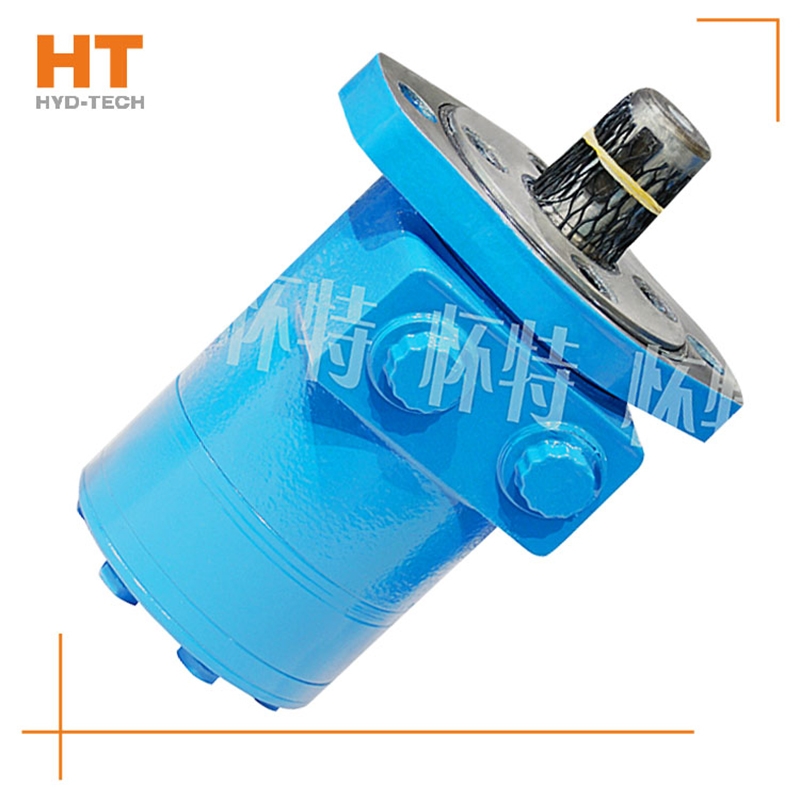
Hydraulic transmission system, the hydraulic transmission system is generally an open loop system without feedback, which mainly transmits power, supplemented by information, and pursues the perfection of transmission characteristics. Hydraulic elements customized Crane cycloid motor The characteristics of components and their interactions determine the working characteristics of the system, and its working quality is greatly affected by the changes of working conditions. Hydraulic drive system is widely used. The hydraulic system of most industrial equipment belongs to this category. In the hydraulic control system, servo valves and other electrohydraulic devices are mostly used in the hydraulic control system Crane cycloid motor manufactor The control valve constitutes a closed-loop system with feedback, which mainly transmits information, supplemented by power, and pursues the perfection of control performance. The system adds detection feedback, which can combine common components into an accurate control system, and its control quality is less affected by the change of working conditions. Hydraulic control system is widely used in high-precision CNC machine tools, metallurgy, aerospace and other industries.
