The hydraulic motor is usually put into operation Foshan customized Clean before use. The purpose of cleaning is to remove the pollutants, metal chips, fiber compounds and iron cores left in Madai. In the first two hours of operation, even if the motor is not completely damaged, there will be a series of failures. Therefore, the hydraulic motor oil circuit should be cleaned as follows: 1. Clean the oil tank with easy drying cleaning solvent, and then remove the solvent residue with filtered air. 2. Clean all pipes of hydraulic motor. In some cases, it may be necessary to impregnate pipes and joints. 3. Install an oil filter on the pipeline to protect the oil supply pipeline and pressure pipeline of the valve. four customized Micro cycloid motor Install a flushing plate on the collector to replace precision valves, such as electro-hydraulic servo valve. 5. Check whether all pipes are of proper size and connected correctly.
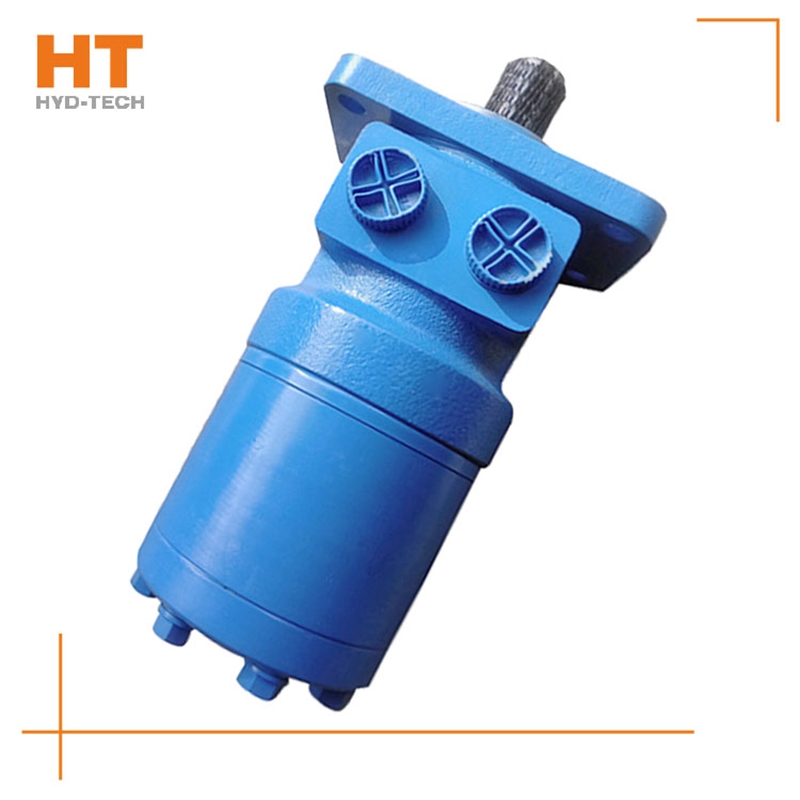
When the high-pressure oil enters the oil distribution shaft and enters each plunger cylinder hole of the working section through the oil distribution window, the corresponding plunger set is pushed against the curved surface of the cam ring L (housing), Foshan Micro cycloid motor The cam ring surface gives a reaction force to the plunger at the contact position. This reaction force N acts on the common plane where the cam ring surface contacts the roller. This normal reaction force N can be decomposed into radial force PH and circumferential force T, which are balanced with the hydraulic pressure at the bottom of the plunger, while the circumferential force T overcomes the load torque, customized Micro cycloid motor Drive cylinder 2 to rotate. Under this working condition, the cam ring and oil distribution shaft do not rotate. At this time, the plunger corresponding to the oil return section of the cam gear moves in the opposite direction, and the oil is discharged through the oil distribution shaft.
