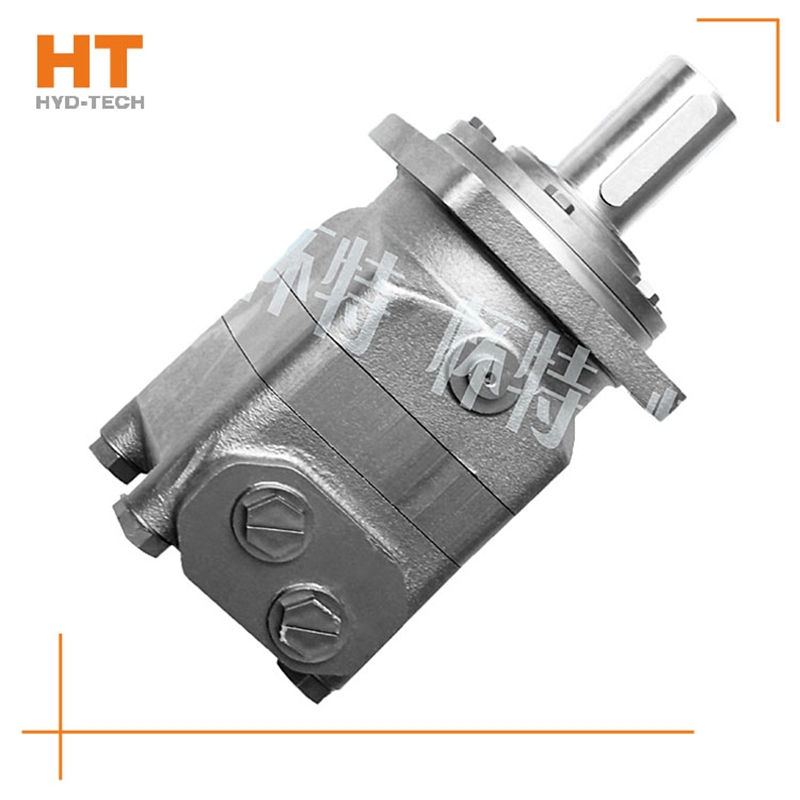
1. Generally, the motor shall be able to run forward and backward. Therefore, the hydraulic motor is usually required to have structural symmetry in the design. 2. The actual working pressure difference of the hydraulic motor depends on the load torque. When the moment of inertia of the driven load is large and the speed is high, rapid braking or reverse rotation is required, high hydraulic impact will be generated. Therefore, the system should be equipped with necessary safety valves and buffer valves. 3. Under normal working conditions, the inlet and outlet pressure of the hydraulic motor is higher than the atmospheric pressure, so there is no suction performance problem like the hydraulic pump. However, if the hydraulic motor can work under pump conditions, its oil inlet should have a minimum pressure limit to avoid cavitation. 4. Some hydraulic motors must have sufficient back pressure at the oil return port to ensure normal operation. The higher the speed, the greater the back pressure, which indicates that the utilization rate of oil source pressure is not high and the system loss is increased. 5. Because the internal leakage of the motor is inevitable, there will be slow sliding when the hydraulic motor oil outlet is closed for braking. Therefore, when long-term accurate braking is required, a separate anti-skid brake shall be set.
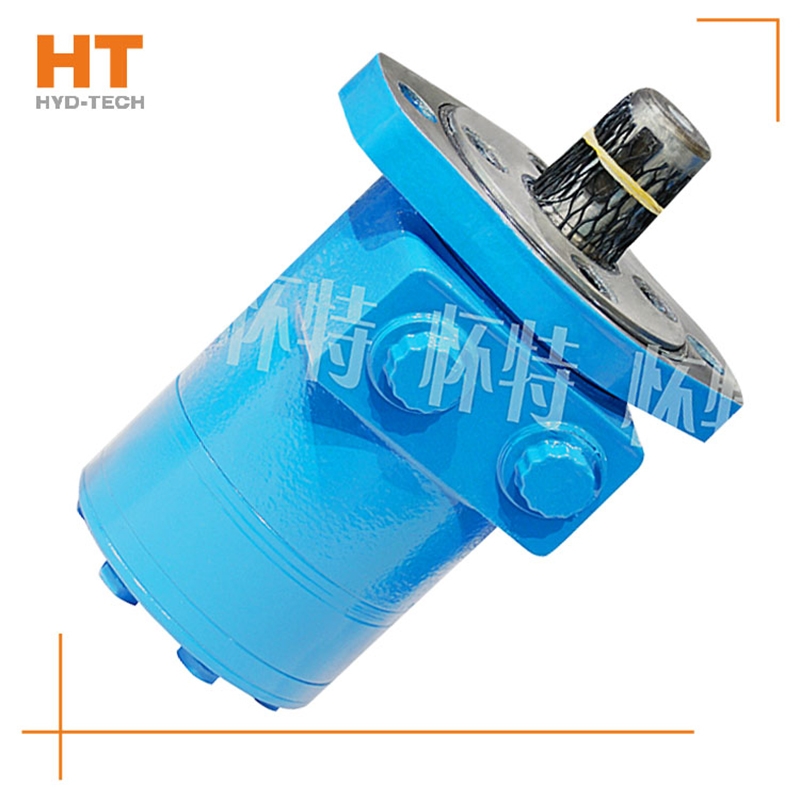
Most of its hydraulic system uses working medium, such as hydraulic oil with continuous fluidity, which converts the mechanical energy of the prime mover driving the pump into the pressure energy of the liquid through the hydraulic pump, and sends it to the actuator (hydraulic cylinder, hydraulic motor or swing hydraulic motor) through various control valves, such