Actuator: hydraulic cylinder, hydraulic motor and swing hydraulic motor. Function: convert the pressure energy of liquid into mechanical energy, which is used to drive the working mechanism to do work and realize reciprocating straight special-purpose Cycloid hydraulic motor Linear motion, continuous rotation or swing; Governor: pressure, flow, direction control valve and other control elements. Function: control the oil pressure, flow and direction from the pump to the actuator in the hydraulic system, so as to control the force (torque) and speed output by the actuator Nanning Cycloid hydraulic motor Degree (speed) and direction, to ensure that the main engine working mechanism driven by the actuator can complete the predetermined motion law; Hydraulic auxiliary device: oil tank, pipe fittings, filter, heat exchanger, accumulator, indicating instrument, etc.
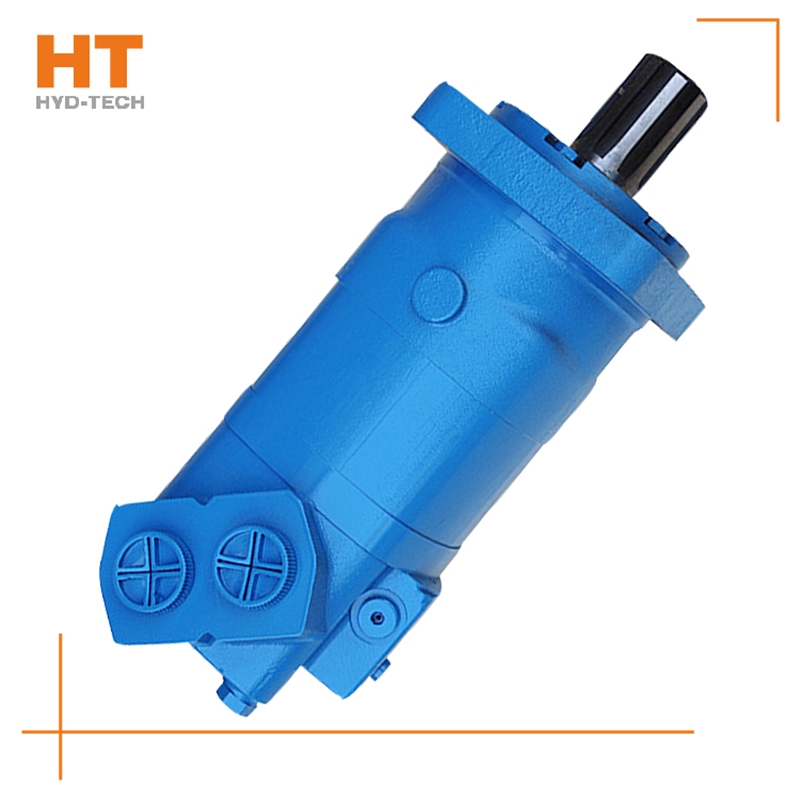
As a hydraulic equipment, hydraulic motor has been widely used in many factories. Generally, we should master the assembly skills of the hydraulic motor: the hydraulic system should special-purpose Cycloid hydraulic motor Correct machining and assembly. The mounting surface of the hydraulic valve on the oil block should be straight, and the sealing surface of the sealing groove should be finished to avoid radial scratches. The preload of the connection between the hydraulic valve and the oil circuit block and the connection between the oil circuit blocks shall be sufficient to prevent surface separation. The hydraulic equipment shall be inspected according to relevant standards before assembly Cycloid hydraulic motor manufactor Check the pressure leakage of system components. If problems are found, corresponding measures shall be taken. If the problem is serious, it should be replaced. Accurately formulate the assembly process documents of hydraulic equipment, configure necessary assembly tools, and strictly follow the assembly process. Keep the hydraulic components, accessories, sealing parts and pipe fittings clean to prevent contamination, and check the integrity of the sealing surface and connecting threads. The hydraulic connector should not be tightened too tightly, otherwise some parts will be severely deformed or even broken, causing leakage. Avoid damaging sealing parts during assembly.
