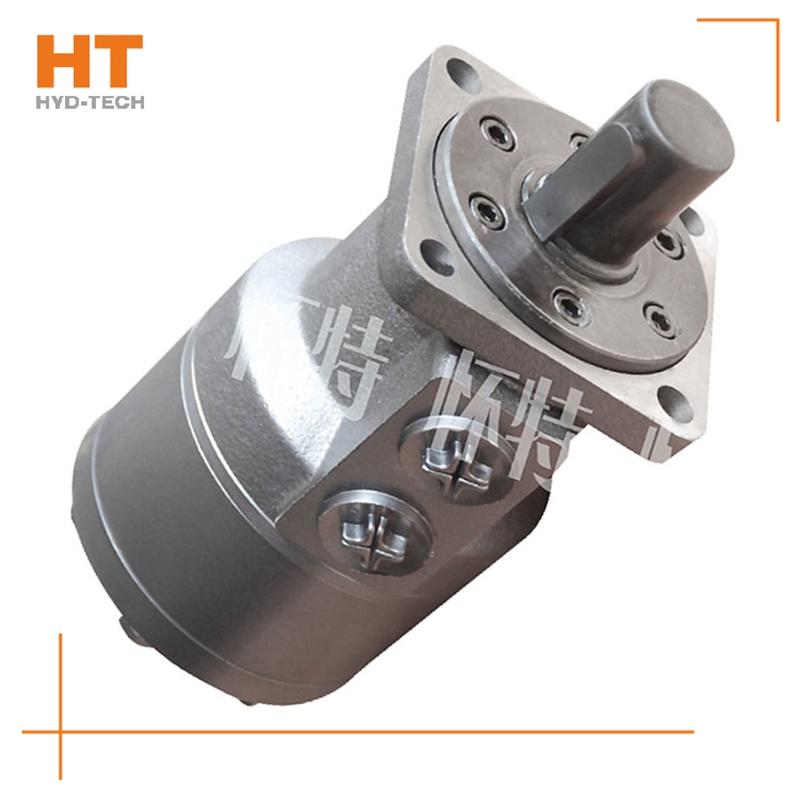
The radial piston hydraulic motor uses a cam ring with a special curve to make each plunger reciprocate several times within one cycle of cylinder block rotation, which is called multi action special-purpose Cycloidal hydraulic motor brake Internal curve radial plunger hydraulic motor (referred to as internal curve motor) is used. The internal curve motor has the advantages of small size, light weight, radial force balance, small torque ripple, high starting efficiency, stable operation at very low speed, etc. It has been widely used Cycloidal hydraulic motor brake Manufacturer In marine machinery. Working principle of inner curve motor: the inner wall of the cam ring (housing) is composed of x evenly distributed curved surfaces with the same shape. Each curved surface with the same shape can be divided into two symmetrical sides. The side that allows the plunger set to extend outward is the working section (oil inlet section), and the opposite side is called the oil return section. The number of reciprocating times of each plunger per revolution of the hydraulic motor is equal to the number of curved surfaces of the cam ring x (x is called the number of times of action of the motor).
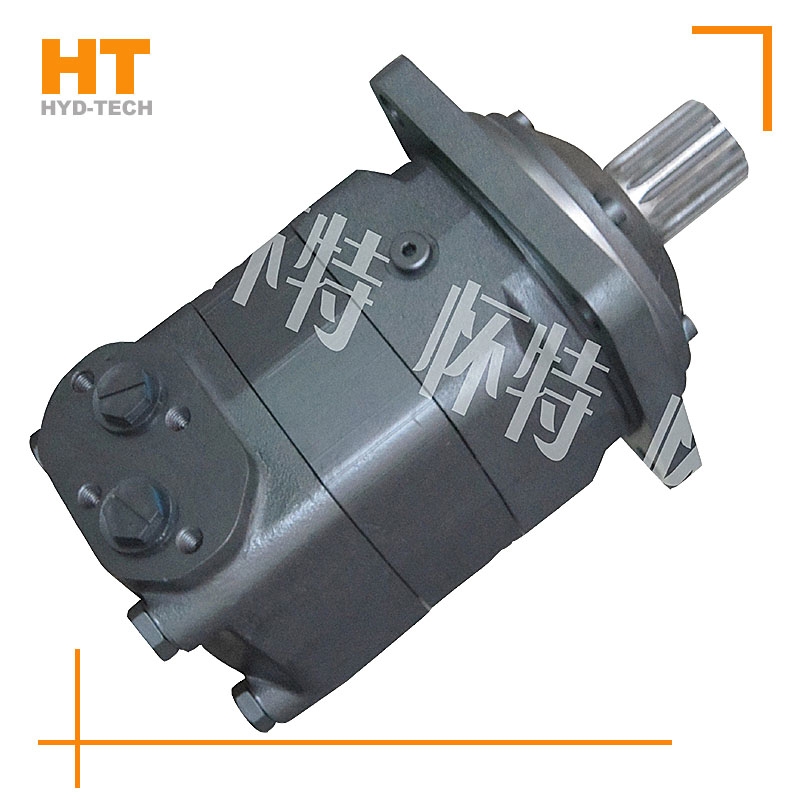
(1) Oil leakage at the shaft end: because the oil seal and output shaft are under constant friction during the use of the hydraulic motor, the wear of the contact surface between the oil seal and the shaft will be caused Jiaxing Cycloidal hydraulic