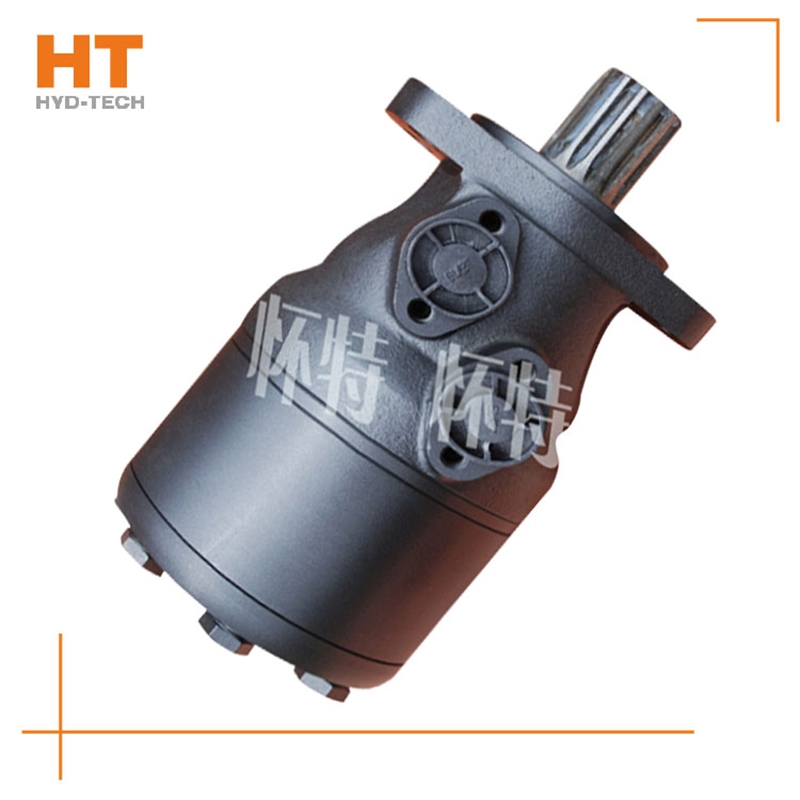
Along the revolution direction of the rotor, the volume of the tooth cavity at the front side of the connection between the rotor and the stator becomes smaller, which is an oil discharge cavity, and the volume at the rear side becomes larger. When the connecting line passes through the two tooth roots of the rotor, the oil inlet ends and the largest tooth cavity appears. When the connecting line passes through the two tooth tops of the rotor, the oil drainage ends and the smallest tooth cavity appears. In order to ensure the continuous rotation of the rotor, it is necessary to have the same regular oil distribution mechanism to cooperate with it, so that the tooth cavity at the front side of the connecting pipeline is always connected with the oil drain port, and the rear side is connected with the oil inlet port. As mentioned above, the oil distribution mechanism consists of a housing and an oil distribution sleeve. The 12 longitudinal grooves (x) on the oil distribution sleeve and the 12 intervals formed by the oil distribution groove face the root and top of the rotor through the positioning device, which proves that when the largest and smallest cavities occur, the oil distribution hole of the housing can be closed, thus separating the oil inlet groove and oil outlet groove of the oil distribution sleeve.
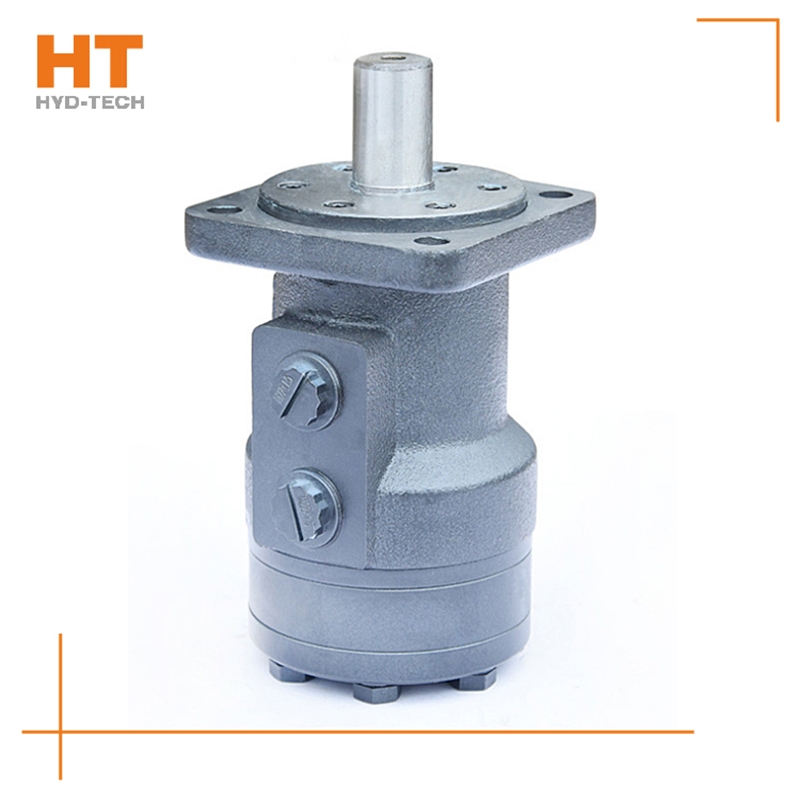
The manufacturer of the hydraulic motor has explained to us the relevant knowledge about the speed and low-speed stability of the hydraulic motor. The speed of the hydraulic motor depends on the flow of the supply fluid q and the discharge of the hydraulic motor itself v. The hydraulic motor has internal leakage. Not all the liquid entering the motor drives the hydraulic motor to work. Some of the liquid is lost due to leakage, and the actual speed of the motor is lower than the ideal situation. When the