Generally, rolling bearing or hydrostatic sliding bearing, hydraulic special-purpose Danfoss cycloid motor Since the pressure motor works under the condition of input pressure oil, it does not need to have self-priming capacity, but it needs to have a certain initial air tightness to provide the necessary starting torque. The existence of these differences makes the structure of the hydraulic motor and the hydraulic pump relatively close, but they cannot work reversibly. The classification of hydraulic motors can be divided into gear type, impeller type, plunger type and other types according to the structure type. According to the rated speed of the hydraulic motor, it can be divided into high speed and low speed. The rated speed exceeds 500r/min Yangzhou Danfoss cycloid motor High speed hydraulic motor, while the rated speed is lower than 500r/min, it belongs to low speed hydraulic motor.
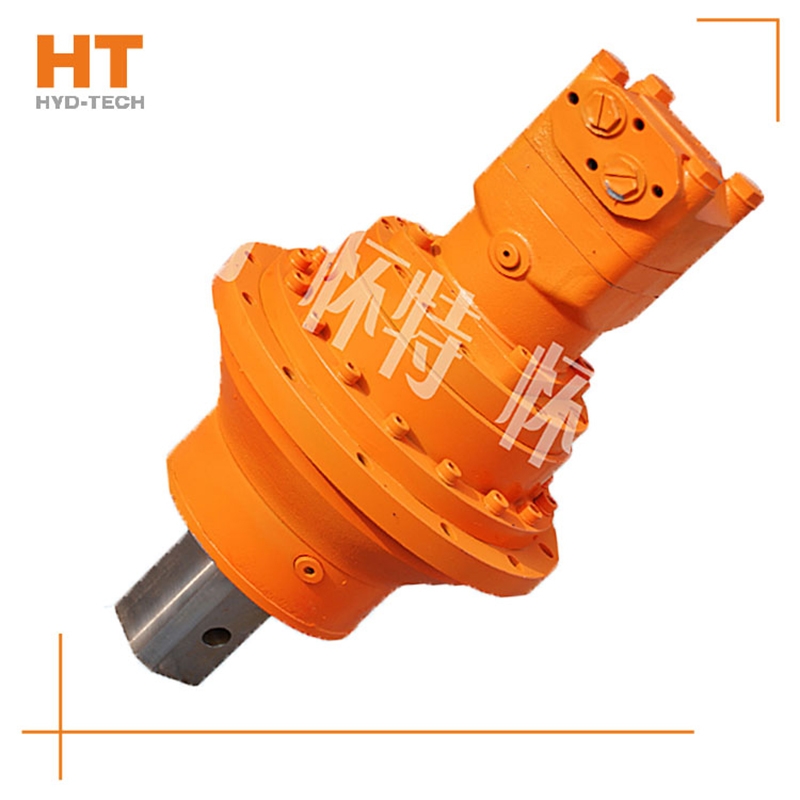
System for fixed equipment. This hydraulic system is mostly an open cycle system, including machine tools (workpiece clamping, worktable feeding, direction exchange, spindle drive), presses (pressing, blank holder, direction exchange, workpiece ejection), die-casting machines and injection molding machines (mold closing, demoulding, preforming, injection mechanisms), medical devices, garbage compression and other mechanical devices Yangzhou special-purpose System of standby and working devices. The hydraulic system for traveling equipment includes both open circulation system and closed circulation system, including vehicle driving (traveling drive, steering, braking and working equipment Danfoss cycloid motor Price ), material conveying, loading, unloading and conveying equipment (conveying mechanism, transposition mechanism), various systems of aviation, space and navigation engineering.
