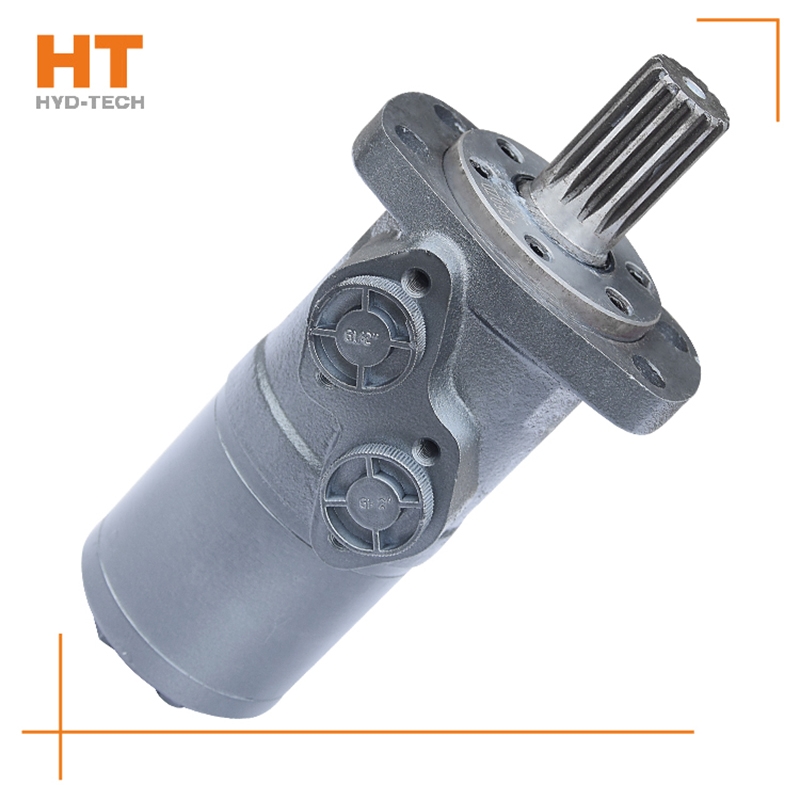
The device that can be converted into rotary motion is called motor. The hydraulic motor is a device that can convert the pressure energy of liquid medium into rotary motion. It converts the hydraulic energy provided by the hydraulic pump into mechanical energy. At the same power output, the weight and size of the hydraulic motor is only 5% - 20% of that of the DC motor, and the relative weight is very light, so the moment of inertia is small, the starting, braking and reversing are fast, the low speed stability is good, and the inorganic speed regulation can be easily realized. how customized Hydraulic cycloid motor Select the hydraulic motor suitable for yourself: the main parameters of the hydraulic motor include pressure, flow, displacement and output power; The choice of the ideal hydraulic motor mainly depends on your desired power and Huai'an manufactor The hydraulic pump you are using now matches. You can also see the selection of displacement. The displacement V is obtained by dividing the system flow Q by the required motor speed n. Select the model according to the displacement and check the prototype to see whether the motor torque meets the requirements.
