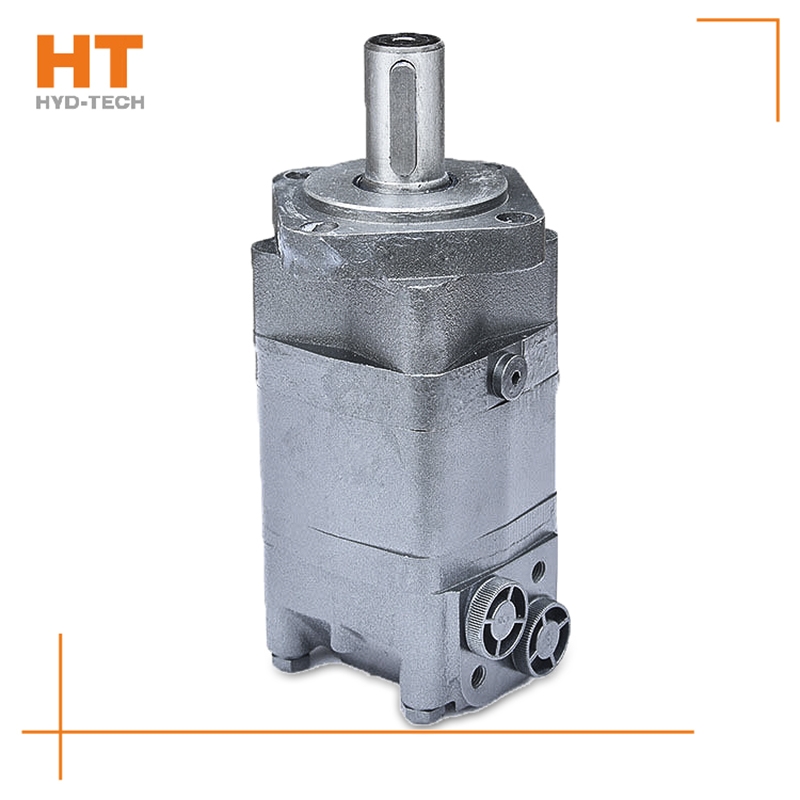
The valve control system controls the flow by changing the opening of the valve throttle, thus controlling the speed of the actuator. Usually, the reason for low efficiency is the existence of throttling and overflow losses. Almost all mechanical equipment adopts valve control system. The pump control system can realize the stepless control of speed by changing the displacement of variable displacement pump, or control the flow through the combination of multiple constant displacement pumps to achieve the stepwise control of speed. The reason for high efficiency is that there is no throttling or overflow loss. It is widely used in high power hydraulic devices such as pressure processing machinery and plastic machinery. The actuator control system controls the flow by changing the variable hydraulic motor flow of the actuator, or through the joint work of multiple quantitative hydraulic motors, or by changing the action area of the composite hydraulic cylinder. Similar to the pump control system, this system has high efficiency because it has no throttling and overflow losses. It is suitable for traveling machinery, press and other hydraulic equipment.
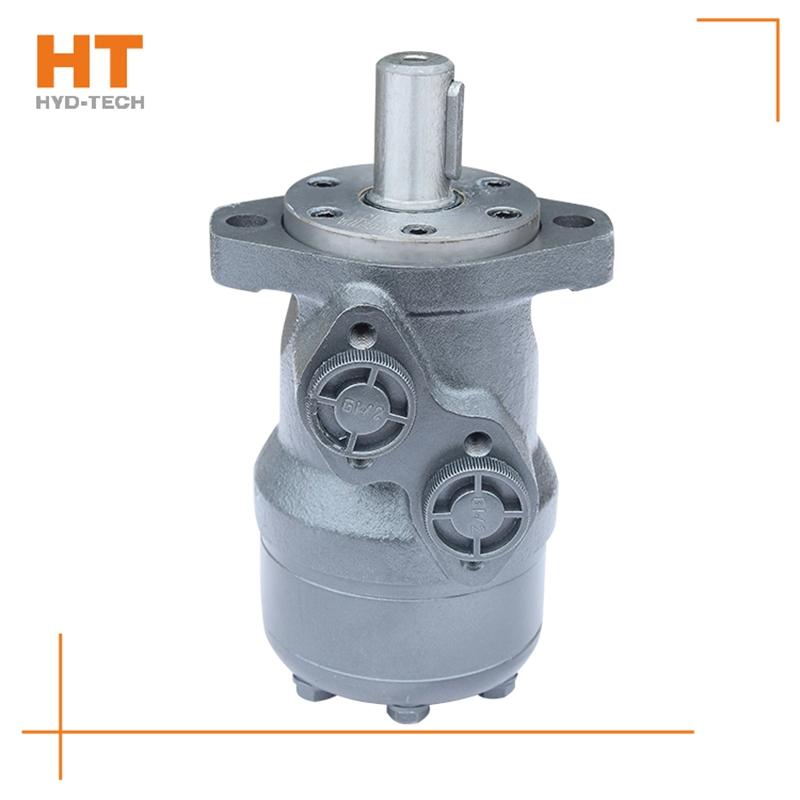
Functions: It is used for the storage, supply and recovery of hydraulic media, the connection between hydraulic components and the transmission of energy carrying hydraulic media, filtering impurities in the hydraulic media, keeping the media required for the normal operation of the system clean, heating or cooling the