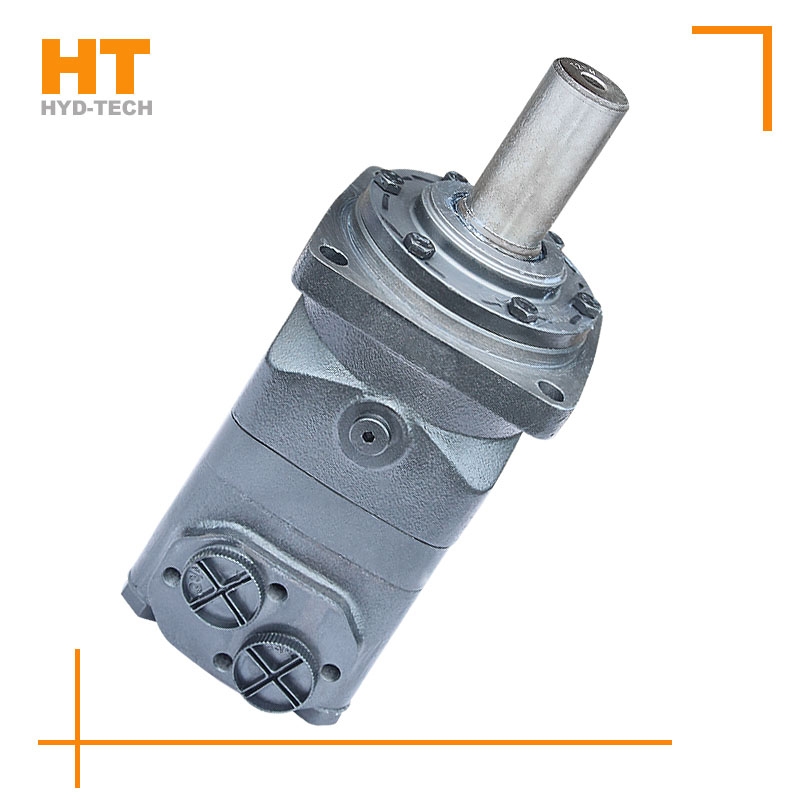
The hydraulic motor has two circuits: the hydraulic motor series circuit and the hydraulic motor braking circuit. These two circuits can be classified into the next category. One of the series circuits of hydraulic motors: three hydraulic motors are connected in series with each other, and a reversing valve is used to control the start stop and steering. The flow through the three motors is basically the same. When the displacement is the same, the speed of each motor is basically the same. The oil supply pressure of the hydraulic pump Zhengzhou manufactor High, small pump flow, generally used for light load and high speed. Serial circuit II of hydraulic motor: each reversing valve in this circuit controls one motor, each motor can work independently or simultaneously, and the rotation direction of each motor is also want to buy OM cycloidal motor optional. The oil supply pressure of the hydraulic pump is the sum of the working pressure difference of each motor, which is applicable to the condition of high speed and small torque.
