The hydraulic motor is usually put into operation Yantai special-purpose Clean before use. The purpose of cleaning is to remove the pollutants, metal chips, fiber compounds and iron cores left in Madai. In the first two hours of operation, even if the motor is not completely damaged, there will be a series of failures. Therefore, the hydraulic motor oil circuit should be cleaned as follows: 1. Clean the oil tank with easy drying cleaning solvent, and then remove the solvent residue with filtered air. 2. Clean all pipes of hydraulic motor. In some cases, it may be necessary to impregnate pipes and joints. 3. Install an oil filter on the pipeline to protect the oil supply pipeline and pressure pipeline of the valve. four special-purpose Hydraulic cycloid motor Install a flushing plate on the collector to replace precision valves, such as electro-hydraulic servo valve. 5. Check whether all pipes are of proper size and connected correctly.
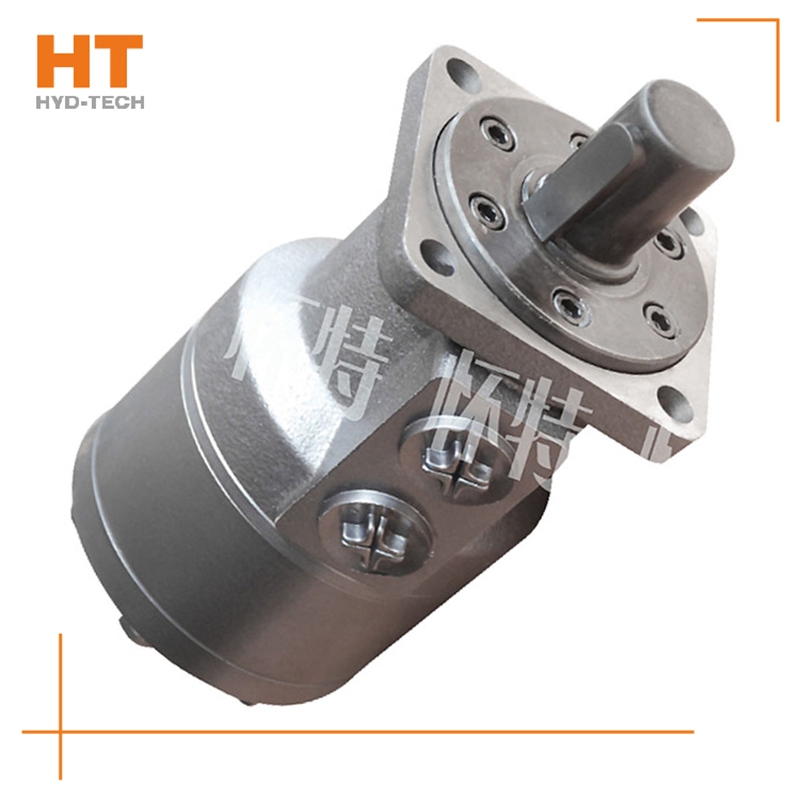
When the high-pressure oil enters the oil distribution shaft and enters each plunger cylinder hole of the working section through the oil distribution window, the corresponding plunger set is pushed against the curved surface of the cam ring L (housing), Yantai Hydraulic cycloid motor The cam ring surface gives a reaction force to the plunger at the contact position. This reaction force N acts on the common plane where the cam ring surface contacts the roller. This normal reaction force N can be decomposed into radial force PH and circumferential force T, which are balanced with the hydraulic pressure at the bottom of the plunger, while the circumferential force T overcomes the load torque, special-purpose Hydraulic cycloid motor Drive cylinder 2 to rotate. Under this working condition, the cam ring and oil distribution shaft do not rotate. At this time, the plunger corresponding to the oil return section of the cam gear moves in the opposite direction, and the oil is discharged through the oil distribution shaft.
