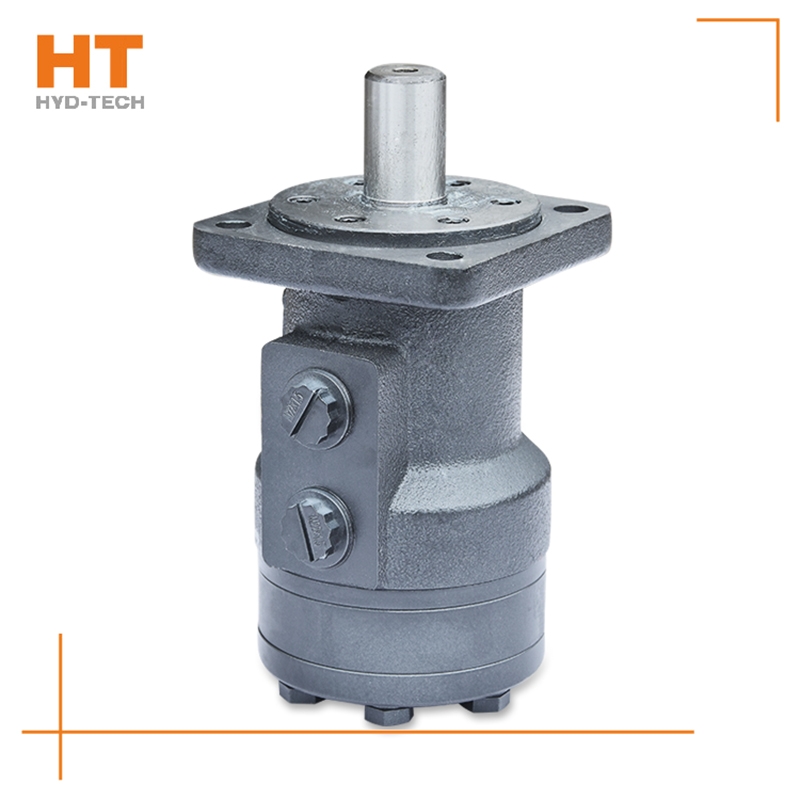
In the middle opening system, the main reversing valve of the middle opening system is in the middle position, through which the hydraulic pump is unloaded, and the liquid returns to the oil tank under low pressure. This kind of system generally uses constant displacement pump as oil source; When the reversing valve is in the middle position, the energy transmission starts with a low value that is basically zero, and the energy rises after changing, so that the pressure liquid enters customized BM cycloid motor The actuator acts on the load; When the reversing valve is in the middle position, the internal leakage is very small. Generally, when the same function is achieved, the energy consumption of the intermediate open circuit is smaller. in Urumqi customized Open system is mostly used for working conditions requiring intermittent movement or supporting load, such as prime movers that do not want to start and stop frequently. The system has high efficiency, and needs to use makeup oil pump and flushing valve for oil makeup and heat exchange.