working speed of the hydraulic motor is too low, it cannot maintain a uniform speed, and it stops when entering city in Guangxi orbit motor The unstable state is a creeping phenomenon. The high-speed hydraulic motor is required to work at a speed below 10r/min and the low-speed high torque hydraulic motor is required to work at a speed below 3r/min. All hydraulic motors can meet the requirements. Generally speaking, the low-speed stability of low-speed large torque hydraulic motors is better than that of high-speed motors. Due to the large emissions and size of the low-speed high torque motor, the sliding speed of the friction pair will not be too low even if the rotation speed is low want to buy orbit motor Large emissions, relatively small impact of leakage, large rotation inertia of the motor itself, easy to obtain good low-speed stability.
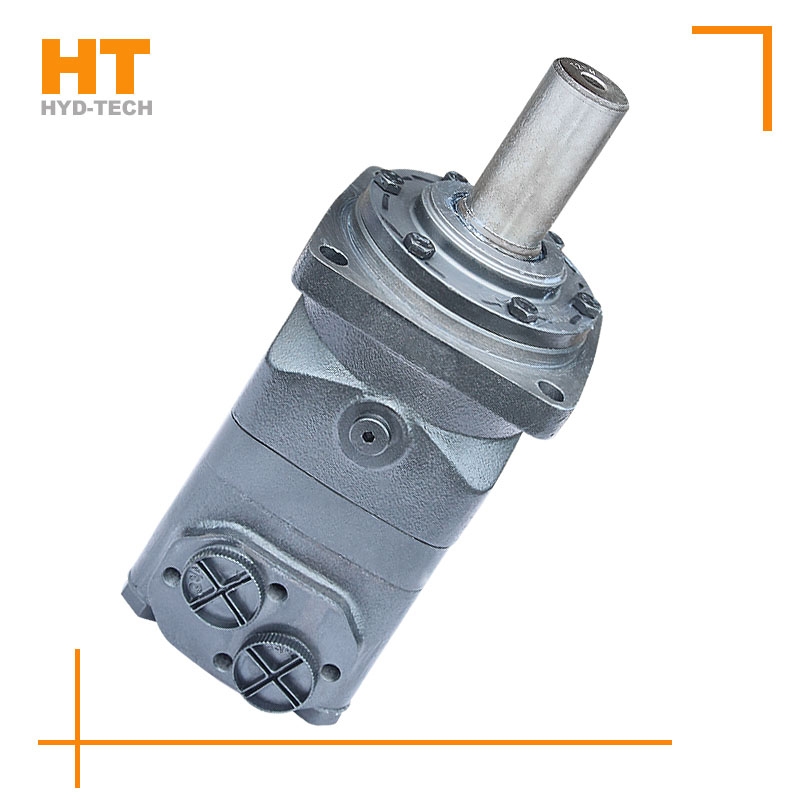
As far as energy conversion is concerned, the hydraulic pump and hydraulic motor are connected as reversible hydraulic components, and the working fluid can be input into any kind of hydraulic pump to make it become a hydraulic motor; On the contrary, when the main shaft of the hydraulic motor rotates under the action of external force orbit motor manufactor It can also become a hydraulic pump. Because they all have the same basic structural elements, namely sealed and recyclable volume and corresponding distribution mechanism. However, the working environment of hydraulic motor and hydraulic pump is different want to buy orbit motor The performance requirements are also different. Therefore, there are many differences between the hydraulic motor and the hydraulic pump of the same model. The first hydraulic motor should be positive and negative, so its internal structure should be symmetrical; The speed range of the motor must be large enough, especially its minimum stable speed must have certain requirements.
