Of course, you can increase the traffic special-purpose Large torque cycloidal motor Increase the speed, but how much will affect the service life. As long as it is within the rated power range, there is no problem. If the oil pressure reaches the rated pressure and the speed increases, it will exceed the power range it can withstand. Of course, it will damage the service life of the cycloidal hydraulic motor. Just like not eating so much hard food, it will damage the stomach. Increasing the flow can only increase the speed in a limited way, from 500 to 900, change the model of the motor, increase the flow of the cycloidal motor, increase the speed without control, increase the internal oil pressure, increase the internal leakage, directly reduce the efficiency, and damage the motor. Above Qinghai Manufacturer Ming can try, and consult the cycloid hydraulic motor expert if he thinks the error is found.
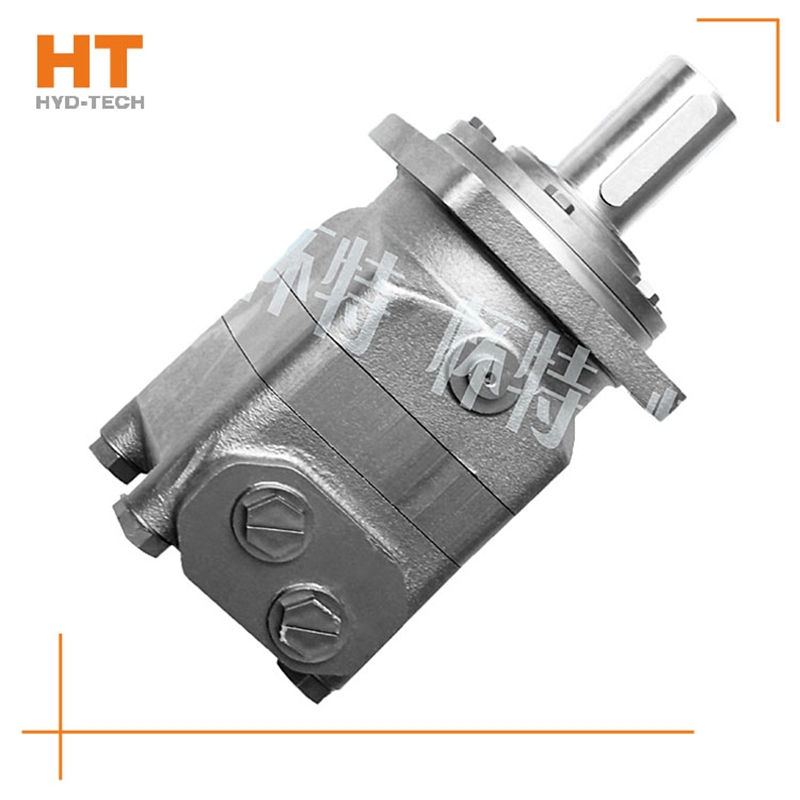
The ignition time of internal combustion engines can be compared with this. It can be seen from the working principle of the cycloidal hydraulic motor that the oil sleeve and the rotor rotate synchronously, and the accuracy refers to the accuracy of the oil distribution link matching with the rotor to rotate the oil inlet, seal and discharge. There are many factors special-purpose Large torque cycloidal motor It will affect the oil distribution accuracy, such as the asymmetry of the rotor spline and cycloid tooth shape, the relative position accuracy of the stator sleeve needle hole and bolt hole, and the relative position asymmetry of the pin hole and spline on the output shaft and its internal spline, Large torque cycloidal motor Manufacturer The relative position accuracy of the longitudinal oil groove and the relative wedge groove of the coupling, and the asymmetry of splines at both ends of the coupling. As long as the above factors are controlled within the tolerance range, they will not have a great impact on the oil distribution accuracy, because all processing errors will not be offset.