system, storing and releasing hydraulic energy or absorbing hydraulic pulsation and impact, and displaying the pressure and oil temperature of the system; Hydraulic working medium: various hydraulic oils (fluids), efficacy: as the energy carrying medium of the system, it plays the role of lubrication and cooling while transferring energy. Generally speaking, the hydraulic components that can complete certain specific functions are called hydraulic circuits. In order to meet the working requirements of certain machinery or equipment, the overall structure of several special basic functional circuits connected or combined together is called hydraulic system.
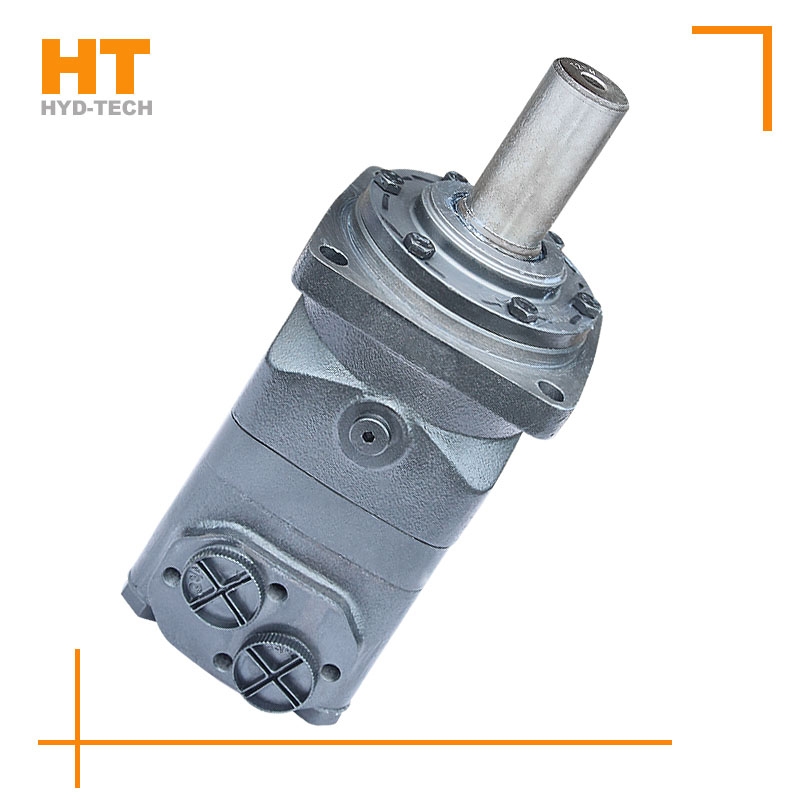
When the working load changes from low speed to high speed in a wide range, the hydraulic motor is also required to be able to drive and regulate speed in the corresponding wide range, which requires the motor to have good low-speed stability and high speed performance. The speed regulation range K of the hydraulic motor is usually expressed by the ratio of the allowable maximum speed to the minimum speed. special-purpose BM cycloid motor It is the highest operating speed of hydraulic motor, but it is limited by many factors, mainly including: 1. Service life. After the speed increases, each pair is worn Harbin manufactor The service life is shortened. 2、 Mechanical efficiency limits. At high speed, the hydraulic motor needs to input large flow, accordingly, the hydraulic loss of each circulating component increases, reducing the mechanical efficiency.
