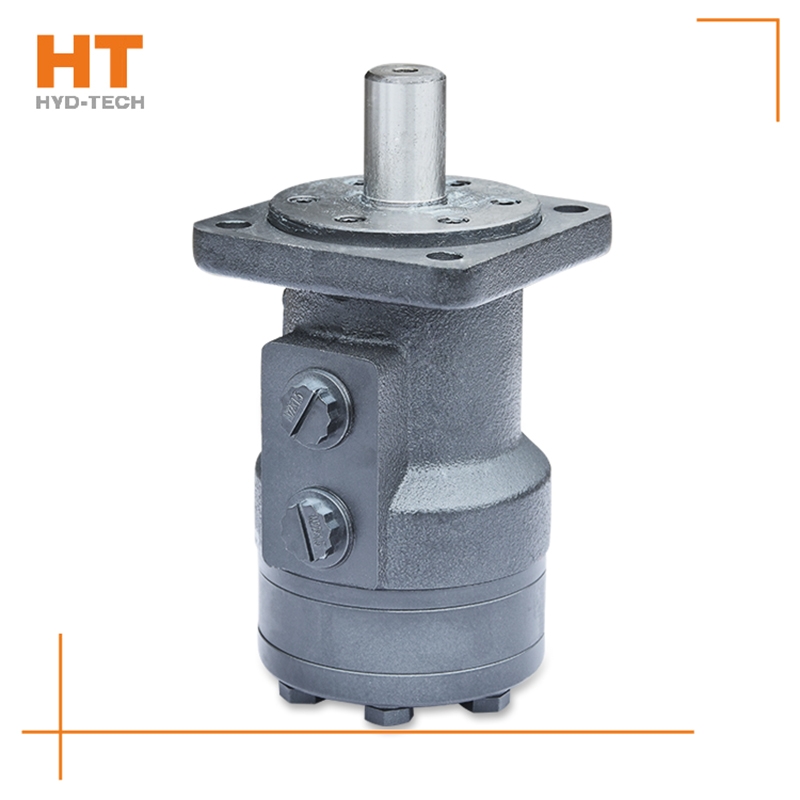
At present, the system used in series by multiple cycloidal motors (see Figure 1) is applied to sweepers, trenchless drills and airport luggage carts. The output shaft of the hydraulic motor often leaks oil during use, so it is useless to replace the dynamic seal of the output shaft. In series application, the problem of casing oil leakage pressure is ignored. The oil leakage pressure of the housing refers to the maximum pressure that the motor shaft seal can bear after the hydraulic motor is fully lubricated inside; If the hydraulic motor is applied special-purpose OM cycloidal motor Improper. After the machine has been working continuously for a period of time, due to various factors, the oil in the housing will not be released, resulting in higher and higher pressure in the housing of the hydraulic motor, which first leads to the failure of the shaft seal. The casing leakage pressure mentioned here is not the bursting pressure of the casing, but the pressure that the motor output shaft dynamic seal can bear. In the motor samples of some manufacturers, only the back pressure is mentioned. Actually, back pressure refers to electricity OM cycloidal motor Manufacturer The return oil pressure of the engine, not the oil discharge pressure of the casing. During operation, the requirements for the oil discharge pressure of the cycloidal motor housing are as follows. Eaton is the world's first cycloid motor manufacturer. In China's domestic cycloidal motor manufacturing industry, Jining Jinjia Hydraulic Co., Ltd. uses Eaton technology to produce cycloidal motors. Its output shaft dynamic seal has better bearing capacity, that is, the unique internal oil circuit design of the company's products enables internal oil drainage not only to lubricate parts, but also to discharge excess oil while maintaining a certain housing oil drainage pressure.
