Hydraulic winch Also known as hydraulic elevator, it is one of the important operating parts of drilling equipment. hydraulic pressure windlass It is mainly used for the lifting and lowering of drilling equipment and protective tube in the whole process of drilling. The rope coring drilling process is adopted. The drilling equipment also needs to be equipped with a hydraulic winch for rope coring with a small lifting force.
1. Foundation requirements
During the whole drilling process, the important function of the lifting system is to take off and lower the drilling equipment. The ratio of take-off and landing process duration to the total drilling duration of all boreholes increases with the depth of the hole, and the ratio can reach 20%~35% for a 2000 m deep hole. Therefore, the soundness of the lifting system can directly affect the drilling efficiency and quality. The lifting system should meet the following basic requirements:
(1) The size, grade, speed range and load capacity of the lifting speed shall be judged to minimize the maneuvering time of the takeoff and landing process and maximize the power utilization.
(2) When running in the hole, the lifting system will bear a relatively large dynamic load based on the actual operation or the sharp change of conditions in the hole; When there is a stuck drill in the hole, carry out strong pulling. Therefore, the takeoff and landing system structure and compressive strength are required to meet this kind of load characteristics.
(3) When taking off and landing drilling equipment, inching takes off and landing action is frequent. Whether such action can be achieved accurately will not only affect the drilling efficiency, but also affect the drilling quality (for example, when lifting the drill, the core will fall off); The accuracy of micro control takeoff and landing in the whole process of solving safety accidents in the hole can directly affect the speed and actual effect of solving safety accidents. Therefore, in addition to the actual operating factors, the hydraulic winch is required to be flexible, stable and reliable.
(4) The accuracy and speed of the take-off and landing process shall be improved to prevent safety accidents. The control part of the hydraulic winch shall be convenient for the operator to carefully observe the orifice.
(5) The arrangement of the hydraulic winch shall facilitate the wire rope winding.
2. Basic working principle of hydraulic winch
As shown in Figure 4-12, the hydraulic winch adopts axial direction Plunger type hydraulic motor Push the main shaft 8, decelerate according to the planetary gear system 10, and transmit it to the wire rope drum 9, and carry out lifting or lowering operation according to the wire rope. The right side of the wire rope drum is equipped with a brake brake and an annular hydraulic cylinder. It can be seen from the figure that the spring 3 clamps the friction plate 6 according to the hydraulic cylinder piston 4, and the brake base is fixed. At this time, the locating disc 5 is braked, and the main shaft 8 cannot rotate.
Figure 4-12 Structural Diagram of Hydraulic Hoist
In the oil circuit design Hydraulic motor It is in parallel with the oil circuit of the annular hydraulic cylinder. When the hydraulic winch operates, it supplies pressure oil to the hydraulic motor and the annular hydraulic cylinder at the same time. The pressure oil entering the annular hydraulic cylinder overcomes the spring tension to loosen the brake brake and the wire rope drum operates. The lifting or lowering of the hydraulic winch is driven by the hydraulic motor. When the oil circuit is depressurized, the pressure of the annular hydraulic cylinder disappears, the brake brake is under the tension function of the spring, the positioning disc is braked, and the wire rope drum is in the braking state. When lowering the drilling equipment, when the lowering speed is too fast and exceeds the oil provided by the hydraulic motor, the drilling equipment will move at a constant speed at a certain speed based on the speed limit function of the balance valve on the oil return passage.
3. Estimation of gear train transmission ratio
Figure 4-13 is the transmission diagram of the winch. The gear train is a hybrid gear train. The hybrid gear train has not only fixed axle gear train but also epicyclic gear train. When calculating the transmission ratio of the hybrid gear train, it is not allowed to regard it as a whole, but to use a unified calculation formula to complete the estimation. It is necessary to separate the fixed axle gear train part and the epicyclic gear train part in the hybrid gear train, and then estimate their transmission ratios in different ways, and finally solve them together.
The key to the division of gear trains is to find out the epicyclic gear trains. The epicyclic gear train is characterized by a planetary gear, so first find the planetary gear, then find the link system (especially note that the link system is not necessarily a simple rod), and all the center wheels that mesh with the planetary gear. Each link system, together with the planet gear on the link system and the center gear engaged with the planet gear, forms an epicyclic gear system. In a complex hybrid gear train, it is likely to include several epicyclic gear trains (each link system corresponds to one epicyclic gear train). When this type of epicyclic gear train is classified, the rest is the fixed axle gear train.
Figure 4-13 Schematic diagram of winch transmission
First, separate the gear train in the winch, as shown in Figure 4-13. It is an epicyclic gear train composed of gears 1, 2, 3 and linkage H. On the left side, since the linkage H1 is fixed, gears 4, 5 and gear 3 form a fixed axle gear train. The gears 4 and 4 'are a duplex gear, and the rod system H is meshed with the external gear 4 by the internal gear spline, which is connected and integrated.
Now estimate their transmission ratios respectively:
The transmission ratio of fixed axle gear train is:
Deep prospecting drilling technology and practice
The transmission ratio of epicyclic gear train is:
Deep prospecting drilling technology and practice
Considering that gear 4 and linkage H are a coupling engaged by internal and external gears,
Deep prospecting drilling technology and practice
The above two equations can be solved simultaneously:
Deep prospecting drilling technology and practice
According to the gear tooth value given in the above formula, different transmission ratios can be obtained, and different drum speeds can be obtained.
