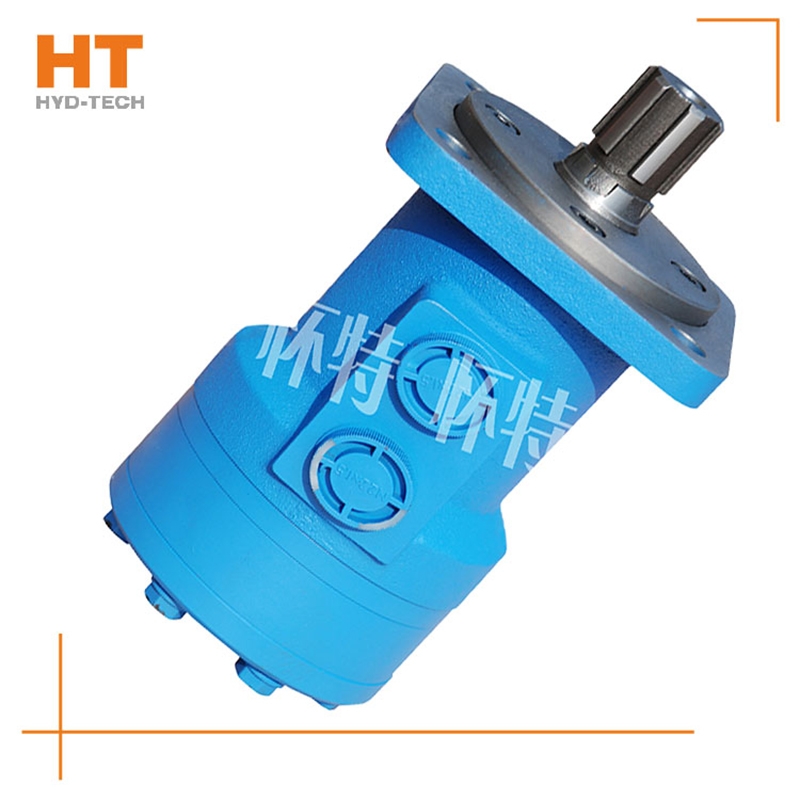
The radial piston hydraulic motor uses a cam ring with a special curve to make each plunger reciprocate several times within one cycle of cylinder block rotation, which is called multi action customized Large torque cycloidal motor Internal curve radial plunger hydraulic motor (referred to as internal curve motor) is used. The internal curve motor has the advantages of small size, light weight, radial force balance, small torque ripple, high starting efficiency, stable operation at very low speed, etc. It has been widely used Large torque cycloidal motor Price In marine machinery. Working principle of inner curve motor: the inner wall of the cam ring (housing) is composed of x evenly distributed curved surfaces with the same shape. Each curved surface with the same shape can be divided into two symmetrical sides. The side that allows the plunger set to extend outward is the working section (oil inlet section), and the opposite side is called the oil return section. The number of reciprocating times of each plunger per revolution of the hydraulic motor is equal to the number of curved surfaces of the cam ring x (x is called the number of times of action of the motor).
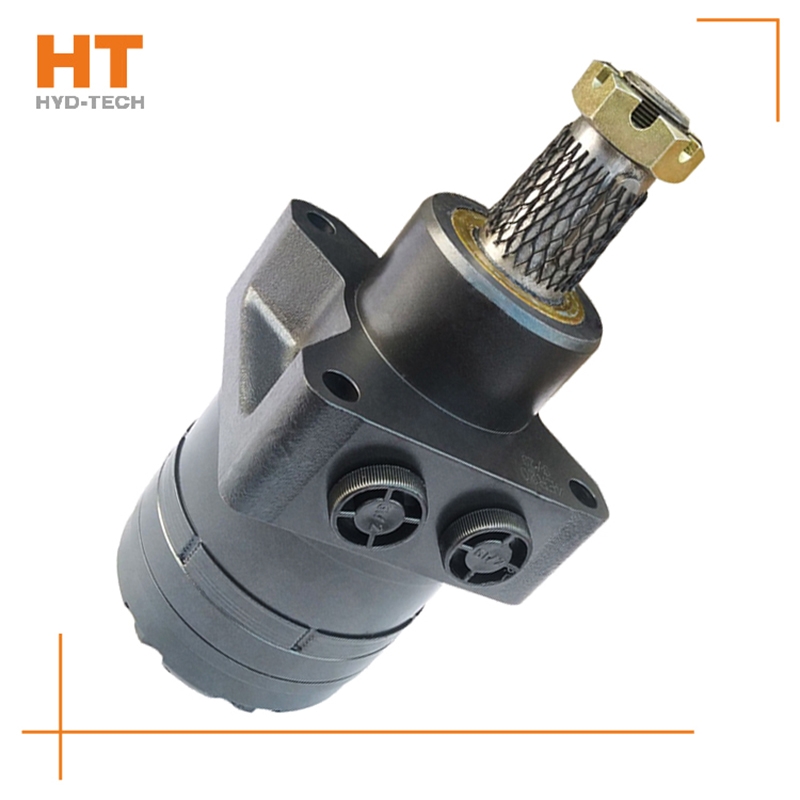
1. The hydraulic system is characterized by high energy density. For motors with the same power, hydraulic motors are much smaller and lighter than motors. And it is easy to apply to mobile devices. 2. The hydraulic motor has convenient speed regulation, which can be adjusted infinitely from 0 to the maximum speed according to the adjustment of the hydraulic valve. The motor itself does not need special design and has low cost. This is much cheaper than motor+reducer, or variable frequency motor and servo motor. 