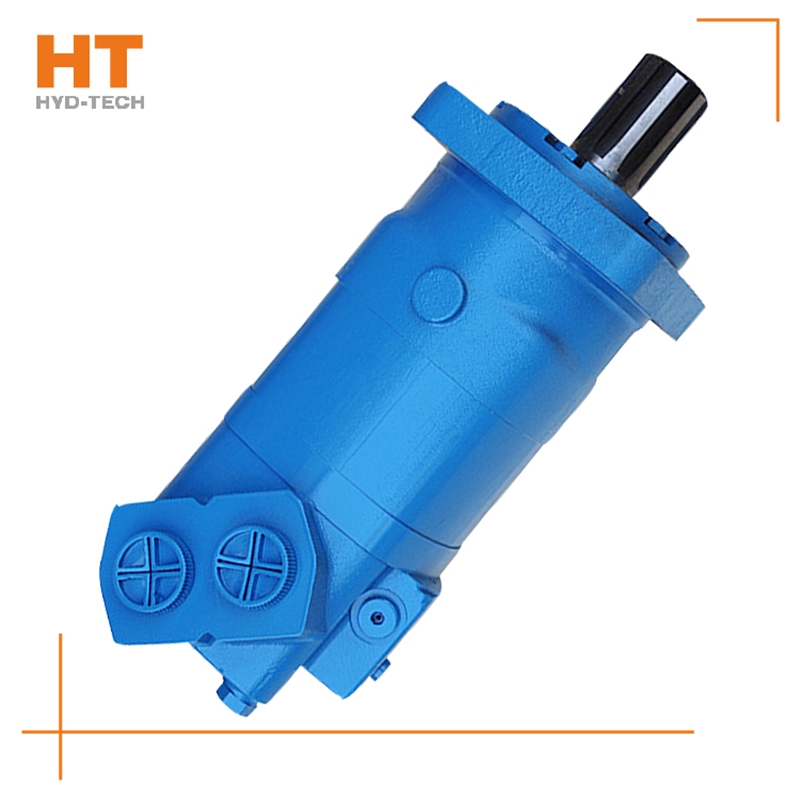
Its basic types are gear type, screw type, vane type and axial plunger type. Its main characteristics are high speed, small moment of inertia, convenient starting and braking, adjustment (speed adjustment and customized Danfoss cycloid motor Reversing) High sensitivity. As the output torque of high-speed hydraulic motor is generally small, it is also called high-speed small torque hydraulic motor. Its basic type is radial plunger type, in addition, there are axial plunger, vane type, gear type and other structural types. Low speed hydraulic motors are mainly characterized by large displacement, large volume and low speed (sometimes Danfoss cycloid motor Manufacturer It can rotate a few revolutions per minute or even a few revolutions per minute), so it can be directly connected to the working mechanism; It does not need a speed reducer, greatly simplifying the transmission mechanism. Usually, the output torque of low-speed hydraulic motor is large, so it is also called low-speed high torque hydraulic motor.