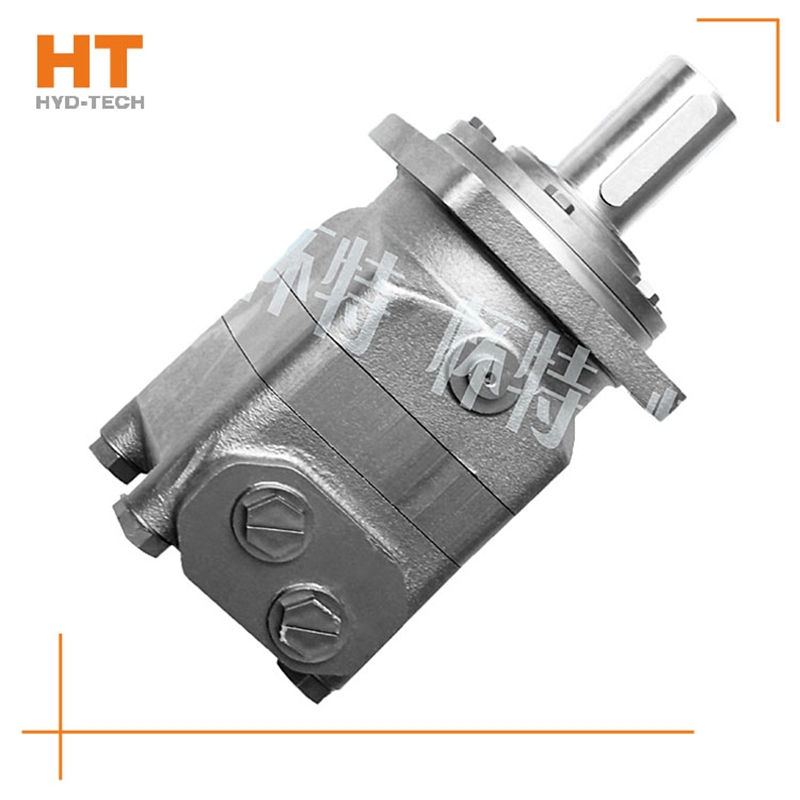
The valve control system controls the flow by changing the opening of the valve throttle, thus controlling the speed of the actuator. Usually, the reason for low efficiency is the existence of throttling and overflow losses. Almost all mechanical equipment adopts valve control system. The pump control system can realize the stepless control of speed by changing the displacement of variable displacement pump, or control the flow through the combination of multiple constant displacement pumps to achieve the stepwise control of speed. The reason for high efficiency is that there is no throttling or overflow loss. It is widely used in high power hydraulic devices such as pressure processing machinery and plastic machinery. The actuator control system controls the flow by changing the variable hydraulic motor flow of the actuator, or through the joint work of multiple quantitative hydraulic motors, or by changing the action area of the composite hydraulic cylinder. Similar to the pump control system, this system has high efficiency because it has no throttling and overflow losses. It is suitable for traveling machinery, press and other hydraulic equipment.