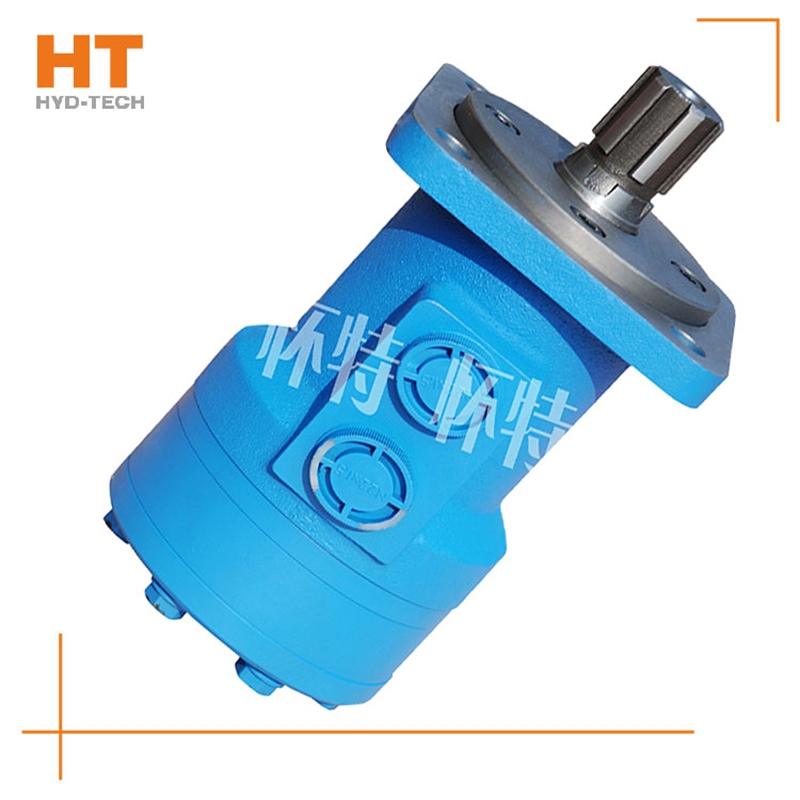
1. Air intrusion. When the air intrudes into the hydraulic system, it has a large volume in the low-pressure area. When it enters the high-pressure area, it is compressed, and the volume suddenly decreases. When it enters the low-pressure area, the volume suddenly increases, resulting in a sudden change in the bubble volume, that is, "explosion" phenomenon, resulting in noise. Solution: Generally, the hydraulic cylinder is equipped with an exhaust device want to buy OM cycloidal motor Exhaust. In addition, a common method is to exhaust the actuator several times during the fast full stroke after startup. 2. The quality of the hydraulic pump or motor is poor. The quality of the hydraulic pump is poor, the accuracy does not fully meet the technical requirements, the pressure and flow fluctuations are large, the oil trapping phenomenon has not been eliminated well, and poor sealing and poor bearing quality are the main reasons for the noise. In use, due to wear of hydraulic pump parts, excessive clearance, insufficient flow Zhengzhou manufactor The force is easy to fluctuate and will also produce noise.
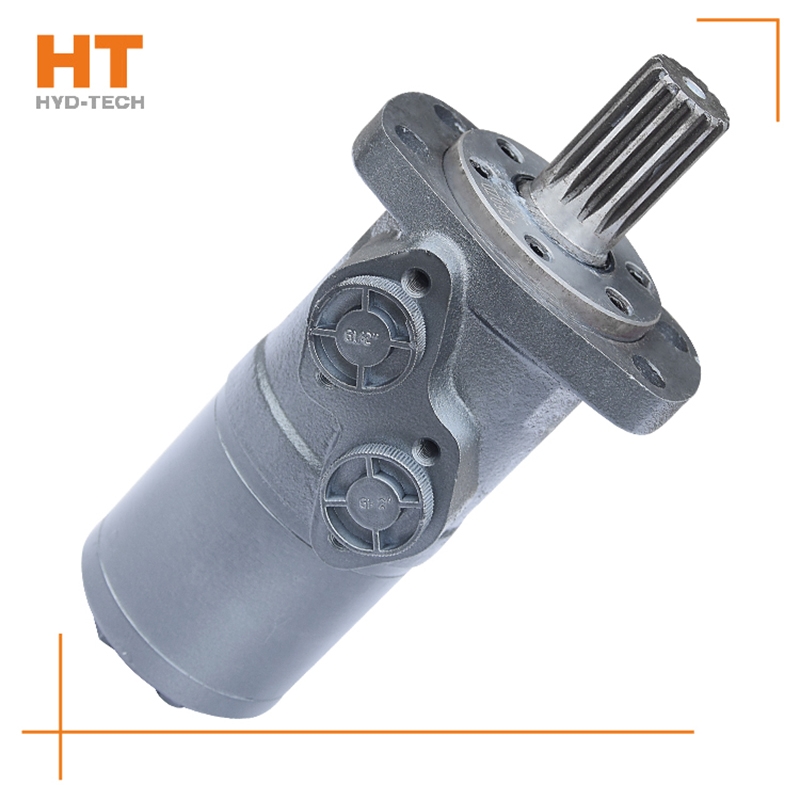
(1) Oil leakage at the shaft end: because the oil seal and output shaft are under constant friction during the use of the hydraulic motor, the wear of the contact surface between the oil seal and the shaft will be caused Zhengzhou OM cycloidal motor A certain limit will make the oil seal lose its sealing effect, and oil will leak. Our solution is very simple: replace the oil seal. If the output shaft is seriously worn, it must be replaced. (2) Crevice oil leakage: the "O" ring between the motor housing and the front side plate, or between the front side plate and the stator body, is aged OM cycloidal motor manufactor Just replace the "O" ring. (3) Oil leakage at the cover: the "O" ring under the cover is aged and loses its sealing effect. The probability of this situation is very low, even if it happens, just replace the "O" ring.