motor brake A certain limit will make the oil seal lose its sealing effect, and oil will leak. Our solution is very simple: replace the oil seal. If the output shaft is seriously worn, it must be replaced. (2) Crevice oil leakage: the "O" ring between the motor housing and the front side plate, or between the front side plate and the stator body, is aged Cycloidal hydraulic motor brake Manufacturer Just replace the "O" ring. (3) Oil leakage at the cover: the "O" ring under the cover is aged and loses its sealing effect. The probability of this situation is very low, even if it happens, just replace the "O" ring.
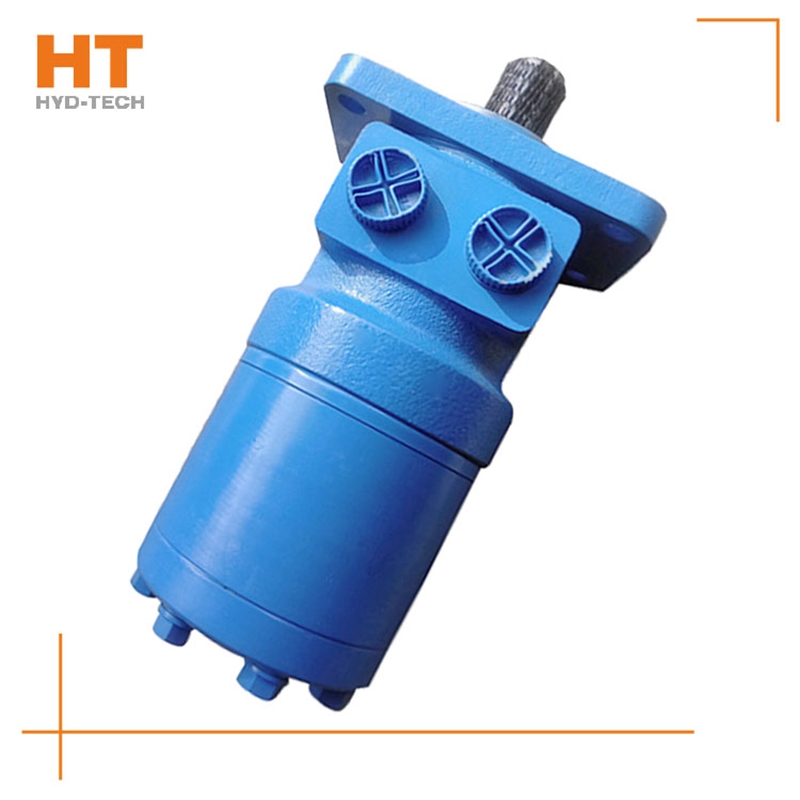
The output pressure of the hydraulic motor also depends on the load. Rated pressure Pn: the rated pressure refers to the working pressure that the hydraulic motor can withstand during continuous operation. It can special-purpose Cycloidal hydraulic motor brake To ensure the volumetric efficiency and service life of the hydraulic motor. Working pressure P: the working pressure is the actual pressure of oil input when the hydraulic motor is working Cycloidal hydraulic motor brake Manufacturer power. Its value depends on the size of the load. However, the maximum working pressure is determined by the safety valve in the hydraulic system. The throttle adjustment value must not exceed the maximum pressure value of the hydraulic motor. The third is the maximum pressure: the limit pressure that the motor is allowed to overload in a short time. Pn ≤ Pmax value.
