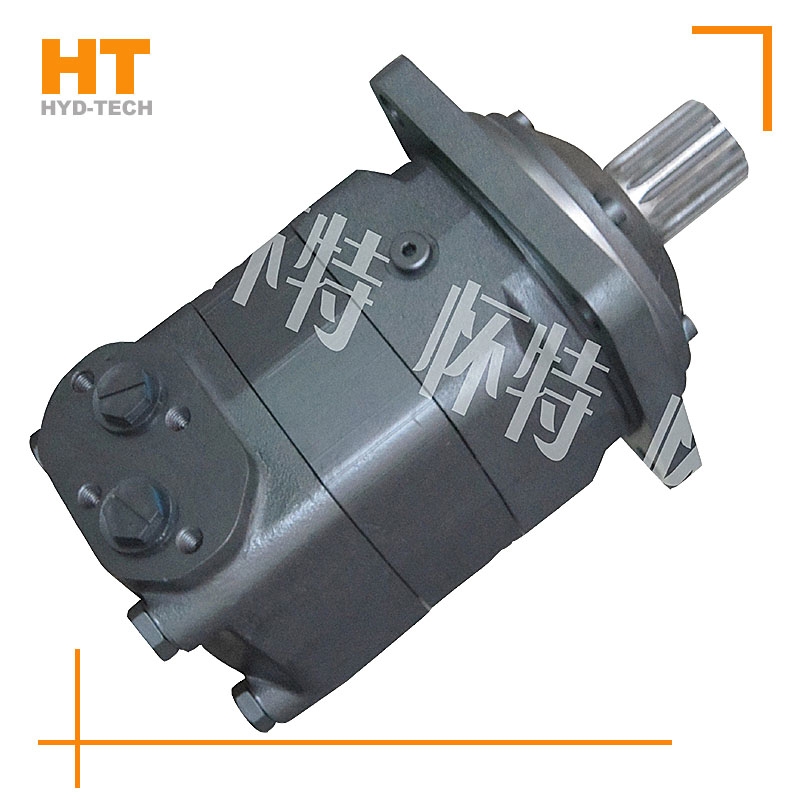
The hydraulic motor manufacturer explains to you the reasons for the poor performance of the hydraulic motor: 1. First of all, according to the analysis of the causes of the wear of the port plate, the main reasons for the weakness of the hydraulic motor are: because the port plate is worn, the oil inlet channel and the oil return channel are connected at the port plate, part of the high-pressure oil leaks, the oil pressure flowing through the stator and rotor pair decreases, and the flow decreases, Eventually, the output speed and torque of the motor will decrease. 2. Due to the wear of the valve plate, its relative position in the valve body has changed Danfoss cycloid motor Manufacturer The preload and adhesion of the spring on the valve body between the valve plates will be reduced, which will intensify the leakage of hydraulic oil and lead to the decline of the performance of the hydraulic motor. 3. With the increase of hydraulic oil temperature, its comprehensive performance declines, driving the cycloidal rotor to rotate Fuyang Manufacturer The ability to move is further reduced. Upon inspection, there is no obvious wear on the joint surface of the stator and rotor pair and the bearing seat and valve disc matched with both sides of the stator and rotor pair. The movement is normal without jamming, which will not cause performance degradation.
