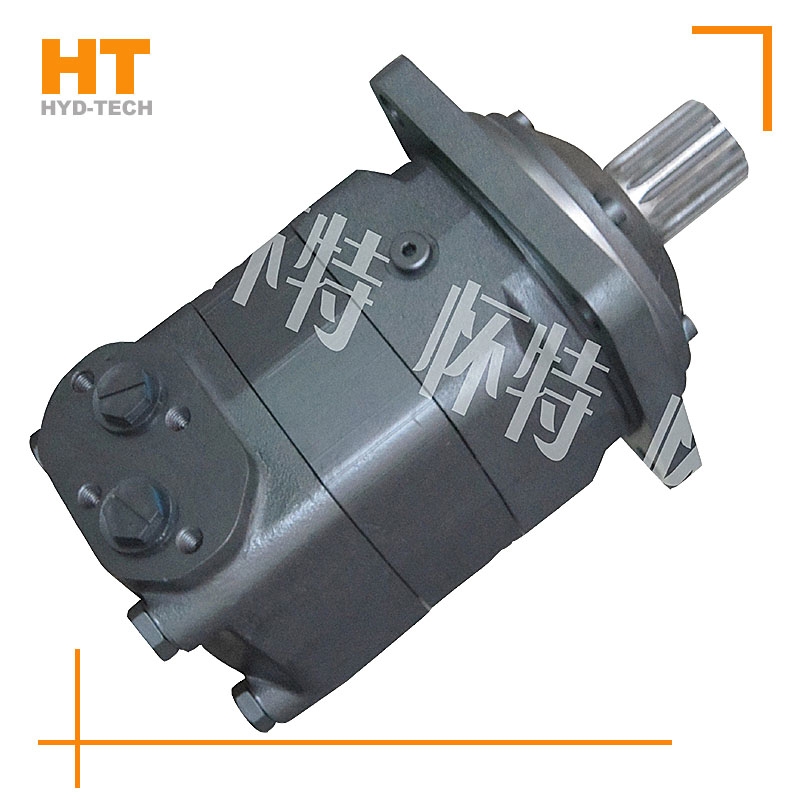
When the main reversing valve of the central closing system and the central closing system is in the neutral position, all oil ports of the reversing valve are closed. If a fixed pump is used for oil supply, the liquid of the hydraulic pump will return to the tank at high pressure through the overflow valve. When the reversing valve is in neutral position, energy transmission starts from the high value, that is, the maximum pressure regulating value of the system. Just reverse Eaton cycloid motor manufactor , its energy can be used by the actuator. When the reversing valve is in the middle position, it sometimes bears all the pressure of the system, so the internal leakage is greater than that of the open system. Generally, when the Suzhou Eaton cycloid motor In this case, the energy consumption of the closed loop is high, but if the intermediate unloading measures are added or the pressure compensated variable pump is used for oil supply, the energy consumption of the closed loop can be greatly reduced. Closed hydraulic systems are used for a variety of equipment.
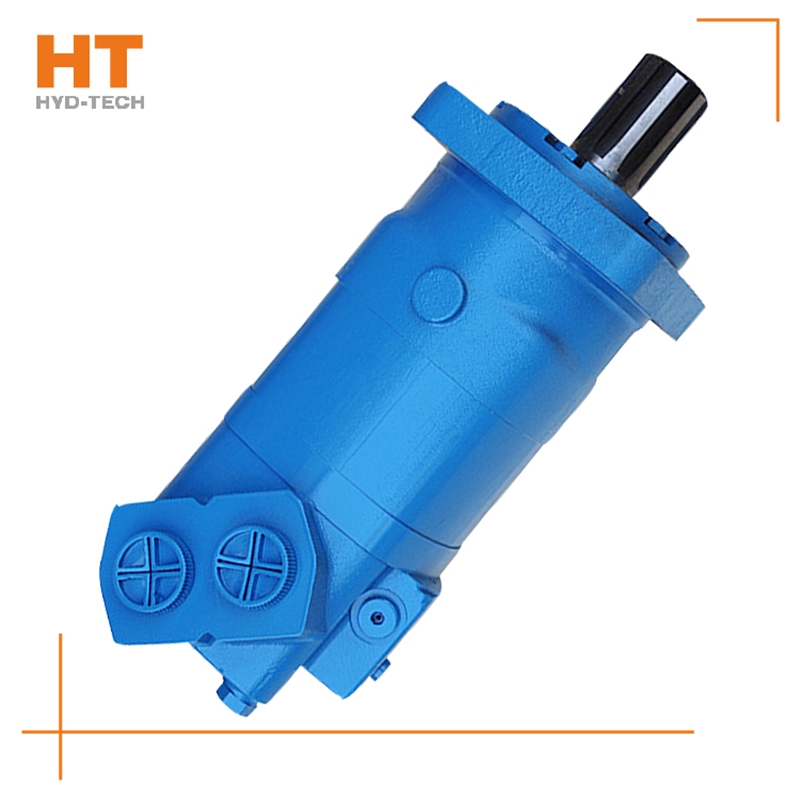
Most of its hydraulic system uses working medium, such as hydraulic oil with continuous fluidity, which converts the mechanical energy of the prime mover driving the pump into the pressure energy of the liquid through the hydraulic pump, and sends it to the actuator (hydraulic cylinder, hydraulic motor or swing hydraulic motor) through various control valves, such as pressure, flow, direction, etc., to convert it into mechanical energy to drive the load. This hydraulic system is generally composed of the following parts: power source, actuator, control