Actuator: hydraulic cylinder, hydraulic motor and swing hydraulic motor. Function: convert the pressure energy of liquid into mechanical energy, which is used to drive the working mechanism to do work and realize reciprocating straight customized OM cycloidal motor Linear motion, continuous rotation or swing; Governor: pressure, flow, direction control valve and other control elements. Function: control the oil pressure, flow and direction from the pump to the actuator in the hydraulic system, so as to control the force (torque) and speed output by the actuator the north sea OM cycloidal motor Degree (speed) and direction, to ensure that the main engine working mechanism driven by the actuator can complete the predetermined motion law; Hydraulic auxiliary device: oil tank, pipe fittings, filter, heat exchanger, accumulator, indicating instrument, etc.
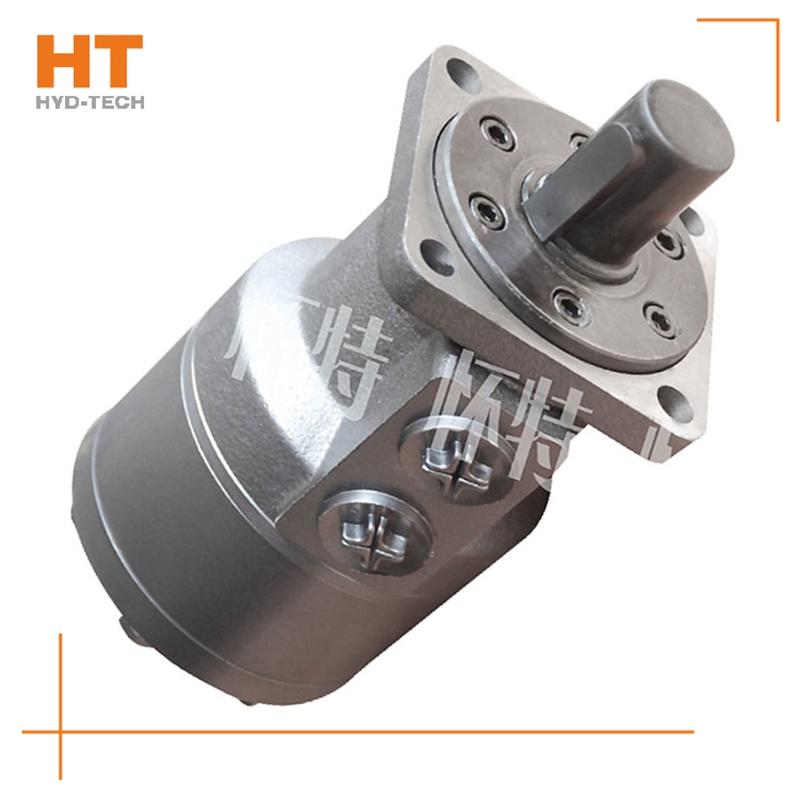
At present, the system used in series by multiple cycloidal motors (see Figure 1) is applied to sweepers, trenchless drills and airport luggage carts. The output shaft of the hydraulic motor often leaks oil during use, so it is useless to replace the dynamic seal of the output shaft. In series application, the problem of casing oil leakage pressure is ignored. The oil leakage pressure of the housing refers to the maximum pressure that the motor shaft seal can bear after the hydraulic motor is fully lubricated inside; If the hydraulic motor is applied customized OM cycloidal motor Improper. After the machine has been working continuously for a period of time, due to various factors, the oil in the housing will not be released, resulting in higher and higher pressure in the housing of the hydraulic motor, which first leads to the failure of the shaft seal. The casing leakage pressure mentioned here is not the bursting pressure of the casing, but the pressure that the motor output shaft dynamic seal can bear. In the motor samples of some manufacturers, only the back pressure is mentioned. Actually, back pressure refers to electricity OM cycloidal motor Manufacturer The return oil pressure of the engine, not the oil discharge pressure of the casing. During operation, the requirements for the oil discharge pressure of the cycloidal motor housing are as follows. Eaton is the world's first cycloid motor manufacturer. In China's domestic cycloidal motor manufacturing industry, Jining Jinjia Hydraulic Co., Ltd. uses Eaton technology to produce cycloidal motors. Its output shaft dynamic seal has better bearing capacity, that is, the unique internal oil circuit design of the company's products enables internal oil drainage not only to lubricate parts, but also to discharge excess oil while maintaining a certain housing oil drainage pressure.