as pressure, flow, direction, etc., to convert it into mechanical energy to drive the load. This hydraulic system is generally composed of the following parts: power source, actuator, control valve, hydraulic auxiliary device and hydraulic working medium, which play their respective roles: power source: prime mover (motor or internal combustion engine) and hydraulic pump, whose role is to convert the mechanical energy generated by the prime mover into the pressure energy of liquid, and output oil with a certain pressure;
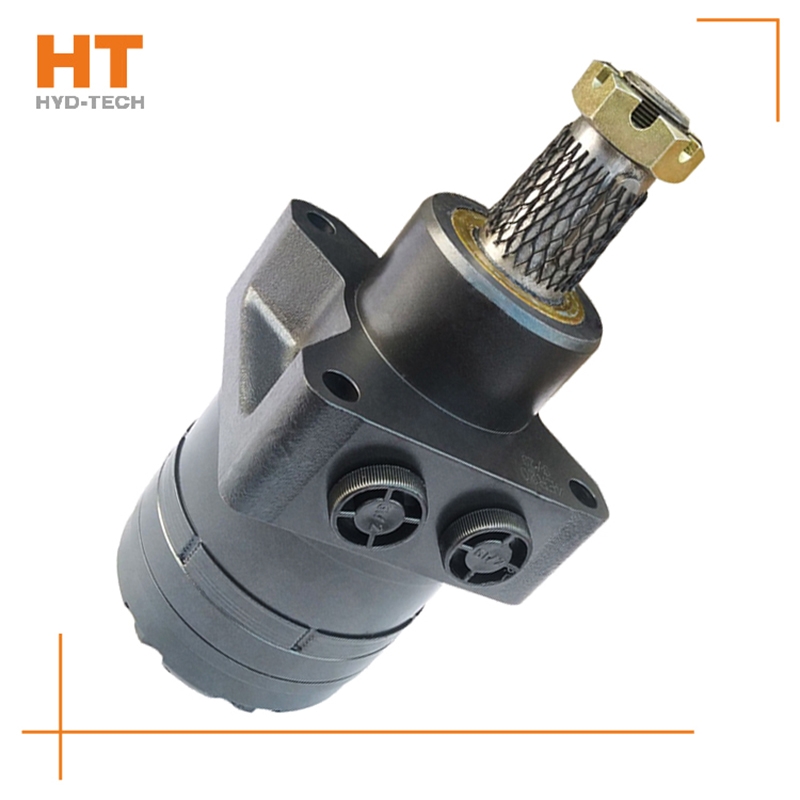
If the hydraulic system is compared to the human body, then the hydraulic oil is equal to human blood. In the hydraulic system, the hydraulic oil plays a role in energy transmission, system lubrication, and prevention Qinghai High torque cycloidal hydraulic motor The functions of corrosion, rust prevention and cooling, and whether the hydraulic system can work effectively are closely related to the type and selection of hydraulic oil. Coding, composition and characteristics of hydraulic system: high purity general machine tool oil, refined mineral lubricating oil, with good rust resistance and oxidation resistance. High wear resistant hydraulic oil, refined mineral lubricating oil, rust proof, anti-oxidation, anti-wear. High temperature and high pressure hydraulic oil, with the characteristics of rust prevention, oxidation resistance, wear resistance, etc., is refined into mining lubricating oil, and added with viscosifier. Refined mining lubricating oil HG hydraulic guide oil, rust proof, anti-oxidation, anti-wear, anti stick slip. HS synthesis special-purpose High torque cycloidal hydraulic motor Hydrocarbon is a kind of low temperature hydraulic oil, which has the characteristics of anti-oxidation and anti-wear.
