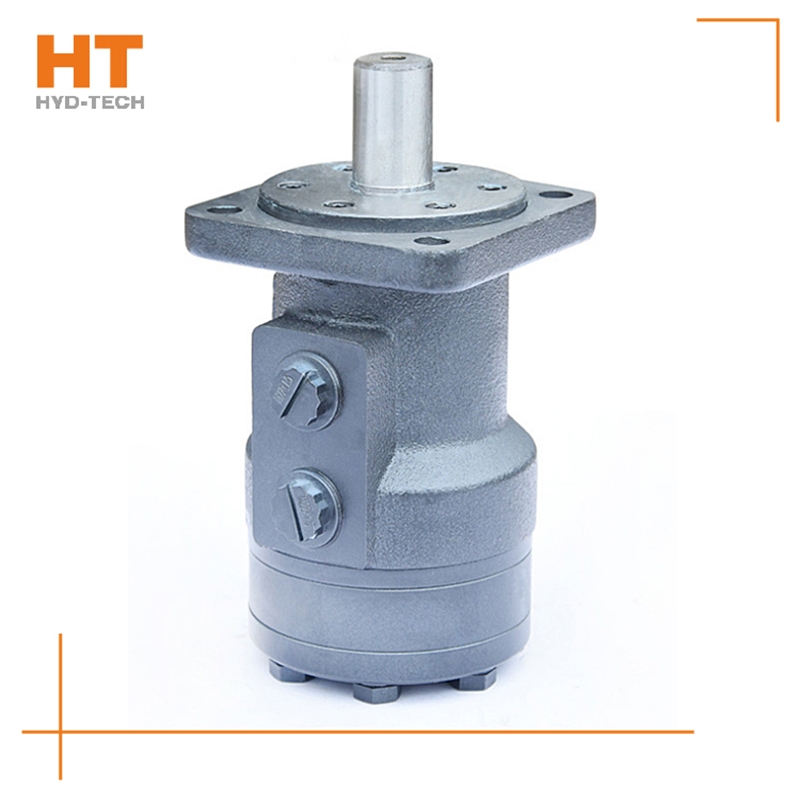
1. The hydraulic system is characterized by high energy density. For motors with the same power, hydraulic motors are much smaller and lighter than motors. And it is easy to apply to mobile devices. 2. The hydraulic motor has convenient speed regulation, which can be adjusted infinitely from 0 to the maximum speed according to the adjustment of the hydraulic valve. The motor itself does not need special design and has low cost. This is much cheaper than motor+reducer, or variable frequency motor and servo motor. 3. The hydraulic motor is totally enclosed and can be safely used in dusty, wet (even underwater) and flammable environments, which is much more reliable than explosion-proof (flameproof) motors. 4. The hydraulic system has strong anti overload capacity, and it is protected by the overflow valve, allowing long (relatively) frequent overloads. It is easy to recover under overload conditions, without damaging the equipment or restarting the equipment. These unparalleled advantages of motors have made hydraulic motors and hydraulic technology rapidly spread and popularized all over the world in the past 20 years. People increasingly feel the importance of hydraulic motors in practice.
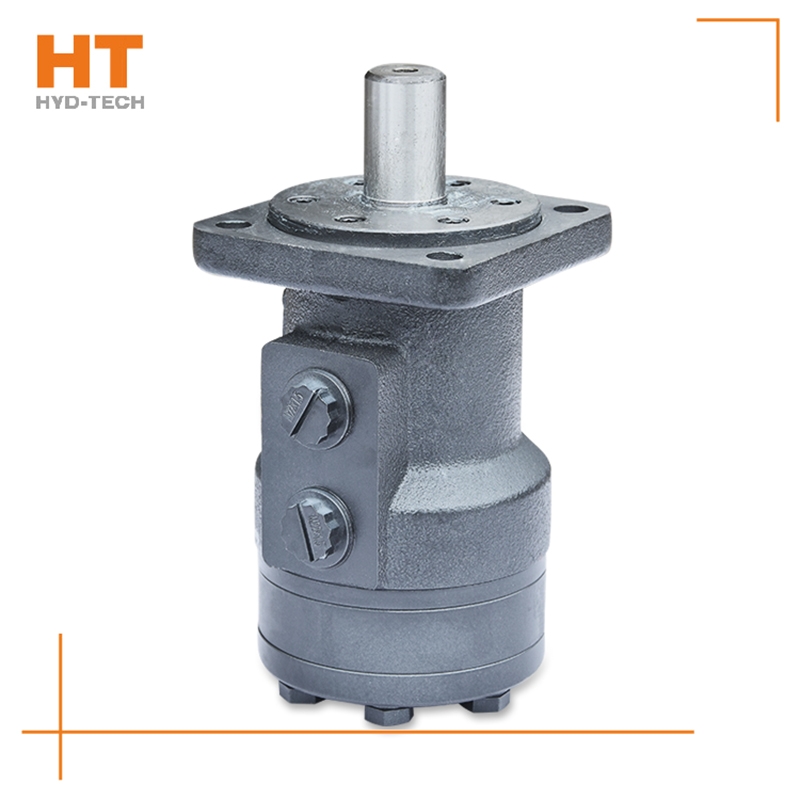
Most of its hydraulic system uses working medium, such as hydraulic oil with continuous fluidity, which converts the mechanical energy of the prime mover driving the pump into the pressure energy of the liquid through the hydraulic pump, and sends it to the actuator (hydraulic cylinder, hydraulic motor or swing hydraulic motor) through various control valves, such as pressure, flow, direction, etc., to convert it into mechanical energy to drive the load. This hydraulic system is generally composed of the following parts: power source, actuator, control valve, hydraulic auxiliary