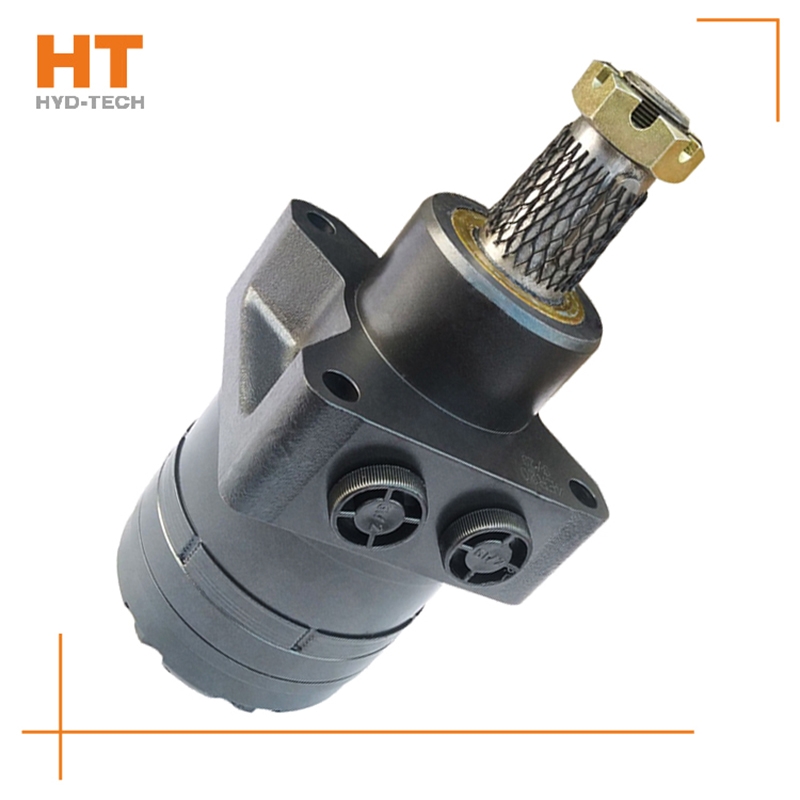
1) Select the hydraulic pump or motor with good quality and conduct regular maintenance. For example, if the tooth profile accuracy of the gear is low, grind the gear to meet the requirements of the contact surface; 2) If the vane pump has trapped oil, the triangular groove of the oil distributor should be corrected to remove the trapped oil; 3) If the axial clearance of the hydraulic pump is too large and the oil delivery is insufficient Crane cycloid motor manufactor Repair to keep the axial clearance within the allowable range; 4) If the hydraulic pump is not selected correctly, it should be replaced immediately. 3. The reversing valve is improperly adjusted. Improper adjustment of the reversing valve causes the valve core of the reversing valve to move too fast, resulting in reversing shock, noise and vibration. During operation, the valve core branch of hydraulic valve Zhoukou Crane cycloid motor Support on the spring. When its frequency is close to the pulsating frequency of oil delivery rate of hydraulic pump or other vibration sources, vibration and noise will be generated.
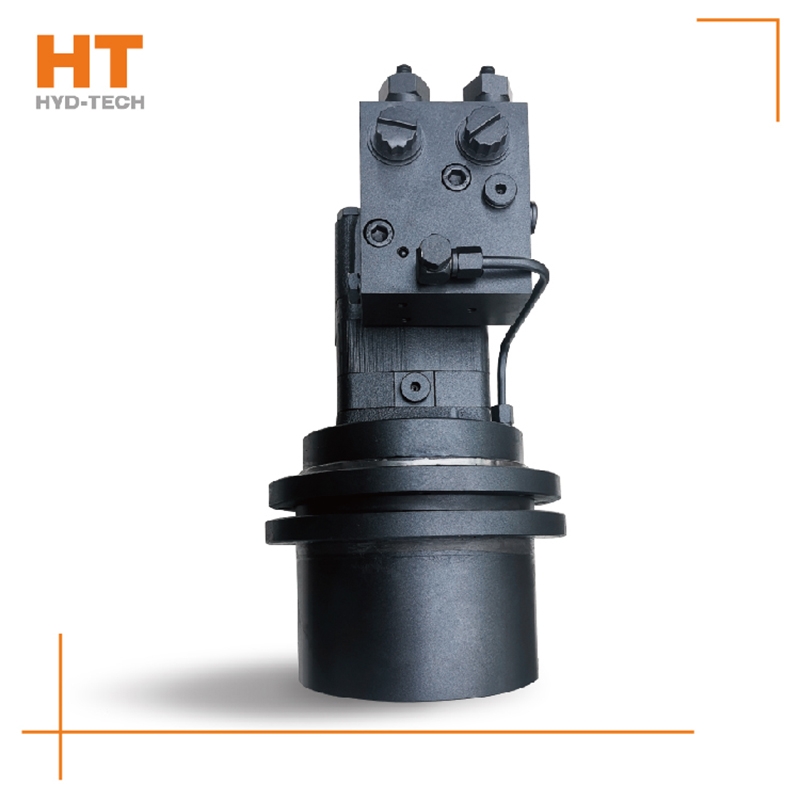
As a kind of hydraulic transmission device, hydraulic motor has been widely used in many places. In fact, I have seen it on many occasions. The main application fields are. 1. The hydraulic motor has convenient speed regulation, which can be adjusted infinitely from 0 to the maximum speed according to the adjustment of the hydraulic valve. The motor itself does not need special design and has low cost. This is much cheaper than motor+reducer, or variable frequency motor and servo motor. 2. The hydraulic system has strong anti overload capacity and relies on the overflow valve for protection, allowing a long time customized Crane cycloid motor (Relatively) Frequent overload, easy to recover under overload, no damage to equipment, no restart of equipment. 3. The hydraulic system is characterized by high energy density. For motors of the same power, hydraulic motors are much smaller than motors Crane cycloid motor manufactor , much lighter. And it is easy to apply to mobile devices. 4. The hydraulic motor is totally enclosed and can be safely used in dusty, wet (even underwater) and flammable environments, which is much more reliable than explosion-proof (flameproof) motors.