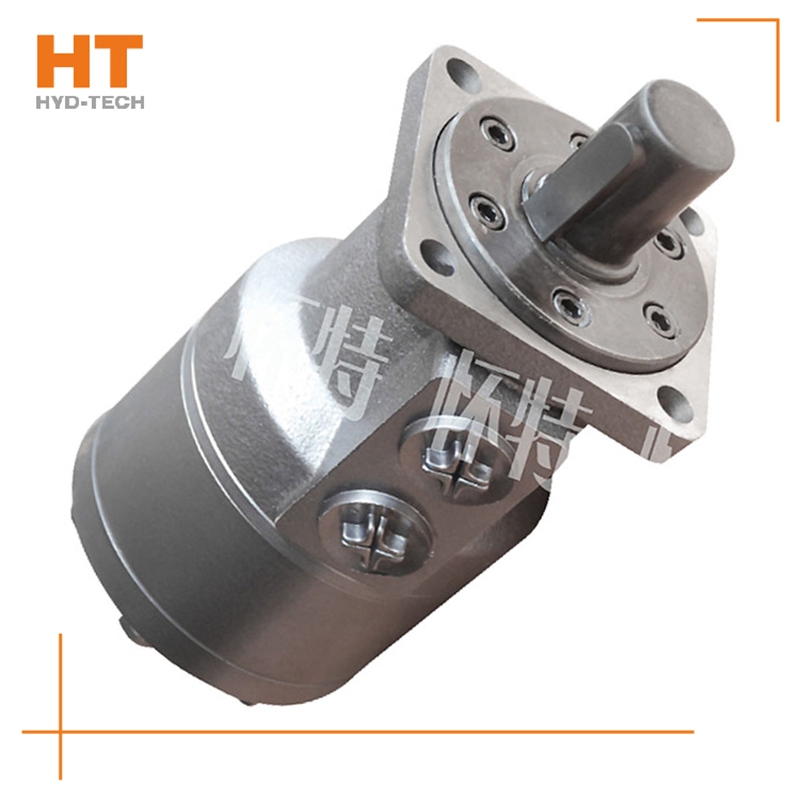
The hydraulic motor manufacturer explains to you the reasons for the poor performance of the hydraulic motor: 1. First of all, according to the analysis of the causes of the wear of the port plate, the main reasons for the weakness of the hydraulic motor are: because the port plate is worn, the oil inlet channel and the oil return channel are connected at the port plate, part of the high-pressure oil leaks, the oil pressure flowing through the stator and rotor pair decreases, and the flow decreases, Eventually, the output speed and torque of the motor will decrease. 2. Due to the wear of the valve plate, its relative position in the valve body has changed High torque cycloidal hydraulic motor Price The preload and adhesion of the spring on the valve body between the valve plates will be reduced, which will intensify the leakage of hydraulic oil and lead to the decline of the performance of the hydraulic motor. 3. With the increase of hydraulic oil temperature, its comprehensive performance declines, driving the cycloidal rotor to rotate Qinghai Price The ability to move is further reduced. Upon inspection, there is no obvious wear on the joint surface of the stator and rotor pair and the bearing seat and valve disc matched with both sides of the stator and rotor pair. The movement is normal without jamming, which will not cause performance degradation.
