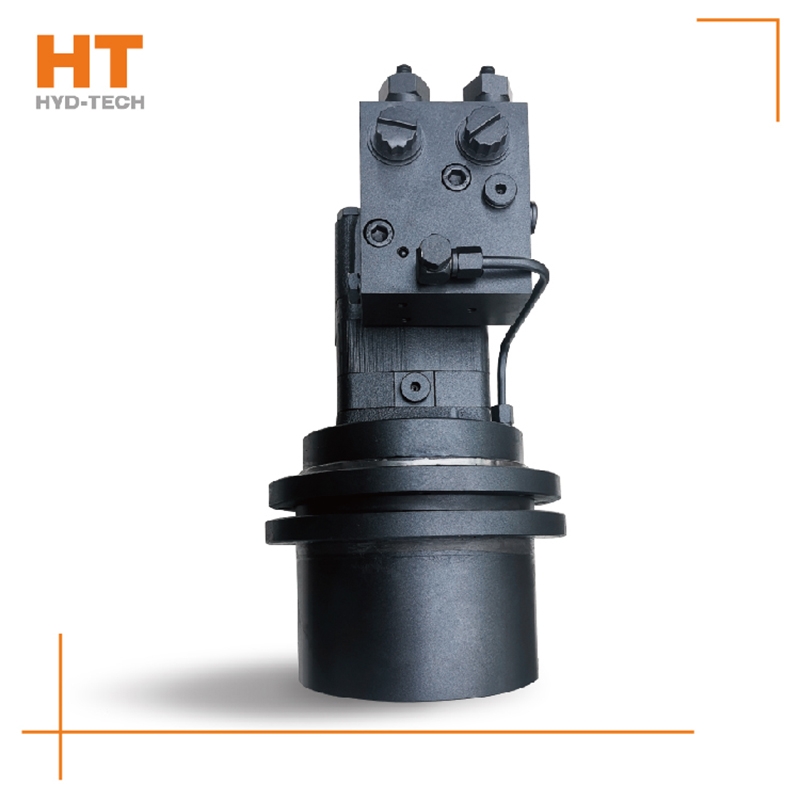
The weight per unit of electricity is very light. Statistics show that the weight of hydraulic pump and hydraulic motor per unit power is only the generator. 1/10 of the motor, hydraulic pump and hydraulic motor can be as small as 0.0025N/W, and the generator and motor with the same power can be about 0.03N/W. As for size, the former is about 12%~13% of the latter. In terms of output force, it is easy to get extremely high pressure hydraulic fluid with a pump, which will produce great force after being delivered to the hydraulic cylinder. Therefore, hydraulic technology has the advantages of light weight Xuchang Price The outstanding characteristics of small size and large output are conducive to the miniaturization and miniaturization of mechanical equipment and its control system for high-power operation. Flexible and convenient layout. The configuration of hydraulic components is not restricted by the strict space position, and it is easy to pass according to the needs of the machine. The connection of all parts of the system is realized through pipes, and the layout setting has great flexibility special-purpose OM cycloidal motor Soft, which can form a complex system that is difficult to form by other methods.
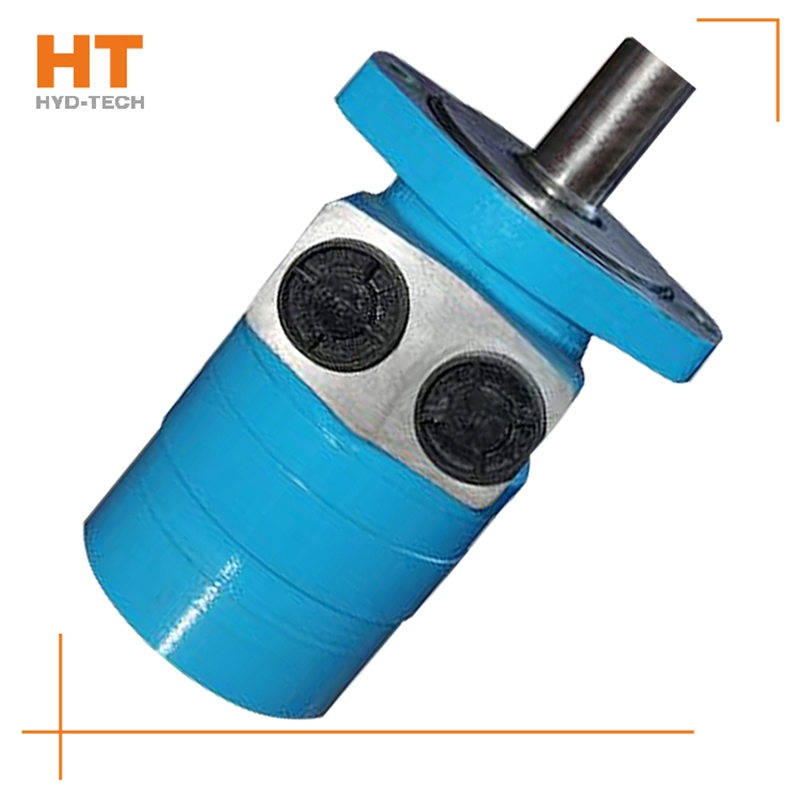
Of course, you can increase the traffic special-purpose OM cycloidal motor Increase the speed, but how much will affect the service life. As long as it is within the rated power range, there is no problem. If the oil pressure reaches the rated pressure and the speed increases, it will