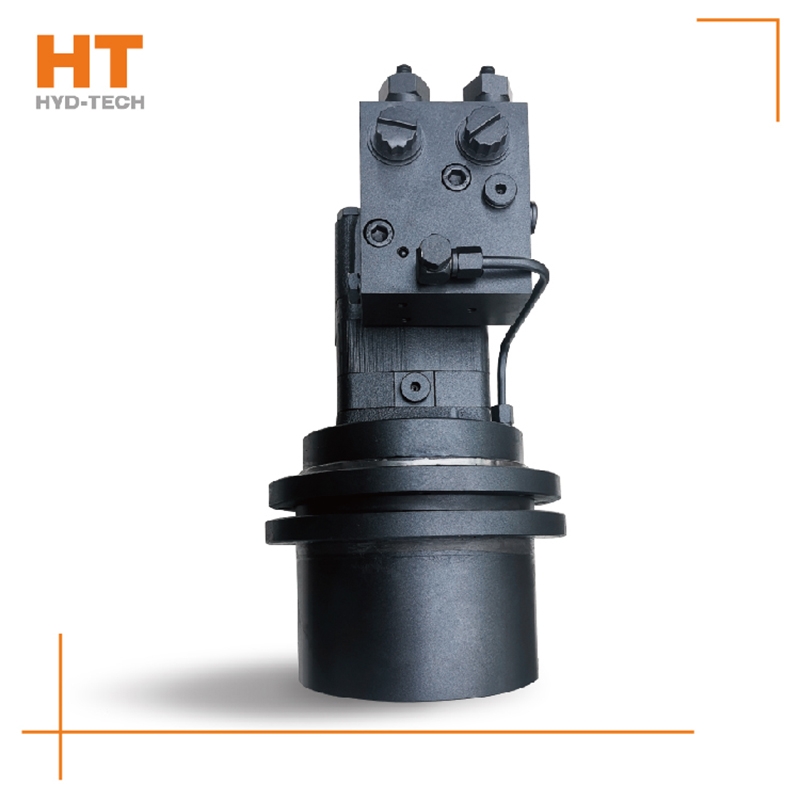
In the middle opening system, the main reversing valve of the middle opening system is in the middle position, through which the hydraulic pump is unloaded, and the liquid returns to the oil tank under low pressure. This kind of system generally uses constant displacement pump as oil source; When the reversing valve is in the middle position, the energy transmission starts with a low value that is basically zero, and the energy rises after changing, so that the pressure liquid enters customized OM cycloidal motor The actuator acts on the load; When the reversing valve is in the middle position, the internal leakage is very small. Generally, when the same function is achieved, the energy consumption of the intermediate open circuit is smaller. in the north sea customized Open system is mostly used for working conditions requiring intermittent movement or supporting load, such as prime movers that do not want to start and stop frequently. The system has high efficiency, and needs to use makeup oil pump and flushing valve for oil makeup and heat exchange.