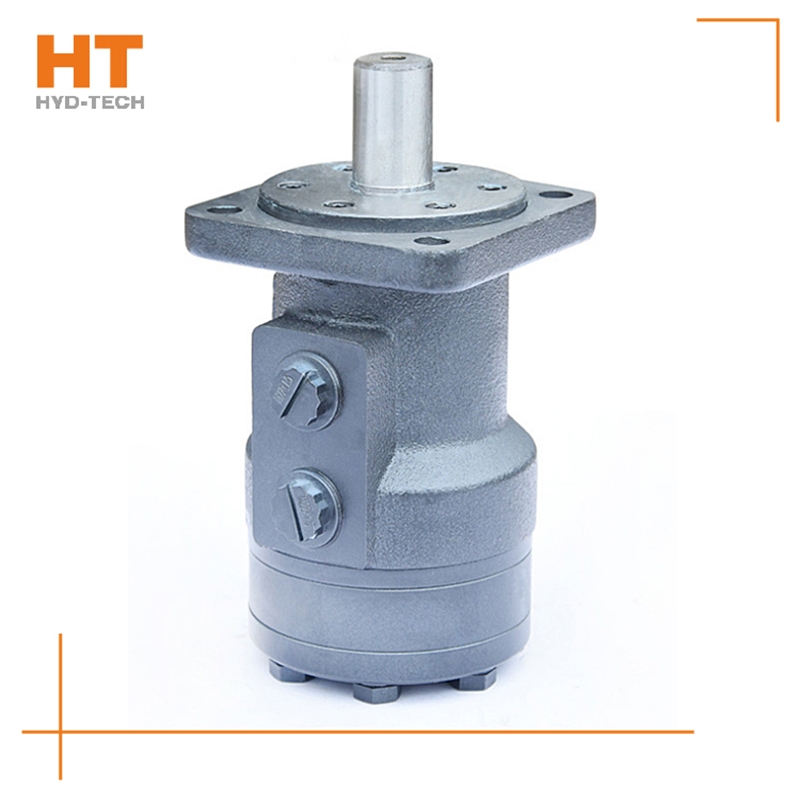
Most of its hydraulic system uses working medium, such as hydraulic oil with continuous fluidity, which converts the mechanical energy of the prime mover driving the pump into the pressure energy of the liquid through the hydraulic pump, and sends it to the actuator (hydraulic cylinder, hydraulic motor or swing hydraulic motor) through various control valves, such as pressure, flow, direction, etc., to convert it into mechanical energy to drive the load. This hydraulic system is generally composed of the following parts: power source, actuator, control valve, hydraulic auxiliary device and hydraulic working medium, which play their respective roles: power source: prime mover (motor or internal combustion engine) and hydraulic pump, whose role is to convert the mechanical energy generated by the prime mover into the pressure energy of liquid, and output oil with a certain pressure;
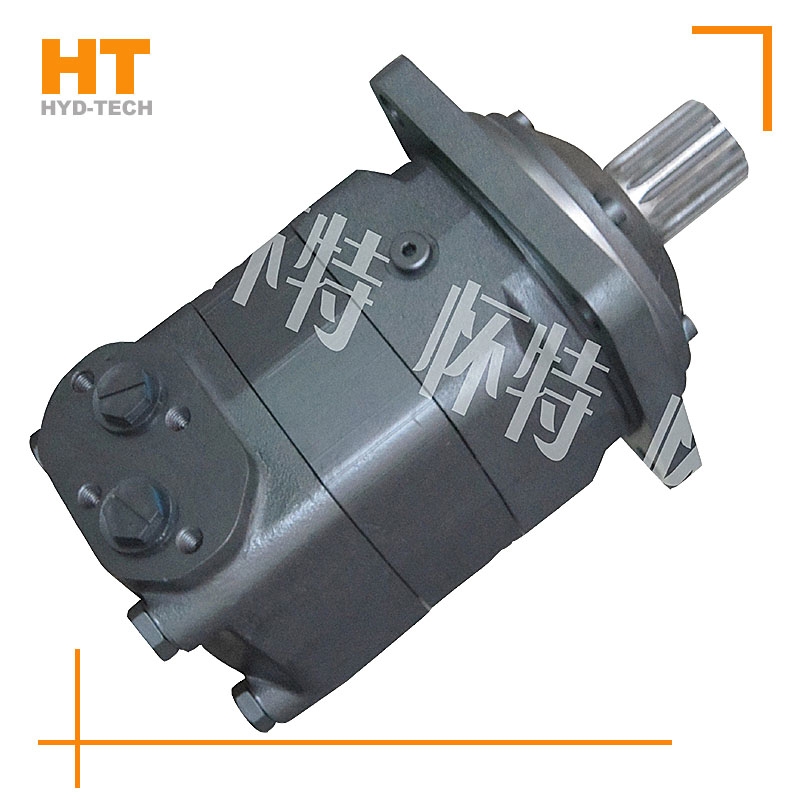
At present, in the hydraulic system of construction machinery, the commonly used oil change method is by cycle or by train number. The hydraulic system of some construction machinery requires that the hydraulic oil be replaced when the motorcycle is 1200. surface customized Danfoss cycloid motor Grid 6 has reference value. For the maintenance of the hydraulic system, the parameters in Table 7 of the used hydraulic oil can better explain the problem. If the three items in Table 7 generally exceed the limit, the hydraulic oil shall be replaced. Except that the solid particles exceed the limit, that is, the hydraulic oil shall be replaced if the solid particles exceed the limit. During field inspection of oil, empirical inspection shall be carried out first, and whether to continue quantitative inspection shall be determined according to the observed oil pollution. According to the test results, determine the solution Danfoss cycloid motor Manufacturer What measures shall be taken for oil pressure (half oil change, full oil change or filtration). Thus, the quality of hydraulic oil in the hydraulic system can be guaranteed, so as to reduce system failures and improve the reliability of the system.