4. Use and maintenance of hydraulic winch
Before using the hydraulic winch, be sure to have a thorough understanding of the structural and mechanical properties of the winch. And comply with operating procedures and safety guidelines.
(1) Replace the gear oil regularly. include:
1) Oil change: the gear oil should be replaced after the first 100h of operation, and then every 1000h or 6 months of operation, whichever is shorter. Gear oil must be replaced to prevent wear parts from damaging the reliability and safety of gear operation, as well as the erosion of bearings, gears and sealing rings. If the oil cannot be changed at the recommended minimum interval, it is likely to cause intermittent brake slip, which may cause damage to the winch, or even serious personal injury.
2) Oil level: the gear oil level shall be checked every 500h or 3 months, whichever is shorter. When checking the oil level, remove the large screw plug located in the center of the drum seat. The oil level should be level with the bottom of this opening.
3) Recommended planetary gear oil: practical experience shows that the use of suitable planetary gear oil can ensure the reliability and safety of the brake clutch
And its corrosion to bearings, gears and sealing rings. If the oil cannot be changed according to the recommended minimum interval, intermittent braking rolling may occur, which may lead to Hoisting winch Damage, even serious accidental injury.
2) Oil level: the gear oil level shall be tested every 500 h or 3 months, whichever is shorter. When testing the oil level, remove the large screw plug located in the center of the roller seat. The oil level should be at the same position as the bottom of this opening.
3) It is recommended to use planetary gear oil: practice has proved that the use of suitable planetary gear oil is particularly important for ensuring the reliability and safety performance of the brake clutch and obtaining a longer gear life.
If the type and viscosity of planetary gear oil used are unreasonable, it may lead to intermittent brake clutch rolling, resulting in damage to the hoist, and even serious accidental injury. Some gear lubricants have a lot of antiskid additives, which may cause the brake clutch to roll and damage the brake clutch disc and sealing ring. Since the temperature of the working environment causes the viscosity of the oil to change, this is also crucial for the credibility of the brake clutch operation. The test operation reflects that too heavy or too thick gear oil may cause intermittent brake clutch rolling. Therefore, it is necessary to ensure that the viscosity of the gear oil on the hoist is consistent with its main operating ambient temperature.
(2) Preheating procedure shall be carried out before hoisting winch operation. Preheating procedures shall be carried out before each operation. When the working environment temperature is less than 4 ℃, preheating must be carried out.
When starting, it should operate according to the lower reliable performance recommended, and ensure that the control valve of the hydraulic winch is in the neutral gear at the same time, so as to ensure that there is sufficient time to preheat the system. Afterwards, the hoisting winch shall be operated back and forth at a low speed for several times, so that the preheated hydraulic oil can be poured into all lubrication points and the gear oil can be lubricated through the planetary gear unit.
If the hoist is not properly preheated, especially when the working environment temperature is low, it may lead to temporary braking rolling due to the high counter pressure operation braking, which may lead to destruction of the hoist and serious accidental injury.
(3) When winding the steel wire rope on the drum of the lifting winch, it is not necessary to look forward to rolling it tightly with hands, but should hold the handle "one by one" to wind it tightly.
(4) Wire ropes with broken strands are not necessary.
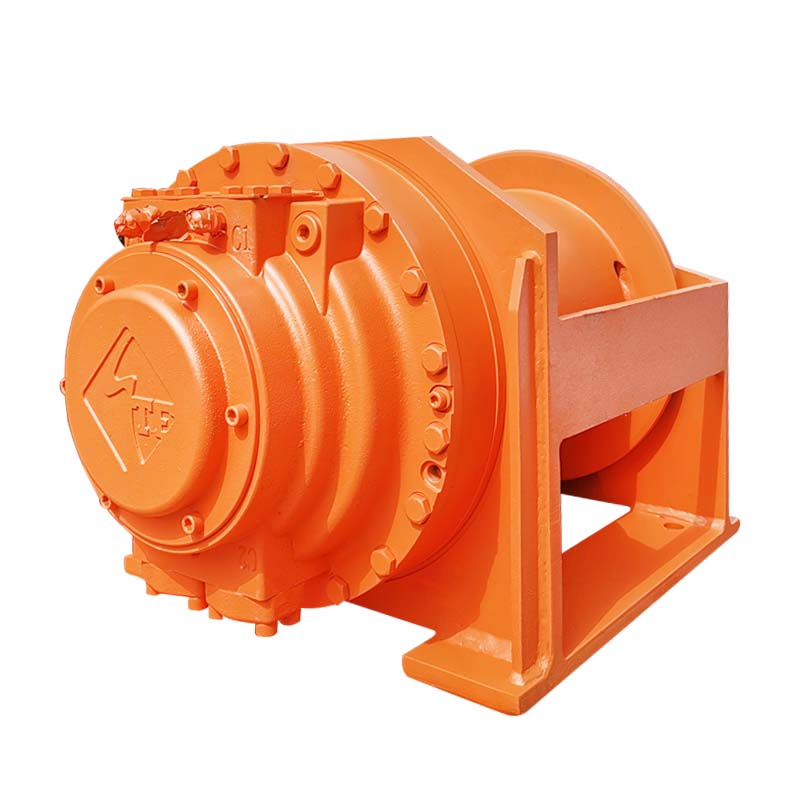