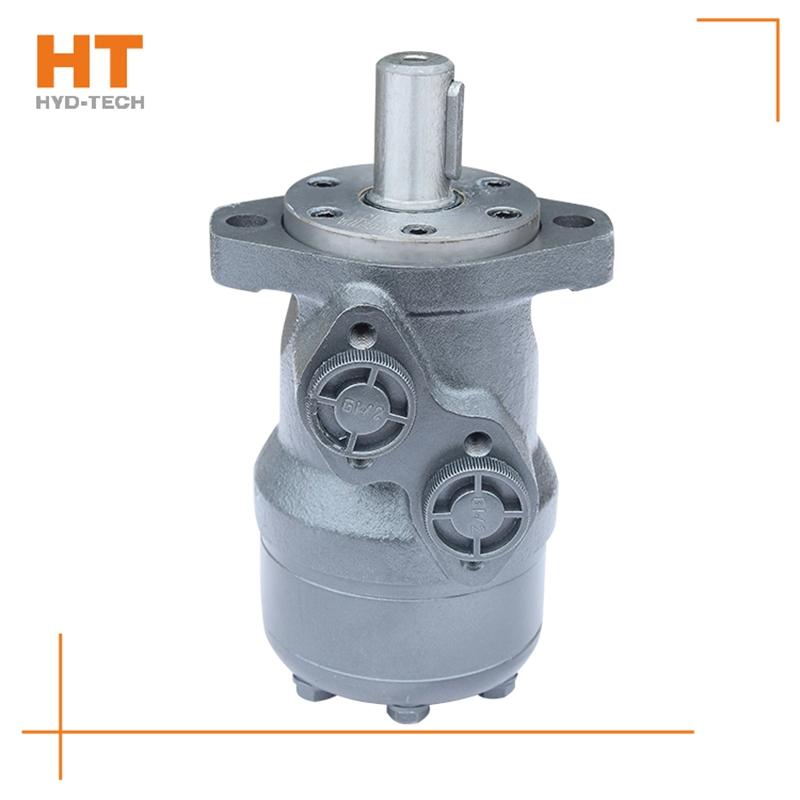
1) Select the hydraulic pump or motor with good quality and conduct regular maintenance. For example, if the tooth profile accuracy of the gear is low, grind the gear to meet the requirements of the contact surface; 2) If the vane pump has trapped oil, the triangular groove of the oil distributor should be corrected to remove the trapped oil; 3) If the axial clearance of the hydraulic pump is too large and the oil delivery is insufficient BM cycloid motor Manufacturer Repair to keep the axial clearance within the allowable range; 4) If the hydraulic pump is not selected correctly, it should be replaced immediately. 3. The reversing valve is improperly adjusted. Improper adjustment of the reversing valve causes the valve core of the reversing valve to move too fast, resulting in reversing shock, noise and vibration. During operation, the valve core branch of hydraulic valve Qinzhou BM cycloid motor Support on the spring. When its frequency is close to the pulsating frequency of oil delivery rate of hydraulic pump or other vibration sources, vibration and noise will be generated.
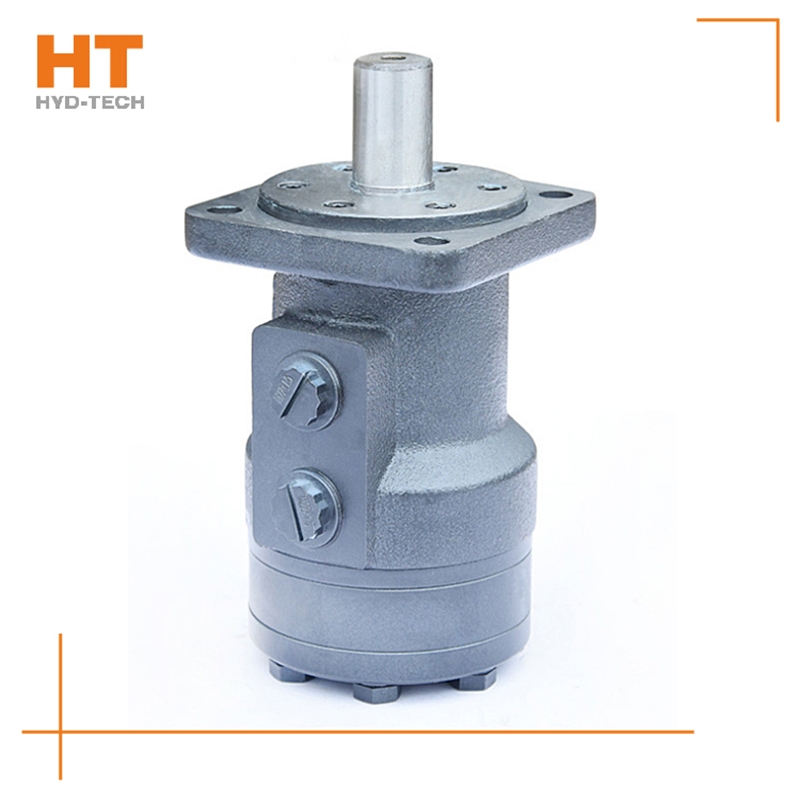
After disassembling and inspecting the hydraulic motor installed on the drill, it was found that the friction surface of the valve disc and the port plate of the hydraulic motor was severely worn, and the deepest worn part was 0. 15mm; The output shaft oil seal is leaking. Cause analysis of oil leakage of output shaft oil seal. After disassembly inspection and test, the axial and radial clearances of the output shaft meet the standard requirements customized BM cycloid motor There is no obvious wear on the oil seal mating surface. However, it is found that the oil seal rubber has hardened and its elasticity has deteriorated. With the increase of sealing lip wear, the pre tightening capacity and sealing performance decrease, and the excessive oil temperature accelerates the wear of sealing lip; In addition, due to the liquid Qinzhou BM cycloid motor The leakage of the pressure motor causes the back pressure in the housing to be too high, which further aggravates the wear and leakage of the sealing lip. The smaller the friction of the rotor in the stator sleeve, the higher the mechanical efficiency of the motor.