device and hydraulic working medium, which play their respective roles: power source: prime mover (motor or internal combustion engine) and hydraulic pump, whose role is to convert the mechanical energy generated by the prime mover into the pressure energy of liquid, and output oil with a certain pressure;
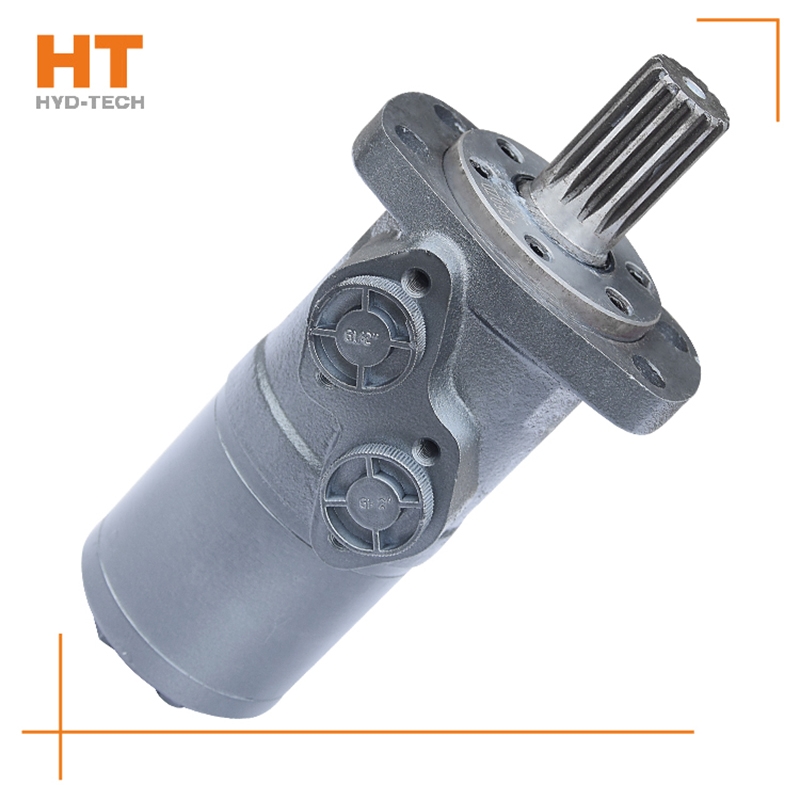
1. Pascal principle: also known as static pressure transmission principle, it refers to the pressure exerted on the static liquid in a closed container is transmitted to all points of the liquid at the same time with equal value. The hyperbolic cosine of 2. The hyperbolic cosine of 2. System pressure: the discharge pressure of the hydraulic pump in the system. The hyperbolic cosine of 3. The hyperbolic cosine of 3. Servo valve and proportional valve: infinitely adjust the output of hydraulic valve, such as pressure, flow and direction, by adjusting the input electrical signal analog quantity. (Servo valve also has pulse special-purpose Cycloidal motor of overhead crane Wide modulation input mode). But the structure of these two valves is completely different. The servo valve controls the work of the torque motor by adjusting the electrical signal to deflect the armature and drive the front valve to work. The front valve control oil enters the main valve and drives the valve core to work. The proportional valve regulates the electrical signal to make the electric iron shift, drive the pilot valve core, drive the control oil generated, and drive the main valve core. The hyperbolic cosine of 4. The hyperbolic cosine of. Mount Huangshan Cycloidal motor of overhead crane Kinematic viscosity: the ratio of dynamic viscosity μ to the liquid density α. The hyperbolic cosine of 5. The hyperbolic cosine of 5. Fluid power: the force exerted by the flowing liquid on the solid wall to change the flow velocity.
