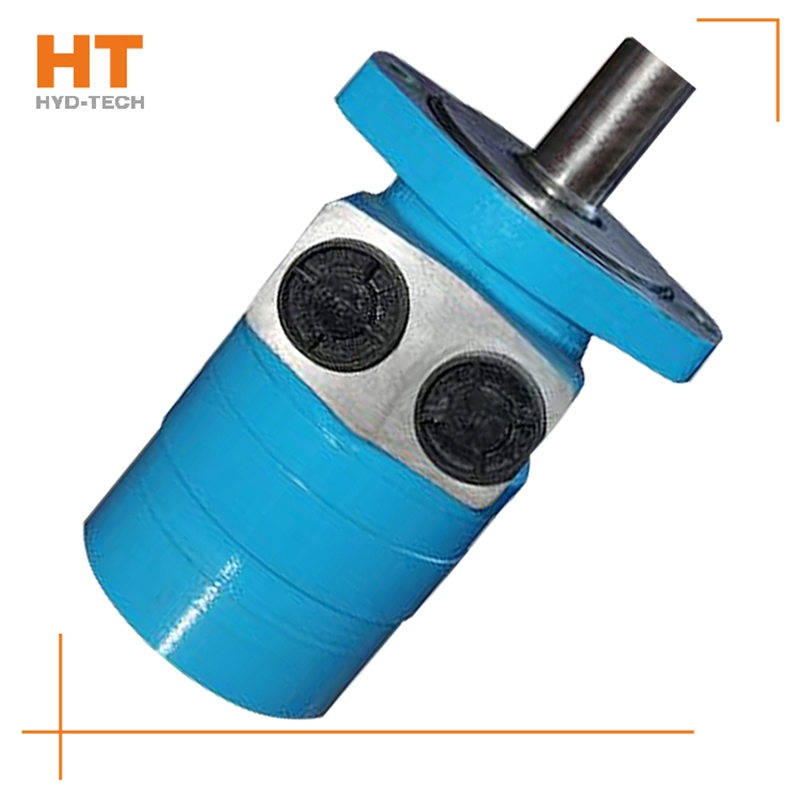
The ignition time of internal combustion engines can be compared with this. It can be seen from the working principle of the cycloidal hydraulic motor that the oil sleeve and the rotor rotate synchronously, and the accuracy refers to the accuracy of the oil distribution link matching with the rotor to rotate the oil inlet, seal and discharge. There are many factors want to buy Low speed high torque cycloidal hydraulic motor It will affect the oil distribution accuracy, such as the asymmetry of the rotor spline and cycloid tooth shape, the relative position accuracy of the stator sleeve needle hole and bolt hole, and the relative position asymmetry of the pin hole and spline on the output shaft and its internal spline, Low speed high torque cycloidal hydraulic motor manufactor The relative position accuracy of the longitudinal oil groove and the relative wedge groove of the coupling, and the asymmetry of splines at both ends of the coupling. As long as the above factors are controlled within the tolerance range, they will not have a great impact on the oil distribution accuracy, because all processing errors will not be offset.