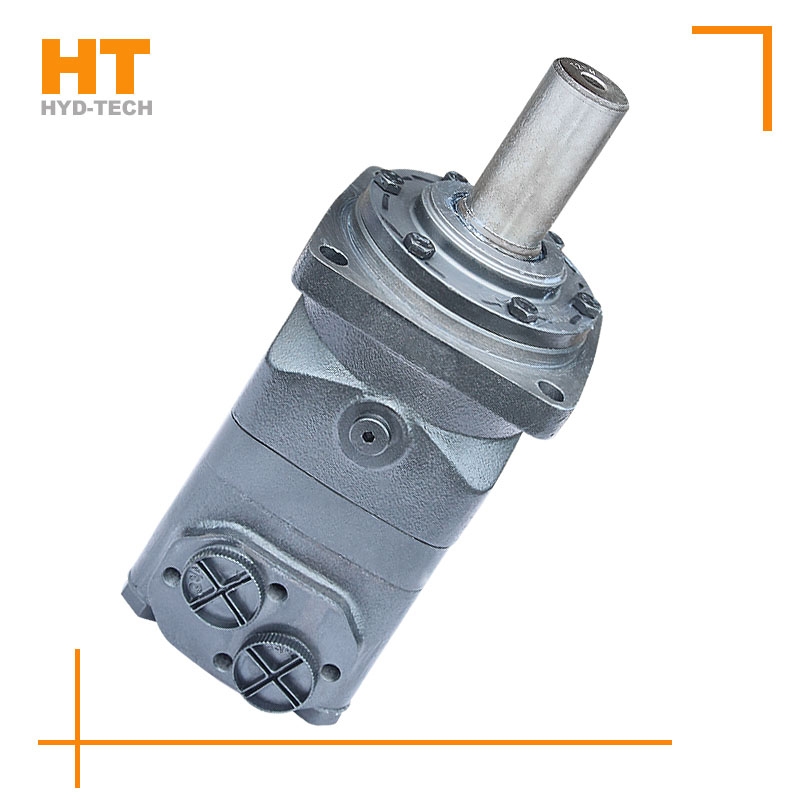
Cycloidal hydraulic motor structure: the internal meshing gear pair consisting of rotor and stator, cycloidal needle wheel, as the meshing pair, has a torque generating part. The stator, together with the spacer and the rear cover, is fixed on the housing to form seven cavities that are only connected with the oil holes on the housing one by one. A distribution mechanism consisting of an oil distribution sleeve and a housing. Two oil distribution sleeves Nanning Cycloid hydraulic motor The ring groove is respectively connected with the oil inlet and return ports of the housing, and its longitudinal groove has twelve oil ports, Cycloid hydraulic motor manufactor Six oil ports and the oil distribution hole of the housing form the oil distribution link. The splines at both ends of the linkage shaft are respectively connected with the rotor and the output shaft, which is used to transmit torque and ensure that the oil sleeve is synchronized with the output shaft. The function of the output shaft is to output the torque generated by the rotor through the linkage shaft and drive the oil distribution device to rotate synchronously.
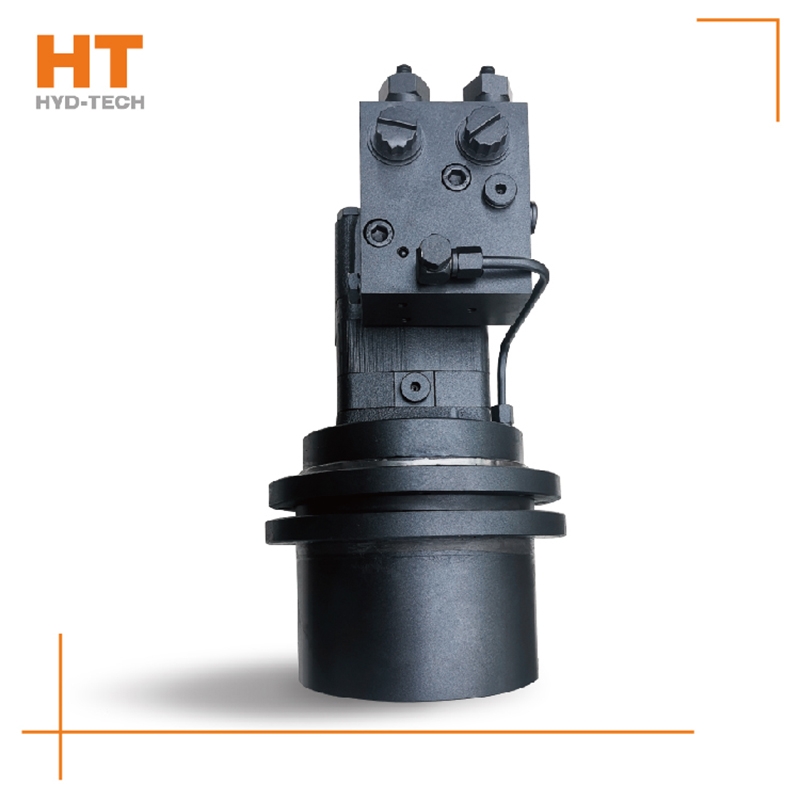
Of course, you can increase the traffic special-purpose Cycloid hydraulic motor Increase the speed, but how much will affect the service life. As long as it is within the rated power range, there is no problem. If the oil pressure reaches the rated pressure and the speed increases, it will exceed the power range it can withstand. Of course, it will damage the service life of the cycloidal hydraulic motor. Just like not eating so much hard food, it will damage the stomach. Increasing the flow can only increase the speed in a limited way, from 500 to 900, change the model of the motor, increase the flow of the cycloidal motor, increase the speed without control, increase the internal oil pressure, increase the internal leakage, directly reduce the efficiency, and damage the motor. Above Nanning manufactor Ming can try, and consult the cycloid hydraulic motor expert if he thinks the error is found.