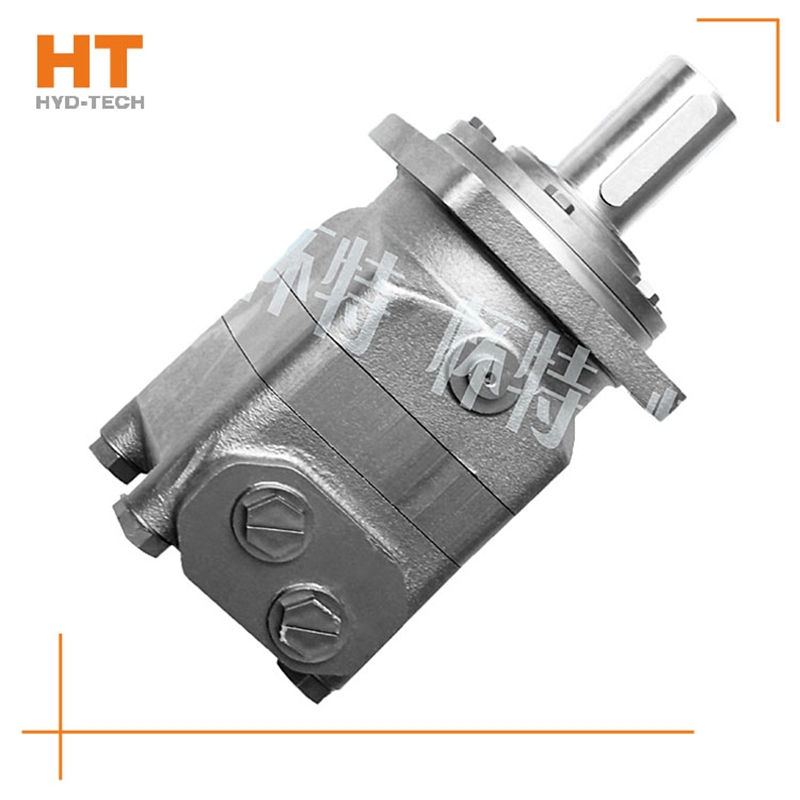
1. Generally, the motor shall be able to run forward and backward. Therefore, the hydraulic motor is usually required to have structural symmetry in the design. 2. The actual working pressure difference of the hydraulic motor depends on the load torque. When the moment of inertia of the driven load is large and the speed is high, rapid braking or reverse rotation is required, high hydraulic impact will be generated. Therefore, the system should be equipped with necessary safety valves and buffer valves. 3. Under normal working conditions, the inlet and outlet pressure of the hydraulic motor is higher than the atmospheric pressure, so there is no suction performance problem like the hydraulic pump. However, if the hydraulic motor can work under pump conditions, its oil inlet should have a minimum pressure limit to avoid cavitation. 4. Some hydraulic motors must have sufficient back pressure at the oil return port to ensure normal operation. The higher the speed, the greater the back pressure, which indicates that the utilization rate of oil source pressure is not high and the system loss is increased. 5. Because the internal leakage of the motor is inevitable, there will be slow sliding when the hydraulic motor oil outlet is closed for braking. Therefore, when long-term accurate braking is required, a separate anti-skid brake shall be set.
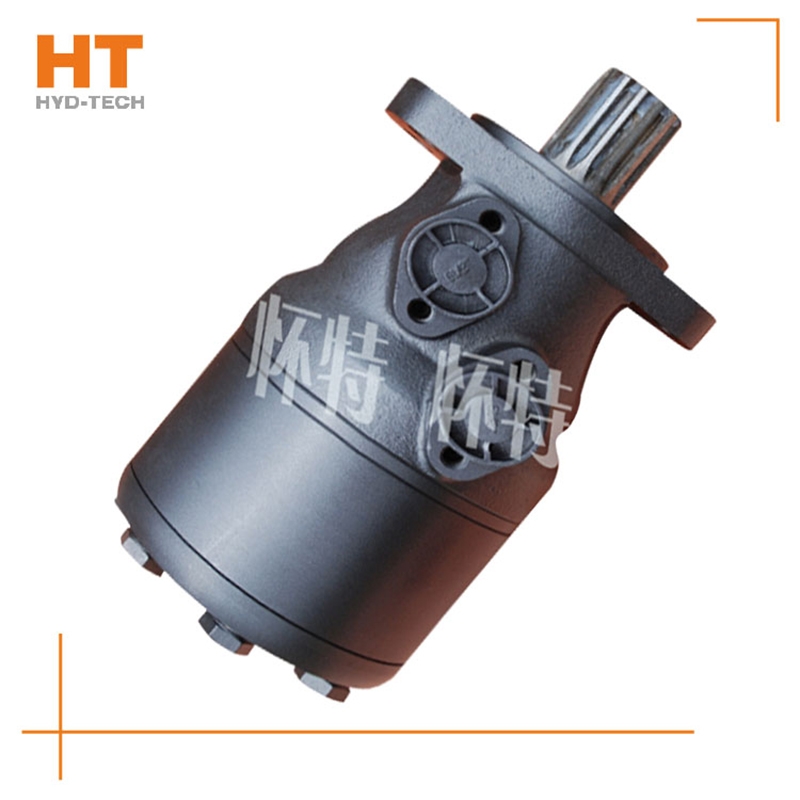
1. Air intrusion. When the air intrudes into the hydraulic system, it has a large volume in the low-pressure area. When it enters the high-pressure area, it is compressed, and the volume suddenly decreases. When it enters the low-pressure area, the volume suddenly increases, resulting in a sudden change in the bubble volume, that is, "explosion" phenomenon, resulting in noise. Solution: Generally, the hydraulic cylinder is equipped with an exhaust device customized Danfoss cycloid motor Exhaust. In addition, a common method is to exhaust the actuator several times during the fast full stroke after startup. 