Hydraulic press pipe installation is a key project of hydraulic machinery installation. The quality of pipeline installation is related to Hydraulic transmission The characteristics of the system during operation are one of the important factors for whether everything is normal.
The pipe routing design scheme and pipe threading shall first consider the components, hydraulic system, tee joints and flanges to be connected as a whole according to the hydraulic schematic diagram Traveling cycloid motor 。
The laying sequence and direction of pipes shall be neat, consistent and clear. Horizontal or vertical pipes shall be used as far as possible, and the unevenness of horizontal pipes shall be ≤ 2/1000; The unevenness of vertical pipes shall be ≤ 2/400. Check with a level gauge.
In the middle of parallel plane or crossed pipeline, Brake hydraulic motor There should be a gap of more than 11mm.
The pipeline must be equipped to facilitate the handling and maintenance of pipelines, hydraulic solenoid valves and other components. All sections of pipes or components in the system software shall be disassembled at will as far as possible without harming other components.
The pipeline must have a certain rigidity and anti vibration capacity when threading. Pipe supports and spring hangers shall be provided as far as possible. The bent pipe shall be equipped with support frame or spring hanger at the starting point.
The pipe shall not be welded with the support or spring hanger immediately.
The net weight of the pipeline shall not be borne by the valve, pump, its hydraulic system and auxiliary parts; The pipe shall not support the net weight of the overweight components.
For longer pipes, reasonable measures must be taken to avoid the ground stress caused by the expansion of pipes due to temperature change.
The applied pipe material must have an established initial basis of raw materials. Pipes with unknown materials are not allowed to be used.
The hydraulic transmission system pipe with a diameter of less than 50mm can be laser cut with a grinding wheel cutter. Pipes above 50mm in diameter shall generally be laser cut by machining. If oxygen cutting is used, a part of the mechanism transformation caused by oxygen cutting must be removed by mechanical processing and manufacturing, and the welding seam can also be removed. Except for the oil return pipe, it is not allowed to use roller extrusion cutting laser cutting for the working pressure of the pipe. The surface of the laser cutting pipe must be leveled to remove burrs, oxide skin, slag, etc. The surface of the wound and the center line of the tube should be vertical.
When a pipeline is composed of two sections of pipeline and supporting facilities, it shall be connected section by section, and the next section shall be equipped after assembly to prevent accumulated difference caused by one-time welding.
In order to better reduce the damage to the pipeline caused by some working pressures, it is necessary to prevent the cross-section of each part of the pipeline from being significantly expanded or reduced and to make it significantly bent.
The pipe connected with the tee joint or flange must be a section of connecting pipe, that is, the pivot axis of this section of pipe should be parallel to and overlap with the pivot axis of the tee joint or flange. The distance of this parallel line segment shall be greater than or equal to 2 times of the pipe diameter.
Pipes with diameter less than 30mm can be cold drawn. When the pipe diameter is 30-50 mm, cold drawing or hot bending method can be used. When the pipe diameter exceeds 50mm, the hot bending method is generally adopted.
Electric welders who weld hydraulic press pipes shall have reasonable high pressure pipe welding certificates.
Selection of welding process: acetylene gas cutting is the key to use for pipes with galvanized steel pipe wall thickness no more than 2mm. The key of arc welding is used for galvanized steel pipes with wall thickness more than 2mm. Argon arc welding machine shall be used for pipe welding as far as possible. For pipes with wall thickness more than 5mm, argon arc welding machine shall be used for internal splicing and arc welding for filling. Necessary places shall be welded by filling and maintaining steam in the nozzle.
The welding wire and flux shall be consistent with the steel pipe materials to be welded, and the model must have established basis materials, product certificate and reasonable application period. The welding wire and flux shall be air dried according to the requirements of the product manual before application, and shall be kept dry throughout the application process and applied on the same day. The welding wire and core shall be free of falling and obvious cracks.
