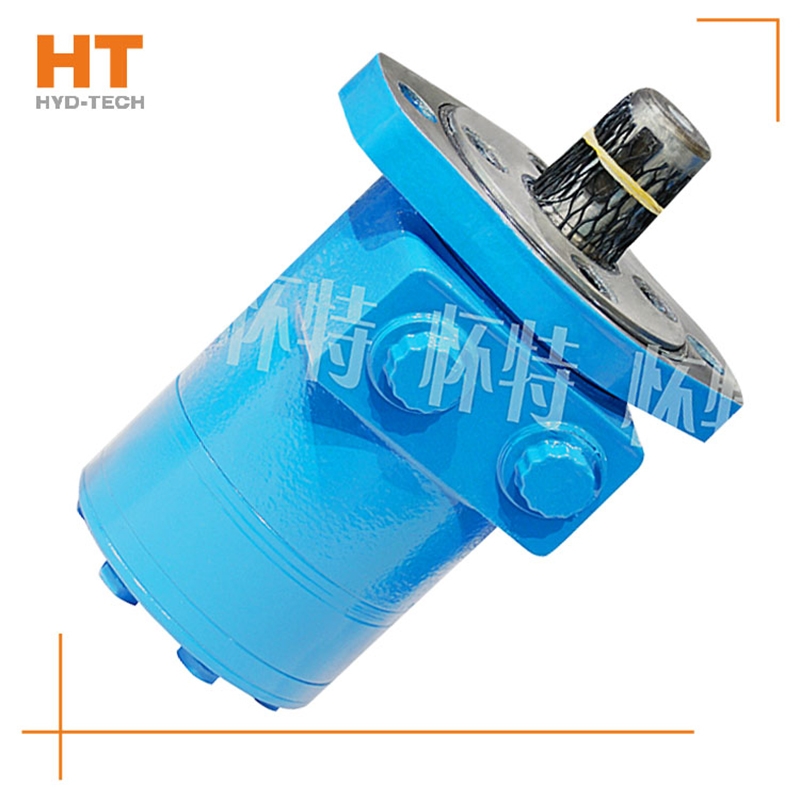
When the high-pressure oil enters the oil distribution shaft and enters each plunger cylinder hole of the working section through the oil distribution window, the corresponding plunger set is pushed against the curved surface of the cam ring L (housing), Foshan Low speed high torque cycloidal hydraulic motor The cam ring surface gives a reaction force to the plunger at the contact position. This reaction force N acts on the common plane where the cam ring surface contacts the roller. This normal reaction force N can be decomposed into radial force PH and circumferential force T, which are balanced with the hydraulic pressure at the bottom of the plunger, while the circumferential force T overcomes the load torque, special-purpose Low speed high torque cycloidal hydraulic motor Drive cylinder 2 to rotate. Under this working condition, the cam ring and oil distribution shaft do not rotate. At this time, the plunger corresponding to the oil return section of the cam gear moves in the opposite direction, and the oil is discharged through the oil distribution shaft.