valve, hydraulic auxiliary device and hydraulic working medium, which play their respective roles: power source: prime mover (motor or internal combustion engine) and hydraulic pump, whose role is to convert the mechanical energy generated by the prime mover into the pressure energy of liquid, and output oil with a certain pressure;
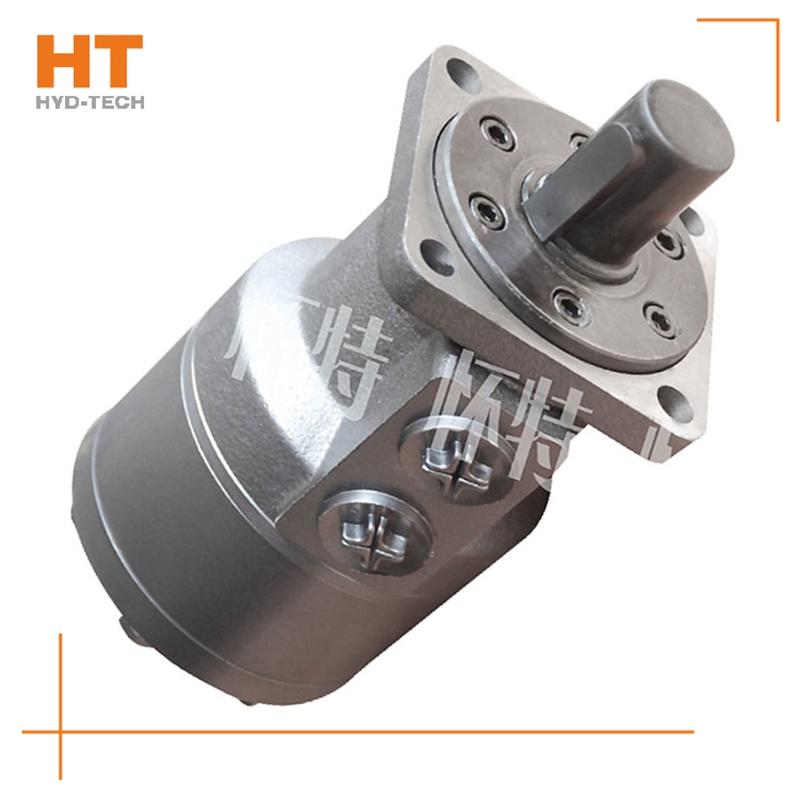
Along the revolution direction of the rotor, the volume of the tooth cavity at the front side of the connection between the rotor and the stator becomes smaller, which is an oil discharge cavity, and the volume at the rear side becomes larger. When the connecting line passes through the two tooth roots of the rotor, the oil inlet ends and the largest tooth cavity appears. When the connecting line passes through the two tooth tops of the rotor, the oil drainage ends and the smallest tooth cavity appears. In order to ensure the continuous rotation of the rotor, it is necessary to have the same regular oil distribution mechanism to cooperate with it, so that the tooth cavity at the front side of the connecting pipeline is always connected with the oil drain port, and the rear side is connected with the oil inlet port. As mentioned above, the oil distribution mechanism consists of a housing and an oil distribution sleeve. The 12 longitudinal grooves (x) on the oil distribution sleeve and the 12 intervals formed by the oil distribution groove face the root and top of the rotor through the positioning device, which proves that when the largest and smallest cavities occur, the oil distribution hole of the housing can be closed, thus separating the oil inlet groove and oil outlet groove of the oil distribution sleeve.
