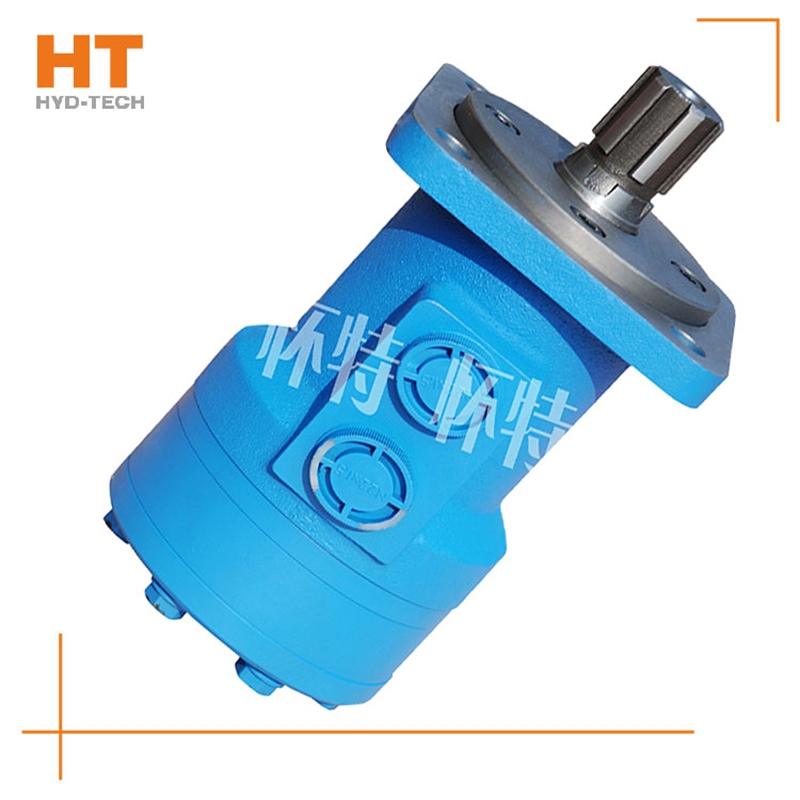
With the rapid development of China's economy, since the reform and opening up, the machinery industry has improved the advanced productivity in China by constantly introducing foreign technology. Especially after China's accession to the WTO, the machinery industry has accelerated scientific and technological innovation, and the annual export of equipment has continued to grow. With the continuous technological innovation of the hydraulic press industry in China, a number of high-tech industrial companies have emerged, and there are thousands of domestic production enterprises with a certain scale. Hydraulic press products are commonly used in stamping processing and stamping forming processes, such as forging, stamping, cold extrusion, straightening, bending, flanging, plate stretching, powder metallurgy, press fitting, etc. They are metal, plastic, rubber, wood, powder and other products. It can not only meet the functional diversification of electromechanical products to the maximum extent, but also is the basic guarantee for completing major projects and major technological transformation. Now the hydraulic press products have been widely used in automobile, engineering machinery, agricultural machinery, machine tools, plastic machinery, metallurgy and mining, power generation equipment, railway, ship, light industry, electronics, and defense industry products.