exceed the power range it can withstand. Of course, it will damage the service life of the cycloidal hydraulic motor. Just like not eating so much hard food, it will damage the stomach. Increasing the flow can only increase the speed in a limited way, from 500 to 900, change the model of the motor, increase the flow of the cycloidal motor, increase the speed without control, increase the internal oil pressure, increase the internal leakage, directly reduce the efficiency, and damage the motor. Above Xuchang Price Ming can try, and consult the cycloid hydraulic motor expert if he thinks the error is found.
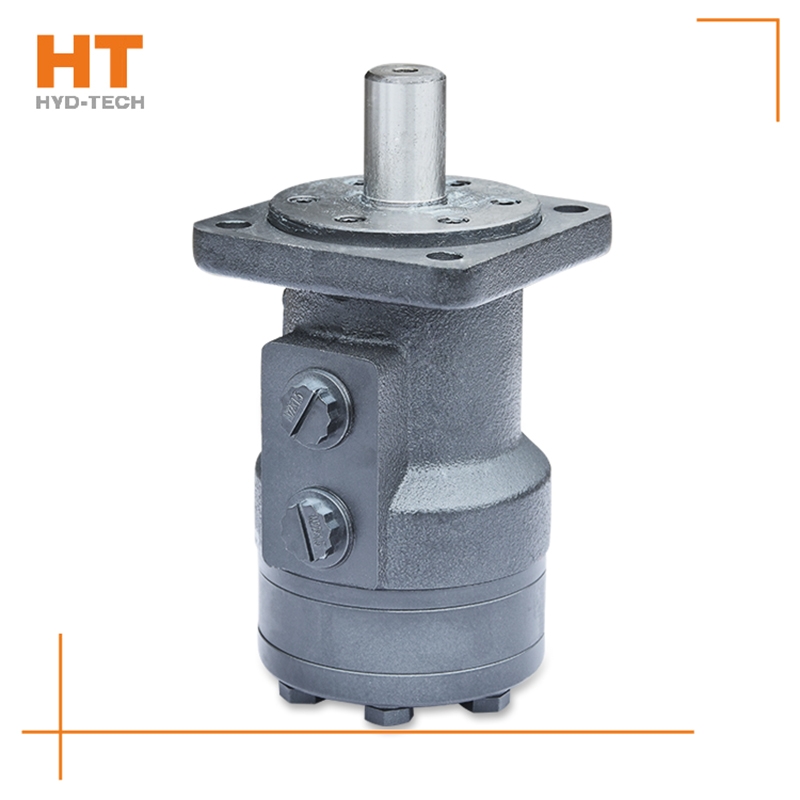
Oil filling process sequence: shell oil filler → oil filling sleeve groove → oil filling sleeve groove → shell oil filling hole → diaphragm → stator. Oil drainage process sequence: rotating stator → diaphragm OM cycloidal motor Price → Shell oil distribution hole → oil distribution jacket longitudinal groove → oil distribution jacket groove → shell oil return port. The rotating motion of the rotor includes rotation (rotation in the direction of expanding the high-pressure cavity around the center of the rotor) and revolution (rotation in the direction of deviation from the radius around the center of the stator). The rotation of the rotor is opposite to the revolution direction, and the rotation is transmitted to the output shaft through the linkage shaft. Rotor rotates for 1 cycle special-purpose OM cycloidal motor The rotor is driven by 42 pressure oil with the maximum volume for 6 revolutions, so the motor has a large emissions.