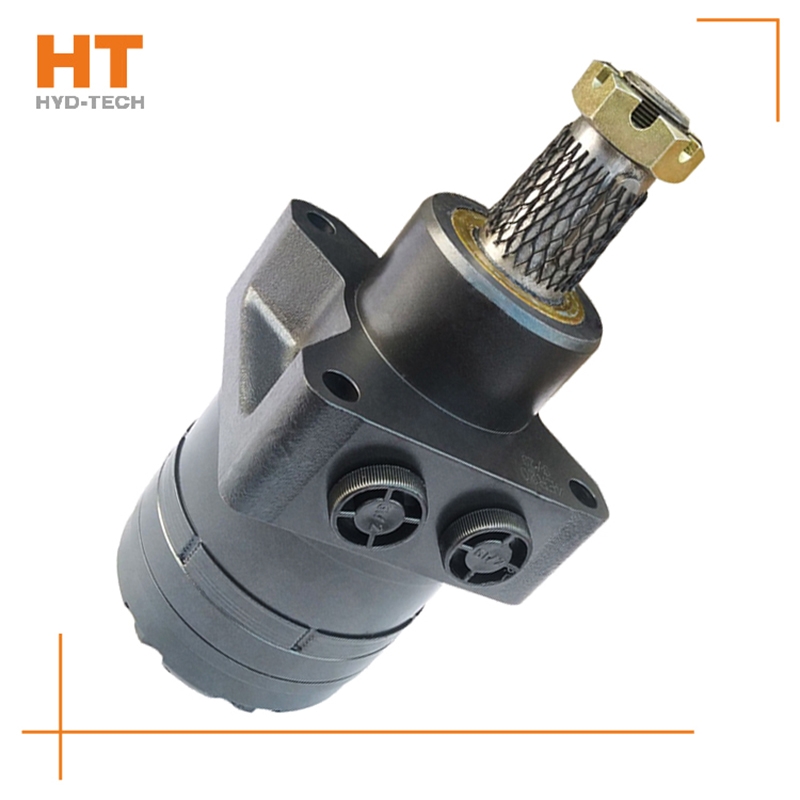
In the late 1850s, the original low-speed high torque hydraulic motor was developed from the fixed rotor part of the oil pump, which consists of an internal gear ring and matching teeth ynz manufactor Wheel or rotor. The inner gear ring is fixedly connected with the housing, and the oil entering from the oil port pushes the rotor to rotate around the center point. This slowly rotating rotor is driven and output by a spline shaft to become a cycloidal hydraulic motor. After the first cycloid motor came out, after decades of evolution, Jinjia hydraulic hydraulic motor delivers high efficiency energy for you. Another concept of motor also began to form. The motor installs the drum in the built-in ring gear. Motors with rollers can provide high starting Low speed high torque cycloidal hydraulic motor manufactor With the running torque, the drum reduces friction and improves efficiency. The low speed output shaft can also produce stable output.
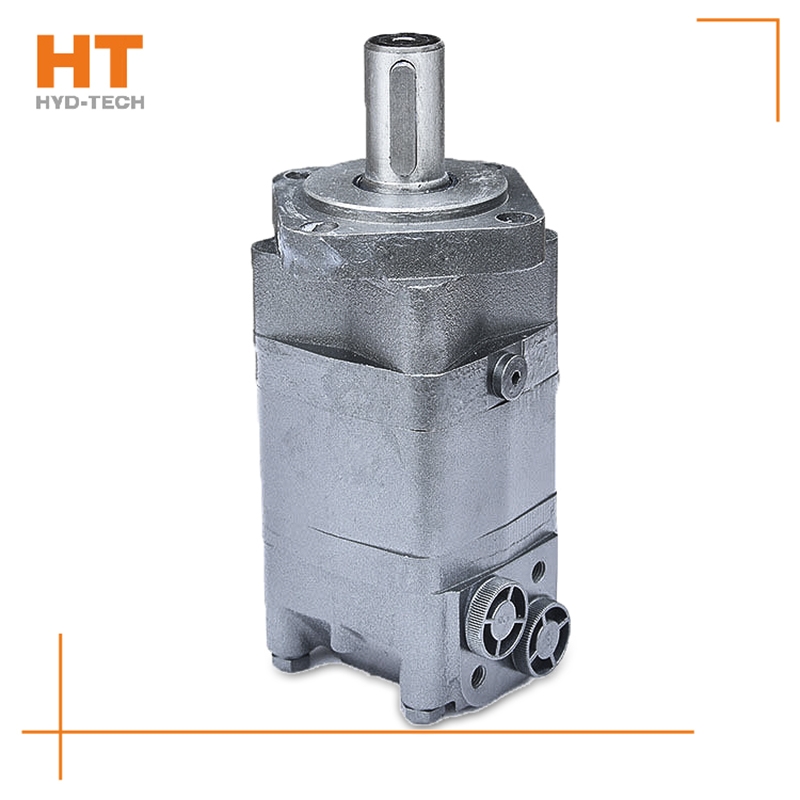
Most of its hydraulic system uses working medium, such as hydraulic oil with continuous fluidity, which converts the mechanical energy of the prime mover driving the pump into the pressure energy of the liquid through the hydraulic pump, and sends it to the actuator (hydraulic cylinder, hydraulic motor or swing hydraulic motor) through various control valves, such as pressure, flow, direction, etc., to convert it into mechanical energy to drive the load. This hydraulic system is generally composed of the following parts: power source, actuator, control valve, hydraulic auxiliary device and hydraulic working