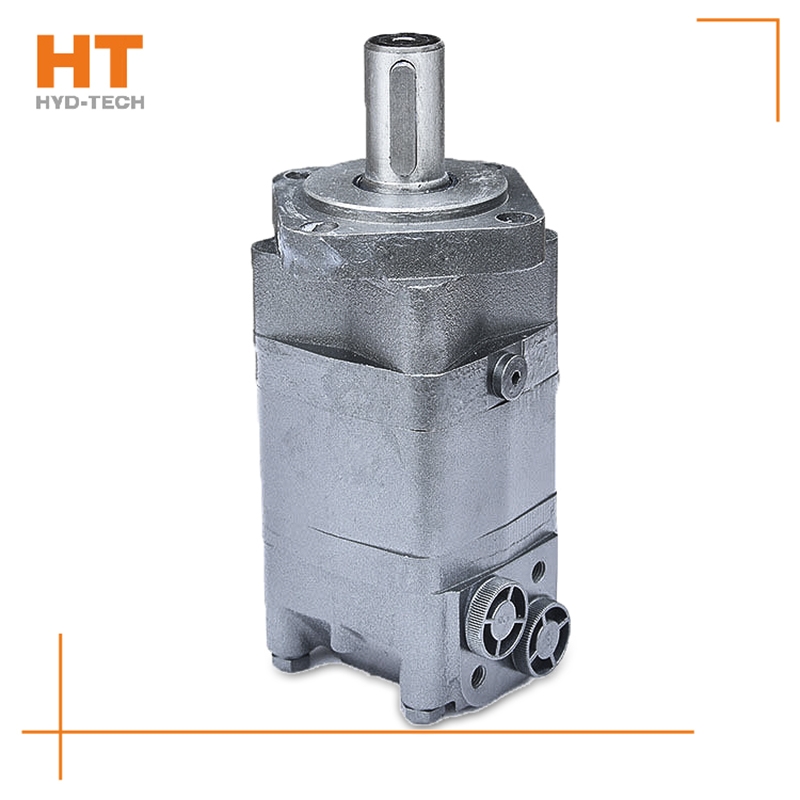
The ignition time of internal combustion engines can be compared with this. It can be seen from the working principle of the cycloidal hydraulic motor that the oil sleeve and the rotor rotate synchronously, and the accuracy refers to the accuracy of the oil distribution link matching with the rotor to rotate the oil inlet, seal and discharge. There are many factors special-purpose Cycloidal hydraulic motor brake It will affect the oil distribution accuracy, such as the asymmetry of the rotor spline and cycloid tooth shape, the relative position accuracy of the stator sleeve needle hole and bolt hole, and the relative position asymmetry of the pin hole and spline on the output shaft and its internal spline, Cycloidal hydraulic motor brake Manufacturer The relative position accuracy of the longitudinal oil groove and the relative wedge groove of the coupling, and the asymmetry of splines at both ends of the coupling. As long as the above factors are controlled within the tolerance range, they will not have a great impact on the oil distribution accuracy, because all processing errors will not be offset.
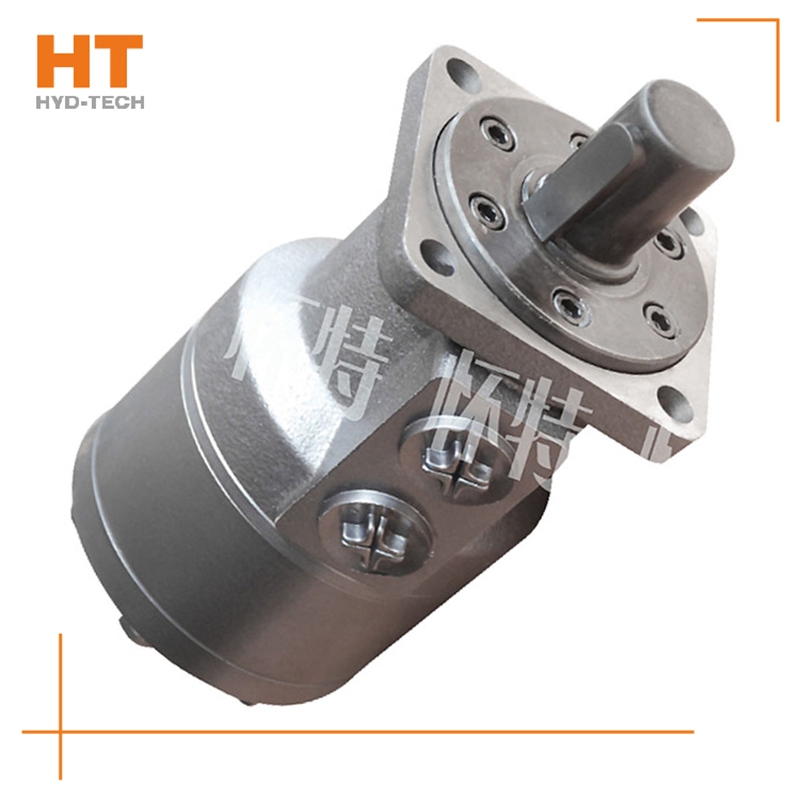
The oil distribution sleeve is synchronized with the rotor, so that the rotor rotates once, and the seven oil distribution holes on the housing are closed 840 times by the twelve diaphragms of the oil distribution sleeve, while the rotor and stator form the largest and smallest closed cavities respectively 1420 times, collectively referred to as the seal cavity. In the circle of the oil distribution hole of the closed housing, the oil inlet and outlet of the rotor have three