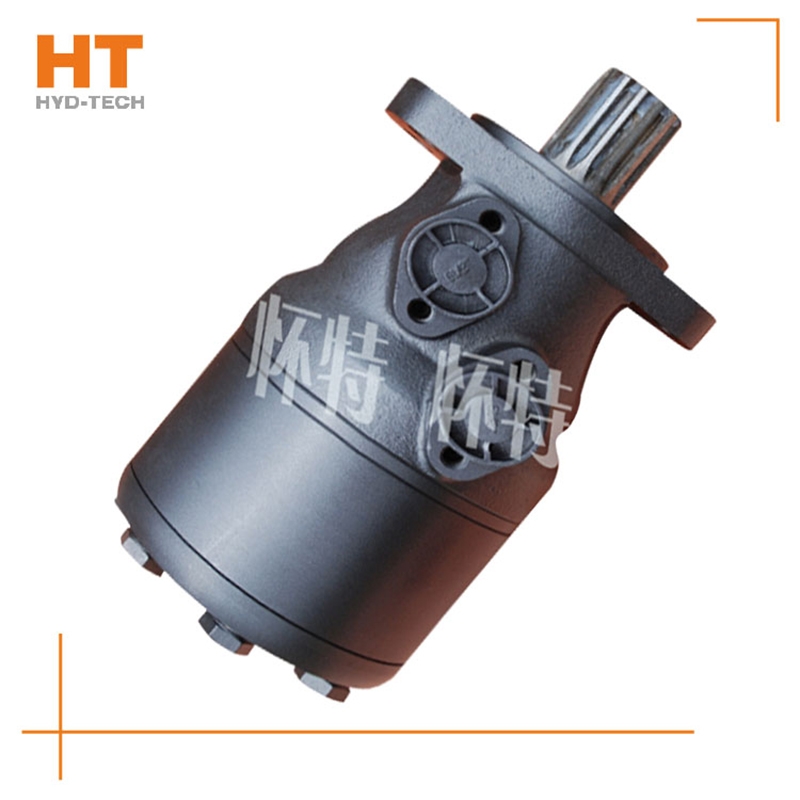
Most of its hydraulic system uses working medium, such as hydraulic oil with continuous fluidity, which converts the mechanical energy of the prime mover driving the pump into the pressure energy of the liquid through the hydraulic pump, and sends it to the actuator (hydraulic cylinder, hydraulic motor or swing hydraulic motor) through various control valves, such as pressure, flow, direction, etc., to convert it into mechanical energy to drive the load. This hydraulic system is generally composed of the following parts: power source, actuator, control valve, hydraulic auxiliary device and hydraulic working medium, which play their respective roles: power source: prime mover (motor or internal combustion engine) and hydraulic pump, whose role is to convert the mechanical energy generated by the prime mover into the pressure energy of liquid, and output oil with a certain pressure;
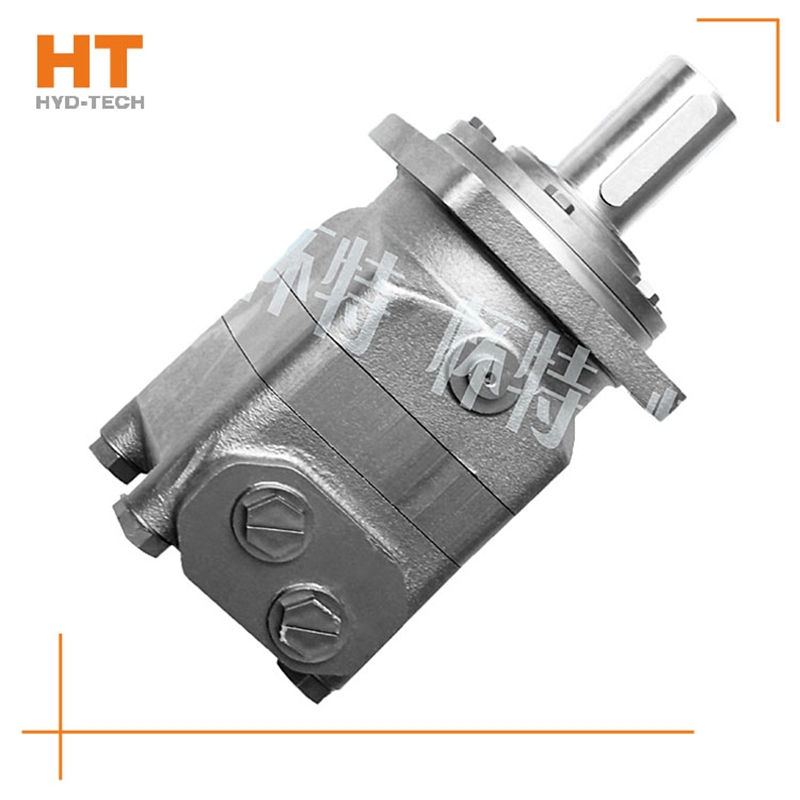
Generally, rolling bearing or hydrostatic sliding bearing, hydraulic customized OM cycloidal motor Since the pressure motor works under the condition of input pressure oil, it does not need to have self-priming capacity, but it needs to have a certain initial air tightness to provide the necessary starting torque. The existence of these differences makes the structure of the hydraulic motor and the hydraulic pump relatively close, but they cannot work reversibly. The classification of hydraulic motors can be divided into gear type, impeller type, plunger type and other types according to the structure type. According to the rated speed of the hydraulic motor, it can be divided into high speed and low speed. The rated speed exceeds 500r/min the north sea OM cycloidal motor High speed hydraulic motor, while the rated speed is lower than 500r/min, it belongs to low speed hydraulic motor.
