The hydraulic motor is usually put into operation Hangzhou special-purpose Clean before use. The purpose of cleaning is to remove the pollutants, metal chips, fiber compounds and iron cores left in Madai. In the first two hours of operation, even if the motor is not completely damaged, there will be a series of failures. Therefore, the hydraulic motor oil circuit should be cleaned as follows: 1. Clean the oil tank with easy drying cleaning solvent, and then remove the solvent residue with filtered air. 2. Clean all pipes of hydraulic motor. In some cases, it may be necessary to impregnate pipes and joints. 3. Install an oil filter on the pipeline to protect the oil supply pipeline and pressure pipeline of the valve. four special-purpose Cycloidal hydraulic motor with brake Install a flushing plate on the collector to replace precision valves, such as electro-hydraulic servo valve. 5. Check whether all pipes are of proper size and connected correctly.
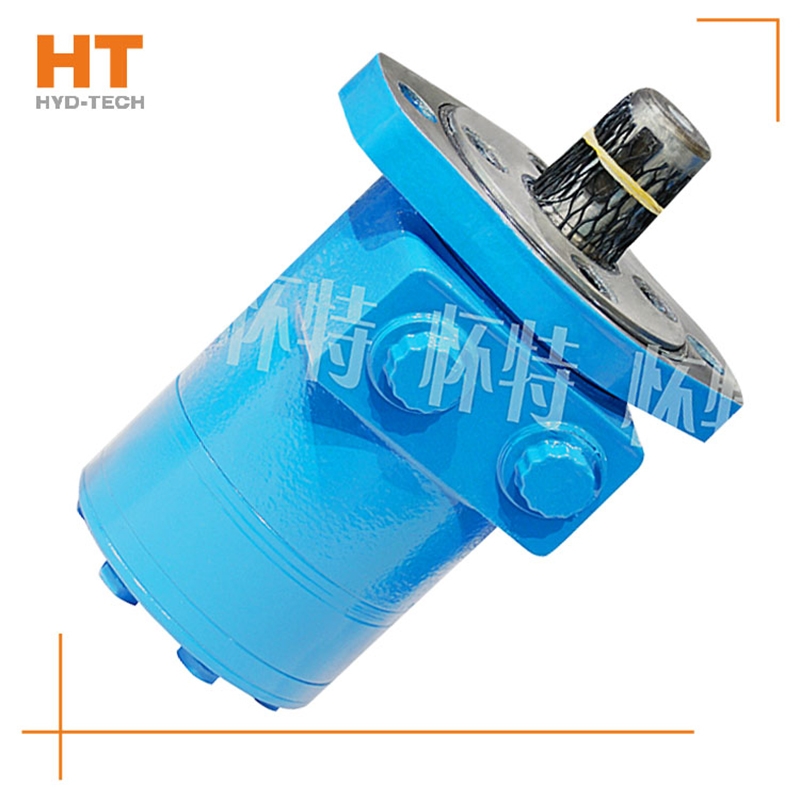
Oil filling process sequence: shell oil filler → oil filling sleeve groove → oil filling sleeve groove → shell oil filling hole → diaphragm → stator. Oil drainage process sequence: rotating stator → diaphragm Cycloidal hydraulic motor with brake manufactor → Shell oil distribution hole → oil distribution jacket longitudinal groove → oil distribution jacket groove → shell oil return port. The rotating motion of the rotor includes rotation (rotation in the direction of expanding the high-pressure cavity around the center of the rotor) and revolution (rotation in the direction of deviation from the radius around the center of the stator). The rotation of the rotor is opposite to the revolution direction, and the rotation is transmitted to the output shaft through the linkage shaft. Rotor rotates for 1 cycle special-purpose Cycloidal hydraulic motor with brake The rotor is driven by 42 pressure oil with the maximum volume for 6 revolutions, so the motor has a large emissions.
