Of course, you can increase the traffic special-purpose Cycloidal hydraulic motor of sanitation vehicle Increase the speed, but how much will affect the service life. As long as it is within the rated power range, there is no problem. If the oil pressure reaches the rated pressure and the speed increases, it will exceed the power range it can withstand. Of course, it will damage the service life of the cycloidal hydraulic motor. Just like not eating so much hard food, it will damage the stomach. Increasing the flow can only increase the speed in a limited way, from 500 to 900, change the model of the motor, increase the flow of the cycloidal motor, increase the speed without control, increase the internal oil pressure, increase the internal leakage, directly reduce the efficiency, and damage the motor. Above Taizhou Manufacturer Ming can try, and consult the cycloid hydraulic motor expert if he thinks the error is found.
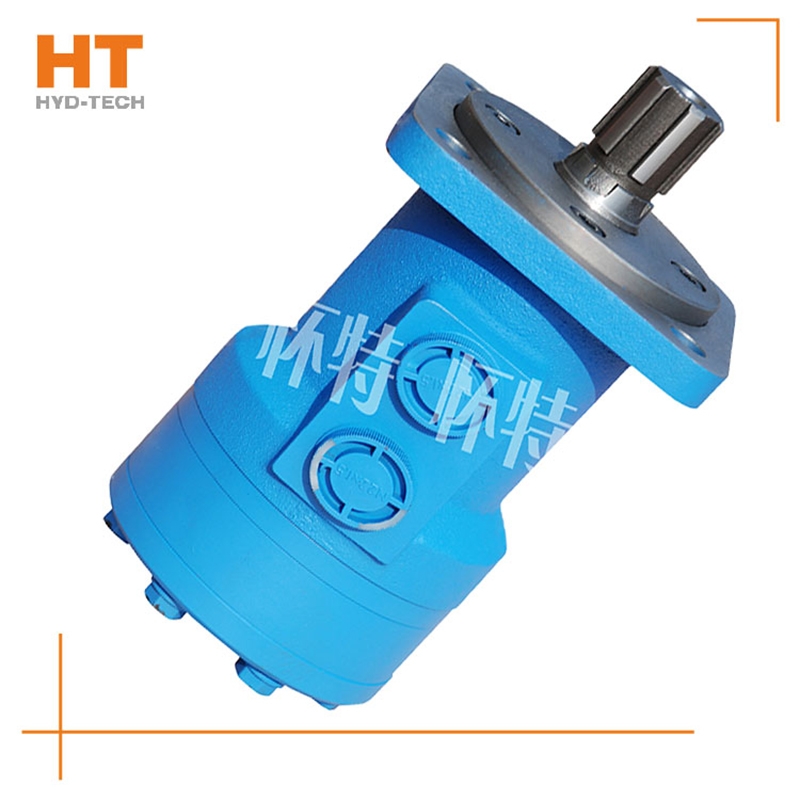
The hydraulic motor manufacturer explains to you the reasons for the poor performance of the hydraulic motor: 1. First of all, according to the analysis of the causes of the wear of the port plate, the main reasons for the weakness of the hydraulic motor are: because the port plate is worn, the oil inlet channel and the oil return channel are connected at the port plate, part of the high-pressure oil leaks, the oil pressure flowing through the stator and rotor pair decreases, and the flow decreases, Eventually, the output speed and torque of the motor will decrease. 2. Due to the wear of the valve plate, its relative position in the valve body has changed Cycloidal hydraulic motor of sanitation vehicle Manufacturer The preload and adhesion of the spring on the valve body between the valve plates will be reduced, which will intensify the leakage of hydraulic oil and lead to the decline of the performance of the hydraulic motor. 3. With the increase of hydraulic oil temperature, its comprehensive performance declines, driving the cycloidal rotor to rotate Taizhou Manufacturer The ability to move is further reduced. Upon inspection, there is no obvious wear on the joint surface of the stator and rotor pair and the bearing seat and valve disc matched with both sides of the stator and rotor pair. The movement is normal without jamming, which will not cause performance degradation.