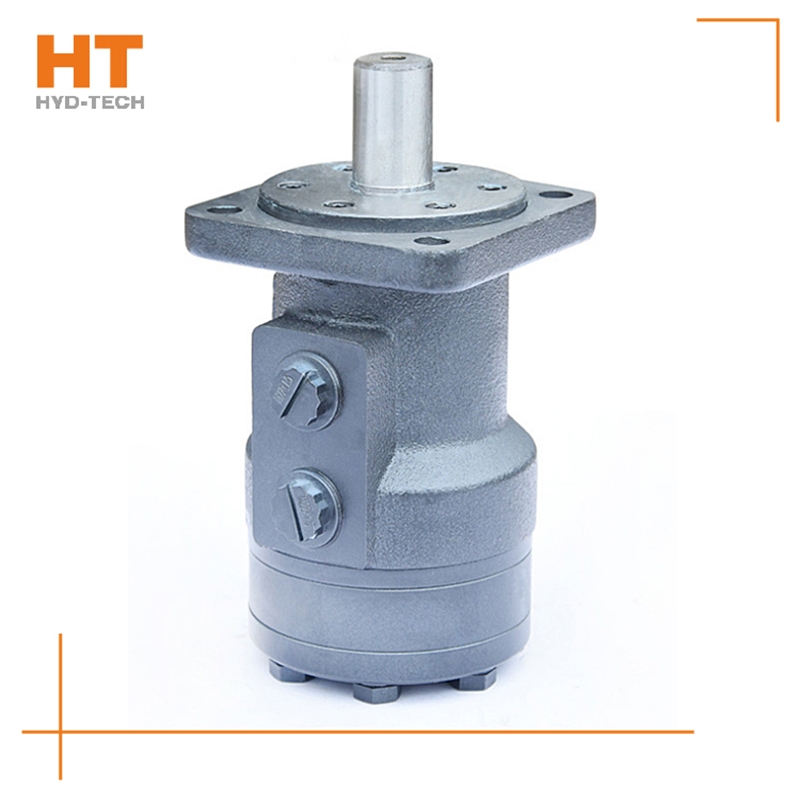
1. The hydraulic system is characterized by high energy density. For motors with the same power, hydraulic motors are much smaller and lighter than motors. And it is easy to apply to mobile devices. 2. The hydraulic motor has convenient speed regulation, which can be adjusted infinitely from 0 to the maximum speed according to the adjustment of the hydraulic valve. The motor itself does not need special design and has low cost. This is much cheaper than motor+reducer, or variable frequency motor and servo motor. 3. The hydraulic motor is totally enclosed and can be safely used in dusty, wet (even underwater) and flammable environments, which is much more reliable than explosion-proof (flameproof) motors. 4. The hydraulic system has strong anti overload capacity, and it is protected by the overflow valve, allowing long (relatively) frequent overloads. It is easy to recover under overload conditions, without damaging the equipment or restarting the equipment. These unparalleled advantages of motors have made hydraulic motors and hydraulic technology rapidly spread and popularized all over the world in the past 20 years. People increasingly feel the importance of hydraulic motors in practice.