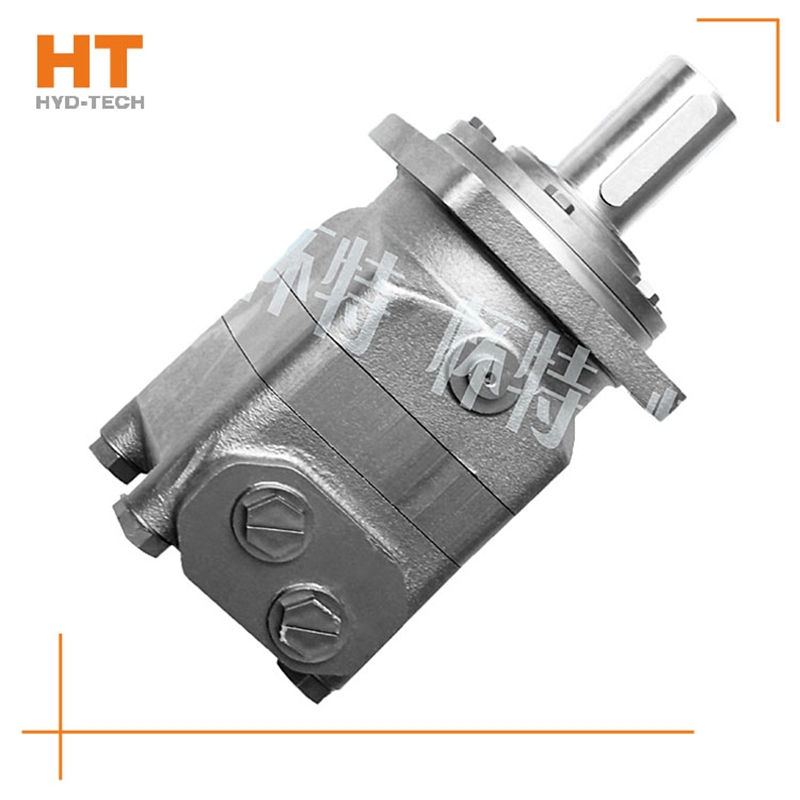
Causes: 1. The pump is damaged, and the pump body is overheated and produces noise. 2. The control valve is closed tightly or the oil supply and return system is blocked, and local overheating occurs. 3. The safety valve is opened, and the valve cries or hisses, and local overheating occurs. 4. The distribution rotary valve is excessively leaking, and the valve chamber is overheated, and it is very hot when touched by hand. 5. The hydraulic motor crankcase is excessively leaking, and the single oil drain pipe is leaking special-purpose Cycloidal hydraulic motor with brake Treatment method for excessive leakage and high oil level: 1. Check the condition of the ball joint 2. Check the sealing condition of the cylinder piston 3. Check the viscosity and operating temperature of the oil 4. Check the contact surface between the oil pan and the housing 5. Check the surface between the connecting rod and the eccentric wheel Cycloidal hydraulic motor with brake manufactor 6. Check the wear of the oil pan and whether the two oil cavity channels at the inlet and outlet of the casting are connected
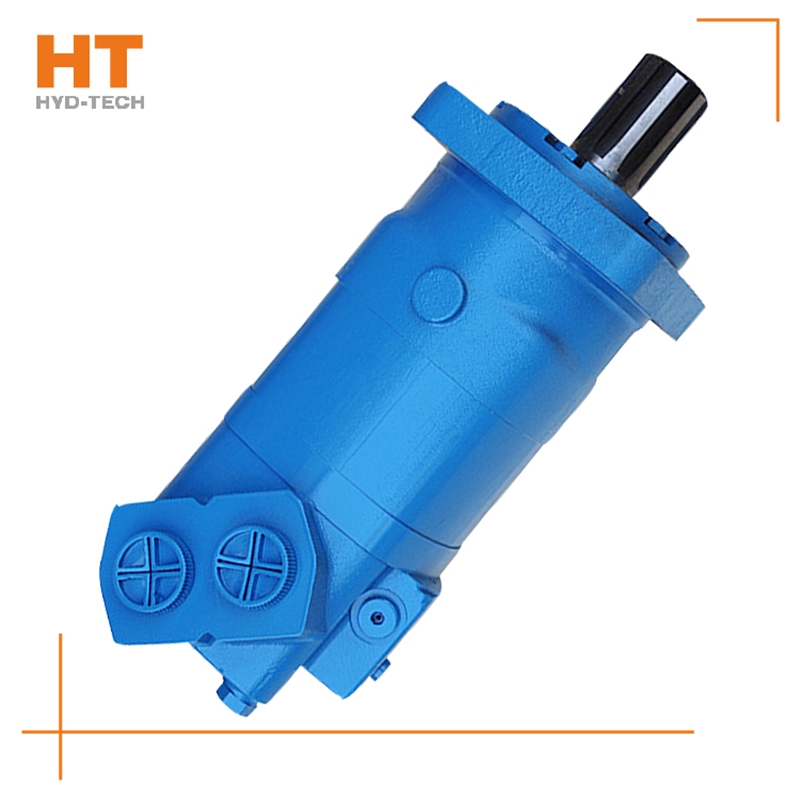
The radial piston hydraulic motor uses a cam ring with a special curve to make each plunger reciprocate several times within one cycle of cylinder block rotation, which is called multi action special-purpose Cycloidal hydraulic motor with brake Internal curve radial plunger hydraulic motor (referred to as internal curve motor) is used. The internal curve motor has the advantages of small size, light weight, radial force balance, small torque ripple, high starting efficiency, stable operation at very low speed, etc. It has been widely used Cycloidal hydraulic motor with brake manufactor In marine machinery. Working principle of inner curve motor: the inner wall of the cam ring (housing) is composed of x evenly distributed curved surfaces with the same shape. Each curved surface with the same shape can be divided into two symmetrical sides. The side that allows the plunger set to extend outward is the working section (oil inlet section), and the opposite side is called the oil return section. The number of reciprocating times of each plunger per revolution of the hydraulic motor is equal to the number of curved surfaces of the cam ring x (x is called the number of times of action of the motor).