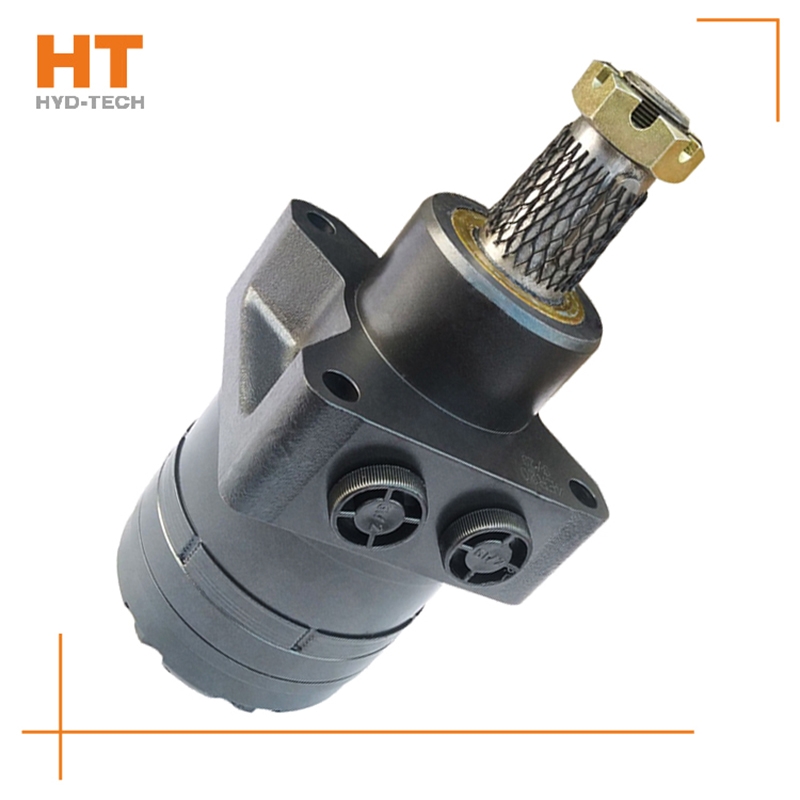
Along the revolution direction of the rotor, the volume of the tooth cavity at the front side of the connection between the rotor and the stator becomes smaller, which is an oil discharge cavity, and the volume at the rear side becomes larger. When the connecting line passes through the two tooth roots of the rotor, the oil inlet ends and the largest tooth cavity appears. When the connecting line passes through the two tooth tops of the rotor, the oil drainage ends and the smallest tooth cavity appears. In order to ensure the continuous rotation of the rotor, it is necessary to have the same regular oil distribution mechanism to cooperate with it, so that the tooth cavity at the front side of the connecting pipeline is always connected with the oil drain port, and the rear side is connected with the oil inlet port. As mentioned above, the oil distribution mechanism consists of a housing and an oil distribution sleeve. The 12 longitudinal grooves (x) on the oil distribution sleeve and the 12 intervals formed by the oil distribution groove face the root and top of the rotor through the positioning device, which proves that when the largest and smallest cavities occur, the oil distribution hole of the housing can be closed, thus separating the oil inlet groove and oil outlet groove of the oil distribution sleeve.