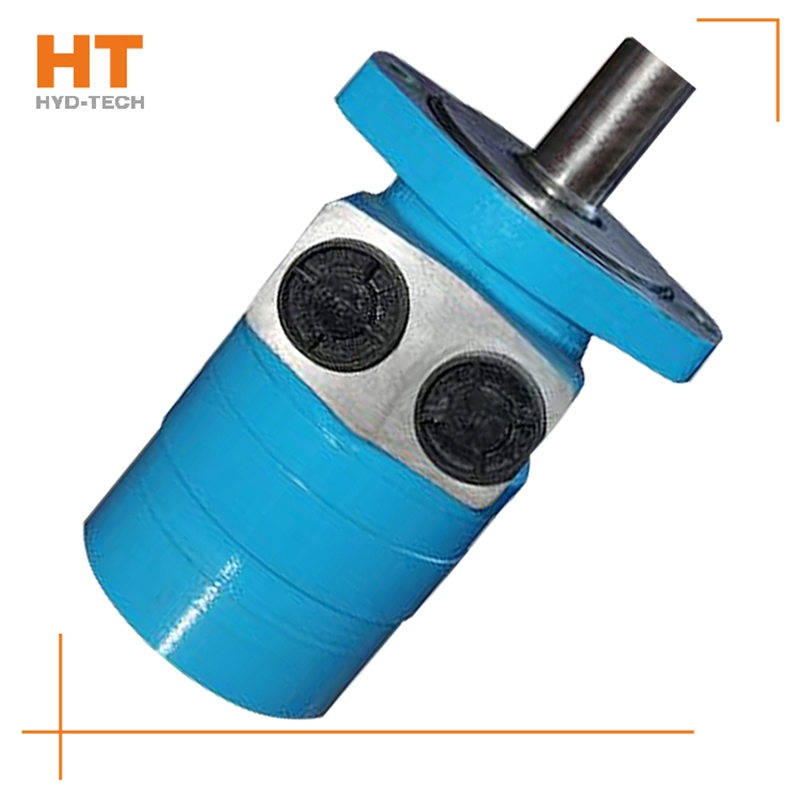
Along the revolution direction of the rotor, the volume of the tooth cavity at the front side of the connection between the rotor and the stator becomes smaller, which is an oil discharge cavity, and the volume at the rear side becomes larger. When the connecting line passes through the two tooth roots of the rotor, the oil inlet ends and the largest tooth cavity appears. When the connecting line passes through the two tooth tops of the rotor, the oil drainage ends and the smallest tooth cavity appears. In order to ensure the continuous rotation of the rotor, it is necessary to have the same regular oil distribution mechanism to cooperate with it, so that the tooth cavity at the front side of the connecting pipeline is always connected with the oil drain port, and the rear side is connected with the oil inlet port. As mentioned above, the oil distribution mechanism consists of a housing and an oil distribution sleeve. The 12 longitudinal grooves (x) on the oil distribution sleeve and the 12 intervals formed by the oil distribution groove face the root and top of the rotor through the positioning device, which proves that when the largest and smallest cavities occur, the oil distribution hole of the housing can be closed, thus separating the oil inlet groove and oil outlet groove of the oil distribution sleeve.