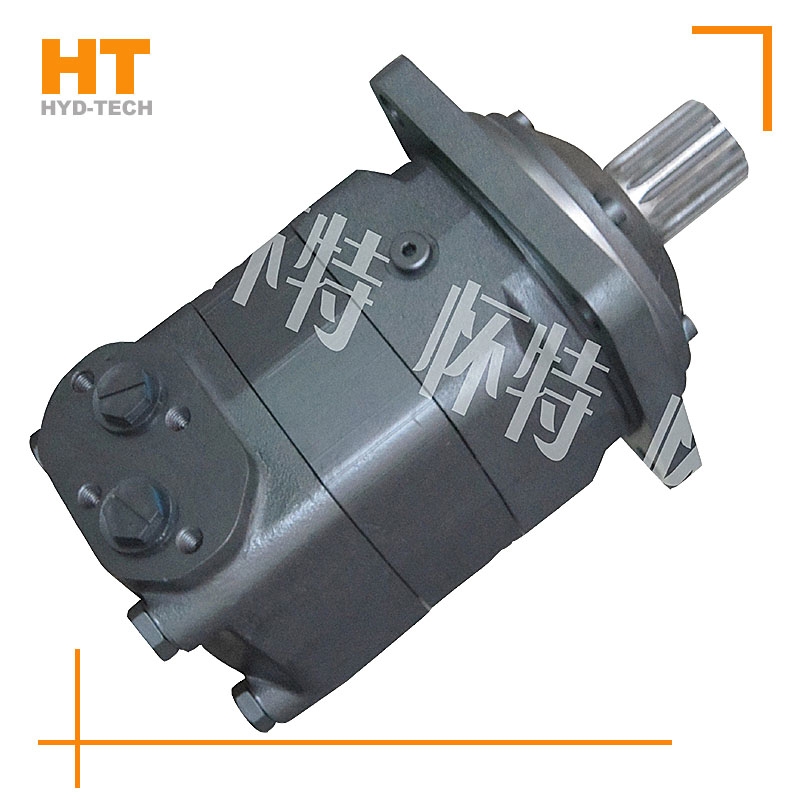
During the operation of hydraulic transmission, the hydraulic actuator can be adjusted steplessly in a large range by adjusting the control valve, and the speed range can reach 2000 meters. Good operation ability and rapidity. The liquid is elastic and can absorb impact, so the hydraulic transmission movement is even and stable; It is easy to realize fast starting, braking and frequent reversing. Reciprocating rotation special-purpose OM cycloidal motor The reversing frequency of rotary motion can reach 500 times/minute, and the reciprocating linear motion can reach 1000 times/minute. It is easy to control operation and realize overload protection. The hydraulic system with convenient operation and control is convenient for automatic control, remote control and overload protection; Automatic lubrication during operation, which is beneficial to Huzhou Manufacturer Heat dissipation, prolong service life. It is convenient for automation and electromechanical hydraulic integration. Hydraulic technology is easy to combine with electronic control and electronic control technology to form an electromechanical hydraulic integration composite system to realize automatic cycle work.
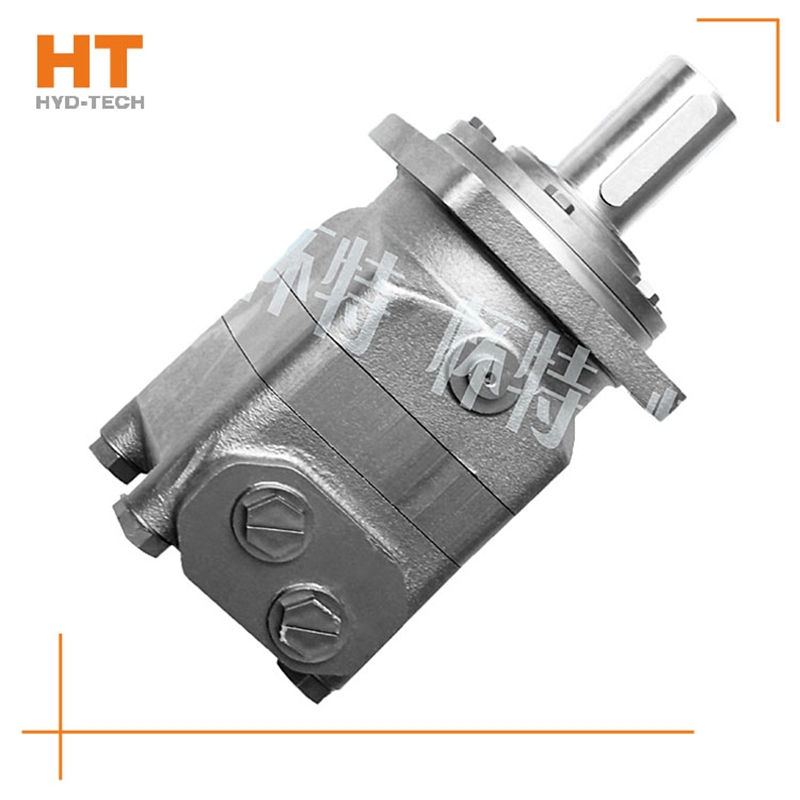
(1) Oil leakage at the shaft end: because the oil seal and output shaft are under constant friction during the use of the hydraulic motor, the wear of the contact surface between the oil seal and the shaft will be caused Huzhou OM cycloidal motor A