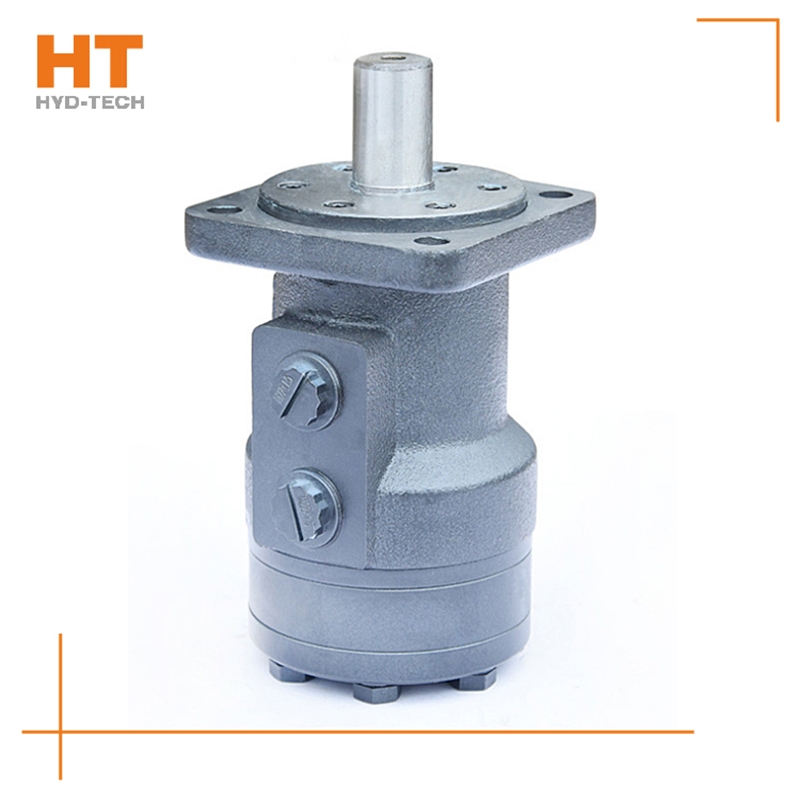
Along the revolution direction of the rotor, the volume of the tooth cavity at the front side of the connection between the rotor and the stator becomes smaller, which is an oil discharge cavity, and the volume at the rear side becomes larger. When the connecting line passes through the two tooth roots of the rotor, the oil inlet ends and the largest tooth cavity appears. When the connecting line passes through the two tooth tops of the rotor, the oil drainage ends and the smallest tooth cavity appears. In order to ensure the continuous rotation of the rotor, it is necessary to have the same regular oil distribution mechanism to cooperate with it, so that the tooth cavity at the front side of the connecting pipeline is always connected with the oil drain port, and the rear side is connected with the oil inlet port. As mentioned above, the oil distribution mechanism consists of a housing and an oil distribution sleeve. The 12 longitudinal grooves (x) on the oil distribution sleeve and the 12 intervals formed by the oil distribution groove face the root and top of the rotor through the positioning device, which proves that when the largest and smallest cavities occur, the oil distribution hole of the housing can be closed, thus separating the oil inlet groove and oil outlet groove of the oil distribution sleeve.
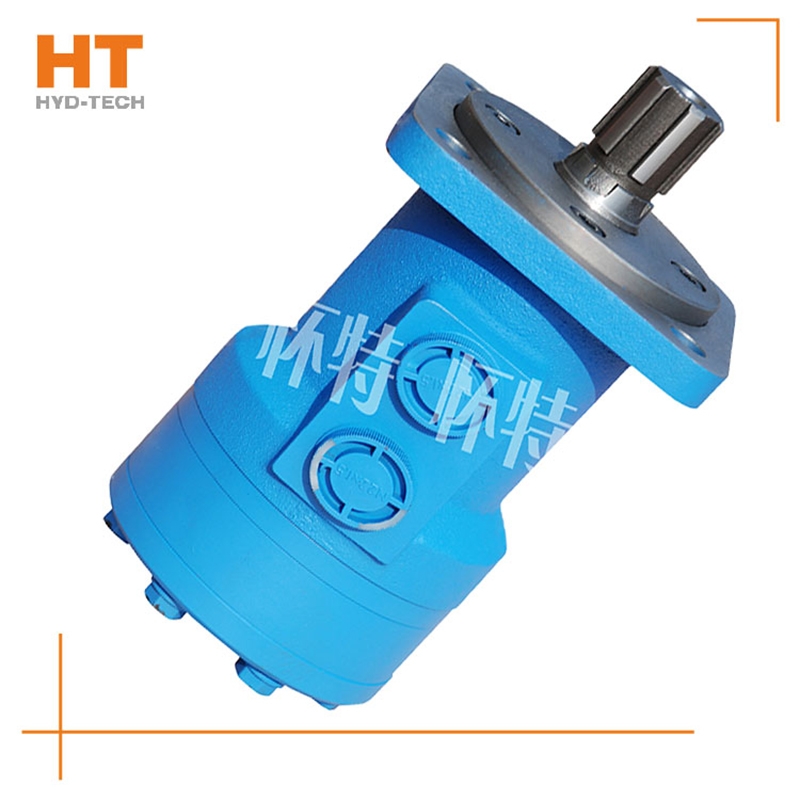
As the power source and actuator of the hydraulic system, the performance of the hydraulic motor has a great impact on the performance of the entire hydraulic system. Therefore, the importance of studying the hydraulic motor performance test system is special-purpose BM cycloid motor It is very important that the rise and application of hydraulic testing technology based on virtual instrument has opened up a broad prospect for