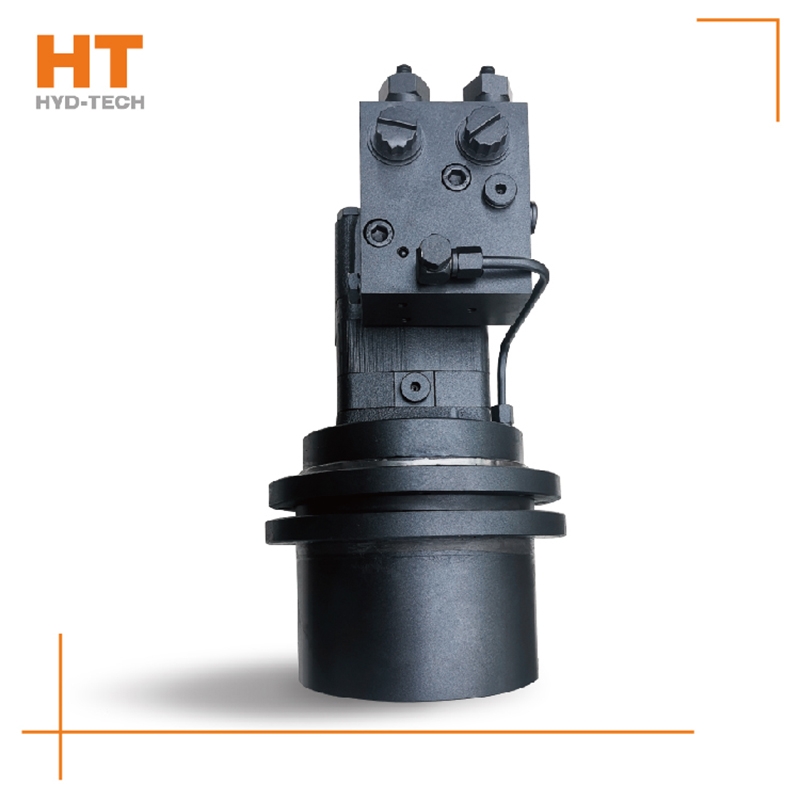
Oil filling process sequence: shell oil filler → oil filling sleeve groove → oil filling sleeve groove → shell oil filling hole → diaphragm → stator. Oil drainage process sequence: rotating stator → diaphragm Hydraulic cycloid motor Manufacturer → Shell oil distribution hole → oil distribution jacket longitudinal groove → oil distribution jacket groove → shell oil return port. The rotating motion of the rotor includes rotation (rotation in the direction of expanding the high-pressure cavity around the center of the rotor) and revolution (rotation in the direction of deviation from the radius around the center of the stator). The rotation of the rotor is opposite to the revolution direction, and the rotation is transmitted to the output shaft through the linkage shaft. Rotor rotates for 1 cycle special-purpose Hydraulic cycloid motor The rotor is driven by 42 pressure oil with the maximum volume for 6 revolutions, so the motor has a large emissions.
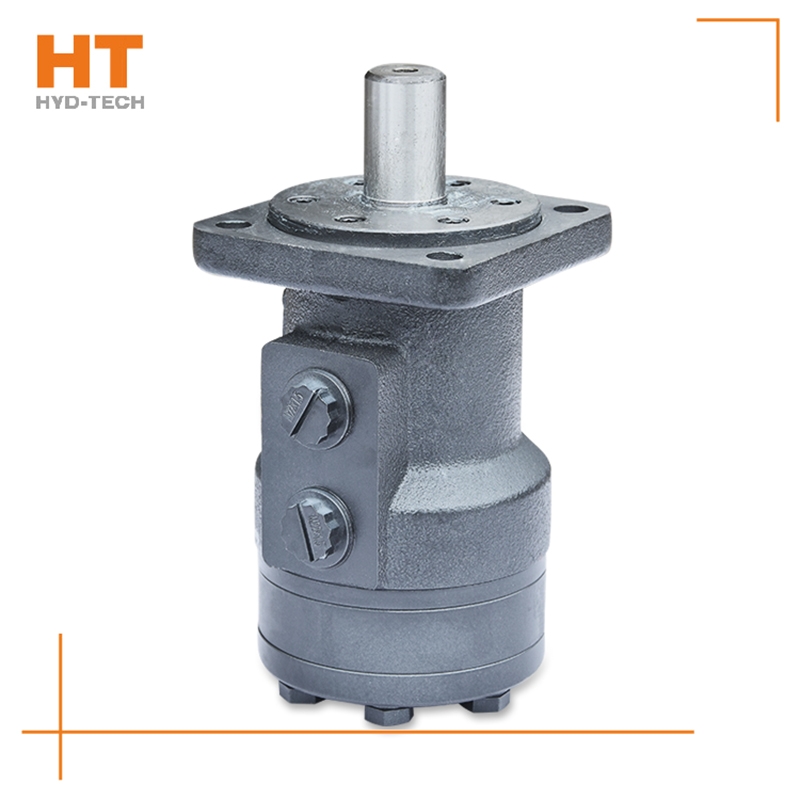
Along the revolution direction of the rotor, the volume of the tooth cavity at the front side of the connection between the rotor and the stator becomes smaller, which is an oil discharge cavity, and the volume at the rear side becomes larger. When the connecting line passes through the two tooth roots of the rotor, the oil inlet ends and the largest tooth cavity appears. When the connecting line passes through the two tooth tops of the rotor, the oil drainage ends and the smallest tooth cavity appears. In order to ensure the continuous rotation of the rotor, it is necessary to have the same regular oil distribution mechanism to cooperate with it, so that the tooth cavity at the front side of the connecting pipeline is always connected with the oil drain port, and the rear side is connected with the oil inlet port. As mentioned above, the oil distribution mechanism consists of a housing and an oil distribution sleeve. The 12 longitudinal grooves (x) on the oil distribution sleeve and the 12 intervals formed by the oil distribution groove face the root and top of the rotor through the positioning device, which proves that when the largest and smallest cavities occur, the oil distribution hole of the housing can be closed, thus separating the oil inlet groove and oil outlet groove of the oil distribution sleeve.