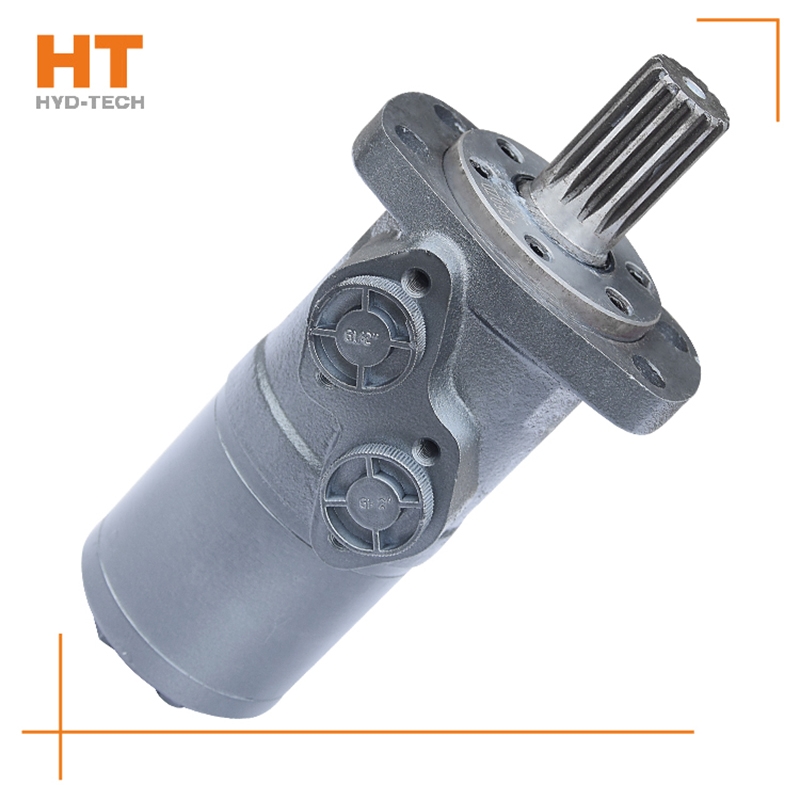
BM cycloidal hydraulic motor is a small low-speed high torque hydraulic motor with single axis flow distribution and fixed rotor set. Its advantages are as follows: 1. It is small in size and light in weight, and its overall size is much smaller than other types of hydraulic motors with the same torque. 2. Wide speed range, stepless speed regulation, minimum stable speed up to 15 rpm, convenient installation and layout, low investment cost. 3. It can be used in series or parallel in the hydraulic system. 4. The moment of inertia is small, and it is easy to start under load. It can rotate in both forward and reverse directions, and it does not need to stop when reversing. BM cycloidal motor is widely used in agriculture, fishery, light industry BM cycloid motor Manufacturer The slewing mechanism of hoisting and transportation, mining, construction machinery and other machinery. Examples of BM cycloidal hydraulic motor used abroad; 1) Agricultural use: various combine harvesters, seeders, rotary tillers, lawn mowers, sprayers, feed mixers, ground drills. 2) Fishery use: net lifter. customized BM cycloid motor 3) Light industry: commercial winding machines, textile machines, printing machines, washing machines. 4) For construction industry: road roller, cement mixer, sweeper.
