What is the practical significance of the torque calculation method of low speed ratio hydraulic motor manufacturers, that is, the hydraulic motor torque?
Generally speaking, the working pressure level of the system shall be determined first, and then the displacement of the motor shall be basically determined according to the load. The torque formula of hydroelectric motor is: T=(pv * mechanical kinetic energy)/(2 * 3.14). The practical significance of motor torque is its professional ability to rotate loads.
As the driving source of the system, the motor is inversely calculated from the load and finally established. The torque and speed ratio of the actuator must be determined, and then the transmission mechanism can be calculated. Finally, the model and specification of the actuator can be determined.
How to calculate the torque?
Hydraulic motor manufacturer Tell you how to calculate the torque?
Operating principle of hydraulic motor The relevant internal curve diagram motor roller solves the problem of impact, vibration and noise caused by the vertical plane of the motor stator double warping plate, and the difficulty of damage caused by serious problems?
The working pressure of the motor housing and oil valve is required. Generally, the working pressure of the oil valve exceeds the working pressure of the housing, then the gear pump will stick to the motor stator ring for operation. If the working pressure of the housing exceeds the working pressure of the oil valve, then the gear pump will be pushed away from the motor stator ring, and all the oil inlet ports will be replaced with high pressure ports, High working pressure will bump the gear pump into the motor stator ring, causing a loud noise. A long time will cause many pits on the motor stator ring, which will not work quickly.
Low speed high torque hydraulic motor How to rotate the wrong stator and rotor pair? The stator and rotor pair is due to the wrong relative position of the rotor and the port plate. The roller line hydraulic motor is divided into two types: shaft port and internal thread port.
The way to carry out flow distribution for the machine tool spindle bearing is to punch an oil groove on the bearing end cover of the rolling bearing to break through the minimum sealing cavity of the rotor stator pair. Try it. If there is a tooth leakage when turning it over, it is OK. Select the port plate to carry out internal thread flow distribution, connect the port shaft with the motor rotor, install the motor stator pair, and measure the deep layer of the airtight cavity. If the cavity in the clockwise direction with the least airtight cavity is higher than the cavity in the reverse direction, it will rotate.
The deep layer is the sum of stator, baffle and port plate. Its key reason lies in the valve plate. Generally speaking, when liquid is fed into the side of the port plate, the clockwise inner cavity (high pressure inner cavity) where the rotor stator is located just leads to the above minimum sealing inner cavity.
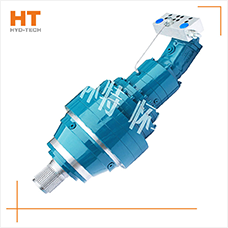