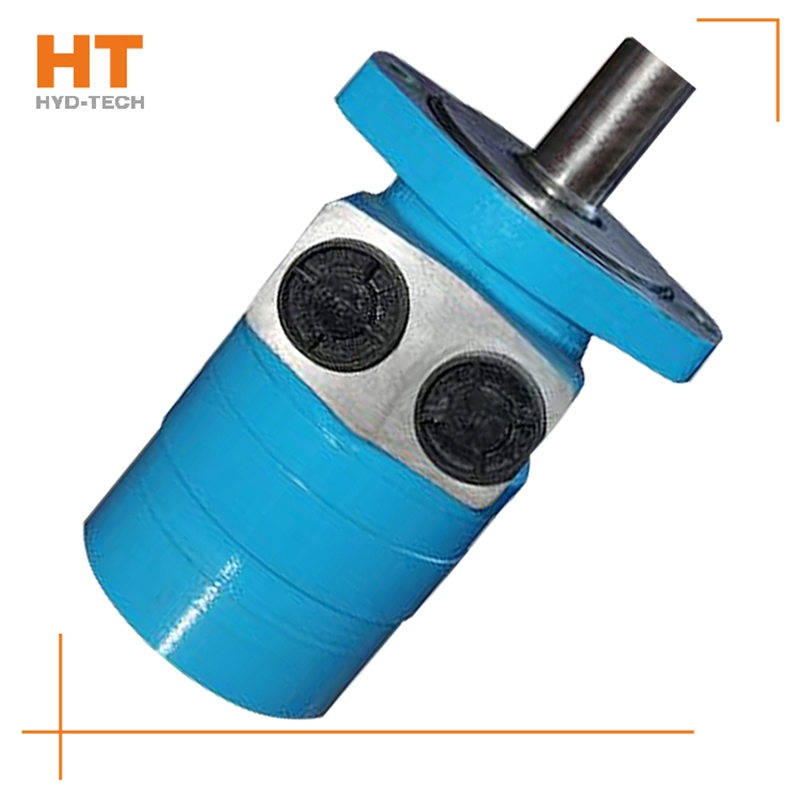
What is the oil supply mode of the hydraulic pump? The straight shaft swashplate plunger pump can be divided into two types: self suction type and pressurized type. Most high-pressure oil supply hydraulic pumps use pneumatic oil tank, and some hydraulic pumps are also equipped with oil make-up slave pump to deliver pressure oil to the oil inlet of the hydraulic pump. The self-priming pump has the characteristics of strong self-priming ability and no need for external oil supply customized Eaton cycloid motor 。 Bearings for hydraulic pumps. The most important part of the plunger pump is the bearing. If the bearing has clearance, the normal clearance of the three pairs of friction pairs inside the hydraulic pump cannot be guaranteed. At the same time, the hydrostatic support oil film thickness of each friction pair will be damaged, thus reducing the service life of the plunger pump bearing. According to the data provided by the manufacturer of the hydraulic pump, the average service life of the bearing is 10000 hours. If the service life exceeds this value, a new port shall be replaced. 3、 Conclusion. The service life of the piston pump is related to the maintenance at ordinary times, the quantity and quality of the hydraulic oil, and the cleanliness of the oil. At the same time, avoid Eaton cycloid motor manufactor The particles in the oil will wear the friction pair of the plunger pump, which is also an effective method to extend its service life.
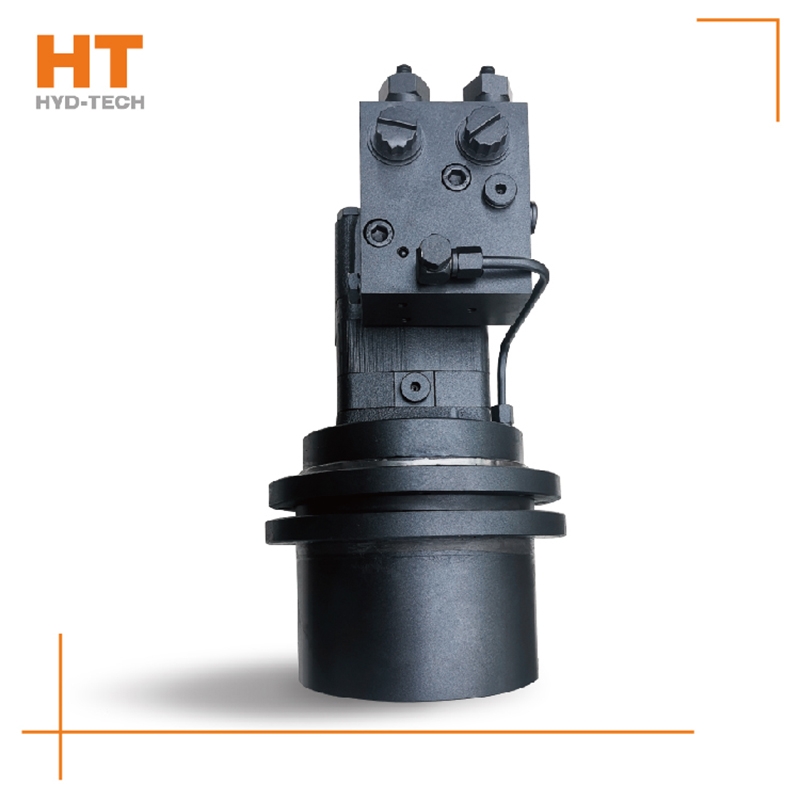
The weight per unit of electricity is very light. Statistics show that the weight of hydraulic pump and hydraulic motor per unit power is only the generator. 1/10 of the motor, hydraulic pump and hydraulic motor can be as small as 0.0025N/W, and the generator and motor with the same power can be about 0.03N/W. As for size, the former is about 12%~13% of the latter. In terms of output force, it is easy to get extremely high pressure hydraulic fluid with a pump, which will produce great force after being delivered to the hydraulic cylinder. Therefore, hydraulic technology has the advantages of light weight Suzhou manufactor The outstanding characteristics of small size and large output are conducive to the miniaturization and miniaturization of mechanical equipment and its control system for high-power operation. Flexible and convenient layout. The configuration of hydraulic components is not restricted by the strict space position, and it is easy to pass according to the needs of the machine. The connection of all parts of the system is realized through pipes, and the layout setting has great flexibility customized Eaton cycloid motor Soft, which can form a complex system that is difficult to form by other methods.