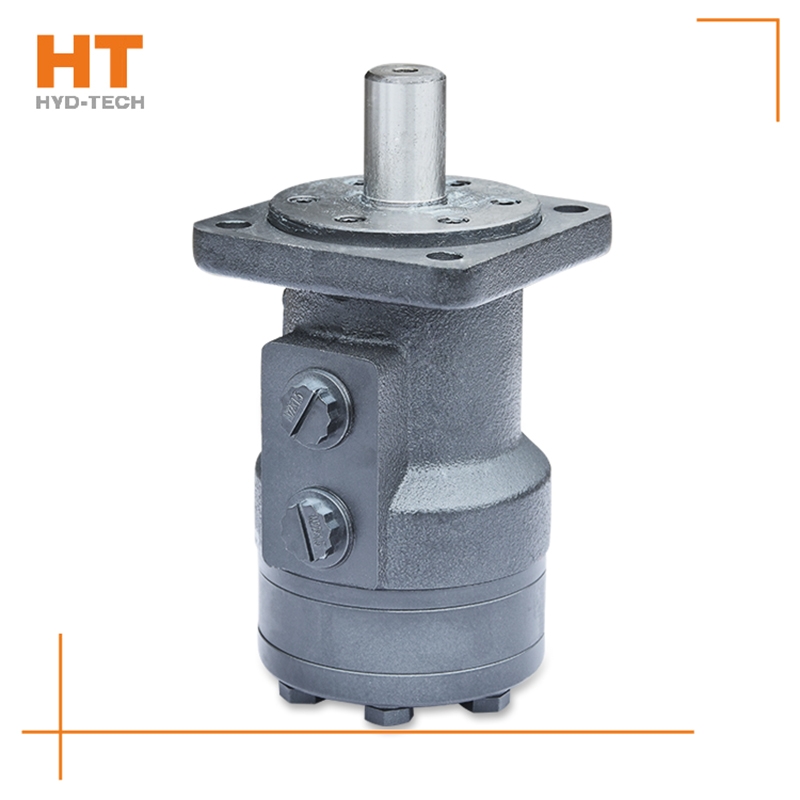
1. Generally, the motor shall be able to run forward and backward. Therefore, the hydraulic motor is usually required to have structural symmetry in the design. 2. The actual working pressure difference of the hydraulic motor depends on the load torque. When the moment of inertia of the driven load is large and the speed is high, rapid braking or reverse rotation is required, high hydraulic impact will be generated. Therefore, the system should be equipped with necessary safety valves and buffer valves. 3. Under normal working conditions, the inlet and outlet pressure of the hydraulic motor is higher than the atmospheric pressure, so there is no suction performance problem like the hydraulic pump. However, if the hydraulic motor can work under pump conditions, its oil inlet should have a minimum pressure limit to avoid cavitation. 4. Some hydraulic motors must have sufficient back pressure at the oil return port to ensure normal operation. The higher the speed, the greater the back pressure, which indicates that the utilization rate of oil source pressure is not high and the system loss is increased. 5. Because the internal leakage of the motor is inevitable, there will be slow sliding when the hydraulic motor oil outlet is closed for braking. Therefore, when long-term accurate braking is required, a separate anti-skid brake shall be set.
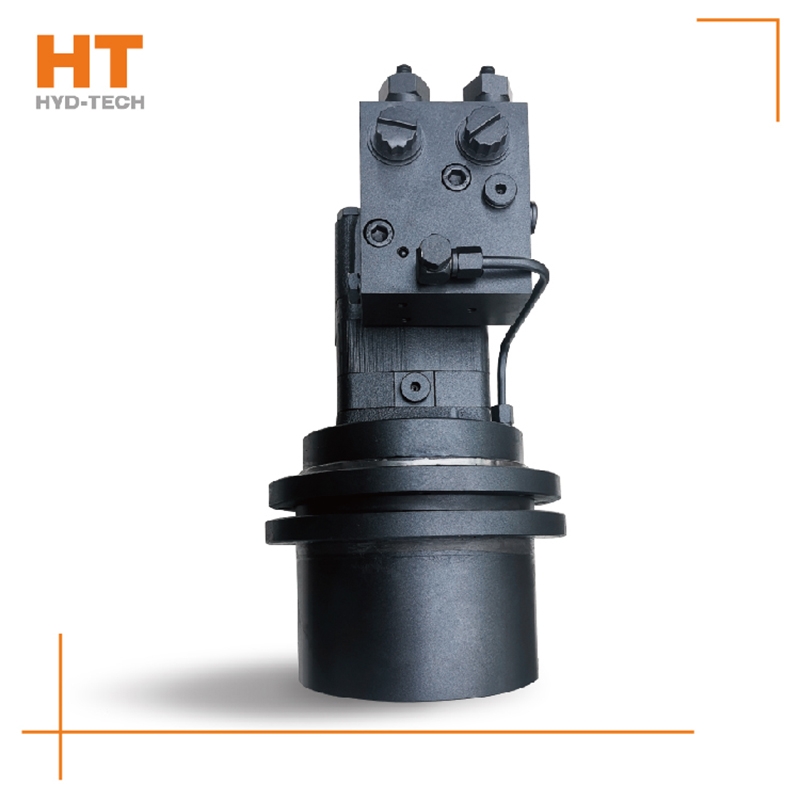
The oil distribution sleeve is synchronized with the rotor, so that the rotor rotates once, and the seven oil distribution holes on the housing are closed 840 times by the twelve diaphragms of the oil distribution sleeve, while the rotor and stator form the largest and smallest closed cavities respectively 1420 times, collectively referred