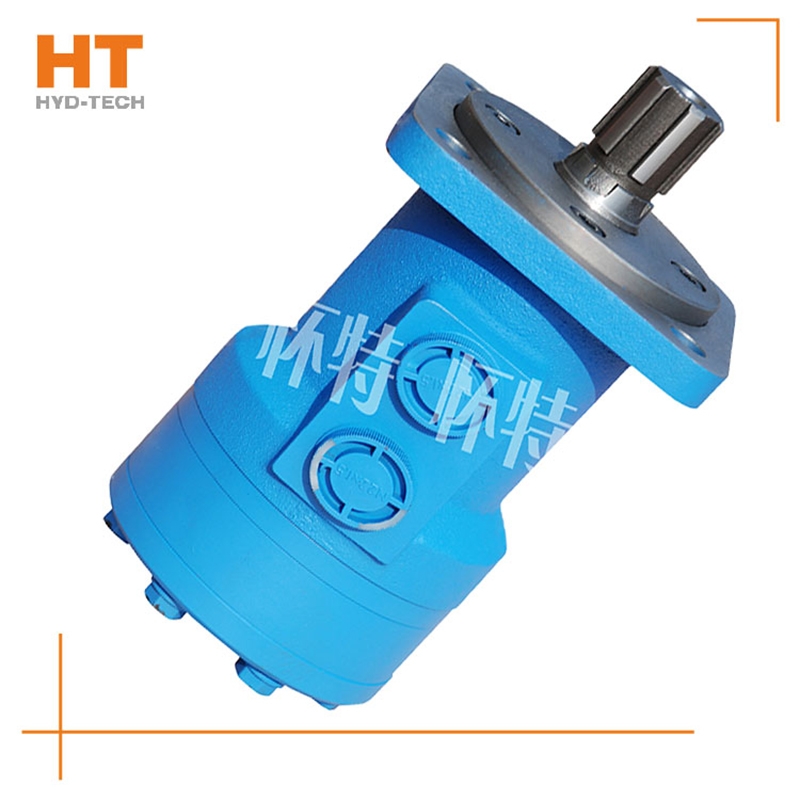
(1) Oil leakage at the shaft end: because the oil seal and output shaft are under constant friction during the use of the hydraulic motor, the wear of the contact surface between the oil seal and the shaft will be caused Huai'an Hydraulic cycloid motor A certain limit will make the oil seal lose its sealing effect, and oil will leak. Our solution is very simple: replace the oil seal. If the output shaft is seriously worn, it must be replaced. (2) Crevice oil leakage: the "O" ring between the motor housing and the front side plate, or between the front side plate and the stator body, is aged Hydraulic cycloid motor manufactor Just replace the "O" ring. (3) Oil leakage at the cover: the "O" ring under the cover is aged and loses its sealing effect. The probability of this situation is very low, even if it happens, just replace the "O" ring.
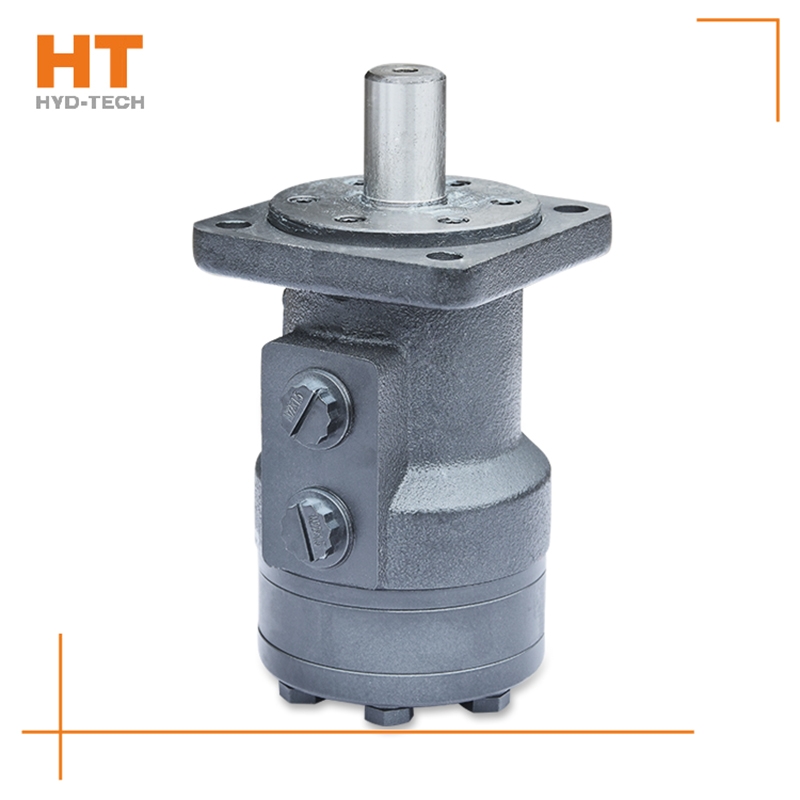
1. Generally, the motor shall be able to run forward and backward. Therefore, the hydraulic motor is usually required to have structural symmetry in the design. 2. The actual working pressure difference of the hydraulic motor depends on the load torque. When the moment of inertia of the driven load is large and the speed is high, rapid braking or reverse rotation is required, high hydraulic impact will be generated. Therefore, the system should be equipped with necessary safety valves and buffer valves. 3. Under normal working conditions, the inlet and outlet pressure of the hydraulic motor is higher than the atmospheric pressure, so there is no suction performance problem like the hydraulic pump. However, if the hydraulic motor can work under pump conditions, its oil inlet should have a minimum pressure limit to avoid cavitation. 4. Some hydraulic motors must have sufficient back pressure at the oil return port to ensure normal operation. The higher the speed, the greater the back pressure, which indicates that the utilization rate of oil source pressure is not high and the system loss is increased. 5. Because the internal leakage of the motor is inevitable, there will be slow sliding when the hydraulic motor oil outlet is closed for braking. Therefore, when long-term accurate braking is required, a separate anti-skid brake shall be set.