2. The quality of the hydraulic pump or motor is poor. The quality of the hydraulic pump is poor, the accuracy does not fully meet the technical requirements, the pressure and flow fluctuations are large, the oil trapping phenomenon has not been eliminated well, and poor sealing and poor bearing quality are the main reasons for the noise. In use, due to wear of hydraulic pump parts, excessive clearance, insufficient flow Fuyang Manufacturer The force is easy to fluctuate and will also produce noise.
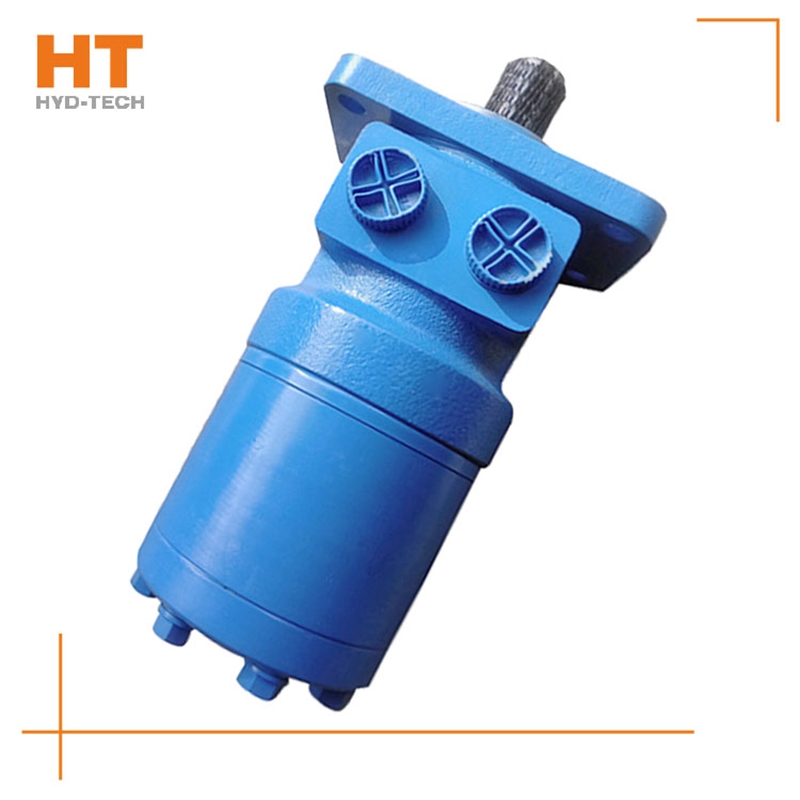
1. Pascal principle: also known as static pressure transmission principle, it refers to the pressure exerted on the static liquid in a closed container is transmitted to all points of the liquid at the same time with equal value. The hyperbolic cosine of 2. The hyperbolic cosine of 2. System pressure: the discharge pressure of the hydraulic pump in the system. The hyperbolic cosine of 3. The hyperbolic cosine of 3. Servo valve and proportional valve: infinitely adjust the output of hydraulic valve, such as pressure, flow and direction, by adjusting the input electrical signal analog quantity. (Servo valve also has pulse customized Danfoss cycloid motor Wide modulation input mode). But the structure of these two valves is completely different. The servo valve controls the work of the torque motor by adjusting the electrical signal to deflect the armature and drive the front valve to work. The front valve control oil enters the main valve and drives the valve core to work. The proportional valve regulates the electrical signal to make the electric iron shift, drive the pilot valve core, drive the control oil generated, and drive the main valve core. The hyperbolic cosine of 4. The hyperbolic cosine of. Fuyang Danfoss cycloid motor Kinematic viscosity: the ratio of dynamic viscosity μ to the liquid density α. The hyperbolic cosine of 5. The hyperbolic cosine of 5. Fluid power: the force exerted by the flowing liquid on the solid wall to change the flow velocity.