Butt welding shall be adopted for hydraulic machine pipe welding. Before welding, remove the dirt, oil stain, moisture and rust on the weld and the surface layer 10-20mm wide.
Butt welding flange shall be used for the welding of pipeline and flange, instead of plug-in flange.
Butt welding shall be adopted for the welding of pipe and tee joint, instead of plug-in welding.
Butt welding shall be adopted for pipe to pipe welding, and plug-in welding is not allowed.
When the hydraulic press pipe is butt welded, the welding chamber must be 0.3-0.5mm higher than the pipe. It is not allowed to enter the cavity. After welding, use a file or portable sand wheel to smooth the welding in the inner cavity. Remove the welding scar and burr to be smooth and level.
The cross section of butt welding shall be vertical to the pipe axis.
The welding cross section is not allowed at the corner, and it should also be prevented from being in the middle of the two elbows of the pipe.
When welding the pipe, be sure to weld accurately according to the installation position, then remove it for welding, and then assemble it for plastic surgery.
During the whole welding process, the erosion of wind, rain and snow shall be avoided. After the pipe is welded, the welding with a wall thickness of no more than 5mm should be cooled at the indoor temperature, instead of forced cooling by strong wind or spraying water.
The welding shall be fully penetrated, and the surface shall be evenly leveled. The welding of working pressure pipeline shall be inspected by sampling flaw detection.
After the pipes are threaded and welded, all pipes shall be pre installed once according to their positions. Connect each hydraulic system, valve block, valve rack and sewage treatment plant. All sockets should certainly meet and align, and cannot be forced to twist. When the three-way joint or flange screw is loosened, the axis of the relative fusion surface shall not have large displacement, gap or seesaw angle. If such a situation occurs, it can be removed by burning plastic surgery.
It can be used to weld the spring hanger and sound card rack firmly after all pipes are threaded, and it can also be carried out in a cross manner as required.
After pipe threading, welding and pre installation, the pipe shall be disassembled again for phosphating treatment. After phosphating treatment, the pipeline enters warm air to dry rapidly. When the gear oil enters the system software and pipe after being dry, it is generally not subject to rust prevention treatment, but should be properly stored. If it is necessary to leave it idle for a long time and wear resistant coating must be applied, it must be applied after two days of pickling and phosphating. It should be noted that the wear-resistant coating must be compatible with the cleaning fluid or gear oil used for pipeline cleaning later.
Before the pipes are installed again after pickling, passivation, phosphating and drying, the inner cavity of each pipe shall be pre cleaned. After the pre cleaning, the system software shall be reinstalled as soon as possible to carry out the overall system software
The purification treatment of the circulating system shall be solved until the cleanliness level specified in the control system design is achieved.
The use of plastic hoses is limited to the following places:
-----Middle of mobile components of machinery and equipment
-----The place for replacing parts
-----Where vibration analysis or noise transmission is suppressed
The installation of plastic hoses must pay attention not to make the plastic hoses and connectors cause additional bearing force, distortion, substantial bending, friction and other poor working conditions.
Before the plastic hose is installed into the system software, the inner wall and connector shall also be cleaned.
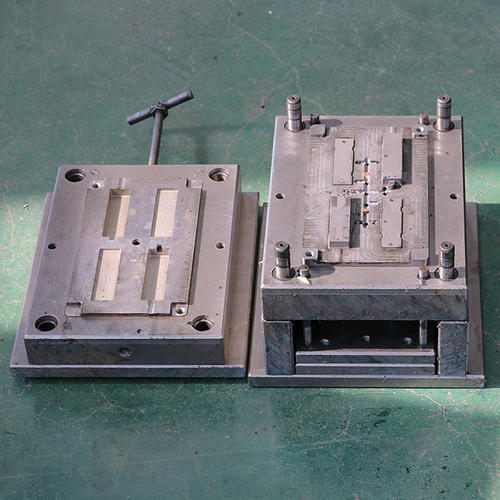