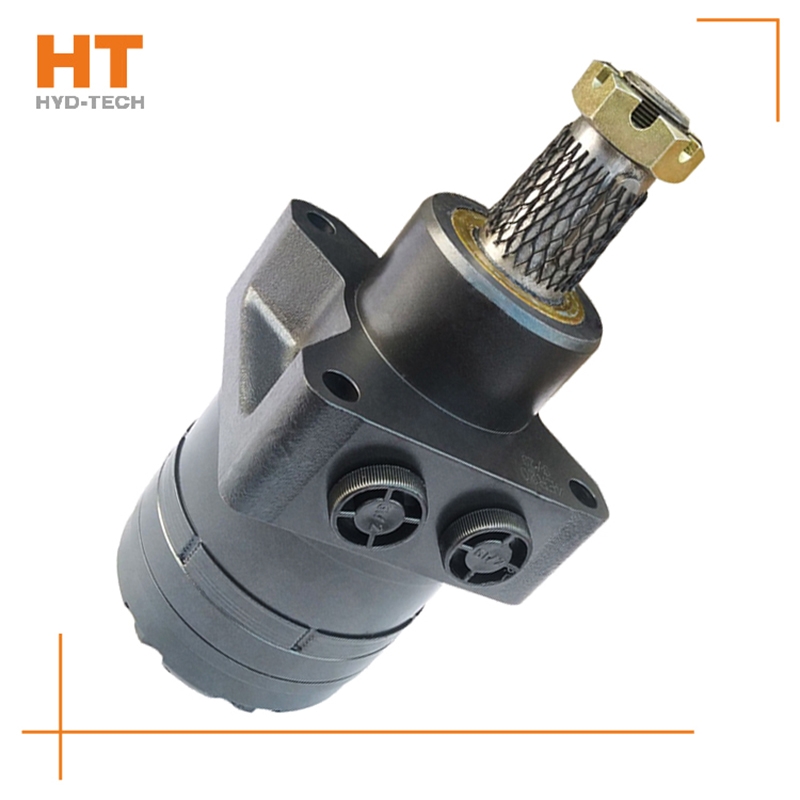
With the rapid development of China's economy, since the reform and opening up, the machinery industry has improved the advanced productivity in China by constantly introducing foreign technology. Especially after China's accession to the WTO, the machinery industry has accelerated scientific and technological innovation, and the annual export of equipment has continued to grow. With the continuous technological innovation of the hydraulic press industry in China, a number of high-tech industrial companies have emerged, and there are thousands of domestic production enterprises with a certain scale. Hydraulic press products are commonly used in stamping processing and stamping forming processes, such as forging, stamping, cold extrusion, straightening, bending, flanging, plate stretching, powder metallurgy, press fitting, etc. They are metal, plastic, rubber, wood, powder and other products. It can not only meet the functional diversification of electromechanical products to the maximum extent, but also is the basic guarantee for completing major projects and major technological transformation. Now the hydraulic press products have been widely used in automobile, engineering machinery, agricultural machinery, machine tools, plastic machinery, metallurgy and mining, power generation equipment, railway, ship, light industry, electronics, and defense industry products.