Special cycloidal motor for hydraulic winch The key raw material of the casing is nodular cast iron, and the purpose of quenching nodular cast iron is to obtain Cycloidal motor for traveling reducer The ferrite mechanism can optimize the crystal and make the mechanism symmetrical, thus improving the compressive strength, hardness and wear resistance of parts, and can be used as the prior heat treatment process of surface heat treatment.
(1) High temperature quenching: the high temperature quenching process is to heat the casting to above the eutectoid temperature range, generally 900~950 ℃, and keep the heat insulation for 1~3h, so that all the base material mechanisms are martensitized, and then announce air cooling to make it within the eutectoid temperature range. Ferrite base materials are obtained because of rapid cooling. For thick wall pipe castings with high silicon content, air cooling should be used, Or spray cooling to ensure that ferrite ductile iron can be obtained after quenching
(2) Ultra low temperature quenching: the ultra low temperature quenching process is to heat the casting to the eutectoid temperature range, that is, 820~860 ℃, heat insulation for 1~4h, so that a part of the base material mechanism is martensitized, and then it is announced that ferrite and dispersed metallographic ductile iron can be obtained after air cooling ultra low temperature quenching, which can improve the ductility and plastic deformation of the casting.
Because the heat transfer of nodular cast iron is weak, and the elastic mold is large, there is a large thermal stress in the castings after quenching. Therefore, most processing plants also carry out a de geostress quenching (often called quenching) after quenching, that is, heating to 550~600 ℃, thermal insulation for 3~4h, and then announce air cooling.
In order to greatly improve the surface hardness, wear resistance and corrosion resistance of gray cast iron surface, and increase the service life of the parts after processing, our company will carry out a soft nitriding solution for the parts.
Generally, nitriding is applied to product workpieces with heavy load and high relativity requirements for touching fatigue, and pays attention to the deep level. The effect of soft nitriding is that it has a fast penetration rate, which is generally used for products with small load and shallow penetration layer. There are two basic nitriding methods: hard nitriding and soft nitriding.
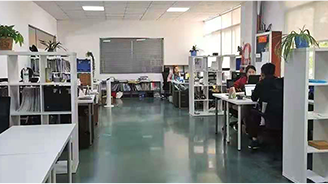