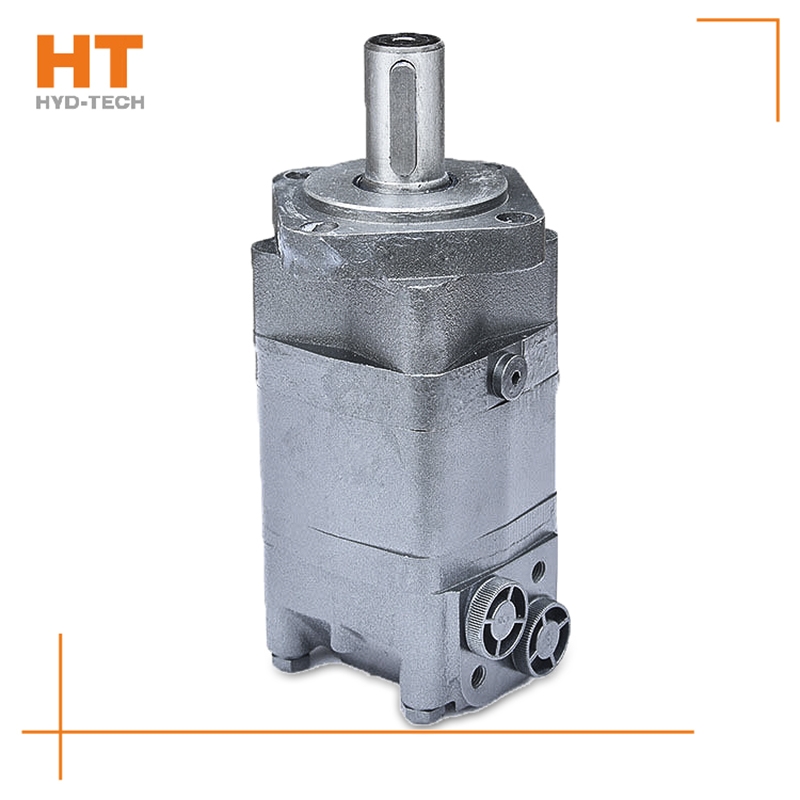
The radial piston hydraulic motor uses a cam ring with a special curve to make each plunger reciprocate several times within one cycle of cylinder block rotation, which is called multi action special-purpose Low speed high torque cycloidal hydraulic motor Internal curve radial plunger hydraulic motor (referred to as internal curve motor) is used. The internal curve motor has the advantages of small size, light weight, radial force balance, small torque ripple, high starting efficiency, stable operation at very low speed, etc. It has been widely used Low speed high torque cycloidal hydraulic motor Manufacturer In marine machinery. Working principle of inner curve motor: the inner wall of the cam ring (housing) is composed of x evenly distributed curved surfaces with the same shape. Each curved surface with the same shape can be divided into two symmetrical sides. The side that allows the plunger set to extend outward is the working section (oil inlet section), and the opposite side is called the oil return section. The number of reciprocating times of each plunger per revolution of the hydraulic motor is equal to the number of curved surfaces of the cam ring x (x is called the number of times of action of the motor).
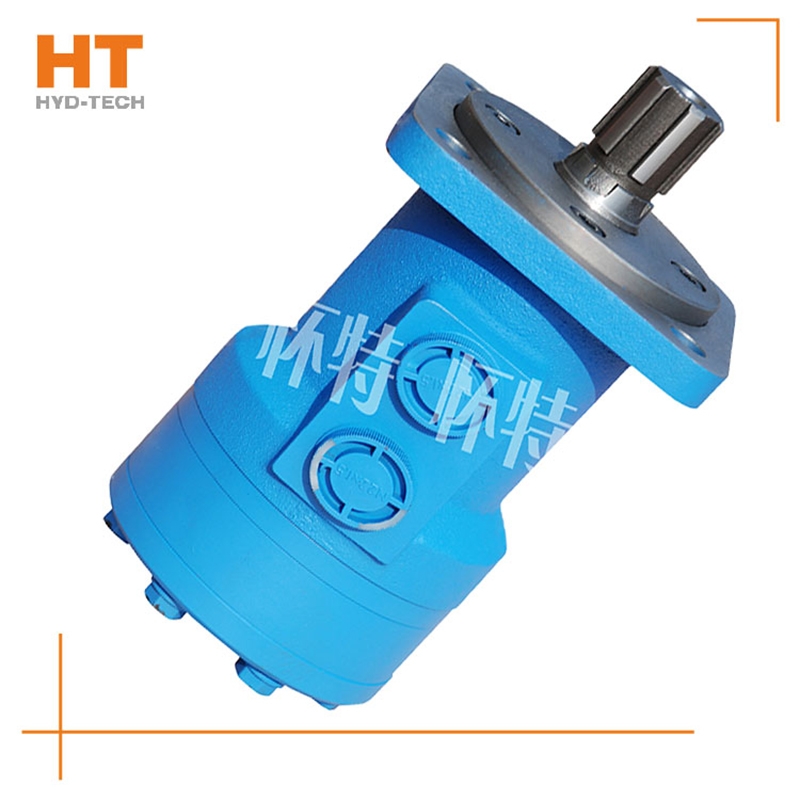
What is the oil supply mode of the hydraulic pump? The straight shaft swashplate plunger pump can be divided into two types: self suction type and pressurized type. Most high-pressure oil supply hydraulic pumps use pneumatic oil tank, and some hydraulic pumps are also equipped with oil make-up slave pump to deliver pressure oil to the oil inlet of the hydraulic pump. The self-priming pump has the characteristics of strong self-priming ability and no need for external oil supply special-purpose Low speed high torque cycloidal hydraulic motor 。 