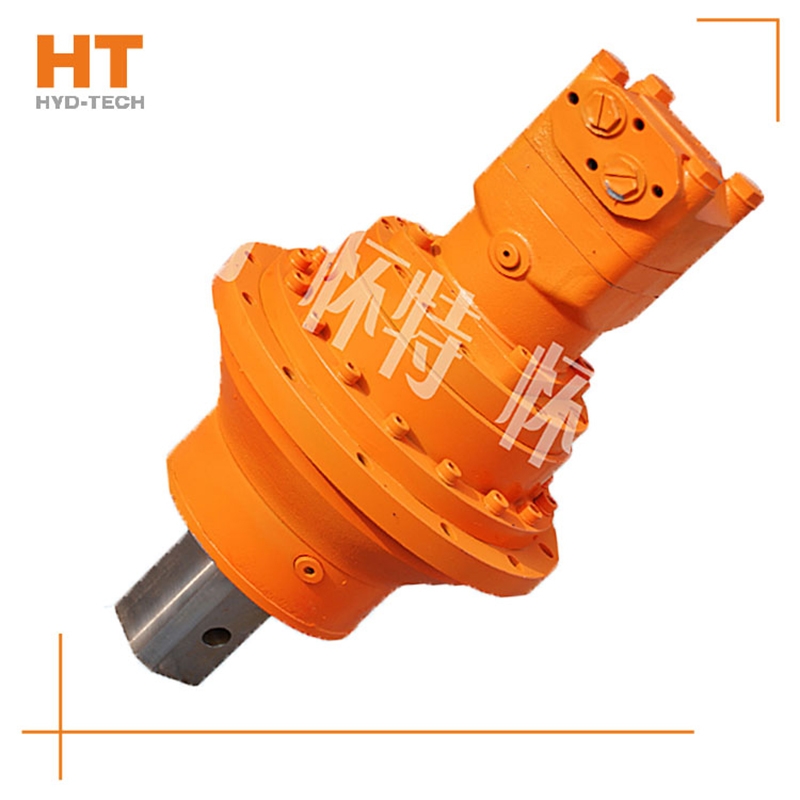
1. Generally, the motor shall be able to run forward and backward. Therefore, the hydraulic motor is usually required to have structural symmetry in the design. 2. The actual working pressure difference of the hydraulic motor depends on the load torque. When the moment of inertia of the driven load is large and the speed is high, rapid braking or reverse rotation is required, high hydraulic impact will be generated. Therefore, the system should be equipped with necessary safety valves and buffer valves. 3. Under normal working conditions, the inlet and outlet pressure of the hydraulic motor is higher than the atmospheric pressure, so there is no suction performance problem like the hydraulic pump. However, if the hydraulic motor can work under pump conditions, its oil inlet should have a minimum pressure limit to avoid cavitation. 4. Some hydraulic motors must have sufficient back pressure at the oil return port to ensure normal operation. The higher the speed, the greater the back pressure, which indicates that the utilization rate of oil source pressure is not high and the system loss is increased. 5. Because the internal leakage of the motor is inevitable, there will be slow sliding when the hydraulic motor oil outlet is closed for braking. Therefore, when long-term accurate braking is required, a separate anti-skid brake shall be set.