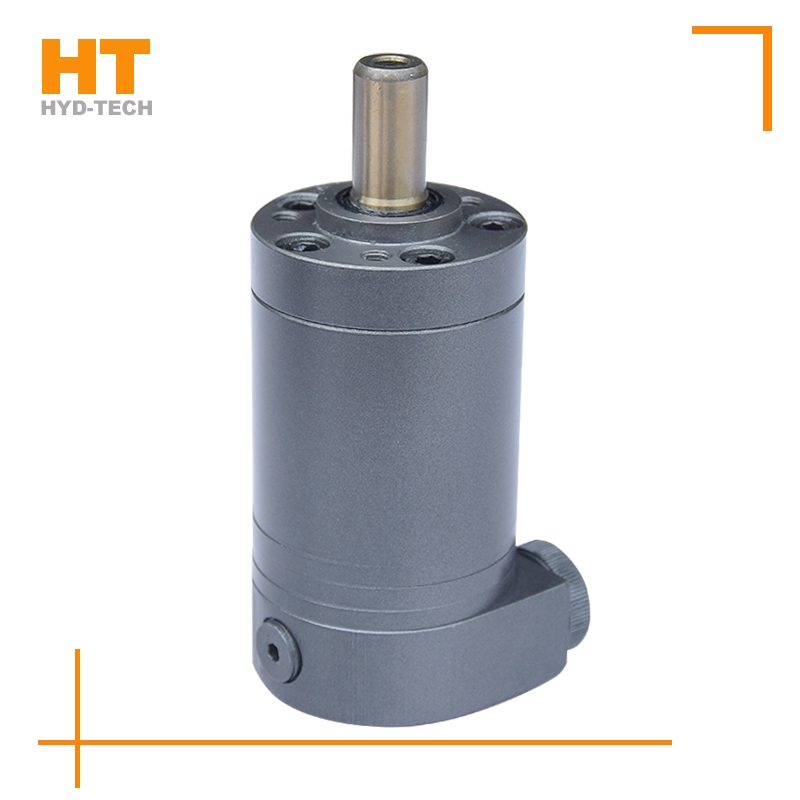
When the main reversing valve of the central closing system and the central closing system is in the neutral position, all oil ports of the reversing valve are closed. If a fixed pump is used for oil supply, the liquid of the hydraulic pump will return to the tank at high pressure through the overflow valve. When the reversing valve is in neutral position, energy transmission starts from the high value, that is, the maximum pressure regulating value of the system. Just reverse Danfoss cycloid motor Manufacturer , its energy can be used by the actuator. When the reversing valve is in the middle position, it sometimes bears all the pressure of the system, so the internal leakage is greater than that of the open system. Generally, when the Fuyang Danfoss cycloid motor In this case, the energy consumption of the closed loop is high, but if the intermediate unloading measures are added or the pressure compensated variable pump is used for oil supply, the energy consumption of the closed loop can be greatly reduced. Closed hydraulic systems are used for a variety of equipment.