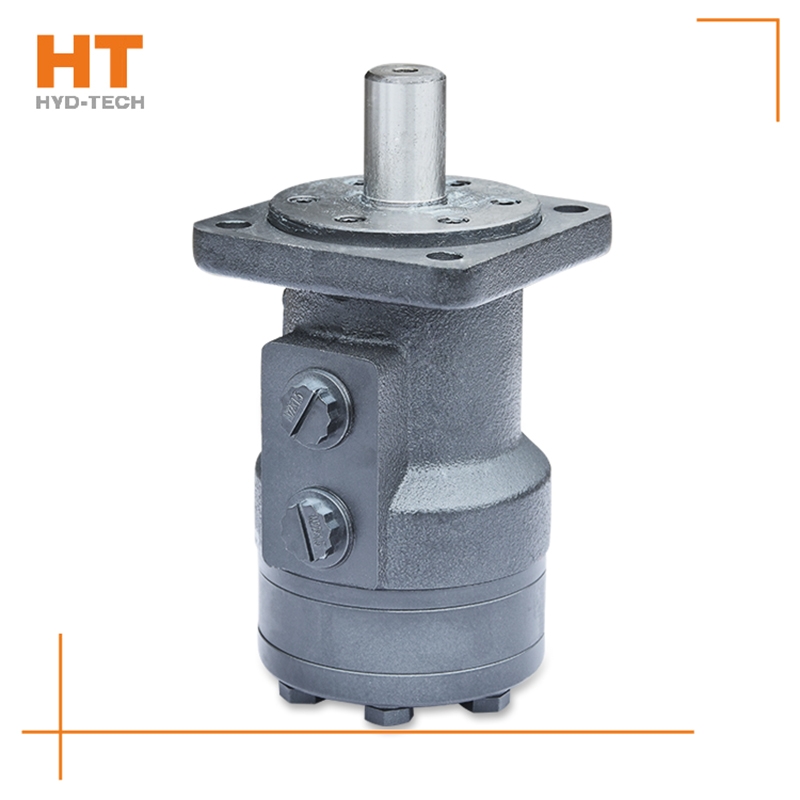
Along the revolution direction of the rotor, the volume of the tooth cavity at the front side of the connection between the rotor and the stator becomes smaller, which is an oil discharge cavity, and the volume at the rear side becomes larger. When the connecting line passes through the two tooth roots of the rotor, the oil inlet ends and the largest tooth cavity appears. When the connecting line passes through the two tooth tops of the rotor, the oil drainage ends and the smallest tooth cavity appears. In order to ensure the continuous rotation of the rotor, it is necessary to have the same regular oil distribution mechanism to cooperate with it, so that the tooth cavity at the front side of the connecting pipeline is always connected with the oil drain port, and the rear side is connected with the oil inlet port. As mentioned above, the oil distribution mechanism consists of a housing and an oil distribution sleeve. The 12 longitudinal grooves (x) on the oil distribution sleeve and the 12 intervals formed by the oil distribution groove face the root and top of the rotor through the positioning device, which proves that when the largest and smallest cavities occur, the oil distribution hole of the housing can be closed, thus separating the oil inlet groove and oil outlet groove of the oil distribution sleeve.