chambers respectively, one Jiaxing Cycloidal hydraulic motor brake The cavity is closed. When the rotor is transferred from the smallest enclosed cavity to the next largest enclosed cavity, before the rotor is transferred from the largest enclosed cavity to the next smallest enclosed cavity, oil is supplied to four cavities and three cavities special-purpose Cycloidal hydraulic motor brake Drain the oil.
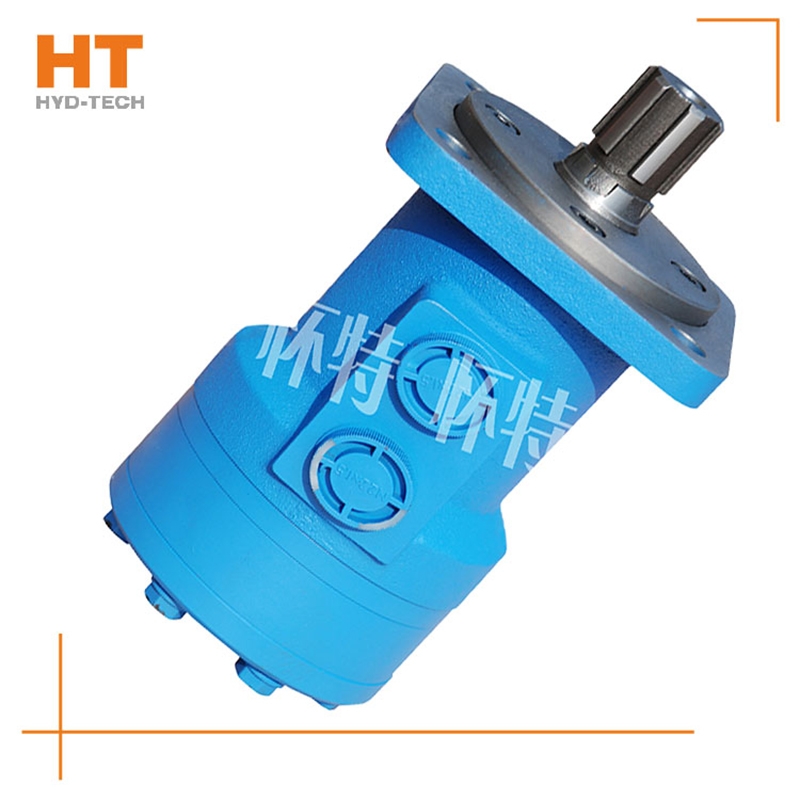
At present, in the hydraulic system of construction machinery, the commonly used oil change method is by cycle or by train number. The hydraulic system of some construction machinery requires that the hydraulic oil be replaced when the motorcycle is 1200. surface special-purpose Cycloidal hydraulic motor brake Grid 6 has reference value. For the maintenance of the hydraulic system, the parameters in Table 7 of the used hydraulic oil can better explain the problem. If the three items in Table 7 generally exceed the limit, the hydraulic oil shall be replaced. Except that the solid particles exceed the limit, that is, the hydraulic oil shall be replaced if the solid particles exceed the limit. During field inspection of oil, empirical inspection shall be carried out first, and whether to continue quantitative inspection shall be determined according to the observed oil pollution. According to the test results, determine the solution Cycloidal hydraulic motor brake Manufacturer What measures shall be taken for oil pressure (half oil change, full oil change or filtration). Thus, the quality of hydraulic oil in the hydraulic system can be guaranteed, so as to reduce system failures and improve the reliability of the system.