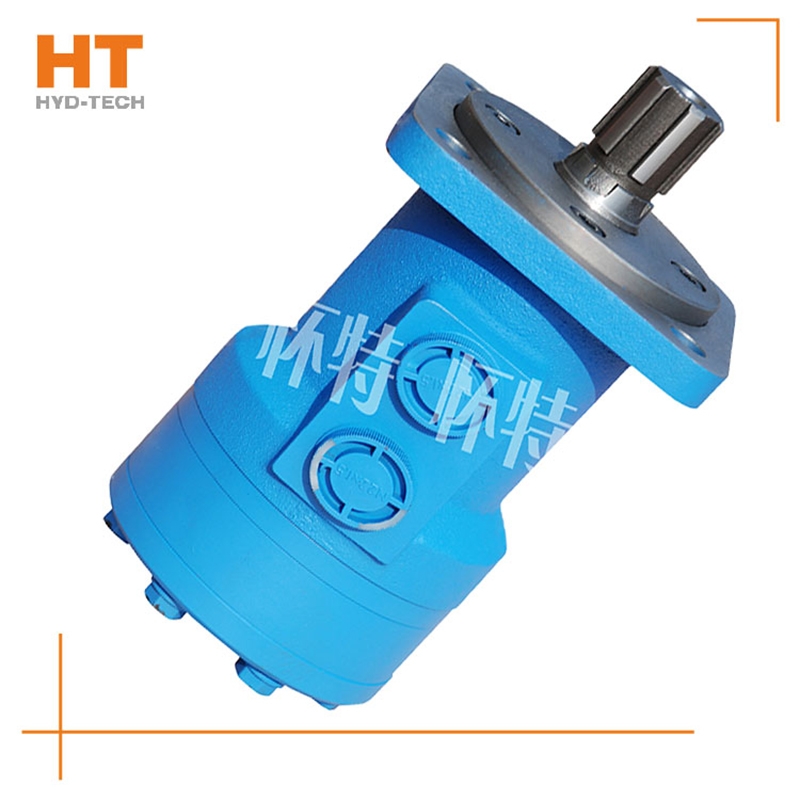
What is the oil supply mode of the hydraulic pump? The straight shaft swashplate plunger pump can be divided into two types: self suction type and pressurized type. Most high-pressure oil supply hydraulic pumps use pneumatic oil tank, and some hydraulic pumps are also equipped with oil make-up slave pump to deliver pressure oil to the oil inlet of the hydraulic pump. The self-priming pump has the characteristics of strong self-priming ability and no need for external oil supply customized BM cycloid motor 。 Bearings for hydraulic pumps. The most important part of the plunger pump is the bearing. If the bearing has clearance, the normal clearance of the three pairs of friction pairs inside the hydraulic pump cannot be guaranteed. At the same time, the hydrostatic support oil film thickness of each friction pair will be damaged, thus reducing the service life of the plunger pump bearing. According to the data provided by the manufacturer of the hydraulic pump, the average service life of the bearing is 10000 hours. If the service life exceeds this value, a new port shall be replaced. 3、 Conclusion. The service life of the piston pump is related to the maintenance at ordinary times, the quantity and quality of the hydraulic oil, and the cleanliness of the oil. At the same time, avoid BM cycloid motor Manufacturer The particles in the oil will wear the friction pair of the plunger pump, which is also an effective method to extend its service life.
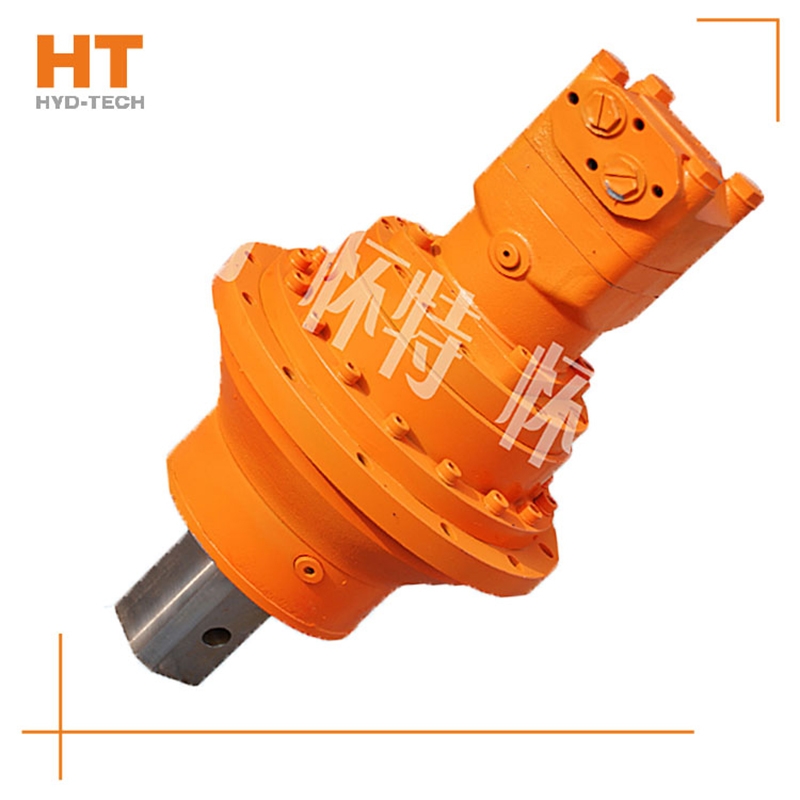
When the main reversing valve of the central closing system and the central closing system is in the neutral position, all oil ports of the reversing valve are closed. If a fixed pump is used for oil supply, the liquid of the hydraulic pump will return to the tank at high pressure through the overflow valve. When the reversing valve is in neutral position, energy transmission starts from the high value, that is, the maximum pressure regulating