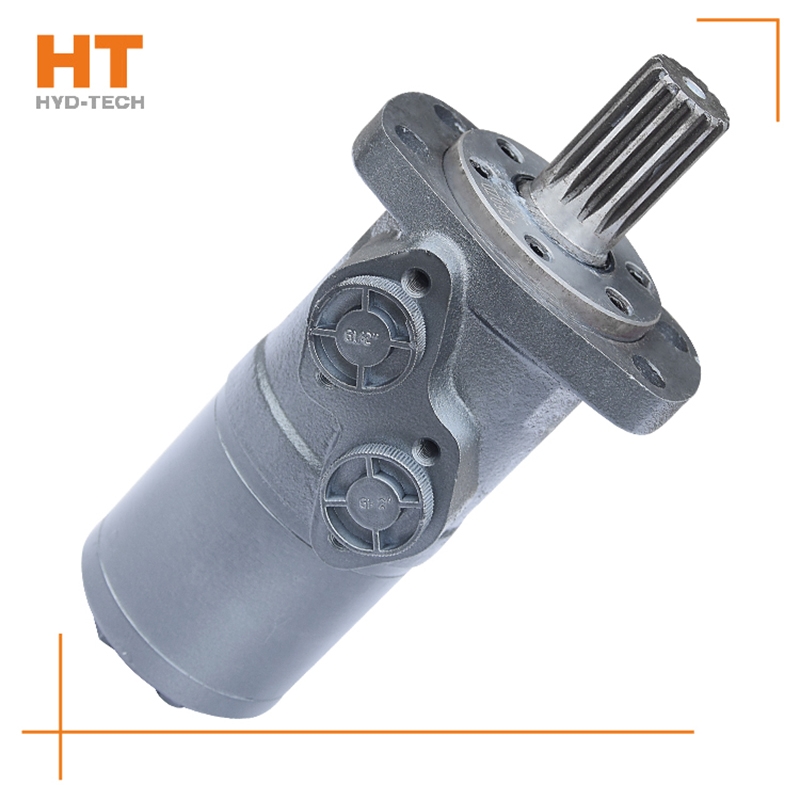
1. Air intrusion. When the air intrudes into the hydraulic system, it has a large volume in the low-pressure area. When it enters the high-pressure area, it is compressed, and the volume suddenly decreases. When it enters the low-pressure area, the volume suddenly increases, resulting in a sudden change in the bubble volume, that is, "explosion" phenomenon, resulting in noise. Solution: Generally, the hydraulic cylinder is equipped with an exhaust device customized Micro cycloid motor Exhaust. In addition, a common method is to exhaust the actuator several times during the fast full stroke after startup. 2. The quality of the hydraulic pump or motor is poor. The quality of the hydraulic pump is poor, the accuracy does not fully meet the technical requirements, the pressure and flow fluctuations are large, the oil trapping phenomenon has not been eliminated well, and poor sealing and poor bearing quality are the main reasons for the noise. In use, due to wear of hydraulic pump parts, excessive clearance, insufficient flow Foshan manufactor The force is easy to fluctuate and will also produce noise.
