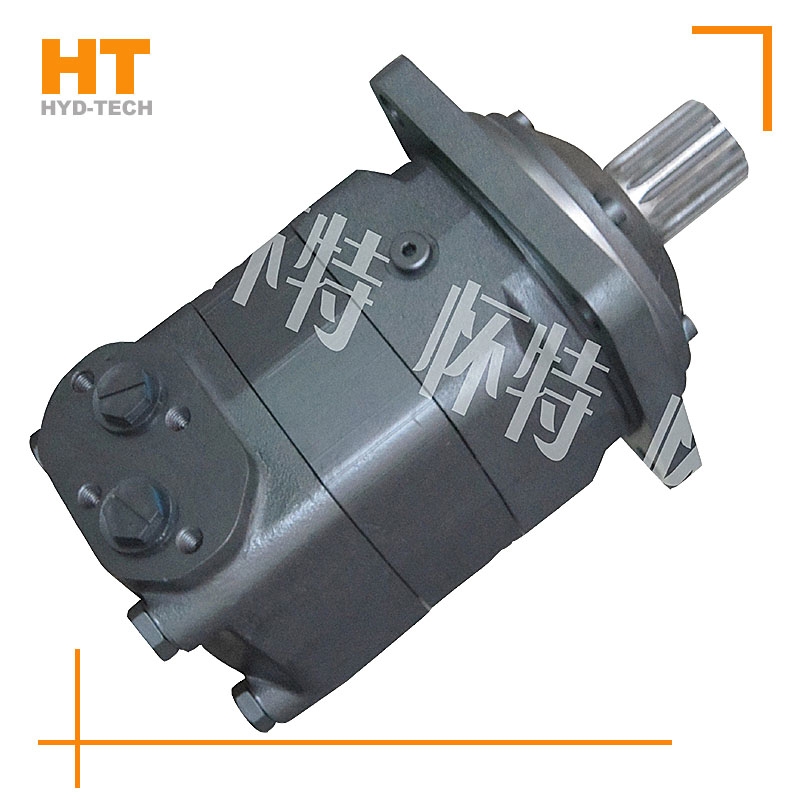
As a kind of hydraulic transmission device, hydraulic motor has been widely used in many places. In fact, I have seen it on many occasions. The main application fields are. 1. The hydraulic motor has convenient speed regulation, which can be adjusted infinitely from 0 to the maximum speed according to the adjustment of the hydraulic valve. The motor itself does not need special design and has low cost. This is much cheaper than motor+reducer, or variable frequency motor and servo motor. 2. The hydraulic system has strong anti overload capacity and relies on the overflow valve for protection, allowing a long time special-purpose Hydraulic cycloid motor (Relatively) Frequent overload, easy to recover under overload, no damage to equipment, no restart of equipment. 3. The hydraulic system is characterized by high energy density. For motors of the same power, hydraulic motors are much smaller than motors Hydraulic cycloid motor Price , much lighter. And it is easy to apply to mobile devices. 4. The hydraulic motor is totally enclosed and can be safely used in dusty, wet (even underwater) and flammable environments, which is much more reliable than explosion-proof (flameproof) motors.