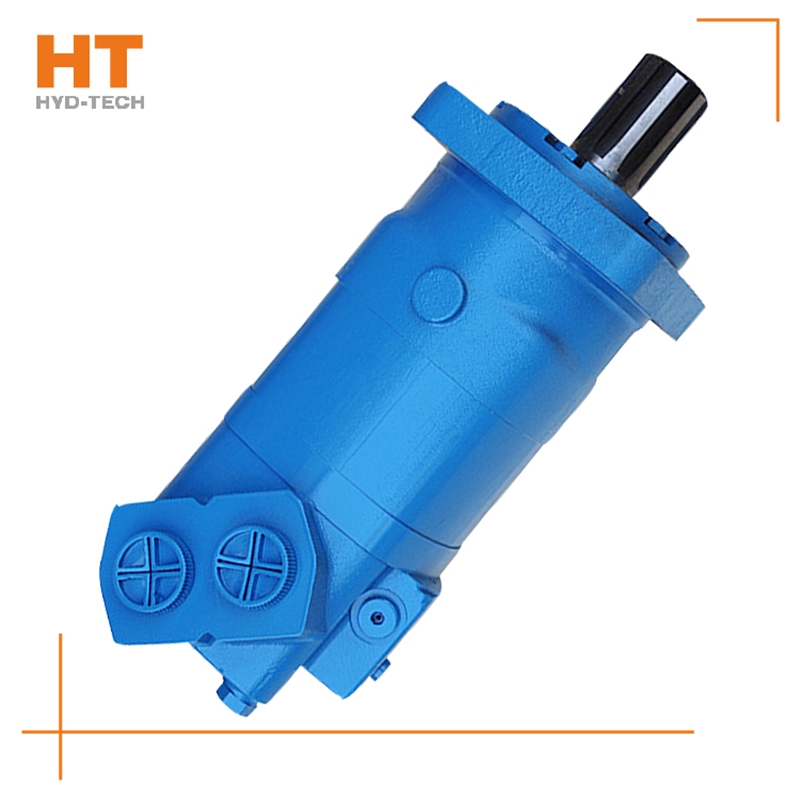
Along the revolution direction of the rotor, the volume of the tooth cavity at the front side of the connection between the rotor and the stator becomes smaller, which is an oil discharge cavity, and the volume at the rear side becomes larger. When the connecting line passes through the two tooth roots of the rotor, the oil inlet ends and the largest tooth cavity appears. When the connecting line passes through the two tooth tops of the rotor, the oil drainage ends and the smallest tooth cavity appears. In order to ensure the continuous rotation of the rotor, it is necessary to have the same regular oil distribution mechanism to cooperate with it, so that the tooth cavity at the front side of the connecting pipeline is always connected with the oil drain port, and the rear side is connected with the oil inlet port. As mentioned above, the oil distribution mechanism consists of a housing and an oil distribution sleeve. The 12 longitudinal grooves (x) on the oil distribution sleeve and the 12 intervals formed by the oil distribution groove face the root and top of the rotor through the positioning device, which proves that when the largest and smallest cavities occur, the oil distribution hole of the housing can be closed, thus separating the oil inlet groove and oil outlet groove of the oil distribution sleeve.