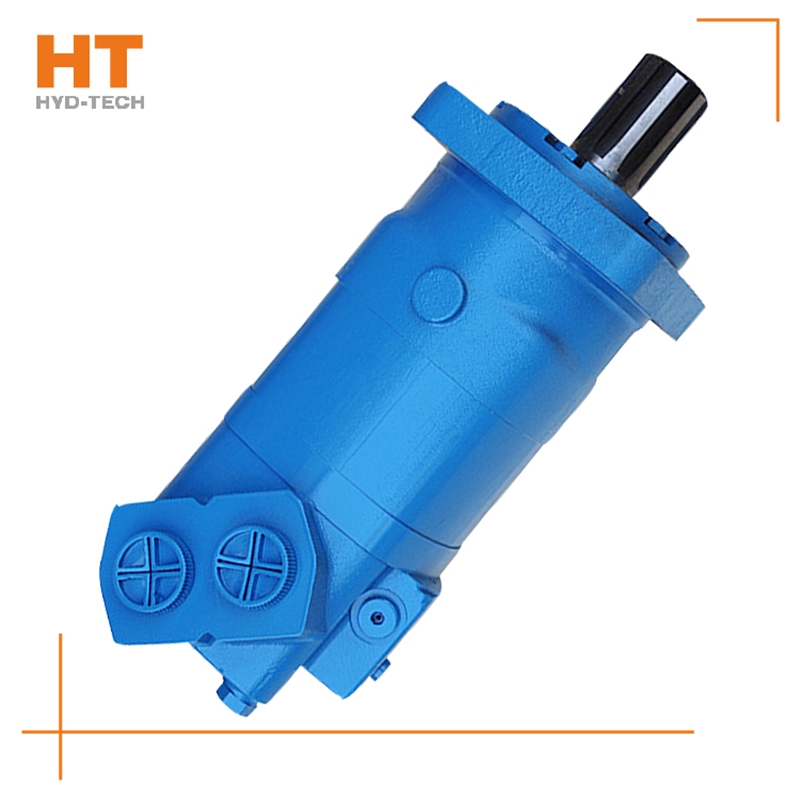
When the main reversing valve of the central closing system and the central closing system is in the neutral position, all oil ports of the reversing valve are closed. If a fixed pump is used for oil supply, the liquid of the hydraulic pump will return to the tank at high pressure through the overflow valve. When the reversing valve is in neutral position, energy transmission starts from the high value, that is, the maximum pressure regulating value of the system. Just reverse High torque cycloidal hydraulic motor Price , its energy can be used by the actuator. When the reversing valve is in the middle position, it sometimes bears all the pressure of the system, so the internal leakage is greater than that of the open system. Generally, when the Qinghai High torque cycloidal hydraulic motor In this case, the energy consumption of the closed loop is high, but if the intermediate unloading measures are added or the pressure compensated variable pump is used for oil supply, the energy consumption of the closed loop can be greatly reduced. Closed hydraulic systems are used for a variety of equipment.
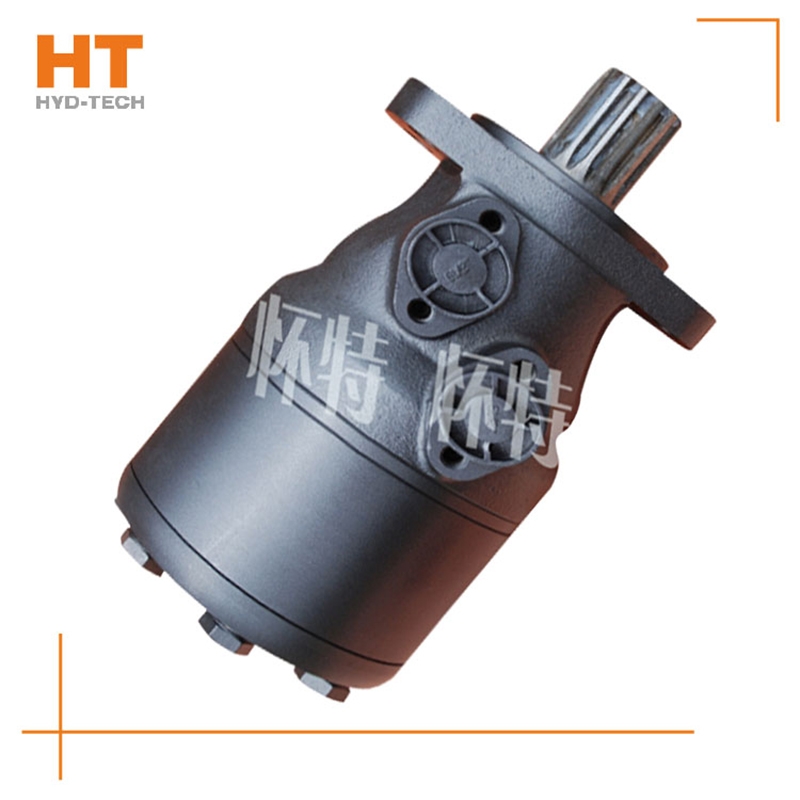
The oil distribution sleeve is synchronized with the rotor, so that the rotor rotates once, and the seven oil distribution holes on the housing are closed 840 times by the twelve diaphragms of the oil distribution sleeve, while the rotor and stator form the largest and smallest closed cavities respectively 1420 times, collectively referred to as the seal cavity. In the circle of the oil distribution hole of the closed housing, the oil inlet and outlet of the rotor have three chambers respectively, one Qinghai High torque cycloidal hydraulic motor The cavity is closed. When the rotor is transferred from the smallest enclosed cavity to the next largest enclosed cavity, before the rotor is transferred from the largest enclosed cavity to the next smallest enclosed cavity, oil is supplied to four cavities and three cavities special-purpose High torque cycloidal hydraulic motor Drain the oil.