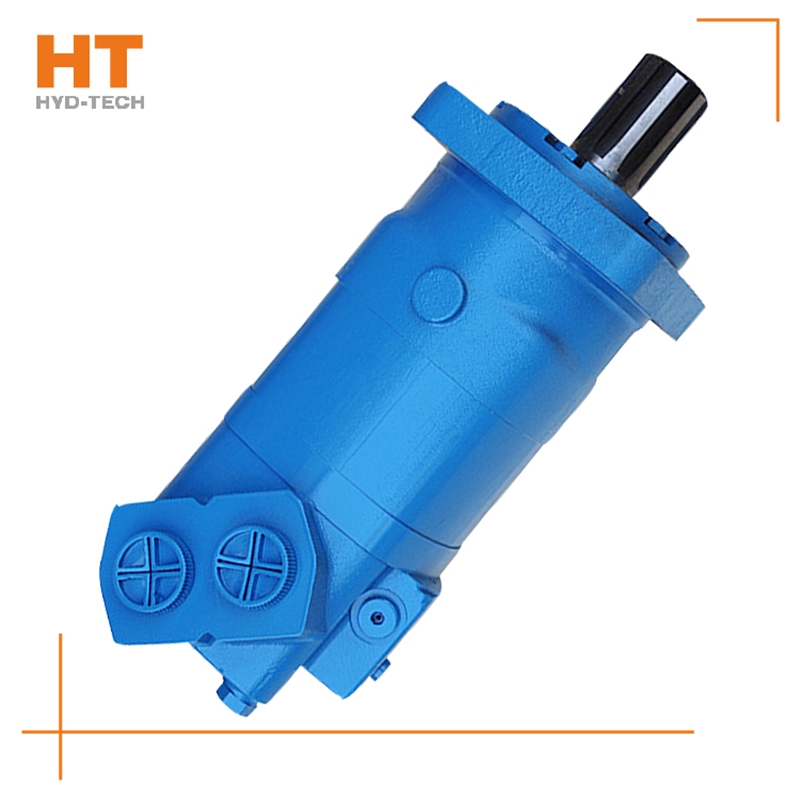
When the working load changes from low speed to high speed in a wide range, the hydraulic motor is also required to be able to drive and regulate speed in the corresponding wide range, which requires the motor to have good low-speed stability and high speed performance. The speed regulation range K of the hydraulic motor is usually expressed by the ratio of the allowable maximum speed to the minimum speed. special-purpose Hydraulic cycloid motor It is the highest operating speed of hydraulic motor, but it is limited by many factors, mainly including: 1. Service life. After the speed increases, each pair is worn Liaoning Price The service life is shortened. 2、 Mechanical efficiency limits. At high speed, the hydraulic motor needs to input large flow, accordingly, the hydraulic loss of each circulating component increases, reducing the mechanical efficiency.
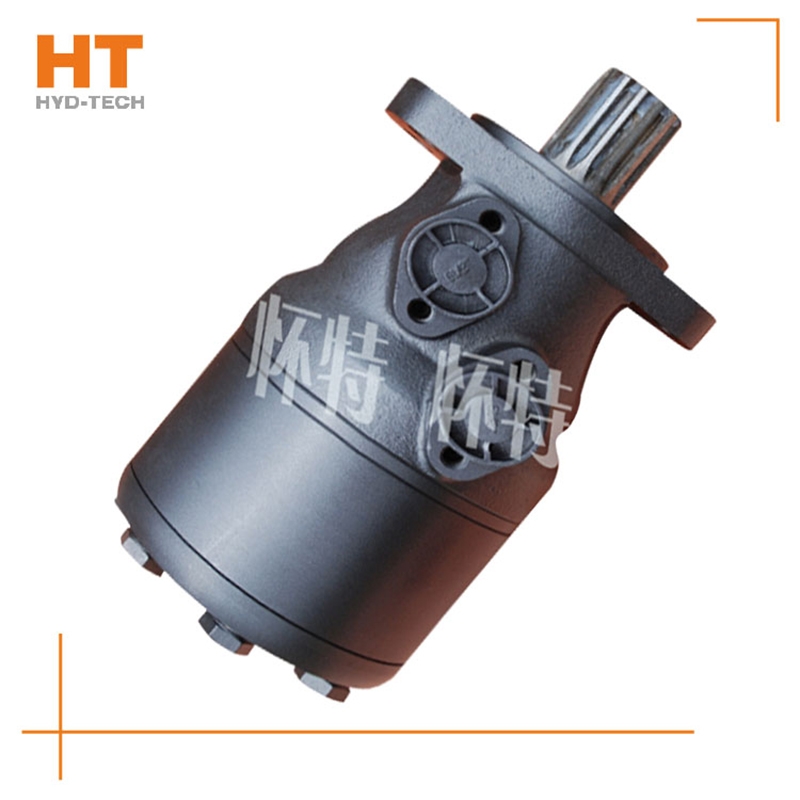
After disassembling and inspecting the hydraulic motor installed on the drill, it was found that the friction surface of the valve disc and the port plate of the hydraulic motor was severely worn, and the deepest worn part was 0. 15mm; The output shaft oil seal is leaking. Cause analysis of oil leakage of output shaft oil seal. After disassembly inspection and test, the axial and radial clearances of the output shaft meet the standard requirements special-purpose Hydraulic cycloid motor There is no obvious wear on the oil seal mating surface. However, it is found that the oil seal rubber has hardened and its elasticity has deteriorated. With the increase of sealing lip wear, the pre tightening capacity and sealing performance decrease, and the excessive oil temperature accelerates the wear of sealing lip; In addition, due to the liquid Liaoning Hydraulic cycloid motor The leakage of the pressure motor causes the back pressure in the housing to be too high, which further aggravates the wear and leakage of the sealing lip. The smaller the friction of the rotor in the stator sleeve, the higher the mechanical efficiency of the motor.