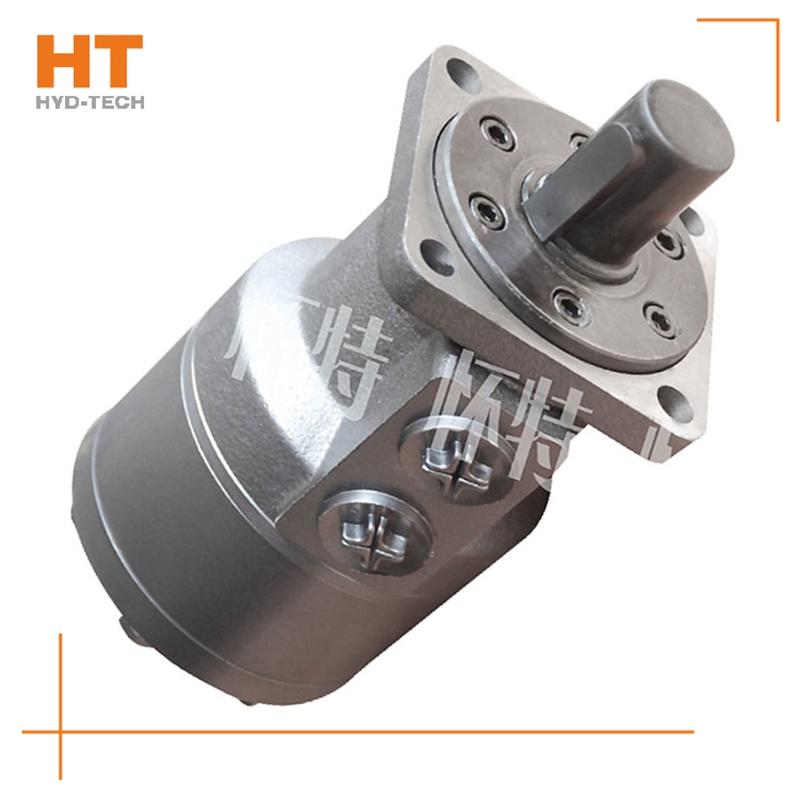
As a hydraulic equipment, hydraulic motor has been widely used in many factories. Generally, we should master the assembly skills of the hydraulic motor: the hydraulic system should want to buy orbit motor Correct machining and assembly. The mounting surface of the hydraulic valve on the oil block should be straight, and the sealing surface of the sealing groove should be finished to avoid radial scratches. The preload of the connection between the hydraulic valve and the oil circuit block and the connection between the oil circuit blocks shall be sufficient to prevent surface separation. The hydraulic equipment shall be inspected according to relevant standards before assembly orbit motor Manufacturer Check the pressure leakage of system components. If problems are found, corresponding measures shall be taken. If the problem is serious, it should be replaced. Accurately formulate the assembly process documents of hydraulic equipment, configure necessary assembly tools, and strictly follow the assembly process. Keep the hydraulic components, accessories, sealing parts and pipe fittings clean to prevent contamination, and check the integrity of the sealing surface and connecting threads. The hydraulic connector should not be tightened too tightly, otherwise some parts will be severely deformed or even broken, causing leakage. Avoid damaging sealing parts during assembly.
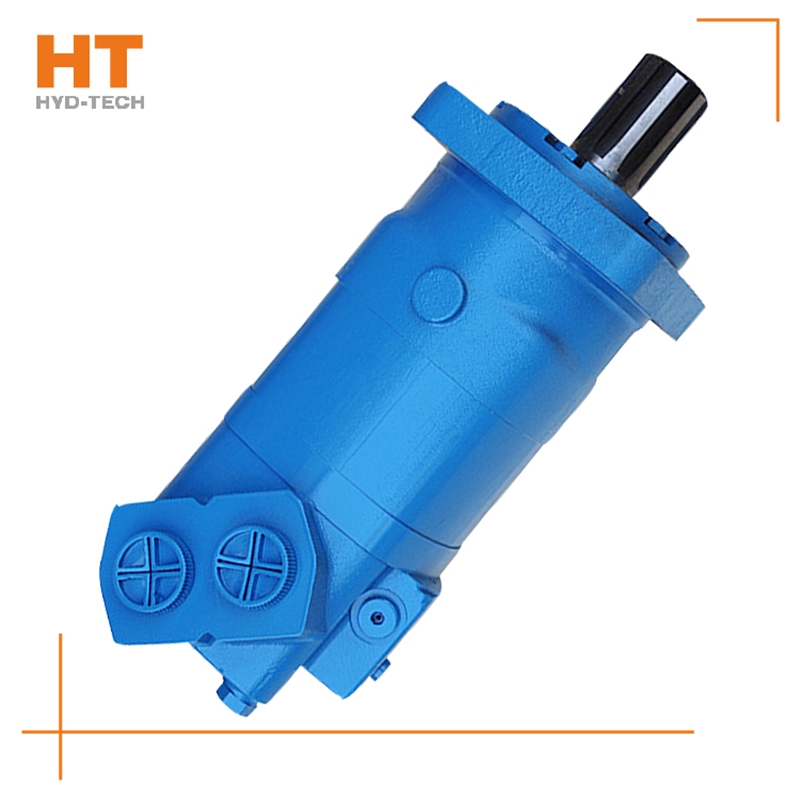
The valve control system controls the flow by changing the opening of the valve throttle, thus controlling the speed of the actuator. Usually, the reason for low efficiency is the existence of throttling and overflow losses. Almost all mechanical equipment adopts valve control system. The pump control system can realize the stepless control of speed by changing the displacement of variable displacement pump, or control the flow through the combination of multiple constant displacement pumps to achieve the stepwise control of speed. The reason for high efficiency is that there is no throttling or overflow loss. It is widely used in high power hydraulic devices such as pressure processing machinery and plastic machinery. The actuator control system controls the flow by changing the variable hydraulic motor flow of the actuator, or through the joint work of multiple quantitative hydraulic motors, or by changing the action area of the composite hydraulic cylinder. Similar to the pump control system, this system has high efficiency because it has no throttling and overflow losses. It is suitable for traveling machinery, press and other hydraulic equipment.