medium, which play their respective roles: power source: prime mover (motor or internal combustion engine) and hydraulic pump, whose role is to convert the mechanical energy generated by the prime mover into the pressure energy of liquid, and output oil with a certain pressure;
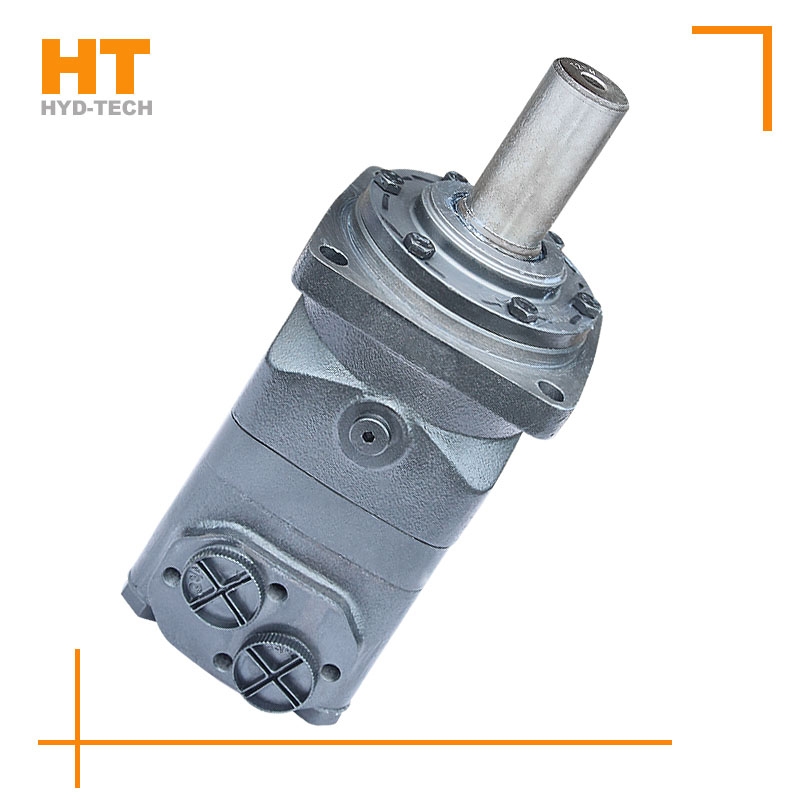
Along the revolution direction of the rotor, the volume of the tooth cavity at the front side of the connection between the rotor and the stator becomes smaller, which is an oil discharge cavity, and the volume at the rear side becomes larger. When the connecting line passes through the two tooth roots of the rotor, the oil inlet ends and the largest tooth cavity appears. When the connecting line passes through the two tooth tops of the rotor, the oil drainage ends and the smallest tooth cavity appears. In order to ensure the continuous rotation of the rotor, it is necessary to have the same regular oil distribution mechanism to cooperate with it, so that the tooth cavity at the front side of the connecting pipeline is always connected with the oil drain port, and the rear side is connected with the oil inlet port. As mentioned above, the oil distribution mechanism consists of a housing and an oil distribution sleeve. The 12 longitudinal grooves (x) on the oil distribution sleeve and the 12 intervals formed by the oil distribution groove face the root and top of the rotor through the positioning device, which proves that when the largest and smallest cavities occur, the oil distribution hole of the housing can be closed, thus separating the oil inlet groove and oil outlet groove of the oil distribution sleeve.