the performance testing of hydraulic motors. Hydraulic motors are widely used in machine tools, metallurgy, engineering machinery, plastic machinery, agricultural machinery, mining machinery, marine machinery and many other important fields. The performance of the hydraulic motor has a decisive impact on the whole system, and will directly affect the stability of the system. At the same time, the performance of the hydraulic motor will have an impact on the life of the system components and the production efficiency of the system. Harbin manufactor Unexpected failure of hydraulic motor will greatly reduce production efficiency.
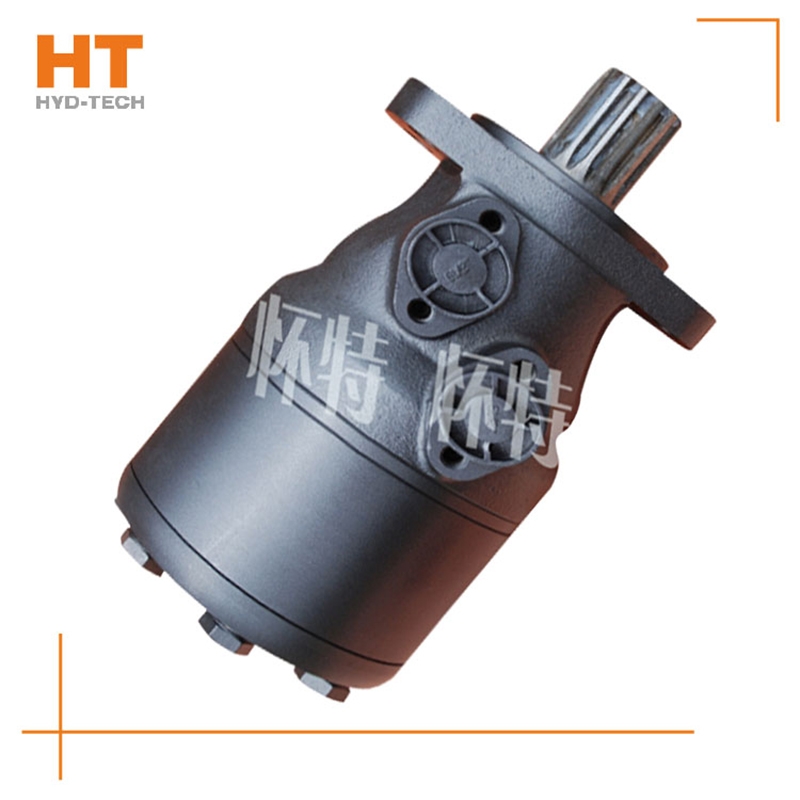
The radial piston hydraulic motor uses a cam ring with a special curve to make each plunger reciprocate several times within one cycle of cylinder block rotation, which is called multi action special-purpose BM cycloid motor Internal curve radial plunger hydraulic motor (referred to as internal curve motor) is used. The internal curve motor has the advantages of small size, light weight, radial force balance, small torque ripple, high starting efficiency, stable operation at very low speed, etc. It has been widely used BM cycloid motor manufactor In marine machinery. Working principle of inner curve motor: the inner wall of the cam ring (housing) is composed of x evenly distributed curved surfaces with the same shape. Each curved surface with the same shape can be divided into two symmetrical sides. The side that allows the plunger set to extend outward is the working section (oil inlet section), and the opposite side is called the oil return section. The number of reciprocating times of each plunger per revolution of the hydraulic motor is equal to the number of curved surfaces of the cam ring x (x is called the number of times of action of the motor).