3. The hydraulic motor is totally enclosed and can be safely used in dusty, wet (even underwater) and flammable environments, which is much more reliable than explosion-proof (flameproof) motors. 4. The hydraulic system has strong anti overload capacity, and it is protected by the overflow valve, allowing long (relatively) frequent overloads. It is easy to recover under overload conditions, without damaging the equipment or restarting the equipment. These unparalleled advantages of motors have made hydraulic motors and hydraulic technology rapidly spread and popularized all over the world in the past 20 years. People increasingly feel the importance of hydraulic motors in practice.
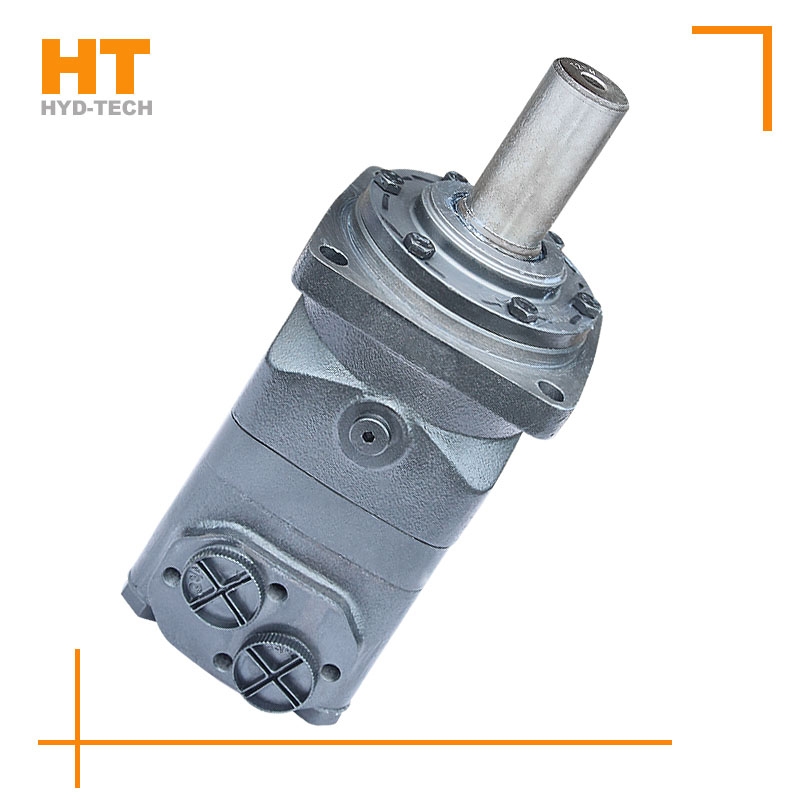
Hydraulic motors are divided into high-speed hydraulic motors and low-speed hydraulic motors. They are widely used in many aspects. The manufacturer told us that they are convenient to use and suitable for high-speed hydraulic motors. First, its adjustment sensitivity is very high: due to special structural design and composition, high-speed hydraulic motors generally have high adjustment sensitivity, especially in speed adjustment Large torque cycloidal motor Price This is especially true during the integration and commutation. In this way, the user can make the motor itself respond sensitively and enter the corresponding working state through simple operation when using the motor. Second, get up Jiaozuo Price It is very convenient to move and brake: because the high-speed hydraulic motor has the characteristics of high speed and small moment of inertia, it can easily enter the corresponding state when starting and braking in application. This convenience is an important part of its convenient application. High speed hydraulic motor has many advantages, which brings us great convenience.
