The specification and model of the small motor of the hydraulic press are convenient for the working reliability of the motor, and it is required to have a certain oil valve condensing type, especially for the motor of the inner trend diagram, or else it will cause the roller to solve the slope of the motor stator guide rail, resulting in impact, vibration, noise, or damage in serious cases. The condensing value cannot be very large. According to the positive proportion of the inlet and outlet pressure difference between the torque of the oil motor and each other, when the inlet working pressure is fixed, the condensing expansion will inevitably reduce the international trade pressure difference of the oil motor, thus causing the oil motor to be sleepy. Generally, the condensing type of oil valve shall be 0.3MPa~1.0MPa.
Oil drain pipeline Oil drain pipeline is generally not connected to the system oil valve channel, White motor For motors with cleaning system, the oil discharge pipeline can be used as the return pipeline for cleaning. When the motor shaft is installed in the horizontal direction, the oil drain pipe should be connected to the oil drain inlet at the top end of the plug. If the motor shaft is installed in the vertical direction, the oil drain pipe should be connected to the optional oil drain inlet of the upper rolling bearing end cap of the motor. If necessary, the appropriate condensing type can be increased on the oil drain pipe. The condensing type value should not be very large, or the shaft seal ring will be damaged and cause leakage. The condensing type value should be controlled below 0.4CPa, In terms of work, the instantaneous value should be less than 0.8MPa, which is known based on the accurate measurement of the working pressure of the motor cover), which is conducive to spreading gear oil inside the motor from beginning to end, and can reduce the operating noise of the motor.
Impeller type Oil motor Since the transmission ratio of the internal trend chart multi acting oil motor is low and the load of ROYALOAKROSEGOLDREPLICA is large, the internal needle bearing cannot cause the lubricating grease film, so it should be greased on time, and the cycle is generally 2000h~3000h.
When installing, disassembling and disassembling the motor, the output shaft of the motor shall be less or less vulnerable to axial force as far as possible, so as to ensure that the internal fulcrum roller bearing of the motor is not vulnerable to additional force. Otherwise, long-term use will cause deflection of the oil distribution mechanism and damage its service life. Therefore, the drive shaft of the motor shall be concentric with other sleeves during installation, or soft connection shall be adopted. For the motor with torque arm, the motor and torque arm should be connected first during installation, and then the constant torque arm should be fixed to avoid damage to the plug or distribution shaft.
Pay attention to the matching of oil motor. If abnormal signals are found, be good at capturing common problem signals, and take measures immediately. The small changes of sound, vibration and temperature all mean the shortcomings of the motor. The motor has been used, and there is internal leakage, and the leakage will increase with the increase of temperature. Since internal leakage can deform the sealing washer and lining ring, it may also cause external leakage. For the identification of internal leakage of the motor, my maintenance experience is: first cut off the oil return pipe of the motor, stop the system cleaning and disconnect the connection between the motor and the cleaning pipe, then adjust the working pressure of the system to at least, after starting the oil pump, gradually adjust the working pressure to all normal ranges, The working pressure change and leakage of the capping can be observed at the pressure measuring point and the oil inlet of the motor. If necessary, the test can be conducted in both positive and negative directions.
Keep the gear oil removed to keep the oil as clean as possible. Behind the most common problems of oil motor is the reduction of oil quality. Most of the common problems are caused by solid particles (particles), air pollution sources and transparent liquids caused by overheating. The work experience summarized is: Hydraulic transmission The gear oil cleanliness level of system software shall be at least within NAS9. Otherwise, the sediment contained in the engine oil will cause the surface of the friction parts in the motor to be damaged, and the friction pair will be damaged into a trench excavation, resulting in the expansion of leakage.
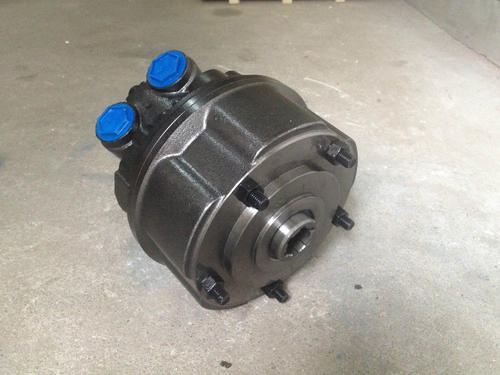