Bearings for hydraulic pumps. The most important part of the plunger pump is the bearing. If the bearing has clearance, the normal clearance of the three pairs of friction pairs inside the hydraulic pump cannot be guaranteed. At the same time, the hydrostatic support oil film thickness of each friction pair will be damaged, thus reducing the service life of the plunger pump bearing. According to the data provided by the manufacturer of the hydraulic pump, the average service life of the bearing is 10000 hours. If this value is exceeded, a new port shall be replaced. 3、 Conclusion. The service life of the piston pump is related to the maintenance at ordinary times, the quantity and quality of the hydraulic oil, and the cleanliness of the oil. At the same time, avoid Low speed high torque cycloidal hydraulic motor Manufacturer The particles in the oil will wear the friction pair of the plunger pump, which is also an effective method to extend its service life.
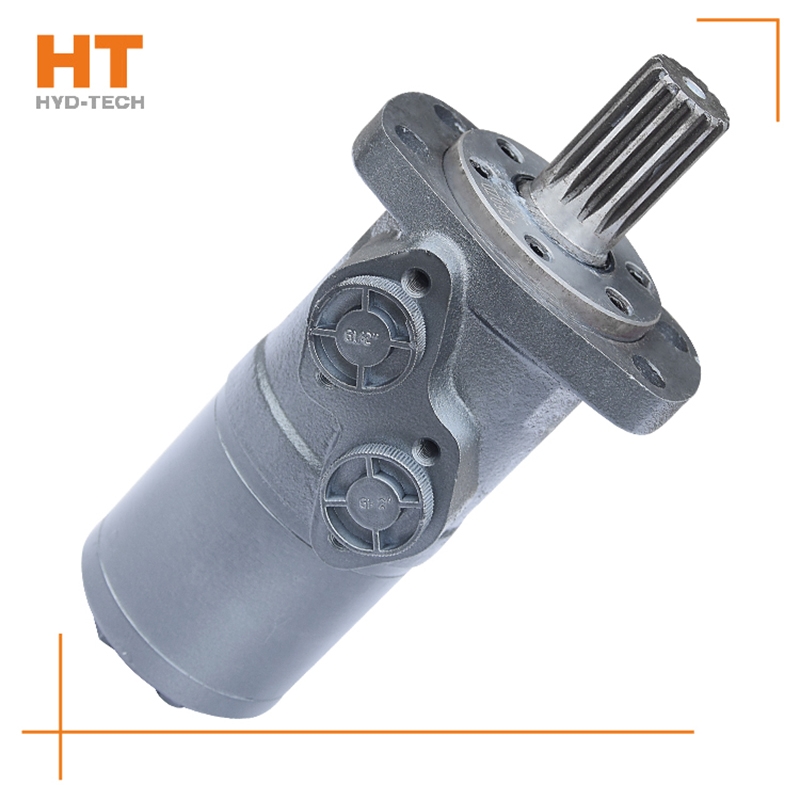
Most of its hydraulic system uses working medium, such as hydraulic oil with continuous fluidity, which converts the mechanical energy of the prime mover driving the pump into the pressure energy of the liquid through the hydraulic pump, and sends it to the actuator (hydraulic cylinder, hydraulic motor or swing hydraulic motor) through various control valves, such as pressure, flow, direction, etc., to convert it into mechanical energy to drive the load. This hydraulic system is generally composed of the following parts: power source, actuator, control valve, hydraulic auxiliary device and hydraulic working medium, which play their respective roles: power source: prime mover (motor or internal combustion engine) and hydraulic pump, whose role is to convert the mechanical energy generated by the prime mover into the pressure energy of liquid, and output oil with a certain pressure;