The piston pump is the main equipment in the hydraulic system. Depending on the reciprocating movement of the plunger in the cylinder body, the volume of the sealed working chamber changes, and the oil suction and pressure processes are completed. The plunger in the cylinder needs to move back and forth, so it has a large amount of movement and needs to bear unlimited friction when working. Therefore, the plunger requires high hardness, high wear resistance, service life and accuracy. After discussion, the quenching heat treatment process that can meet the technical requirements of the plunger is selected. Hardening is to heat the steel to the critical temperature of Ac3 (hypoeutectoid steel) or Ac1 (hypereutectoid steel), and hold at this temperature for a period of time to make it completely or partially austenitized.
The piston pump is the main equipment in the hydraulic system. Depending on the reciprocating movement of the plunger in the cylinder body, the volume of the sealed working chamber changes, and the oil suction and pressure processes are completed.
The plunger in the cylinder needs to move back and forth, so it has a large amount of movement and needs to bear unlimited friction when working. Therefore, Cycloidal motor manufacturer Plunger requires high hardness, high wear resistance, service life and precision, etc. After discussion, the quenching heat treatment process that can meet the technical requirements of the plunger is selected.
Hardening refers to heating the steel to a critical temperature above Ac3 (hypoeutectoid steel) or Ac1 (hypereutectoid steel) and holding it for a period of time, White cycloid motor Fully or partially austenitize, then Cycloidal motor speed Heat treatment technique of rapidly cooling below Ms (or isothermal near Ms) at a cooling rate higher than the critical cooling rate to change martensite (or bainite). Quenching technology is widely used in modern machinery manufacturing industry. The main parts of the machine, especially the steel parts used in cars, aircraft and rockets, are all quenched.
All openings of the fuselage and base are covered. Place the unit on the foundation where the anchor bolts are buried, and use a pair of wedge pads between the base and the foundation for calibration. The concentricity of the pump shaft and motor shaft shall be corrected, and the allowable error of the outer circle of the coupling shaft shall be 0.1mm; Ensure that the gap between the two coupling planes is 2~4mm, (small value for small pump) the gap should be even, with a tolerance of 0.3mm. After connecting the pipe and judging the rotation direction of the motor, connect the coupling, check the coupling, and judge the rotation direction of the coupling. After 2~3 hours of trial operation, the unit is comprehensively inspected. If there is no defect, the equipment is considered qualified. During the test, observe the bearing temperature and vibration as follows: loosen the coupling, place a level on the pump shaft and base of the electric oil pump, adjust the wedge, correct the unit level, and properly tighten the anchor bolts to prevent walking. In order to prevent sundries in the pipeline from entering the pump, for the pipeline of new equipment, a filter shall be installed on the pump rubber layer, and the effective section of the filter shall be 2-3 times larger than that of the suction pipeline.
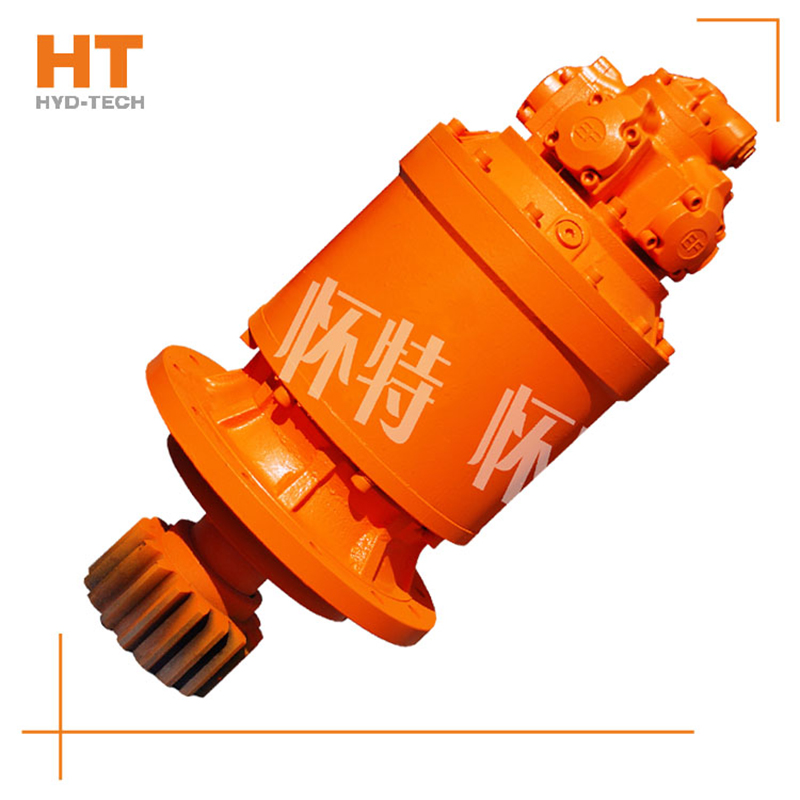