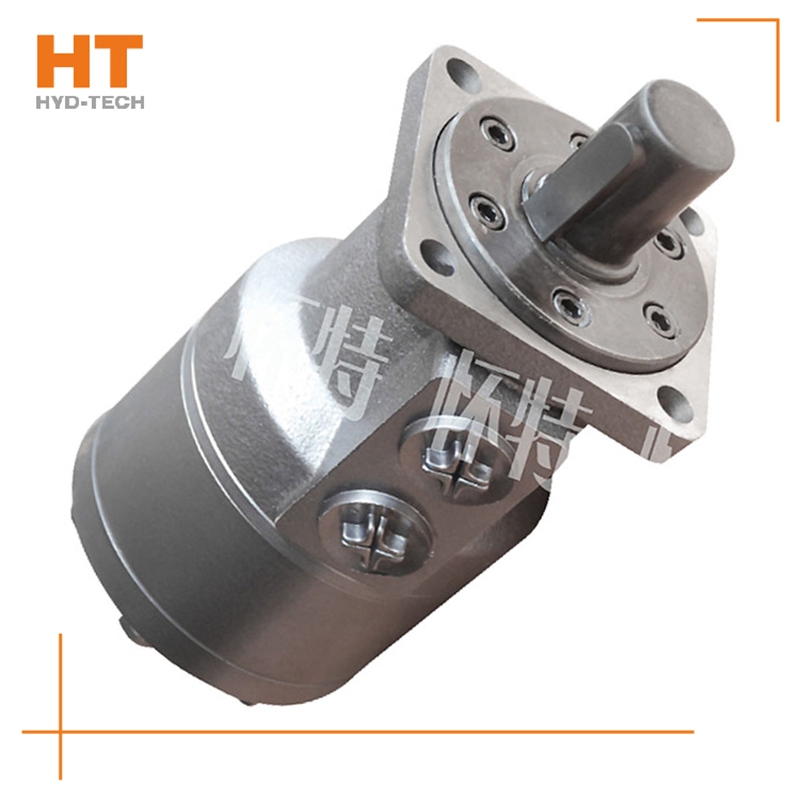
At present, the system used in series by multiple cycloidal motors (see Figure 1) is applied to sweepers, trenchless drills and airport luggage carts. The output shaft of the hydraulic motor often leaks oil during use, so it is useless to replace the dynamic seal of the output shaft. In series application, the problem of casing oil leakage pressure is ignored. The oil leakage pressure of the housing refers to the maximum pressure that the motor shaft seal can bear after the hydraulic motor is fully lubricated inside; If the hydraulic motor is applied customized Eaton cycloid motor Improper. After the machine has been working continuously for a period of time, due to various factors, the oil in the housing will not be released, resulting in higher and higher pressure in the housing of the hydraulic motor, which first leads to the failure of the shaft seal. The casing leakage pressure mentioned here is not the bursting pressure of the casing, but the pressure that the motor output shaft dynamic seal can bear. In the motor samples of some manufacturers, only the back pressure is mentioned. Actually, back pressure refers to electricity Eaton cycloid motor manufactor The return oil pressure of the engine, not the oil discharge pressure of the casing. During operation, the requirements for the oil discharge pressure of the cycloidal motor housing are as follows. Eaton is the world's first cycloid motor manufacturer. In China's domestic cycloidal motor manufacturing industry, Jining Jinjia Hydraulic Co., Ltd. uses Eaton technology to produce cycloidal motors. Its output shaft dynamic seal has better bearing capacity, that is, the unique internal oil circuit design of the company's products enables internal oil drainage not only to lubricate parts, but also to discharge excess oil while maintaining a certain housing oil drainage pressure.