certain limit will make the oil seal lose its sealing effect, and oil will leak. Our solution is very simple: replace the oil seal. If the output shaft is seriously worn, it must be replaced. (2) Crevice oil leakage: the "O" ring between the motor housing and the front side plate, or between the front side plate and the stator body, is aged OM cycloidal motor Manufacturer Just replace the "O" ring. (3) Oil leakage at the cover: the "O" ring under the cover is aged and loses its sealing effect. The probability of this situation is very low, even if it happens, just replace the "O" ring.
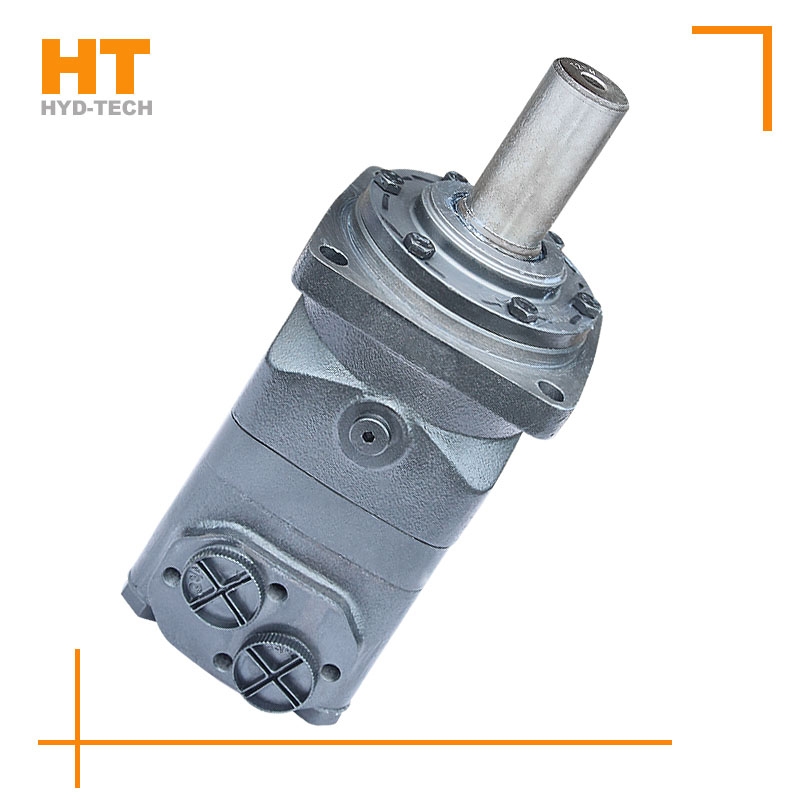
Most of its hydraulic system uses working medium, such as hydraulic oil with continuous fluidity, which converts the mechanical energy of the prime mover driving the pump into the pressure energy of the liquid through the hydraulic pump, and sends it to the actuator (hydraulic cylinder, hydraulic motor or swing hydraulic motor) through various control valves, such as pressure, flow, direction, etc., to convert it into mechanical energy to drive the load. This hydraulic system is generally composed of the following parts: power source, actuator, control valve, hydraulic auxiliary device and hydraulic working medium, which play their respective roles: power source: prime mover (motor or internal combustion engine) and hydraulic pump, whose role is to convert the mechanical energy generated by the prime mover into the pressure energy of liquid, and output oil with a certain pressure;