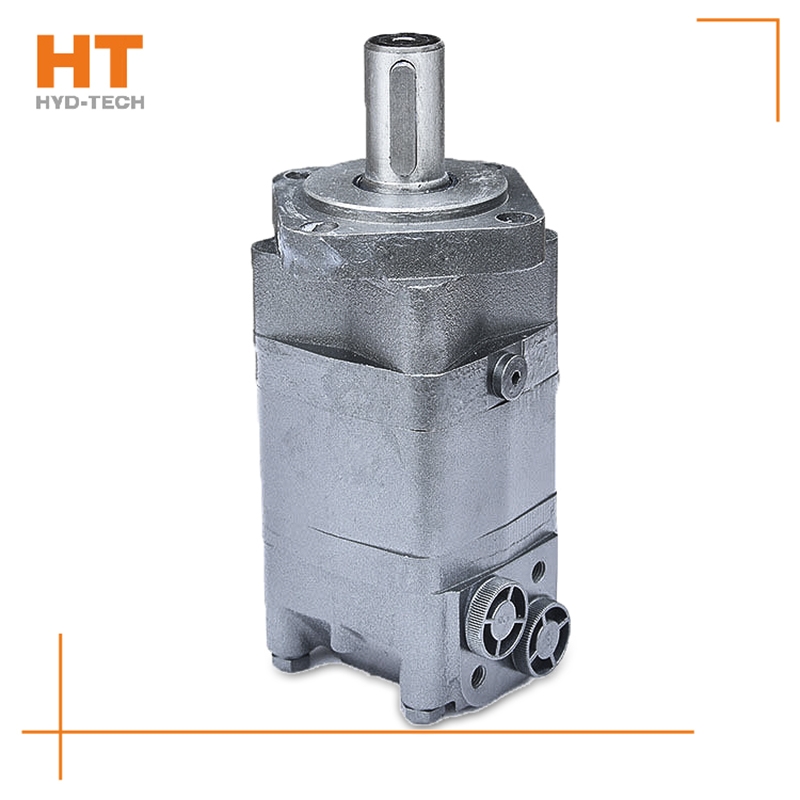
Oil filling process sequence: shell oil filler → oil filling sleeve groove → oil filling sleeve groove → shell oil filling hole → diaphragm → stator. Oil drainage process sequence: rotating stator → diaphragm Danfoss cycloid motor Price → Shell oil distribution hole → oil distribution jacket longitudinal groove → oil distribution jacket groove → shell oil return port. The rotating motion of the rotor includes rotation (rotation in the direction of expanding the high-pressure cavity around the center of the rotor) and revolution (rotation in the direction of deviation from the radius around the center of the stator). The rotation of the rotor is opposite to the revolution direction, and the rotation is transmitted to the output shaft through the linkage shaft. Rotor rotates for 1 cycle special-purpose Danfoss cycloid motor The rotor is driven by 42 pressure oil with the maximum volume for 6 revolutions, so the motor has a large emissions.
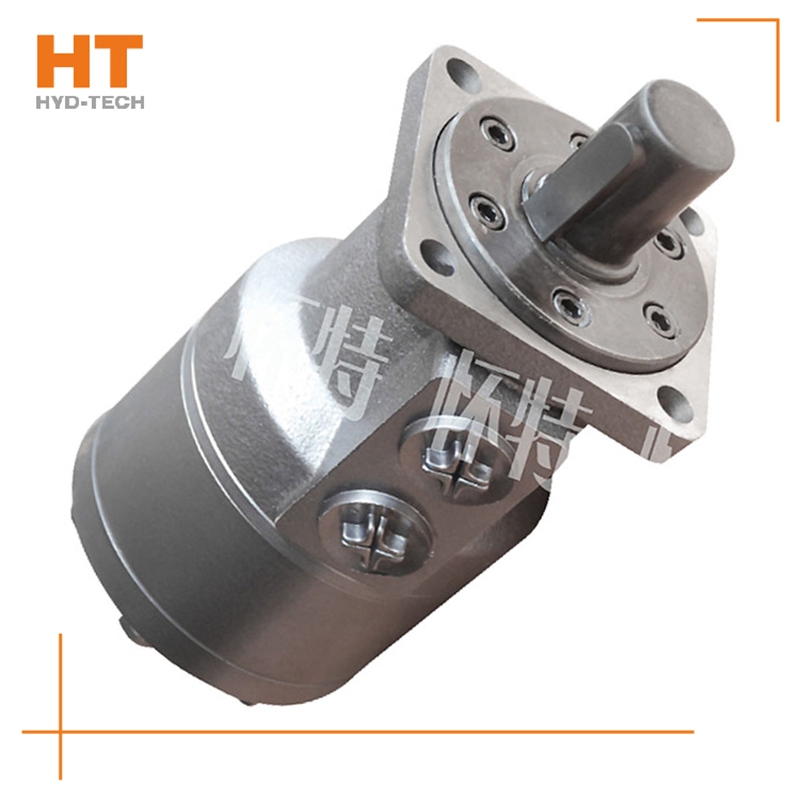
Along the revolution direction of the rotor, the volume of the tooth cavity at the front side of the connection between the rotor and the stator becomes smaller, which is an oil discharge cavity, and the volume at the rear side becomes larger. When the connecting line passes through the two tooth roots of the rotor, the oil inlet ends and the largest tooth cavity appears. When the connecting line passes through the two tooth tops of the rotor, the oil drainage ends and the smallest tooth cavity appears. In order to ensure the continuous rotation of the rotor, it is necessary to have the same regular oil distribution mechanism to cooperate with it, so that the tooth cavity at the front side of the connecting pipeline is always connected with the oil drain port, and the rear side is connected with the oil inlet port. As mentioned above, the oil distribution mechanism consists of a housing and an oil distribution sleeve. The 12 longitudinal grooves (x) on the oil distribution sleeve and the 12 intervals formed by the oil distribution groove face the root and top of the rotor through the positioning device, which proves that when the largest and smallest cavities occur, the oil distribution hole of the housing can be closed, thus separating the oil inlet groove and oil outlet groove of the oil distribution sleeve.