When the working load changes from low speed to high speed in a wide range, the hydraulic motor is also required to be able to drive and regulate speed in the corresponding wide range, which requires the motor to have good low-speed stability and high speed performance. The speed regulation range K of the hydraulic motor is usually expressed by the ratio of the allowable maximum speed to the minimum speed. special-purpose M+S cycloidal motor It is the highest operating speed of hydraulic motor, but it is limited by many factors, mainly including: 1. Service life. After the speed increases, each pair is worn Yantai Price The service life is shortened. 2、 Mechanical efficiency limits. At high speed, the hydraulic motor needs to input large flow, accordingly, the hydraulic loss of each circulating component increases, reducing the mechanical efficiency.
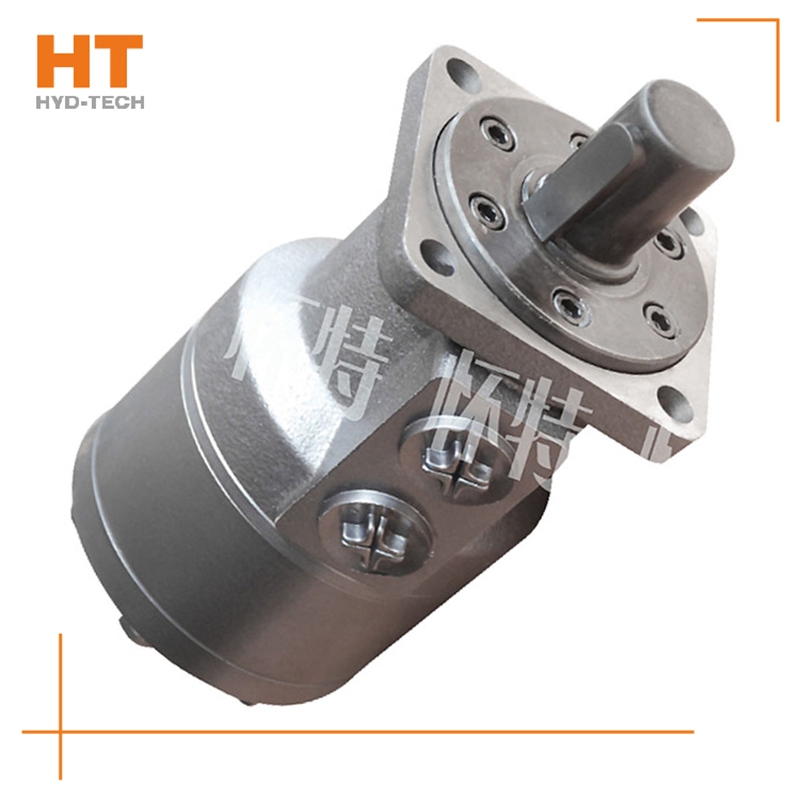
The weight per unit of electricity is very light. Statistics show that the weight of hydraulic pump and hydraulic motor per unit power is only the generator. 1/10 of the motor, hydraulic pump and hydraulic motor can be as small as 0.0025N/W, and the generator and motor with the same power can be about 0.03N/W. As for size, the former is about 12%~13% of the latter. In terms of output force, it is easy to get extremely high pressure hydraulic fluid with a pump, which will produce great force after being delivered to the hydraulic cylinder. Therefore, hydraulic technology has the advantages of light weight Yantai Price The outstanding characteristics of small size and large output are conducive to the miniaturization and miniaturization of mechanical equipment and its control system for high-power operation. Flexible and convenient layout. The configuration of hydraulic components is not restricted by the strict space position, and it is easy to pass according to the needs of the machine. The connection of all parts of the system is realized through pipes, and the layout setting has great flexibility special-purpose M+S cycloidal motor Soft, which can form a complex system that is difficult to form by other methods.
