Cycloidal hydraulic motor, as a kind of construction machinery equipment with small price increase and light weight, is also widely used in daily life. Cycloidal hydraulic motor is a kind of motor, which is essential for some equipment. In fact, the operation of all hydraulic systems is almost the same. This cycloidal hydraulic motor is widely used Anqing want to buy It is used in construction, manufacturing, mining and other industries, so pay attention to daily maintenance when using the motor to ensure the service life of the cycloidal hydraulic motor. In order to keep the whole system in a stable state, it is necessary to ensure that the motor function has a constant pressure, ensure that the hydraulic system is normal, and ensure that the pressure in the system is not orbit motor Price leak.
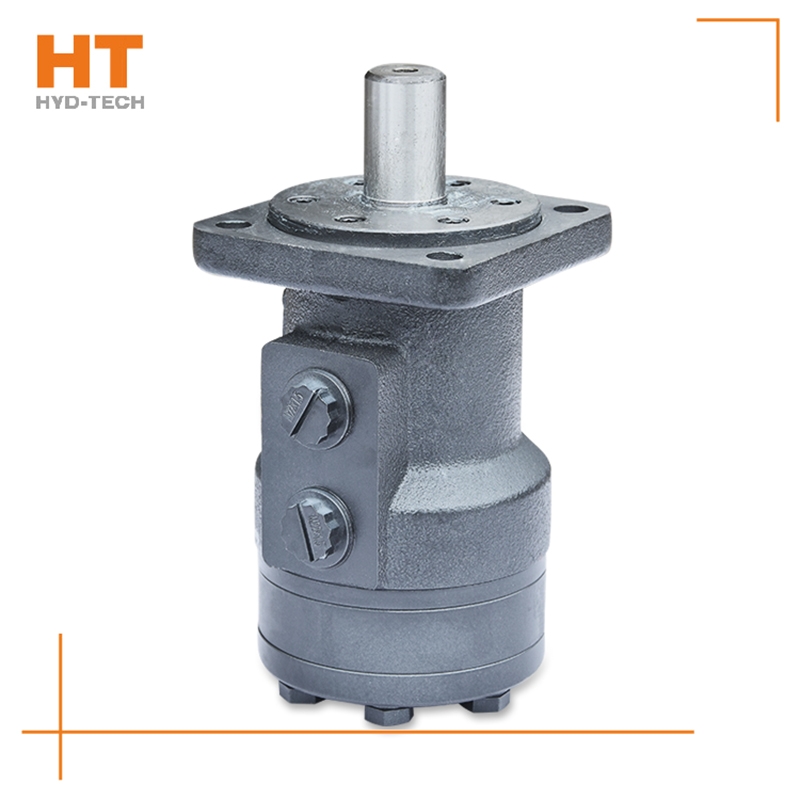
1. Generally, the motor shall be able to run forward and backward. Therefore, the hydraulic motor is usually required to have structural symmetry in the design. 2. The actual working pressure difference of the hydraulic motor depends on the load torque. When the moment of inertia of the driven load is large and the speed is high, rapid braking or reverse rotation is required, high hydraulic impact will be generated. Therefore, the system should be equipped with necessary safety valves and buffer valves. 3. Under normal working conditions, the inlet and outlet pressure of the hydraulic motor is higher than the atmospheric pressure, so there is no suction performance problem like the hydraulic pump. However, if the hydraulic motor can work under pump conditions, its oil inlet should have a minimum pressure limit to avoid cavitation. 4. Some hydraulic motors must have sufficient back pressure at the oil return port to ensure normal operation. The higher the speed, the greater the back pressure, which indicates that the utilization rate of oil source pressure is not high and the system loss is increased. 5. Because the internal leakage of the motor is inevitable, there will be slow sliding when the hydraulic motor oil outlet is closed for braking. Therefore, when long-term accurate braking is required, a separate anti-skid brake shall be set.