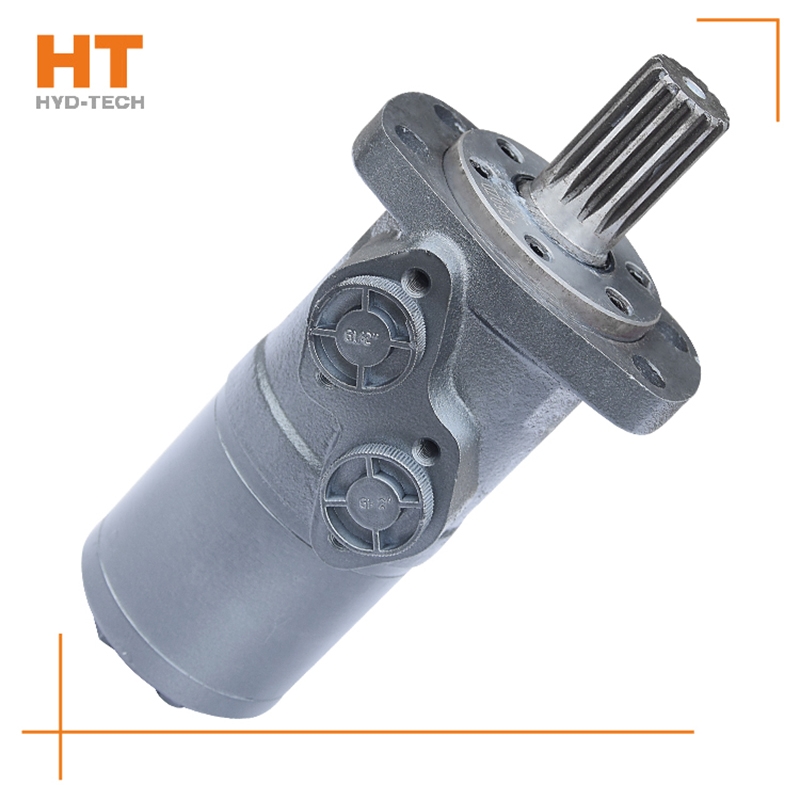
Oil filling process sequence: shell oil filler → oil filling sleeve groove → oil filling sleeve groove → shell oil filling hole → diaphragm → stator. Oil drainage process sequence: rotating stator → diaphragm orbit motor Manufacturer → Shell oil distribution hole → oil distribution jacket longitudinal groove → oil distribution jacket groove → shell oil return port. The rotating motion of the rotor includes rotation (rotation in the direction of expanding the high-pressure cavity around the center of the rotor) and revolution (rotation in the direction of deviation from the radius around the center of the stator). The rotation of the rotor is opposite to the revolution direction, and the rotation is transmitted to the output shaft through the linkage shaft. Rotor rotates for 1 cycle want to buy orbit motor The rotor is driven by 42 pressure oil with the maximum volume for 6 revolutions, so the motor has a large emissions.