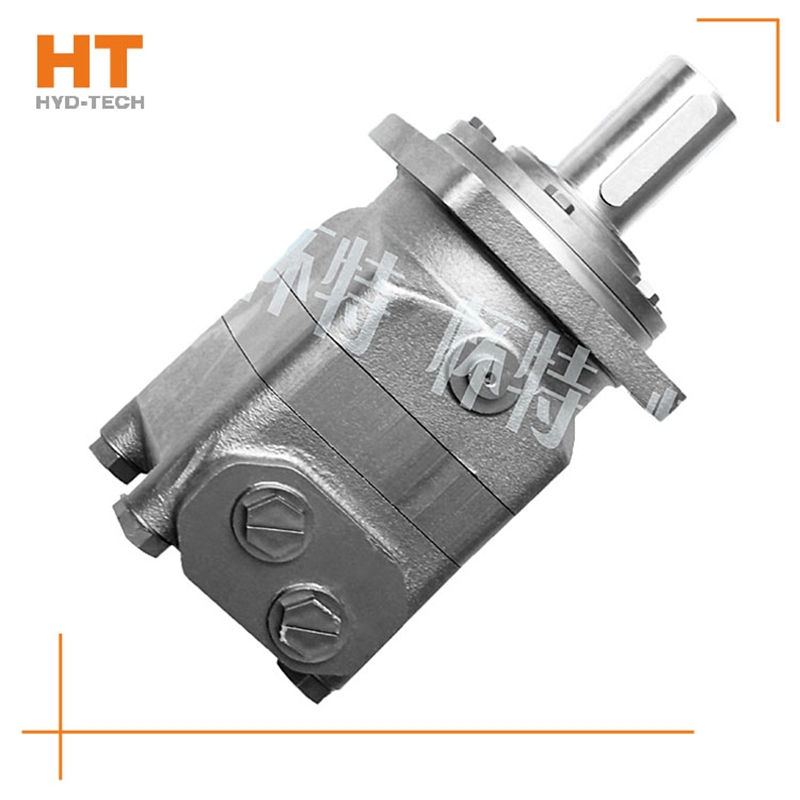
As a hydraulic equipment, hydraulic motor has been widely used in many factories. Generally, we should master the assembly skills of the hydraulic motor: the hydraulic system should special-purpose M+S cycloidal motor Correct machining and assembly. The mounting surface of the hydraulic valve on the oil block should be straight, and the sealing surface of the sealing groove should be finished to avoid radial scratches. The preload of the connection between the hydraulic valve and the oil circuit block and the connection between the oil circuit blocks shall be sufficient to prevent surface separation. The hydraulic equipment shall be inspected according to relevant standards before assembly M+S cycloidal motor Price Check the pressure leakage of system components. If problems are found, corresponding measures shall be taken. If the problem is serious, it should be replaced. Accurately formulate the assembly process documents of hydraulic equipment, configure necessary assembly tools, and strictly follow the assembly process. Keep the hydraulic components, accessories, sealing parts and pipe fittings clean to prevent contamination, and check the integrity of the sealing surface and connecting threads. The hydraulic connector should not be tightened too tightly, otherwise some parts will be severely deformed or even broken, causing leakage. Avoid damaging sealing parts during assembly.