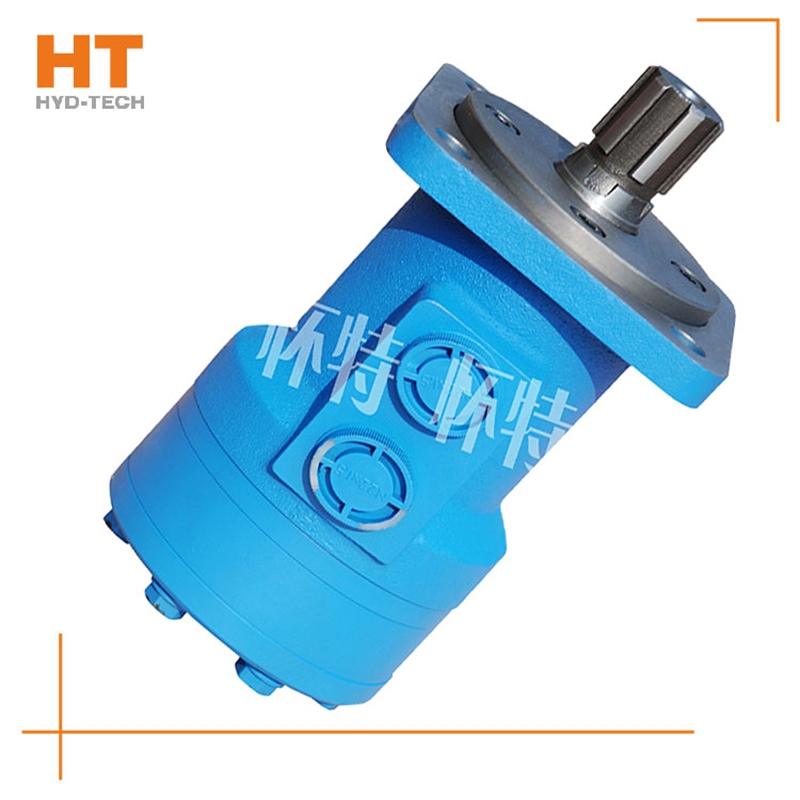
When the main reversing valve of the central closing system and the central closing system is in the neutral position, all oil ports of the reversing valve are closed. If a fixed pump is used for oil supply, the liquid of the hydraulic pump will return to the tank at high pressure through the overflow valve. When the reversing valve is in neutral position, energy transmission starts from the high value, that is, the maximum pressure regulating value of the system. Just reverse Cycloidal motor of overhead crane Manufacturer , its energy can be used by the actuator. When the reversing valve is in the middle position, it sometimes bears all the pressure of the system, so the internal leakage is greater than that of the open system. Generally, when the Mount Huangshan Cycloidal motor of overhead crane In this case, the energy consumption of the closed loop is high, but if the intermediate unloading measures are added or the pressure compensated variable pump is used for oil supply, the energy consumption of the closed loop can be greatly reduced. Closed hydraulic systems are used for a variety of equipment.
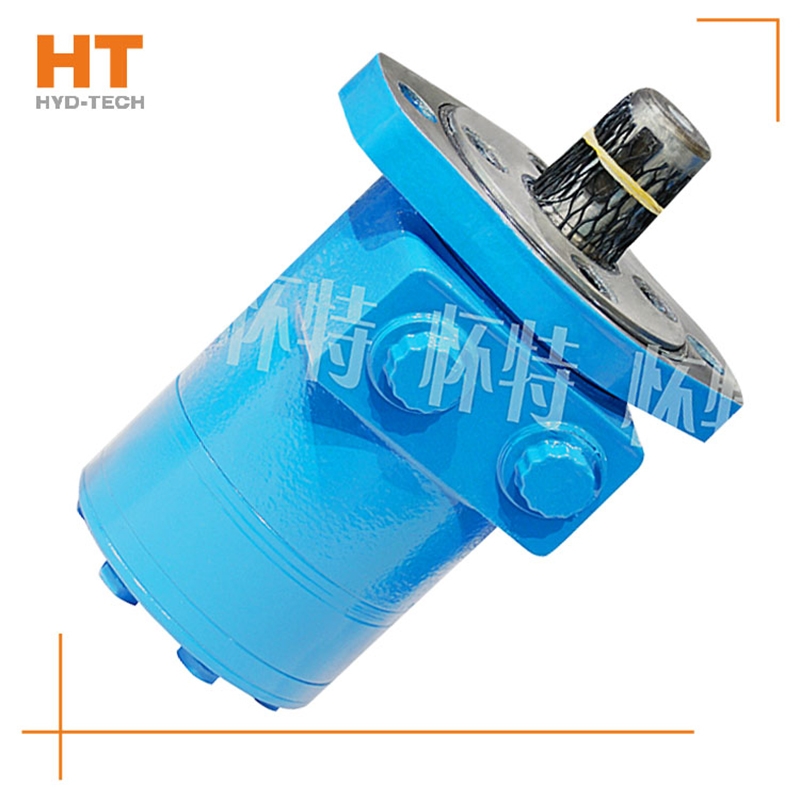
After disassembling and inspecting the hydraulic motor installed on the drill, it was found that the friction surface of the valve disc and the port plate of the hydraulic motor was severely worn, and the deepest worn part was 0. 15mm; The output shaft oil seal is leaking. Cause analysis of oil leakage of output shaft oil seal. After disassembly inspection and test, the axial and radial clearances of the output shaft meet the standard requirements special-purpose Cycloidal motor of overhead crane There is no obvious wear on the oil seal mating surface. However, it is found that the oil seal rubber has hardened and its elasticity has deteriorated. With the increase of sealing lip wear, the pre tightening capacity and sealing performance decrease, and the excessive oil temperature accelerates the wear of sealing lip; In addition, due to the liquid Mount Huangshan Cycloidal motor of overhead crane The leakage of the pressure motor causes the back pressure in the housing to be too high, which further aggravates the wear and leakage of the sealing lip. The smaller the friction of the rotor in the stator sleeve, the higher the mechanical efficiency of the motor.