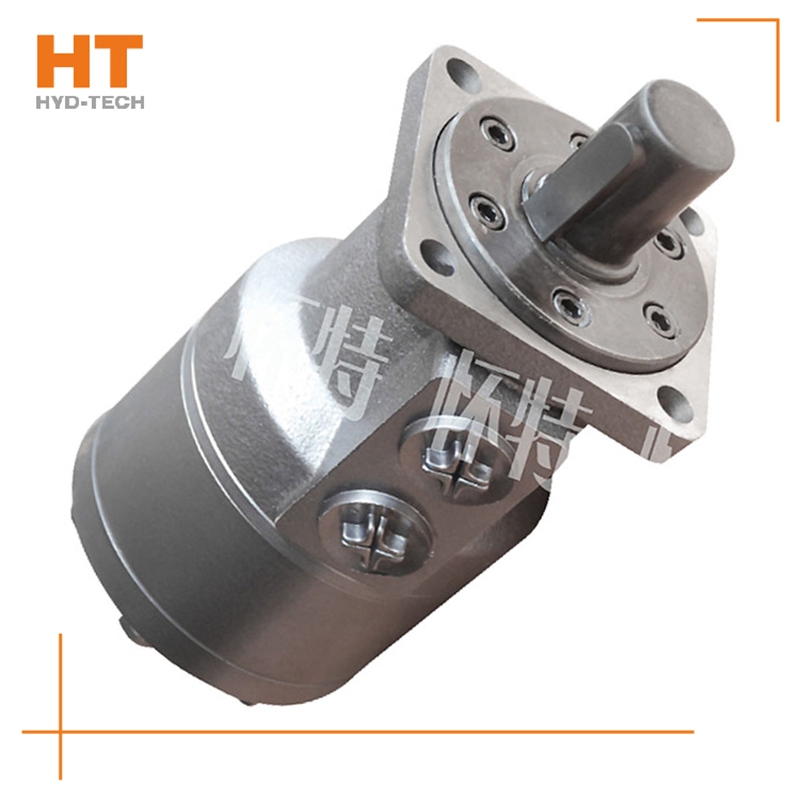
Causes: 1. The pump is damaged, and the pump body is overheated and produces noise. 2. The control valve is closed tightly or the oil supply and return system is blocked, and local overheating occurs. 3. The safety valve is opened, and the valve cries or hisses, and local overheating occurs. 4. The distribution rotary valve is excessively leaking, and the valve chamber is overheated, and it is very hot when touched by hand. 5. The hydraulic motor crankcase is excessively leaking, and the single oil drain pipe is leaking customized Micro cycloid motor Treatment method for excessive leakage and high oil level: 1. Check the condition of the ball joint 2. Check the sealing condition of the cylinder piston 3. Check the viscosity and operating temperature of the oil 4. Check the contact surface between the oil pan and the housing 5. Check the surface between the connecting rod and the eccentric wheel Micro cycloid motor manufactor 6. Check the wear of the oil pan and whether the two oil cavity channels at the inlet and outlet of the casting are connected
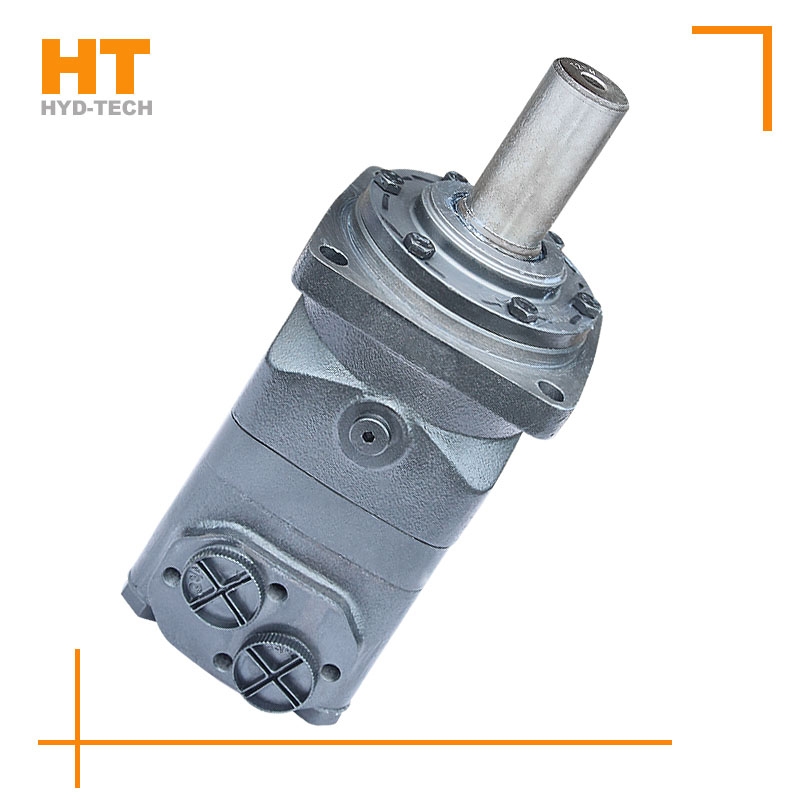
Precautions during operation of cycloidal hydraulic motor: before operation, check whether all parts of the hydraulic system are connected correctly, and inject oil into the specified Foshan Micro cycloid motor Height. Start and run without load for 10-15 minutes, and exhaust. Air bubbles in the oil tank, noise in the system, and gas accumulation in the engine oil cylinder all prove that there is air in the system. After the gas is discharged, fill the oil tank, and then gradually increase the load of the motor until the load is too large. Observe whether there is noise, oil rise, oil leakage and other abnormal phenomena. After 50 hours of operation, change the oil according to the maintenance rules, and then the oil according to the maintenance rules Foshan manufactor Replace. If there is no motor fault, do not disassemble it easily.