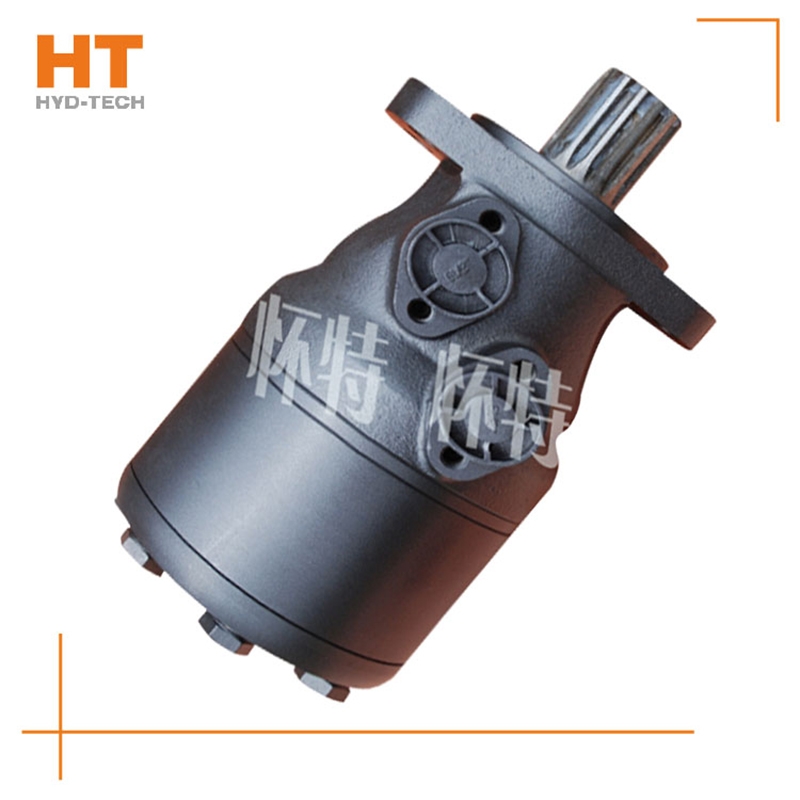
Causes: 1. The pump is damaged, and the pump body is overheated and produces noise. 2. The control valve is closed tightly or the oil supply and return system is blocked, and local overheating occurs. 3. The safety valve is opened, and the valve cries or hisses, and local overheating occurs. 4. The distribution rotary valve is excessively leaking, and the valve chamber is overheated, and it is very hot when touched by hand. 5. The hydraulic motor crankcase is excessively leaking, and the single oil drain pipe is leaking special-purpose M+S cycloidal motor Treatment method for excessive leakage and high oil level: 1. Check the condition of the ball joint 2. Check the sealing condition of the cylinder piston 3. Check the viscosity and operating temperature of the oil 4. Check the contact surface between the oil pan and the housing 5. Check the surface between the connecting rod and the eccentric wheel M+S cycloidal motor Price 6. Check the wear of the oil pan and whether the two oil cavity channels at the inlet and outlet of the casting are connected
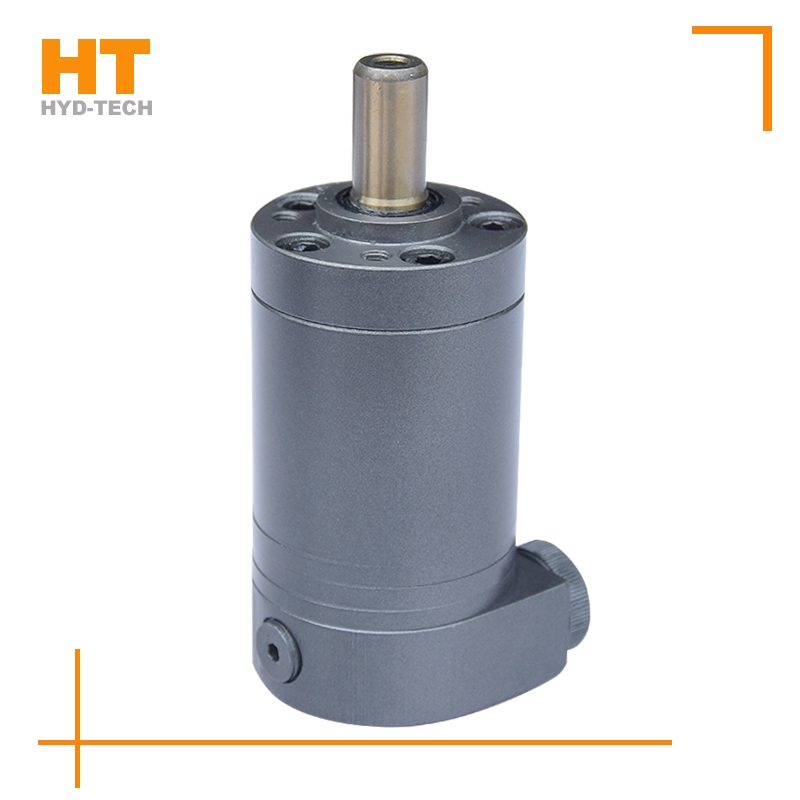
The output pressure of the hydraulic motor also depends on the load. Rated pressure Pn: the rated pressure refers to the working pressure that the hydraulic motor can withstand during continuous operation. It can special-purpose M+S cycloidal motor To ensure the volumetric efficiency and service life of the hydraulic motor. Working pressure P: the working pressure is the actual pressure of oil input when the hydraulic motor is working M+S cycloidal motor Price power. Its value depends on the size of the load. However, the maximum working pressure is determined by the safety valve in the hydraulic system. The throttle adjustment value must not exceed the maximum pressure value of the hydraulic motor. The third is the maximum pressure: the limit pressure that the motor is allowed to overload in a short time. Pn ≤ Pmax value.