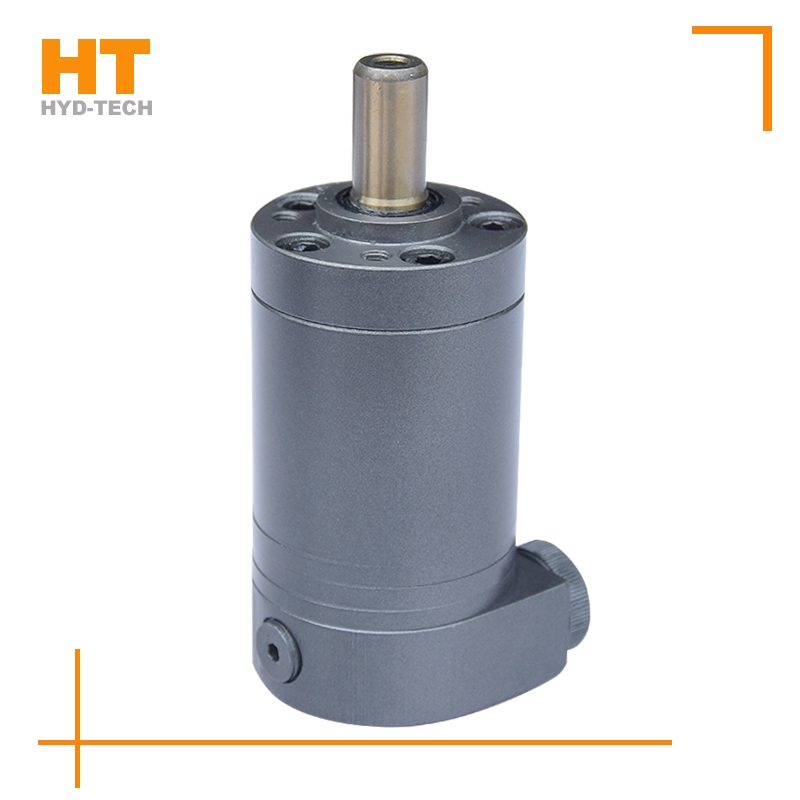
The hydraulic motor manufacturer explains to you the reasons for the poor performance of the hydraulic motor: 1. First of all, according to the analysis of the causes of the wear of the port plate, the main reasons for the weakness of the hydraulic motor are: because the port plate is worn, the oil inlet channel and the oil return channel are connected at the port plate, part of the high-pressure oil leaks, the oil pressure flowing through the stator and rotor pair decreases, and the flow decreases, Eventually, the output speed and torque of the motor will decrease. 2. Due to the wear of the valve plate, its relative position in the valve body has changed BM cycloid motor manufactor The preload and adhesion of the spring on the valve body between the valve plates will be reduced, which will intensify the leakage of hydraulic oil and lead to the decline of the performance of the hydraulic motor. 3. With the increase of hydraulic oil temperature, its comprehensive performance declines, driving the cycloidal rotor to rotate Urumqi manufactor The ability to move is further reduced. Upon inspection, there is no obvious wear on the joint surface of the stator and rotor pair and the bearing seat and valve disc matched with both sides of the stator and rotor pair. The movement is normal without jamming, which will not cause performance degradation.
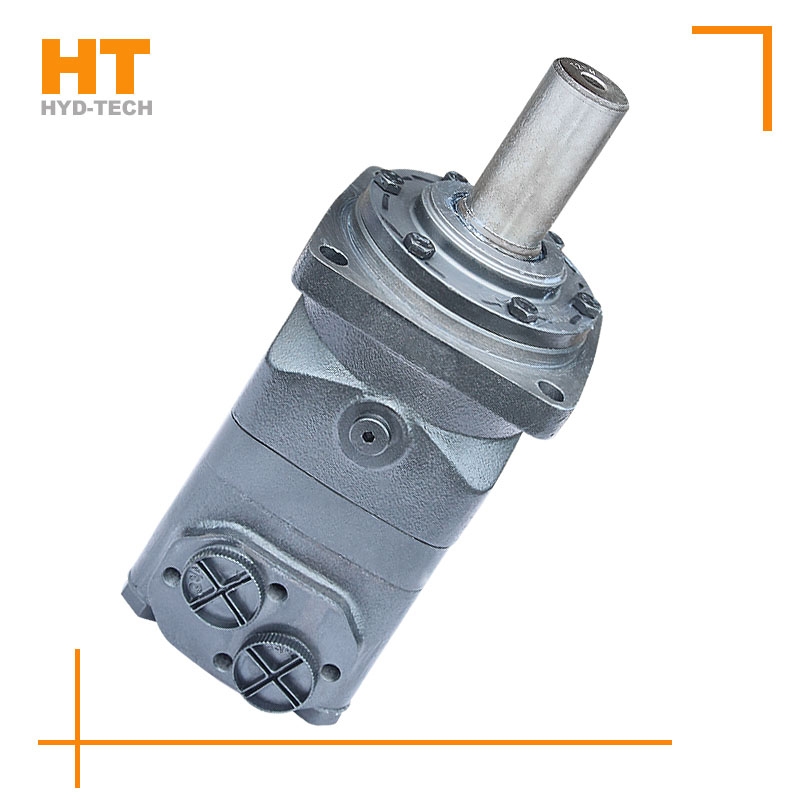
The device that can be converted into rotary motion is called motor. The hydraulic motor is a device that can convert the pressure energy of liquid medium into rotary motion. It converts the hydraulic energy provided by the hydraulic pump into mechanical energy. At the same power output, the weight and size of the hydraulic motor is only 5% - 20% of that of the DC motor, and the relative weight is very light, so the moment of inertia is small, the starting, braking and reversing are fast, the low speed stability is good, and the inorganic speed regulation can be easily realized. how customized BM cycloid motor Select the hydraulic motor suitable for yourself: the main parameters of the hydraulic motor include pressure, flow, displacement and output power; The choice of the ideal hydraulic motor mainly depends on your desired power and Urumqi manufactor The hydraulic pump you are using now matches. You can also see the selection of displacement. The displacement V is obtained by dividing the system flow Q by the required motor speed n. Select the model according to the displacement and check the prototype to see whether the motor torque meets the requirements.