value of the system. Just reverse BM cycloid motor Manufacturer , its energy can be used by the actuator. When the reversing valve is in the middle position, it sometimes bears all the pressure of the system, so the internal leakage is greater than that of the open system. Generally, when the Qinzhou BM cycloid motor In this case, the energy consumption of the closed loop is high, but if the intermediate unloading measures are added or the pressure compensated variable pump is used for oil supply, the energy consumption of the closed loop can be greatly reduced. Closed hydraulic systems are used for a variety of equipment.
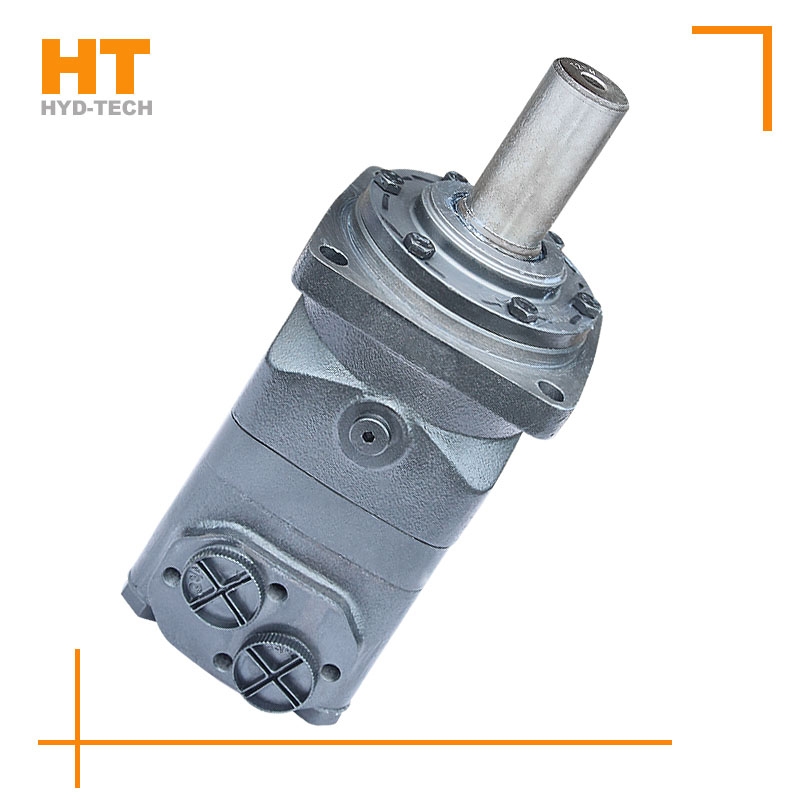
Along the revolution direction of the rotor, the volume of the tooth cavity at the front side of the connection between the rotor and the stator becomes smaller, which is an oil discharge cavity, and the volume at the rear side becomes larger. When the connecting line passes through the two tooth roots of the rotor, the oil inlet ends and the largest tooth cavity appears. When the connecting line passes through the two tooth tops of the rotor, the oil drainage ends and the smallest tooth cavity appears. In order to ensure the continuous rotation of the rotor, it is necessary to have the same regular oil distribution mechanism to cooperate with it, so that the tooth cavity at the front side of the connecting pipeline is always connected with the oil drain port, and the rear side is connected with the oil inlet port. As mentioned above, the oil distribution mechanism consists of a housing and an oil distribution sleeve. The 12 longitudinal grooves (x) on the oil distribution sleeve and the 12 intervals formed by the oil distribution groove face the root and top of the rotor through the positioning device, which proves that when the largest and smallest cavities occur, the oil distribution hole of the housing can be closed, thus separating the oil inlet groove and oil outlet groove of the oil distribution sleeve.