to as the seal cavity. In the circle of the oil distribution hole of the closed housing, the oil inlet and outlet of the rotor have three chambers respectively, one Taizhou Cycloidal hydraulic motor of sanitation vehicle The cavity is closed. When the rotor is transferred from the smallest enclosed cavity to the next largest enclosed cavity, before the rotor is transferred from the largest enclosed cavity to the next smallest enclosed cavity, oil is supplied to four cavities and three cavities special-purpose Cycloidal hydraulic motor of sanitation vehicle Drain the oil.
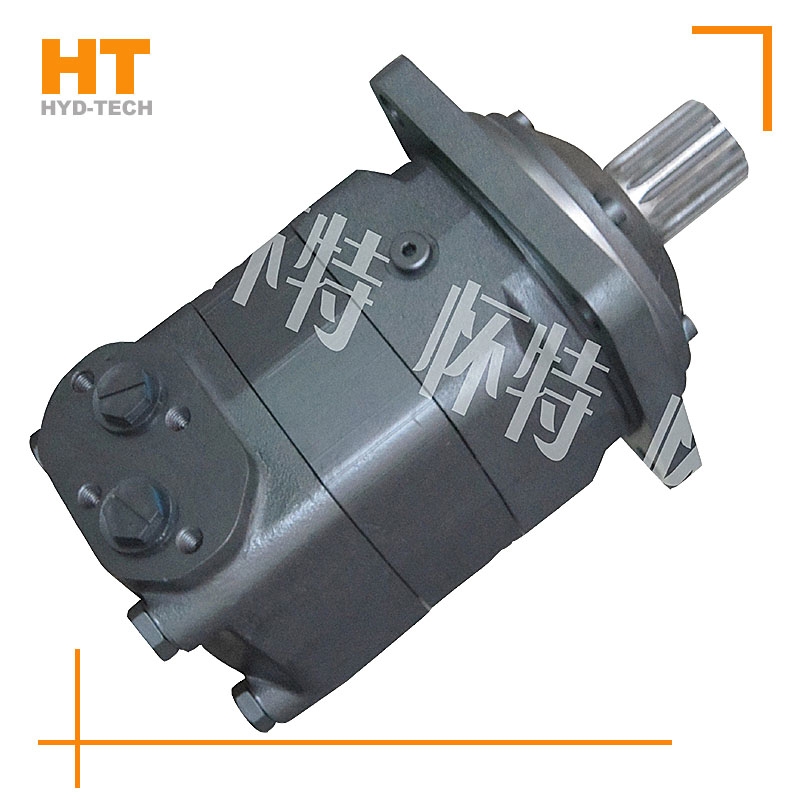
The valve control system controls the flow by changing the opening of the valve throttle, thus controlling the speed of the actuator. Usually, the reason for low efficiency is the existence of throttling and overflow losses. Almost all mechanical equipment adopts valve control system. The pump control system can realize the stepless control of speed by changing the displacement of variable displacement pump, or control the flow through the combination of multiple constant displacement pumps to achieve the stepwise control of speed. The reason for high efficiency is that there is no throttling or overflow loss. It is widely used in high power hydraulic devices such as pressure processing machinery and plastic machinery. The actuator control system controls the flow by changing the variable hydraulic motor flow of the actuator, or through the joint work of multiple quantitative hydraulic motors, or by changing the action area of the composite hydraulic cylinder. Similar to the pump control system, this system has high efficiency because it has no throttling and overflow losses. It is suitable for traveling machinery, press and other hydraulic equipment.