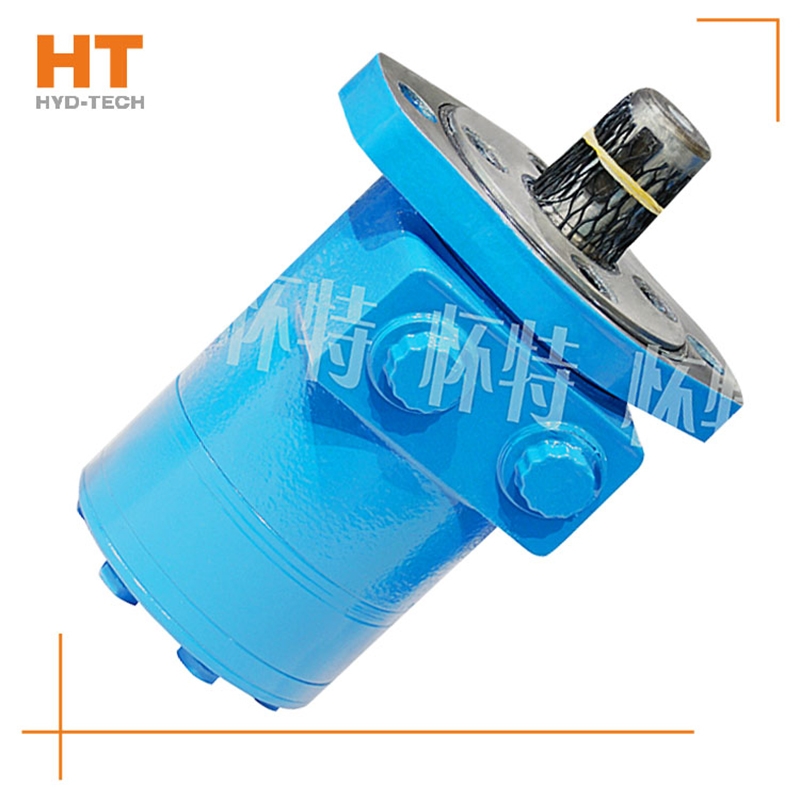
The output pressure of the hydraulic motor also depends on the load. Rated pressure Pn: the rated pressure refers to the working pressure that the hydraulic motor can withstand during continuous operation. It can want to buy orbit motor To ensure the volumetric efficiency and service life of the hydraulic motor. Working pressure P: the working pressure is the actual pressure of oil input when the hydraulic motor is working orbit motor manufactor power. Its value depends on the size of the load. However, the maximum working pressure is determined by the safety valve in the hydraulic system. The throttle adjustment value must not exceed the maximum pressure value of the hydraulic motor. The third is the maximum pressure: the limit pressure that the motor is allowed to overload in a short time. Pn ≤ Pmax value.
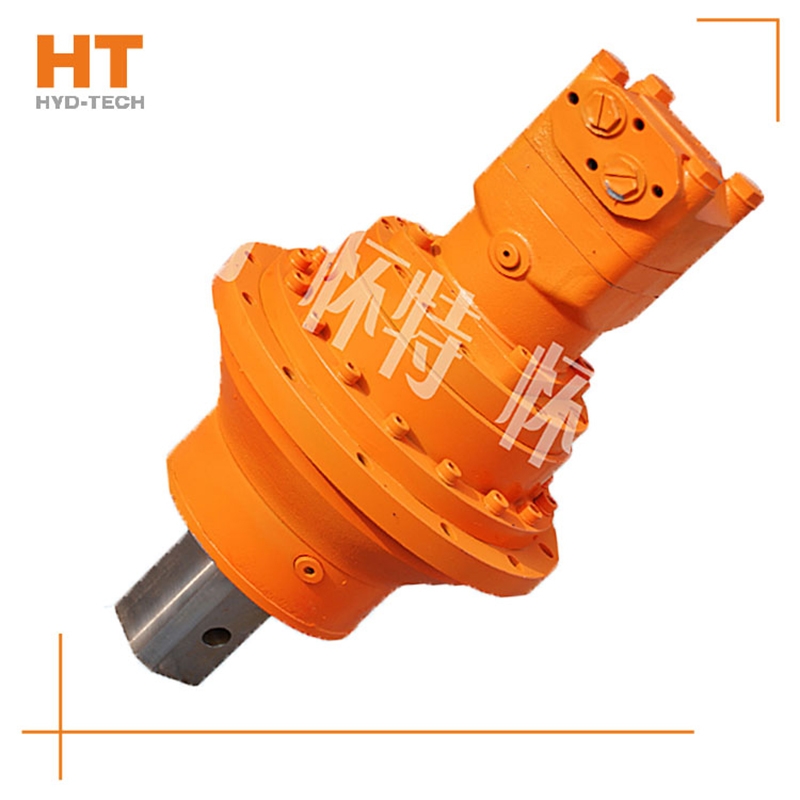
As a hydraulic equipment, hydraulic motor has been widely used in many factories. Generally, we should master the assembly skills of the hydraulic motor: the hydraulic system should want to buy orbit motor Correct machining and assembly. The mounting surface of the hydraulic valve on the oil block should be straight, and the sealing surface of the sealing groove should be finished to avoid radial scratches. The preload of the connection between the hydraulic valve and the oil circuit block and the connection between the oil circuit blocks shall be sufficient to prevent surface separation. The hydraulic equipment shall be inspected according to relevant standards before assembly orbit motor manufactor Check the pressure leakage of system components. If problems are found, corresponding measures shall be taken. If the problem is serious, it