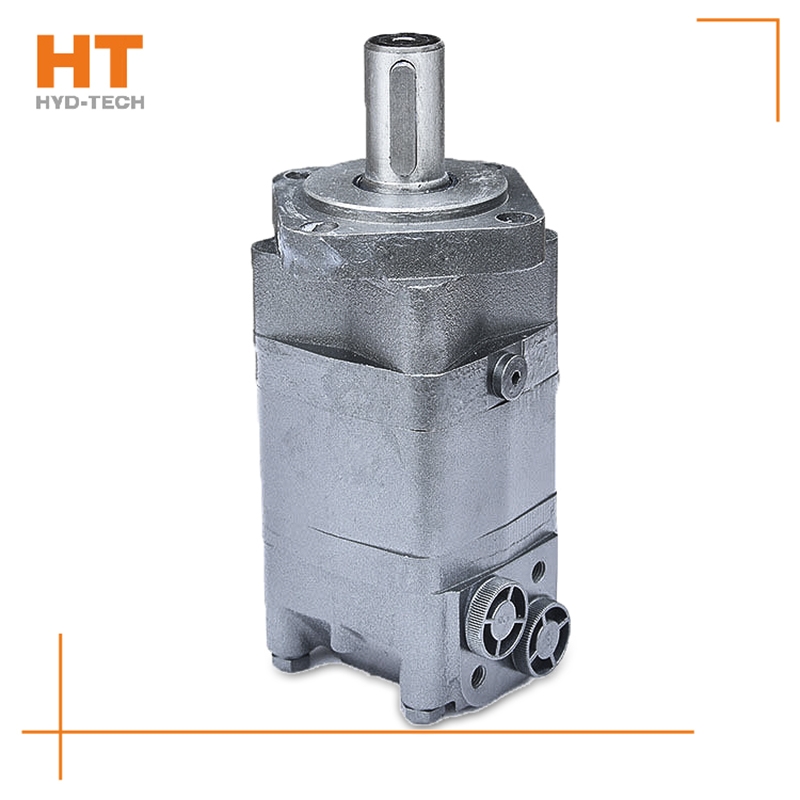
1. Pascal principle: also known as static pressure transmission principle, it refers to the pressure exerted on the static liquid in a closed container is transmitted to all points of the liquid at the same time with equal value. The hyperbolic cosine of 2. The hyperbolic cosine of 2. System pressure: the discharge pressure of the hydraulic pump in the system. The hyperbolic cosine of 3. The hyperbolic cosine of 3. Servo valve and proportional valve: infinitely adjust the output of hydraulic valve, such as pressure, flow and direction, by adjusting the input electrical signal analog quantity. (Servo valve also has pulse special-purpose Hydraulic cycloid motor Wide modulation input mode). But the structure of these two valves is completely different. The servo valve controls the work of the torque motor by adjusting the electrical signal to deflect the armature and drive the front valve to work. The front valve control oil enters the main valve and drives the valve core to work. The proportional valve regulates the electrical signal to make the electric iron shift, drive the pilot valve core, drive the control oil generated, and drive the main valve core. The hyperbolic cosine of 4. The hyperbolic cosine of. Liaoning Hydraulic cycloid motor Kinematic viscosity: the ratio of dynamic viscosity μ to the liquid density α. The hyperbolic cosine of 5. The hyperbolic cosine of 5. Fluid power: the force exerted by the flowing liquid on the solid wall to change the flow velocity.