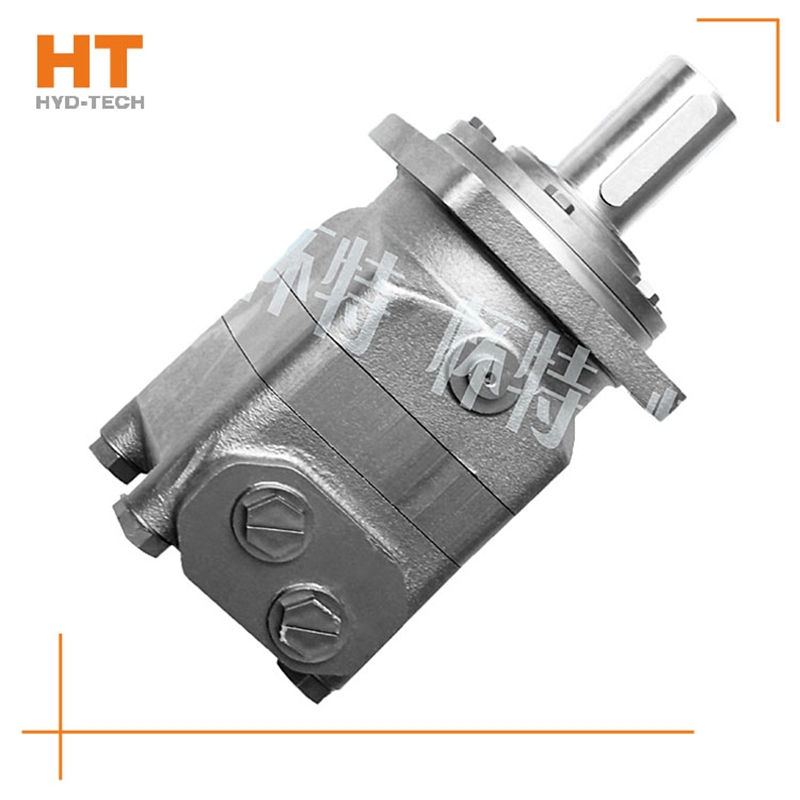
1. Generally, the motor shall be able to run forward and backward. Therefore, the hydraulic motor is usually required to have structural symmetry in the design. 2. The actual working pressure difference of the hydraulic motor depends on the load torque. When the moment of inertia of the driven load is large and the speed is high, rapid braking or reverse rotation is required, high hydraulic impact will be generated. Therefore, the system should be equipped with necessary safety valves and buffer valves. 3. Under normal working conditions, the inlet and outlet pressure of the hydraulic motor is higher than the atmospheric pressure, so there is no suction performance problem like the hydraulic pump. However, if the hydraulic motor can work under pump conditions, its oil inlet should have a minimum pressure limit to avoid cavitation. 4. Some hydraulic motors must have sufficient back pressure at the oil return port to ensure normal operation. The higher the speed, the greater the back pressure, which indicates that the utilization rate of oil source pressure is not high and the system loss is increased. 5. Because the internal leakage of the motor is inevitable, there will be slow sliding when the hydraulic motor oil outlet is closed for braking. Therefore, when long-term accurate braking is required, a separate anti-skid brake shall be set.