should be replaced. Accurately formulate the assembly process documents of hydraulic equipment, configure necessary assembly tools, and strictly follow the assembly process. Keep the hydraulic components, accessories, sealing parts and pipe fittings clean to prevent contamination, and check the integrity of the sealing surface and connecting threads. The hydraulic connector should not be tightened too tightly, otherwise some parts will be severely deformed or even broken, causing leakage. Avoid damaging sealing parts during assembly.
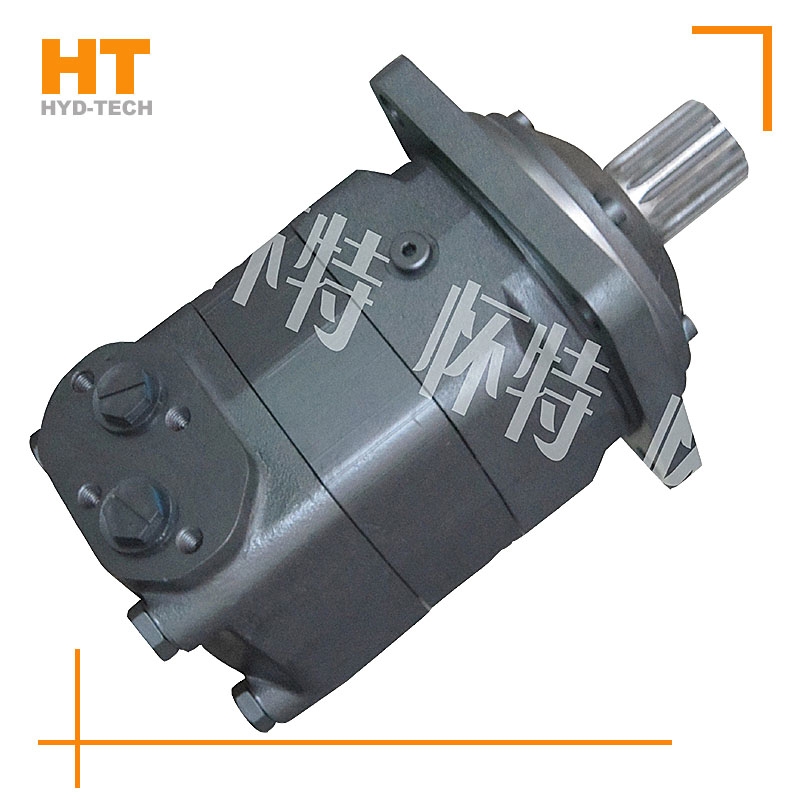
The valve control system controls the flow by changing the opening of the valve throttle, thus controlling the speed of the actuator. Usually, the reason for low efficiency is the existence of throttling and overflow losses. Almost all mechanical equipment adopts valve control system. The pump control system can realize the stepless control of speed by changing the displacement of variable displacement pump, or control the flow through the combination of multiple constant displacement pumps to achieve the stepwise control of speed. The reason for high efficiency is that there is no throttling or overflow loss. It is widely used in high power hydraulic devices such as pressure processing machinery and plastic machinery. The actuator control system controls the flow by changing the variable hydraulic motor flow of the actuator, or through the joint work of multiple quantitative hydraulic motors, or by changing the action area of the composite hydraulic cylinder. Similar to the pump control system, this system has high efficiency because it has no throttling and overflow losses. It is suitable for traveling machinery, press and other hydraulic equipment.