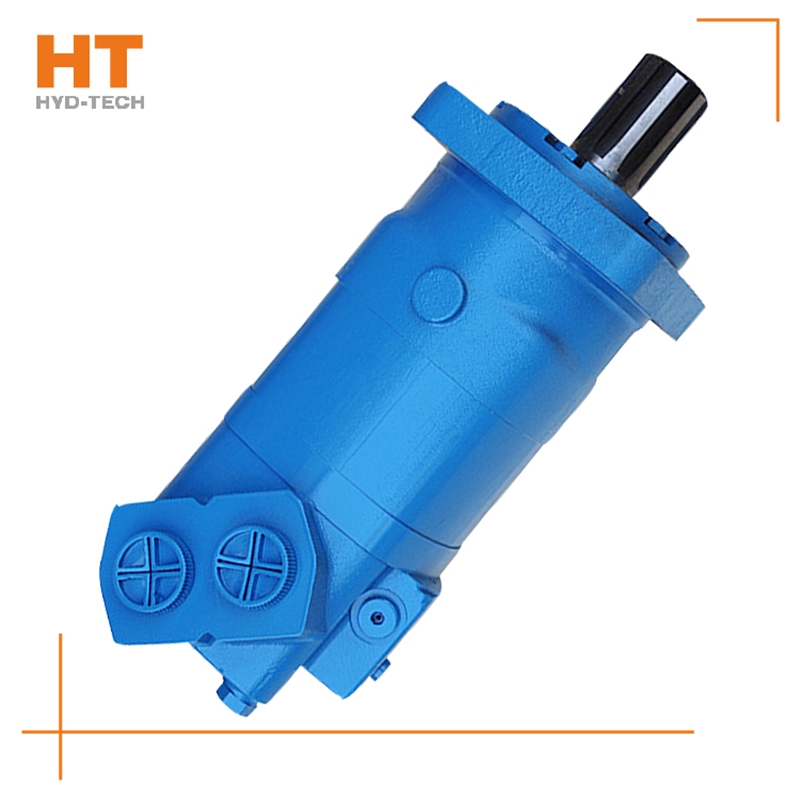
Along the revolution direction of the rotor, the volume of the tooth cavity at the front side of the connection between the rotor and the stator becomes smaller, which is an oil discharge cavity, and the volume at the rear side becomes larger. When the connecting line passes through the two tooth roots of the rotor, the oil inlet ends and the largest tooth cavity appears. When the connecting line passes through the two tooth tops of the rotor, the oil drainage ends and the smallest tooth cavity appears. In order to ensure the continuous rotation of the rotor, it is necessary to have the same regular oil distribution mechanism to cooperate with it, so that the tooth cavity at the front side of the connecting pipeline is always connected with the oil drain port, and the rear side is connected with the oil inlet port. As mentioned above, the oil distribution mechanism consists of a housing and an oil distribution sleeve. The 12 longitudinal grooves (x) on the oil distribution sleeve and the 12 intervals formed by the oil distribution groove face the root and top of the rotor through the positioning device, which proves that when the largest and smallest cavities occur, the oil distribution hole of the housing can be closed, thus separating the oil inlet groove and oil outlet groove of the oil distribution sleeve.
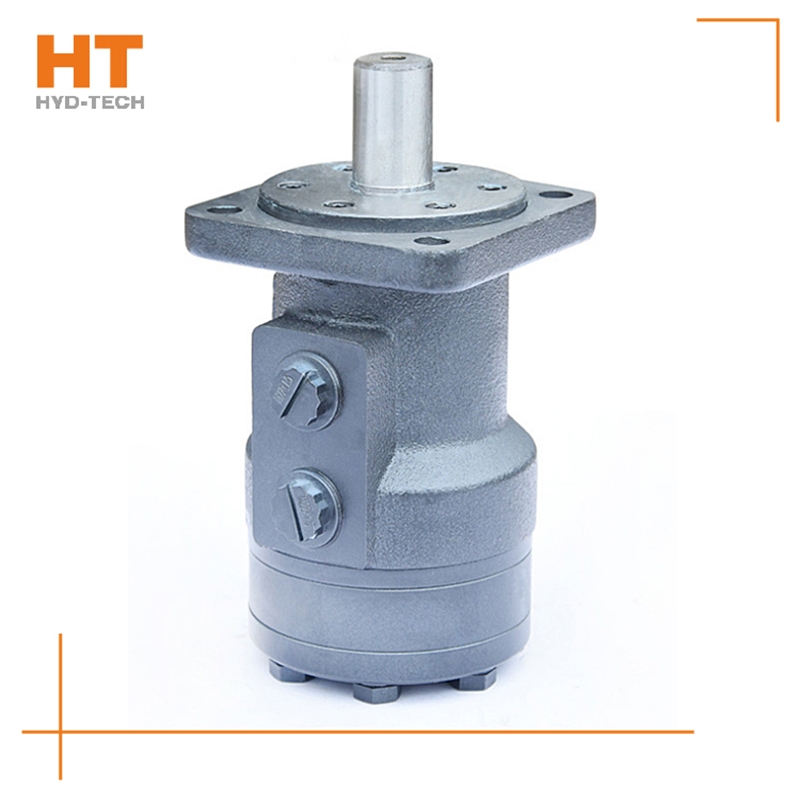
The output pressure of the hydraulic motor also depends on the load. Rated pressure Pn: the rated pressure refers to the working pressure that the hydraulic motor can withstand during continuous operation. It can special-purpose Large torque cycloidal motor To ensure the volumetric efficiency and service life of the hydraulic motor. Working pressure P: the working pressure is the actual pressure of oil input when the hydraulic motor is working Large torque cycloidal motor Manufacturer power. Its value depends on the size of the load. However, the maximum working pressure is determined by the safety valve in the hydraulic system. The throttle adjustment value must not exceed the maximum pressure value of the hydraulic motor. The third is the maximum pressure: the limit pressure that the motor is allowed to overload in a short time. Pn ≤ Pmax value.