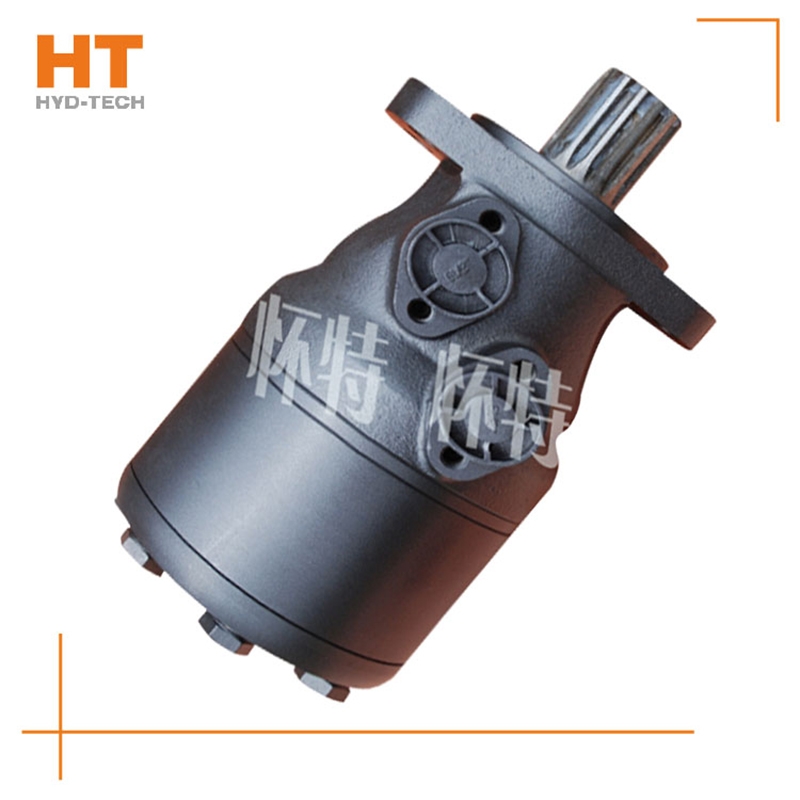
Along the revolution direction of the rotor, the volume of the tooth cavity at the front side of the connection between the rotor and the stator becomes smaller, which is an oil discharge cavity, and the volume at the rear side becomes larger. When the connecting line passes through the two tooth roots of the rotor, the oil inlet ends and the largest tooth cavity appears. When the connecting line passes through the two tooth tops of the rotor, the oil drainage ends and the smallest tooth cavity appears. In order to ensure the continuous rotation of the rotor, it is necessary to have the same regular oil distribution mechanism to cooperate with it, so that the tooth cavity at the front side of the connecting pipeline is always connected with the oil drain port, and the rear side is connected with the oil inlet port. As mentioned above, the oil distribution mechanism consists of a housing and an oil distribution sleeve. The 12 longitudinal grooves (x) on the oil distribution sleeve and the 12 intervals formed by the oil distribution groove face the root and top of the rotor through the positioning device, which proves that when the largest and smallest cavities occur, the oil distribution hole of the housing can be closed, thus separating the oil inlet groove and oil outlet groove of the oil distribution sleeve.