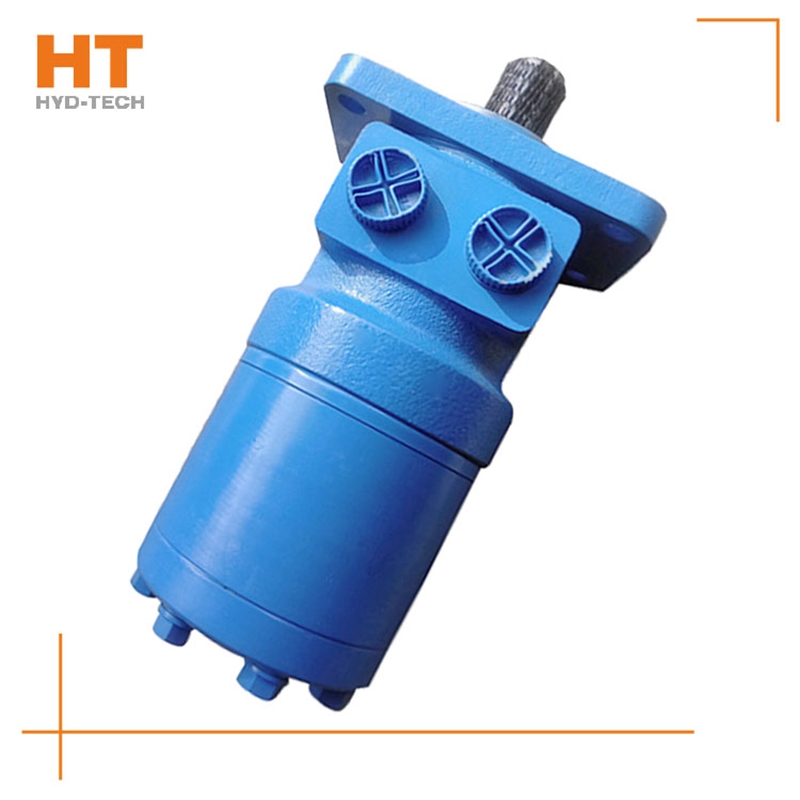
At present, the system used in series by multiple cycloidal motors (see Figure 1) is applied to sweepers, trenchless drills and airport luggage carts. The output shaft of the hydraulic motor often leaks oil during use, so it is useless to replace the dynamic seal of the output shaft. In series application, the problem of casing oil leakage pressure is ignored. The oil leakage pressure of the housing refers to the maximum pressure that the motor shaft seal can bear after the hydraulic motor is fully lubricated inside; If the hydraulic motor is applied special-purpose Cycloidal motor of overhead crane Improper. After the machine has been working continuously for a period of time, due to various factors, the oil in the housing will not be released, resulting in higher and higher pressure in the housing of the hydraulic motor, which first leads to the failure of the shaft seal. The casing leakage pressure mentioned here is not the bursting pressure of the casing, but the pressure that the motor output shaft dynamic seal can bear. In the motor samples of some manufacturers, only the back pressure is mentioned. Actually, back pressure refers to electricity Cycloidal motor of overhead crane Manufacturer The return oil pressure of the engine, not the oil discharge pressure of the casing. During operation, the requirements for the oil discharge pressure of the cycloidal motor housing are as follows. Eaton is the world's first cycloid motor manufacturer. In China's domestic cycloidal motor manufacturing industry, Jining Jinjia Hydraulic Co., Ltd. uses Eaton technology to produce cycloidal motors. Its output shaft dynamic seal has better bearing capacity, that is, the unique internal oil circuit design of the company's products enables internal oil drainage not only to lubricate parts, but also to discharge excess oil while maintaining a certain housing oil drainage pressure.