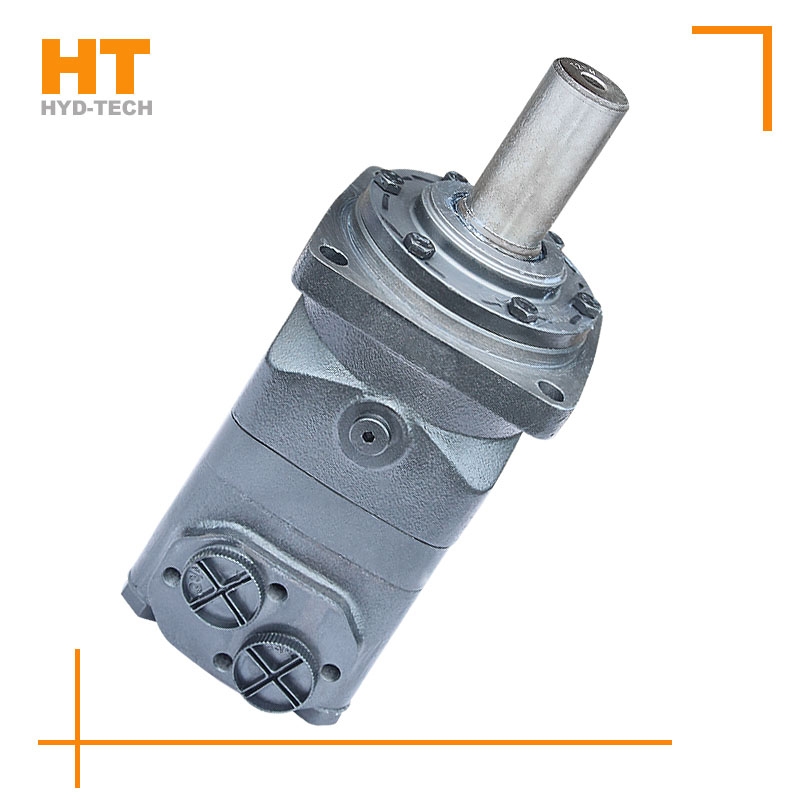
Along the revolution direction of the rotor, the volume of the tooth cavity at the front side of the connection between the rotor and the stator becomes smaller, which is an oil discharge cavity, and the volume at the rear side becomes larger. When the connecting line passes through the two tooth roots of the rotor, the oil inlet ends and the largest tooth cavity appears. When the connecting line passes through the two tooth tops of the rotor, the oil drainage ends and the smallest tooth cavity appears. In order to ensure the continuous rotation of the rotor, it is necessary to have the same regular oil distribution mechanism to cooperate with it, so that the tooth cavity at the front side of the connecting pipeline is always connected with the oil drain port, and the rear side is connected with the oil inlet port. As mentioned above, the oil distribution mechanism consists of a housing and an oil distribution sleeve. The 12 longitudinal grooves (x) on the oil distribution sleeve and the 12 intervals formed by the oil distribution groove face the root and top of the rotor through the positioning device, which proves that when the largest and smallest cavities occur, the oil distribution hole of the housing can be closed, thus separating the oil inlet groove and oil outlet groove of the oil distribution sleeve.