Oil trapped condition
During stable operation of gear oil pump, the coincidence index of gear mesh must exceed 1, that is, at least one pair BMK6 cycloidal hydraulic motor The transmission gear above is additionally engaged, so during the whole process of work, part of the oil will be trapped in the closed oil cavity generated when two pairs of transmission gears engage. As shown in Figure 2.5, the size of this sealing volume changes with the rotation of the transmission gear. From Figure 2.5 (a) to 2.5 (b), the sealing volume decreases slowly; From Figure 2.5 (b) to 2.5 (c), the sealing volume slowly expands; From Figure 2.5 (c) to the sealing volume, it will decrease again, which will cause the regular expansion and reduction of the sealing volume. The trapped oil is squeezed to form, resulting in instant high pressure. If the trapped oil in the seal chamber is not interconnected with the oil drain port, the oil will be squeezed from the gap, causing the oil to burn, and rolling bearings and other parts will also suffer from additional impact loads; If there is no filling of oil when the sealing volume is expanded, it will lead to partial vacuum pumps to extract the vapor in the dissolved oil, causing CB Hagelung hydraulic motor Cavitation is the trapped oil condition of the gear oil pump.
The trapped oil condition makes the gear oil pump cause obvious noise, vibration and cavitation. In addition, it reduces the volume efficiency of the pump, endangering the stability and service life in work. The way to remove the trapped oil is generally to open a discharge slot on the rear cover plates on both sides, as shown in the diagonal frame in the figure. When the closed volume is reduced, the discharge chute on the right side is interconnected with the oil pressure chamber, while when the closed volume is expanded, the pressure relief chute on the left side is interconnected with the oil suction chamber. The interval between the two pressure relief grooves must ensure that oil suction and drainage are not interconnected at any time.
Radial unbalance force
In the gear oil pump, the working pressure of the oil efficiency at the wheel edge is not uniform. From the bottom pressure chamber to the high pressure chamber, the working pressure increases tooth by tooth along the rotation direction of the transmission gear. Therefore, the transmission gear and shaft suffer from the effect of radial imbalance force. The higher the pressure, the greater the radial imbalance force. When the radial imbalance force is very large, the pump shaft can be bent, This causes the engagement angle to press against the bottom pressure end of the motor stator, causing eccentric wear of the motor stator. In addition, it also speeds up the damage of the rolling bearing and reduces the service life of the rolling bearing. In order to better reduce the harm of radial unbalanced force, the method of reducing the oil pressure port is often used to make the working pressure of the oil pressure chamber only work within the range of one tooth to two teeth. In addition, the radial clearance is moderately expanded so that the tooth top does not touch the metal material with the inner surface of the motor stator, and cylindrical roller bearings or rolling bearings are mostly used at the support points.
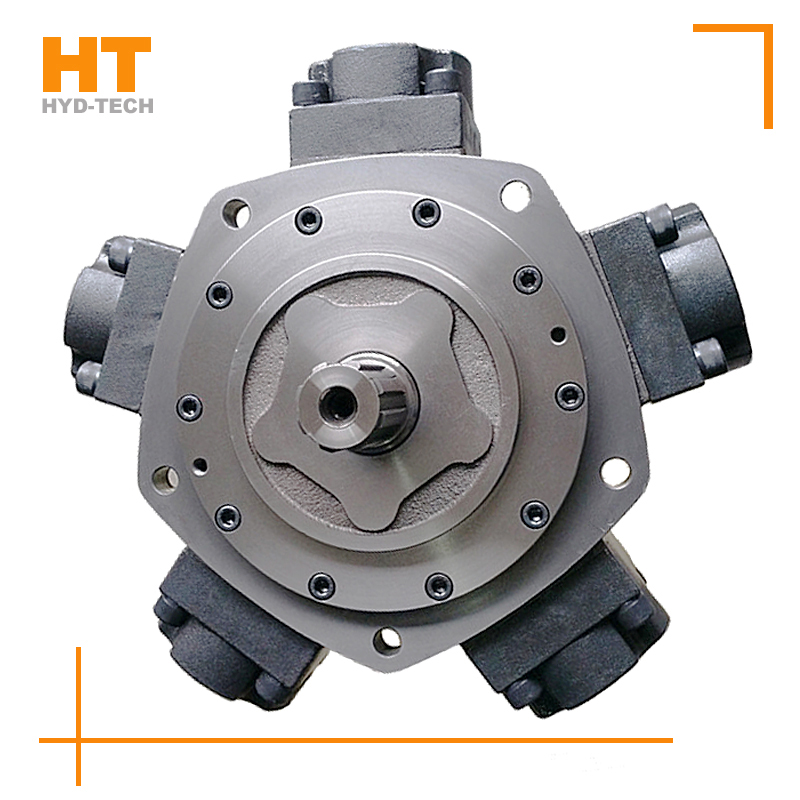