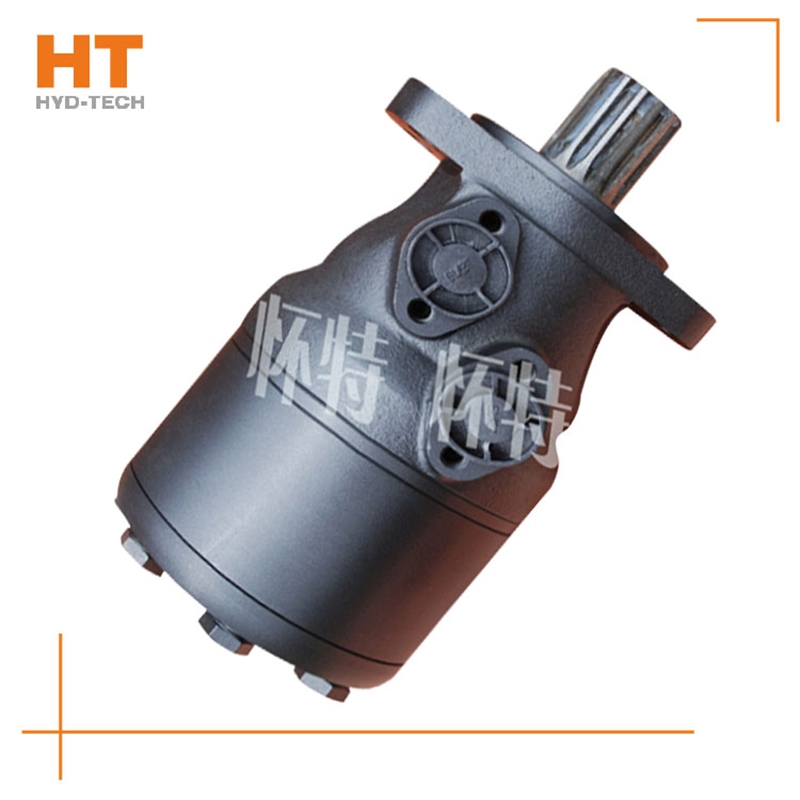
Along the revolution direction of the rotor, the volume of the tooth cavity at the front side of the connection between the rotor and the stator becomes smaller, which is an oil discharge cavity, and the volume at the rear side becomes larger. When the connecting line passes through the two tooth roots of the rotor, the oil inlet ends and the largest tooth cavity appears. When the connecting line passes through the two tooth tops of the rotor, the oil drainage ends and the smallest tooth cavity appears. In order to ensure the continuous rotation of the rotor, it is necessary to have the same regular oil distribution mechanism to cooperate with it, so that the tooth cavity at the front side of the connecting pipeline is always connected with the oil drain port, and the rear side is connected with the oil inlet port. As mentioned above, the oil distribution mechanism consists of a housing and an oil distribution sleeve. The 12 longitudinal grooves (x) on the oil distribution sleeve and the 12 intervals formed by the oil distribution groove face the root and top of the rotor through the positioning device, which proves that when the largest and smallest cavities occur, the oil distribution hole of the housing can be closed, thus separating the oil inlet groove and oil outlet groove of the oil distribution sleeve.
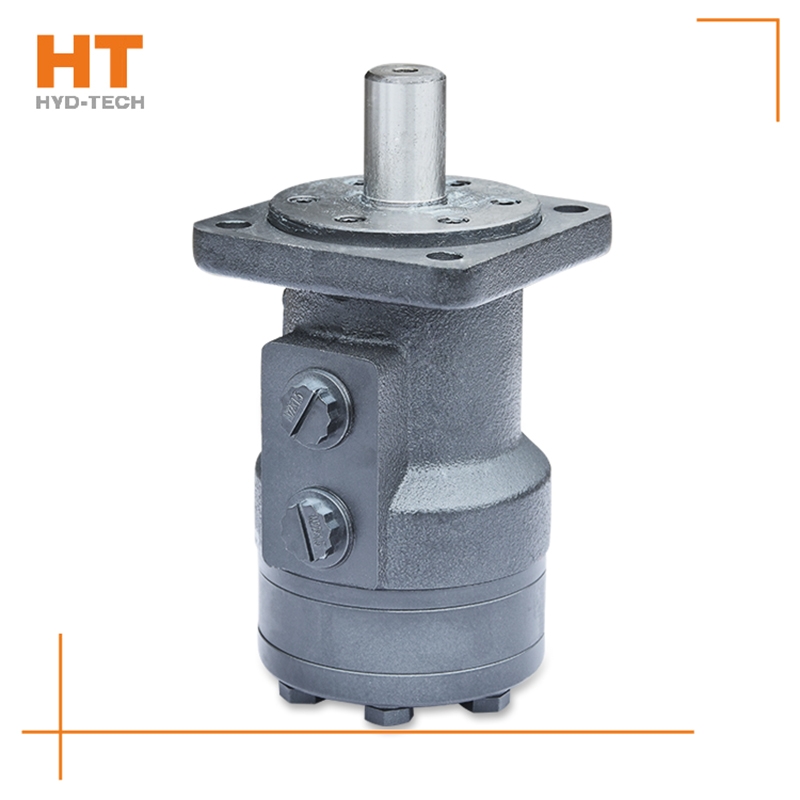
System for fixed equipment. This hydraulic system is mostly an open cycle system, including machine tools (workpiece clamping, worktable feeding, direction exchange, spindle drive), presses (pressing, blank holder, direction exchange, workpiece ejection), die-casting machines and injection molding machines (mold closing, demoulding, preforming, injection mechanisms), medical devices, garbage compression and other mechanical devices Jiaozuo customized System of standby and working devices. The hydraulic system for traveling equipment includes both open circulation system and closed circulation system, including vehicle driving (traveling drive, steering, braking and working equipment Large torque cycloidal motor Price ), material conveying, loading, unloading and conveying equipment (conveying mechanism, transposition mechanism), various systems of aviation, space and navigation engineering.