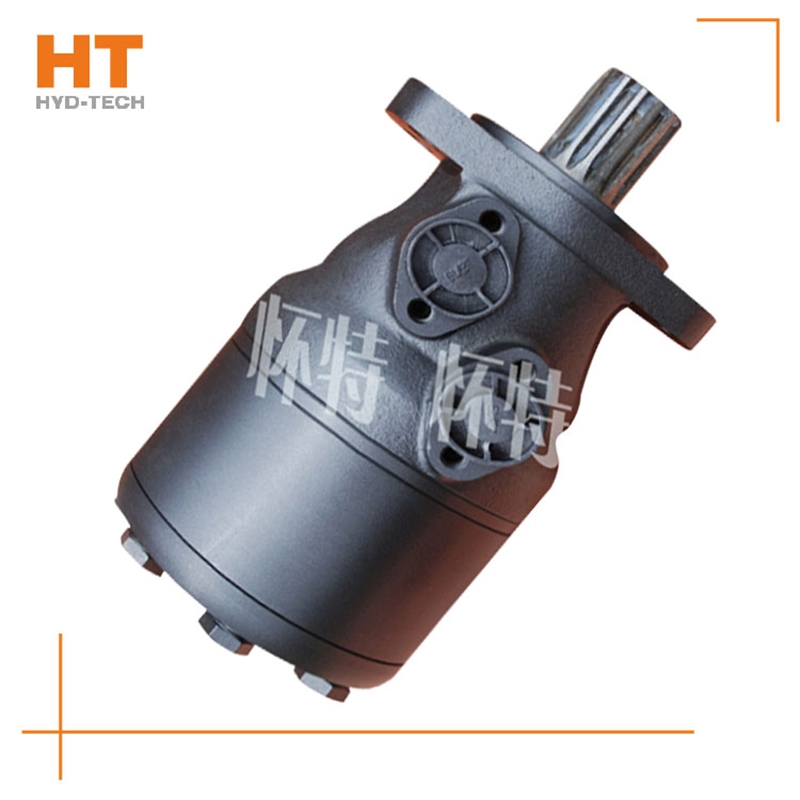
Most of its hydraulic system uses working medium, such as hydraulic oil with continuous fluidity, which converts the mechanical energy of the prime mover driving the pump into the pressure energy of the liquid through the hydraulic pump, and sends it to the actuator (hydraulic cylinder, hydraulic motor or swing hydraulic motor) through various control valves, such as pressure, flow, direction, etc., to convert it into mechanical energy to drive the load. This hydraulic system is generally composed of the following parts: power source, actuator, control valve, hydraulic auxiliary device and hydraulic working medium, which play their respective roles: power source: prime mover (motor or internal combustion engine) and hydraulic pump, whose role is to convert the mechanical energy generated by the prime mover into the pressure energy of liquid, and output oil with a certain pressure;
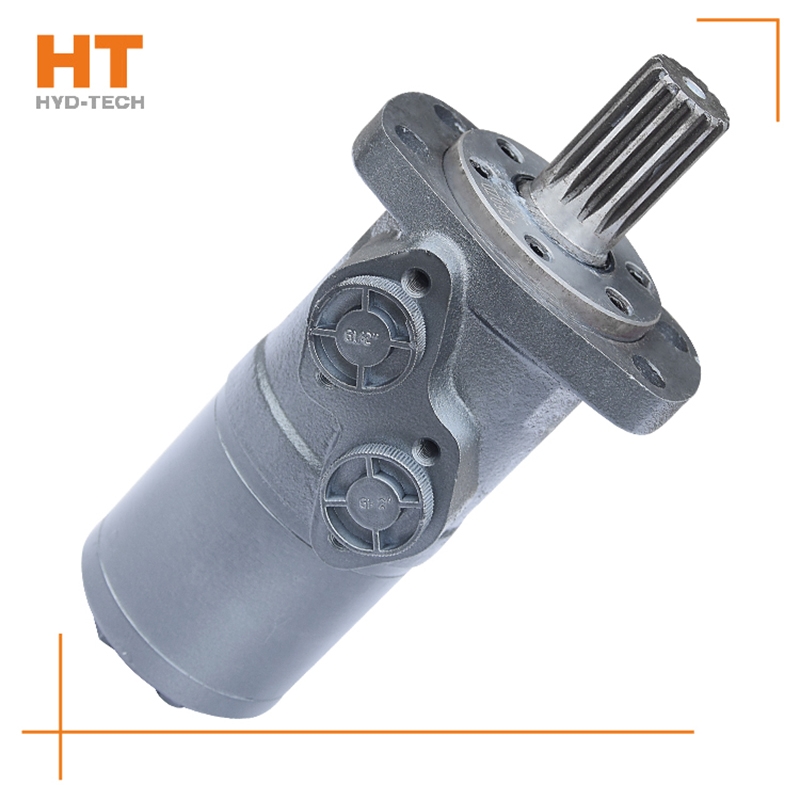
As far as energy conversion is concerned, the hydraulic pump and hydraulic motor are connected as reversible hydraulic components, and the working fluid can be input into any kind of hydraulic pump to make it become a hydraulic motor; On the contrary, when the main shaft of the hydraulic motor rotates under the action of external force OM cycloidal motor Price It can also become a hydraulic pump. Because they all have the same basic structural elements, namely sealed and recyclable volume and corresponding distribution mechanism. However, the working environment of hydraulic motor and hydraulic pump is different special-purpose OM cycloidal motor The performance requirements are also different. Therefore, there are many differences between the hydraulic motor and the hydraulic pump of the same model. The first hydraulic motor should be positive and negative, so its internal structure should be symmetrical; The speed range of the motor must be large enough, especially its minimum stable speed must have certain requirements.