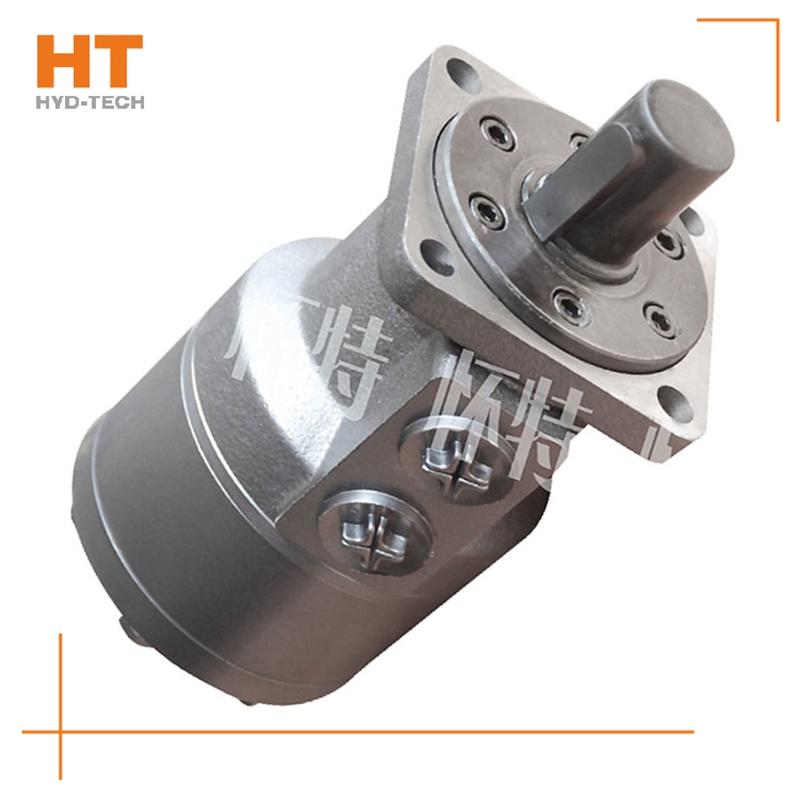
Most of its hydraulic system uses working medium, such as hydraulic oil with continuous fluidity, which converts the mechanical energy of the prime mover driving the pump into the pressure energy of the liquid through the hydraulic pump, and sends it to the actuator (hydraulic cylinder, hydraulic motor or swing hydraulic motor) through various control valves, such as pressure, flow, direction, etc., to convert it into mechanical energy to drive the load. This hydraulic system is generally composed of the following parts: power source, actuator, control valve, hydraulic auxiliary device and hydraulic working medium, which play their respective roles: power source: prime mover (motor or internal combustion engine) and hydraulic pump, whose role is to convert the mechanical energy generated by the prime mover into the pressure energy of liquid, and output oil with a certain pressure;