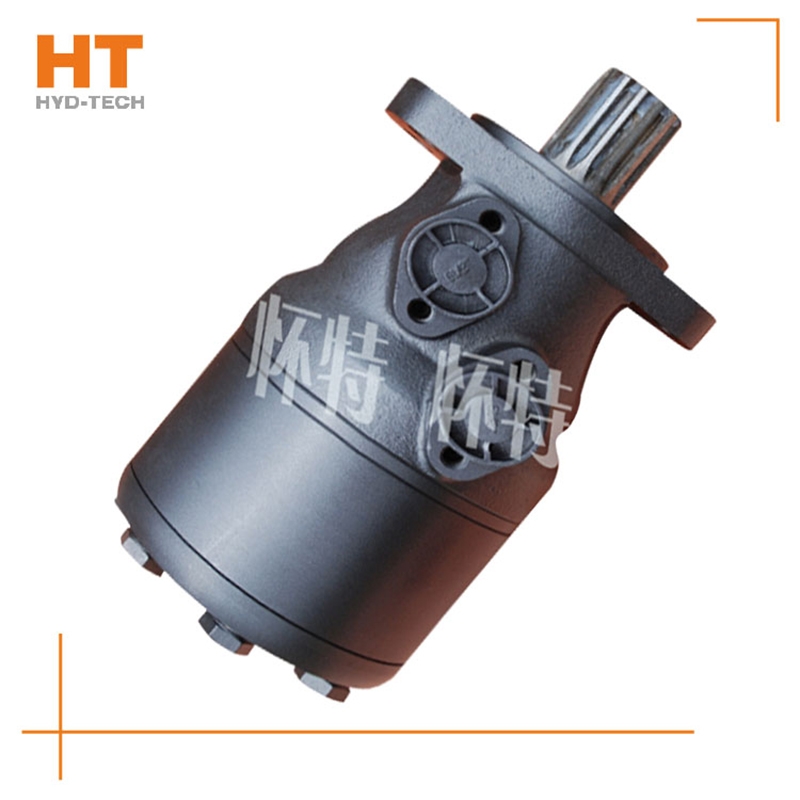
The output pressure of the hydraulic motor also depends on the load. Rated pressure Pn: the rated pressure refers to the working pressure that the hydraulic motor can withstand during continuous operation. It can want to buy orbit motor To ensure the volumetric efficiency and service life of the hydraulic motor. Working pressure P: the working pressure is the actual pressure of oil input when the hydraulic motor is working orbit motor Price power. Its value depends on the size of the load. However, the maximum working pressure is determined by the safety valve in the hydraulic system. The throttle adjustment value must not exceed the maximum pressure value of the hydraulic motor. The third is the maximum pressure: the limit pressure that the motor is allowed to overload in a short time. Pn ≤ Pmax value.
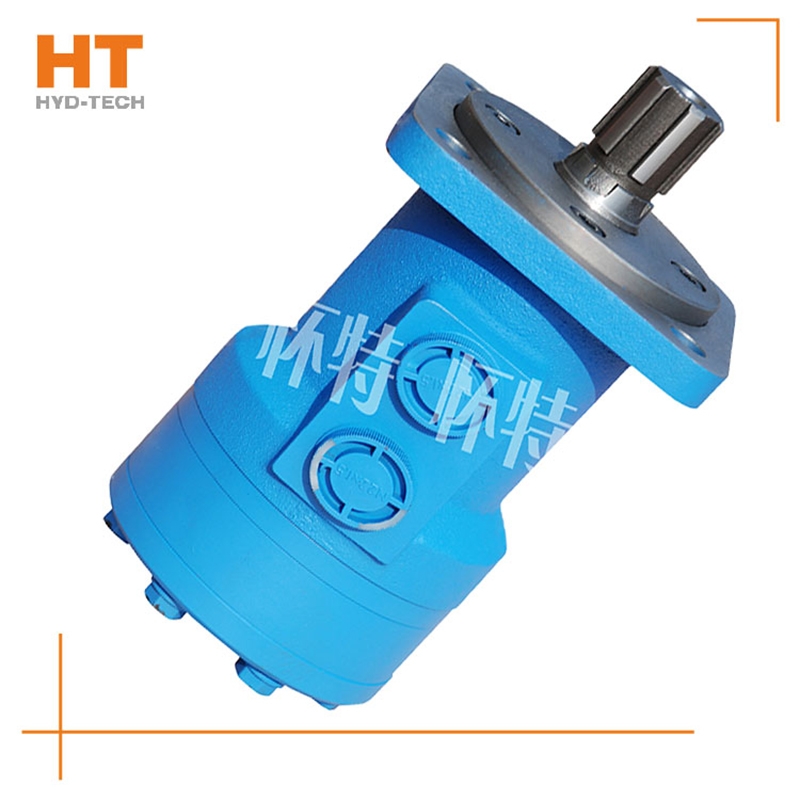
At present, in the hydraulic system of construction machinery, the commonly used oil change method is by cycle or by train number. The hydraulic system of some construction machinery requires that the hydraulic oil be replaced when the motorcycle is 1200. surface want to buy orbit motor Grid 6 has reference value. For the maintenance of the hydraulic system, the parameters in Table 7 of the used hydraulic oil can better explain the problem. If the three items in Table 7 generally exceed the limit, the hydraulic oil shall be replaced. Except that the solid particles exceed the limit, that is, the hydraulic oil shall be replaced if the solid particles exceed the limit. During field inspection of oil, empirical inspection shall be carried out first, and whether to continue quantitative inspection shall be determined according to the observed oil pollution. According to the test results, determine the solution orbit motor Price What measures shall be taken for oil pressure (half oil change, full oil change or filtration). Thus, the quality of hydraulic oil in the hydraulic system can be guaranteed, so as to reduce system failures and improve the reliability of the system.