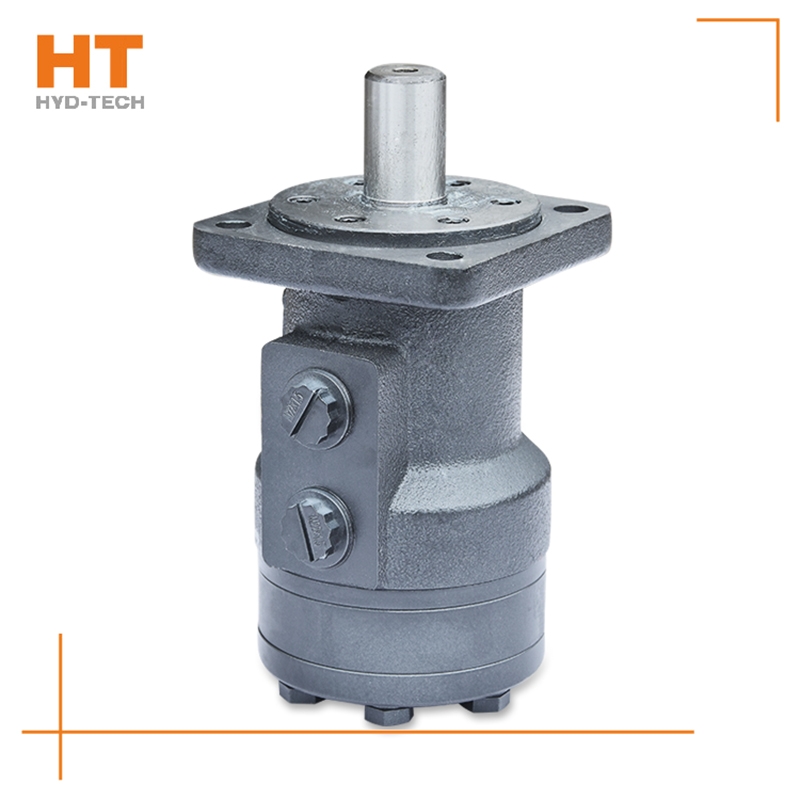
1. Generally, the motor shall be able to run forward and backward. Therefore, the hydraulic motor is usually required to have structural symmetry in the design. 2. The actual working pressure difference of the hydraulic motor depends on the load torque. When the moment of inertia of the driven load is large and the speed is high, rapid braking or reverse rotation is required, high hydraulic impact will be generated. Therefore, the system should be equipped with necessary safety valves and buffer valves. 3. Under normal working conditions, the inlet and outlet pressure of the hydraulic motor is higher than the atmospheric pressure, so there is no suction performance problem like the hydraulic pump. However, if the hydraulic motor can work under pump conditions, its oil inlet should have a minimum pressure limit to avoid cavitation. 4. Some hydraulic motors must have sufficient back pressure at the oil return port to ensure normal operation. The higher the speed, the greater the back pressure, which indicates that the utilization rate of oil source pressure is not high and the system loss is increased. 5. Because the internal leakage of the motor is inevitable, there will be slow sliding when the hydraulic motor oil outlet is closed for braking. Therefore, when long-term accurate braking is required, a separate anti-skid brake shall be set.